How EBM Technology is Revolutionizing Aerospace Manufacturing
Table of Contents
The aerospace industry thrives on innovation. Every gram shaved off an aircraft translates to increased fuel efficiency and longer flight ranges. Every component that boasts superior strength-to-weight ratio pushes the boundaries of what’s possible. Enter Electron Beam Melting (EBM) technology, a revolutionary additive manufacturing (AM) process that’s rapidly transforming how we design and manufacture critical parts for airplanes, rockets, and spacecraft.
EBM 101: Building Metal One Layer at a Time
Imagine a 3D printer, but instead of plastic filament, it uses a high-powered electron beam to melt metal powder layer by layer, meticulously building a complex, three-dimensional object based on a digital design file. That’s the essence of EBM. The entire process takes place in a vacuum chamber, ensuring a clean and controlled environment that minimizes oxidation and other contaminants. This meticulous approach allows EBM to produce near-net-shape parts with exceptional accuracy, complex geometries, and outstanding mechanical properties.
Here’s a breakdown of the key benefits that make EBM so attractive for aerospace applications:
- Lightweighting: EBM excels at creating intricate, lightweight structures. This translates directly to fuel savings and improved aircraft performance. Think of it like replacing bulky metal components with finely crafted, high-strength lacework – all while maintaining the structural integrity needed for soaring through the skies.
- Design Freedom: Traditional manufacturing techniques often impose limitations on design complexity. EBM breaks those shackles. With EBM, aerospace engineers can unleash their creativity, designing intricate internal features and lattice structures that were previously impossible to manufacture. This opens doors to a whole new realm of possibilities for optimizing part performance and weight reduction.
- Material Versatility: EBM isn’t limited to just a few metals. It can handle a wide range of metal powders, including high-performance alloys like nickel superalloys, titanium alloys, and Inconel. These materials offer exceptional strength, heat resistance, and corrosion resistance, making them ideal for demanding aerospace applications.
- Reduced Waste: Traditional manufacturing often generates a significant amount of scrap material. EBM, on the other hand, is an additive process, meaning it only uses the metal powder needed to build the part. This minimizes waste and contributes to a more sustainable manufacturing approach.
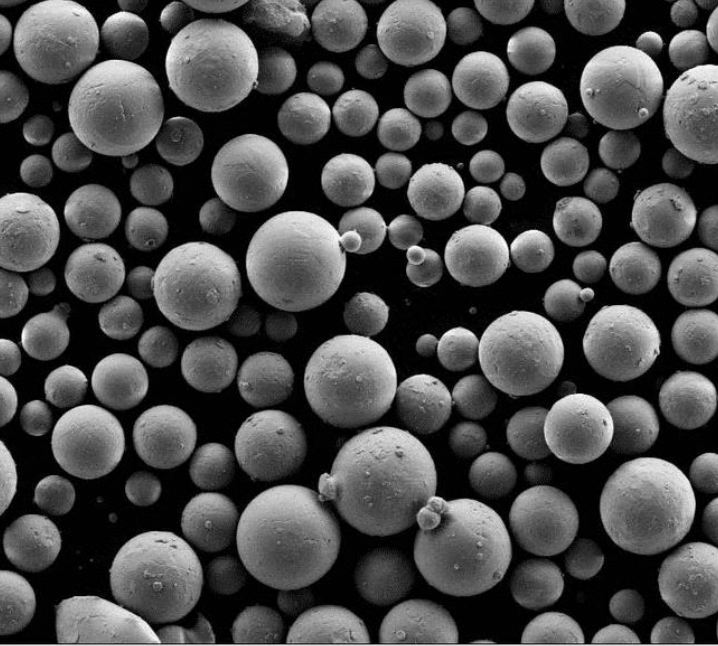
The Building Blocks of Aerospace Innovation
Now that we’ve explored the advantages of EBM, let’s delve into the specific metal powders that are fueling this aerospace revolution.
Metal Powder | Composition | Properties | Applications in Aerospace |
---|---|---|---|
Ti-6Al-4V | Titanium (Ti), Aluminum (Al), Vanadium (V) | High strength-to-weight ratio, excellent corrosion resistance, biocompatible | Engine components, landing gear parts, airframe components |
Inconel 625 | Nickel (Ni), Chromium (Cr), Molybdenum (Mo), Iron (Fe) | Exceptional high-temperature strength, good oxidation resistance | Turbine blades, combustor liners, exhaust ducts |
Maraging Steel | Iron (Fe), Nickel (Ni), Molybdenum (Mo), Titanium (Ti), Aluminum (Al) | High strength, good ductility, excellent dimensional stability | Rocket engine components, landing gear components, high-pressure vessels |
Aluminum (AlSi10Mg) | Aluminum (Al), Silicon (Si), Magnesium (Mg) | Lightweight, good corrosion resistance, high thermal conductivity | Heat exchangers, structural components requiring weight reduction |
Nickel Superalloy CM247LC | Nickel (Ni), Chromium (Cr), Cobalt (Co), Molybdenum (Mo), Tantalum (Ta) | Superior creep resistance at high temperatures, good oxidation resistance | Turbine blades, combustor liners, afterburner components |
Copper (Cu) | Copper (Cu) | Excellent thermal and electrical conductivity, good machinability | Heat exchangers, busbars for electrical systems |
Stainless Steel 316L | Iron (Fe), Chromium (Cr), Nickel (Ni), Molybdenum (Mo) | Good corrosion resistance, biocompatible | Fluid handling components, medical implants used in aerospace applications |
Rene 41 | Nickel (Ni), Chromium (Co), Cobalt (Mo), Titanium (Ti), Aluminum (Al) | High strength at elevated temperatures, good oxidation resistance | Turbine disks, compressor blades, afterburner components |
Titanium Aluminide (TiAl4Si3) | Titanium (Ti), Aluminum (Al), Silicon (Si) | Low density, high-temperature oxidation resistance | Turbine blades, combustor liners for hypersonic vehicles |
Inconel 718 | Nickel (Ni), Chromium (Cr), Iron (Fe), Niobium (Nb), Molybdenum (Mo) | High strength, good fatigue resistance, excellent machinability | Structural components, landing gear |
Manufacturing Complex Shaped Parts using EBM Technology
The ability to manufacture intricate, near-net-shape parts is another significant advantage of EBM for aerospace applications. Traditional manufacturing processes often rely on subtractive techniques like machining, which involve removing material from a solid block to achieve the desired shape. This can be a time-consuming and wasteful process, especially for complex geometries.
EBM, on the other hand, is an additive process. It builds the part layer by layer, directly from a digital design file. This allows for the creation of highly complex internal features, channels, and lattice structures that would be nearly impossible (or incredibly expensive) to achieve with traditional methods. These internal features can play a crucial role in optimizing part performance. For instance, intricate cooling channels within a turbine blade can improve heat dissipation and extend its lifespan.
Here are some specific examples of how EBM is being used to manufacture complex shaped parts in aerospace:
- Fuel Nozzles: EBM is being used to create fuel nozzles with intricate internal flow paths that optimize fuel atomization and combustion efficiency, leading to improved engine performance.
- Lightweight Heat Exchangers: The ability to create intricate lattice structures with EBM allows for the development of lightweight heat exchangers with superior heat transfer capabilities. This is crucial for managing the immense amount of heat generated by aircraft engines.
- Landing Gear Components: EBM is being employed to manufacture landing gear components with complex internal structures that combine high strength with reduced weight. This contributes to improved fuel efficiency and overall aircraft performance.
EBM Technology Can Reduce the Weight of Parts
The aerospace industry is constantly striving to shave off every gram possible from aircraft. Even a slight weight reduction can translate to significant fuel savings and increased range. This is where EBM shines. Here’s how:
- Material Selection: As we explored earlier, EBM is compatible with a wide range of metal powders, including lightweight materials like titanium and aluminum alloys. These materials offer excellent strength-to-weight ratios, allowing engineers to create parts that are both strong and lightweight.
- Lattice Structures: EBM excels at manufacturing intricate lattice structures. These internal networks of struts and beams provide exceptional strength while minimizing weight. Imagine a bridge – a traditional solid structure would be incredibly heavy, but a network of trusses can achieve the same level of support with significantly less material. EBM allows for the creation of similar lightweight, high-strength structures within aerospace components.
Here’s a real-world example:
- EBM-manufactured landing gear component: Compared to a traditionally manufactured counterpart, an EBM-made landing gear component can be up to 30% lighter while maintaining the same level of strength and functionality. This translates to a significant weight reduction for the entire aircraft, leading to improved fuel efficiency and increased range.
EBM Technology Can Shorten Manufacturing Cycles
Time is money, especially in the fast-paced world of aerospace. Traditional manufacturing processes can be lengthy, involving multiple steps and long lead times for procuring parts. EBM offers a potential solution for streamlining production:
- Reduced Complexity: EBM can often consolidate multiple parts into a single, complex component. This eliminates the need for assembly processes and reduces overall manufacturing time.
- On-demand Manufacturing: EBM allows for on-demand production of parts. This can be particularly beneficial for creating prototypes or spare parts that may not be readily available through traditional channels.
Here’s an example of how EBM can shorten manufacturing cycles:
- Manufacturing a complex rocket engine component: Traditionally, this component might require multiple parts to be machined and then assembled. With EBM, the entire component can be manufactured as a single unit, significantly reducing production time and complexity.
EBM Technology Can Reduce Manufacturing Costs
While the initial investment in EBM equipment can be higher compared to traditional methods, there are several factors that can contribute to reduced overall manufacturing costs:
- Reduced Material Waste: EBM is an additive process, meaning it only uses the metal powder needed to build the part. This minimizes scrap material and reduces overall material costs.
- Consolidation of Parts: As mentioned earlier, EBM can often consolidate multiple parts into a single unit. This eliminates the need for additional machining and assembly processes, reducing labor costs.
- Faster Production Times: The ability to streamline production with EBM can lead to shorter lead times and potentially lower inventory carrying costs.
Here’s an example of how EBM can reduce manufacturing costs:
- Manufacturing a heat exchanger: Traditionally, a heat exchanger might require multiple components to be brazed or welded together. With EBM, the entire heat exchanger can be manufactured as a single unit, eliminating the need for these additional processes and associated labor costs.
EBM Technology: Advantages and Limitations
Advantages:
- Design Freedom: EBM allows for the creation of complex geometries and internal features that are impossible with traditional methods. This opens doors for innovative part design and performance optimization.
- Lightweighting: EBM excels at manufacturing lightweight parts with high strength-to-weight ratios, contributing to improved fuel efficiency and aircraft performance.
- Material Versatility: EBM can handle a wide range of metal powders, including high-performance alloys that are ideal for demanding aerospace applications.
- Reduced Waste: EBM is an additive process that minimizes scrap material, promoting a more sustainable manufacturing approach.
Limitations:
- High Initial Investment: The cost of EBM equipment can be higher compared to traditional manufacturing methods.
- Limited Build Volume: Current EBM machines have limitations on the size of parts they can produce. This may not be suitable for very large aerospace components.
- Surface Roughness: While EBM offers good surface finish, some applications might require additional post-processing techniques to achieve a smoother surface.
- Support Structures: EBM requires the use of support structures to build overhanging features. These supports need to be removed after the build process, which can add time and complexity.
FAQ
Q: What are some of the challenges associated with using EBM technology in aerospace?
A: As with any new technology, there are challenges to overcome. Some of the key challenges for EBM in aerospace include the high initial investment cost, limitations on build volume for very large parts, and the need for post-processing techniques to achieve desired surface finishes.
Q: How is EBM technology expected to impact the future of aerospace manufacturing?
A: EBM has the potential to revolutionize aerospace manufacturing by enabling the production of lighter, more complex, and higher-performing parts. As the technology matures and costs come down, we can expect EBM to be used more extensively for a wider range of aerospace applications.
Q: Is EBM environmentally friendly?
A: Compared to traditional manufacturing methods that generate significant scrap material, EBM offers a more sustainable approach. EBM is an additive process that uses only the metal powder needed to build the part, minimizing waste.
Q: What are some of the safety considerations for using EBM technology?
A: EBM involves working with high-powered electron beams and metal powders. Proper safety protocols need to be followed to ensure operator safety. This includes using appropriate personal protective equipment (PPE) and adhering to established safety guidelines.
Q: Where can I learn more about EBM technology?
A: Several resources are available online and in libraries that provide detailed information about EBM technology. Additionally, industry associations and research institutions can offer valuable insights into the latest advancements and applications of EBM in aerospace manufacturing.
Conclusion
EBM technology is rapidly transforming the aerospace industry by enabling the creation of lighter, stronger, and more complex components. With its ability to produce intricate near-net-shape parts, EBM is pushing the boundaries of design and manufacturing, paving the way for a new generation of high-performance aircraft. As EBM technology continues to mature and costs become more competitive, we can expect to see its adoption expanding across the aerospace sector, shaping the future of flight.
Share On
MET3DP Technology Co., LTD is a leading provider of additive manufacturing solutions headquartered in Qingdao, China. Our company specializes in 3D printing equipment and high-performance metal powders for industrial applications.
Inquiry to get best price and customized Solution for your business!
Related Articles
About Met3DP
Recent Update
Our Product
CONTACT US
Any questions? Send us message now! We’ll serve your request with a whole team after receiving your message.
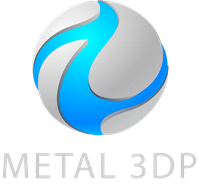
Metal Powders for 3D Printing and Additive Manufacturing