Notes on EBM technology
Table of Contents
Electron Beam Melting (EBM) has emerged as a revolutionary force in the world of 3D printing, allowing for the creation of complex, high-performance metal parts. But what exactly is EBM, and how does it work? This comprehensive guide delves into the intricacies of EBM technology, exploring its core principles, the fascinating world of EBM metal powders, and its diverse applications across industries.
EBM Explained: A Fusion of Power and Precision
Imagine a sculptor wielding a miniature sunbeam, meticulously building a metal masterpiece layer by layer. That’s the essence of EBM. In this additive manufacturing process, a high-powered electron beam acts as the sculptor’s tool, melting metal powder into a predetermined design. Here’s a breakdown of the magic behind EBM:
- The Mighty Electron Beam: EBM utilizes an electron gun that generates a concentrated beam of electrons. This beam, boasting incredible energy, serves as the heat source for melting the metal powder.
- The Powder Playground: The build chamber houses a bed of fine metal powder. Depending on the desired final product, the powder material can vary – from titanium and stainless steel to exotic alloys like Inconel.
- Building Block by Block: A computer-controlled system meticulously spreads the metal powder across the build platform in thin layers. The electron beam then scans the design blueprint, selectively melting the powder particles in each layer, fusing them together.
- Layer Upon Layer: This process of spreading powder, melting, and fusing repeats itself layer by layer, gradually building the 3D object from the ground up. Once complete, the finished part is separated from the excess powder, ready to take on its designated role.
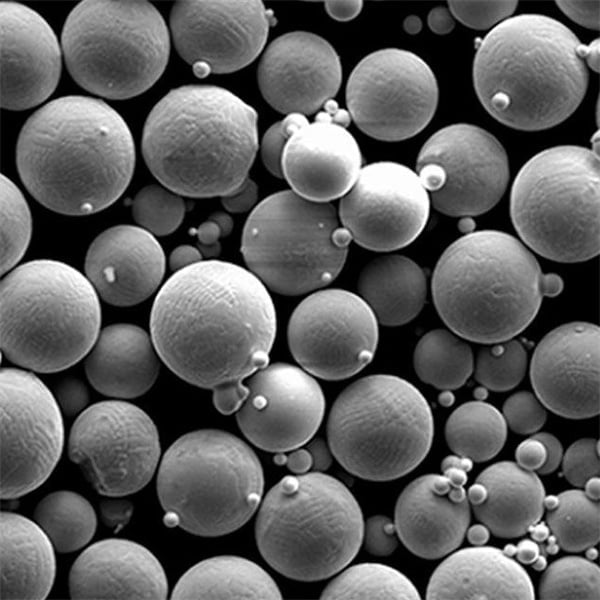
A Universe of EBM Metal Powders
The heart of EBM lies in the metal powders used. Just like artists have their preferred paints and brushes, the choice of metal powder significantly impacts the final product’s properties. Let’s explore some of the most commonly used EBM metal powders:
Material | Description | Properties |
---|---|---|
Titanium (Ti-6Al-4V) | The most widely used EBM powder, known for its excellent strength-to-weight ratio, biocompatibility, and corrosion resistance. | Ideal for aerospace parts, medical implants, and sporting goods. |
Stainless Steel (316L) | A versatile and cost-effective option, offering good corrosion resistance and mechanical properties. | Widely used in industrial components, automotive parts, and chemical processing equipment. |
Inconel 625 | A high-performance nickel-chromium superalloy renowned for its exceptional strength at high temperatures. | Used in demanding applications like jet engine components, gas turbines, and heat exchangers. |
Cobalt Chrome (CoCr) | A biocompatible alloy valued for its wear resistance and hardness. | A popular choice for hip and knee replacements and other orthopedic implants. |
Aluminum (AlSi10Mg) | A lightweight option with good strength and castability. | Finding applications in automotive parts, aerospace components, and electronic enclosures. |
Copper | An excellent conductor of heat and electricity. | Used for heat sinks, electrical components, and thermal management applications. |
Tungsten | An incredibly dense and heat-resistant metal. | Primarily used for electrodes, ballistic applications, and high-temperature components. |
Molybdenum | A refractory metal with high melting point and good strength at elevated temperatures. | Used in crucible liners, furnace components, and aerospace applications. |
Nickel | A versatile metal with good corrosion resistance and formability. | Often used for electronic components, chemical processing equipment, and electroplating applications. |
Tantalum | A biocompatible and corrosion-resistant metal with a high melting point. | Finding use in capacitors, surgical implants, and chemical processing equipment. |
This list represents just a glimpse into the vast array of EBM metal powders available. Each powder boasts unique properties that cater to specific application needs.
Beyond the Basics: Key Considerations When Choosing EBM Metal Powders
Selecting the right EBM metal powder goes beyond just the base material. Here are some additional factors to consider:
- Particle size and distribution: The size and distribution of the powder particles significantly impact the surface finish, mechanical properties, and overall printability of the final part.
- Flowability: The powder’s ability to flow freely ensures even distribution and optimal layer formation during the printing process.
- Sphericity: Spherical powder particles offer better packing density and minimize voids within the printed part, leading to improved strength.
Powder Purity and EBM Performance
The chemical composition and purity of the EBM metal powder play a crucial role in the final product’s quality. Even minor variations in the powder’s chemistry can significantly impact factors like:
- Mechanical Properties: Impurities can act as weak points within the material, affecting its strength, ductility, and fatigue resistance.
- Microstructure: The presence of unwanted elements can alter the grain size and distribution within the metal, influencing its overall properties.
- Surface Quality: Chemical inconsistencies can lead to surface defects and imperfections on the finished part.
Manufacturers employ strict quality control measures to ensure EBM metal powders meet the highest purity standards. This often involves techniques like:
- Atomization: The process of transforming molten metal into a fine powder using techniques like gas atomization or water atomization. Precise control over the atomization process helps achieve consistent particle size and morphology.
- Sieving and Classification: Powders are meticulously sieved and classified to achieve the desired particle size distribution, optimizing printability and final part properties.
- Chemical Analysis: Rigorous chemical analysis techniques like X-ray fluorescence (XRF) or mass spectrometry ensure the powder meets the specified chemical composition.
The EBM Advantage: A Spectrum of Applications
EBM technology unlocks a treasure trove of benefits for various industries. Here’s a closer look at some of the compelling advantages of EBM and its diverse applications:
Advantages:
- Unmatched Design Freedom: EBM allows for the creation of intricate geometries with internal channels, lattices, and overhangs, often impossible with traditional manufacturing methods.
- High-Performance Parts: EBM produces near-net-shape parts with excellent mechanical properties, including high strength, good fatigue resistance, and superior surface finish.
- Material Versatility: EBM works with a wide range of metals, including reactive materials like titanium and refractory metals like tungsten, expanding design possibilities.
- Minimal Material Waste: Compared to subtractive manufacturing techniques, EBM offers minimal material waste, promoting sustainability and cost-efficiency.
Applications:
- Aerospace: EBM is a game-changer in aerospace, enabling the creation of lightweight, high-strength components for aircraft, satellites, and spacecraft. From complex engine parts to intricate rocket nozzles, EBM pushes the boundaries of aerospace design.
- Medical Implants: The biocompatibility of certain EBM metal powders, like titanium and CoCr, makes them ideal for creating custom-designed medical implants like hip and knee replacements. EBM implants offer excellent osseointegration (bonding with bone) and long-term durability.
- Automotive: The automotive industry is leveraging EBM for high-performance components like lightweight pistons, complex gear designs, and intricate cooling channels in engine blocks. EBM parts contribute to weight reduction and improved fuel efficiency.
- Tooling and Molds: EBM is revolutionizing the creation of complex molds and tooling inserts with intricate shapes and conformal cooling channels. These EBM-produced molds offer superior strength, heat resistance, and improved production efficiency.
- Defense and Security: EBM finds applications in the defense sector for creating high-strength components with intricate designs, such as firearm parts and components for armored vehicles. The technology’s ability to work with specialty alloys further expands its defense applications.
Beyond the Hype: A Look at EBM’s Limitations
While EBM boasts a plethora of advantages, it’s essential to acknowledge its limitations:
- Build Speed: Compared to some other 3D printing methods, EBM can be a slower process due to the high-powered electron beam melting each layer meticulously.
- Machine Cost: EBM systems tend to be expensive compared to other 3D printers. However, the high-performance parts they produce can often justify the initial investment.
- Surface Roughness: While EBM offers good surface finish, some applications might require post-processing techniques for smoother surfaces.
EBM Specifications: A Technical Deep Dive
Metal Powder Properties
Property | Description |
---|---|
Particle size and distribution | The size and distribution of the powder particles significantly impact the surface finish, mechanical properties, and overall printability of the final part. |
Flowability | The powder’s ability to flow freely ensures even distribution and optimal layer formation during the printing process. |
Sphericity | Spherical powder particles offer better packing density and minimize voids within the printed part, leading to improved strength. |
Chemical composition | The chemical makeup of the powder directly influences the final part’s properties like mechanical strength, corrosion resistance, and biocompatibility. |
Purity | Impurities in the powder can negatively impact the final part’s quality. Stringent quality control measures ensure high purity levels. |
EBM System Specifications
Specification | Description |
---|---|
Chamber size (build volume) | The maximum dimensions (length, width, and height) a part can be printed within the EBM system. |
Beam power | The power output of the electron beam, impacting melting depth and overall build speed. |
Accuracy and resolution | The level of detail and dimensional precision achievable by the EBM system. |
Material compatibility | The specific metal powders the EBM system is designed to work with. |
Inert gas atmosphere | The type of inert gas used in the build chamber to prevent oxidation of the molten metal. |
EBM Part Properties
Property | Description |
---|---|
Density | How closely packed the material is within the printed part, typically close to 99.5% of the theoretical density for the chosen metal. |
Mechanical properties | Tensile strength, yield strength, elongation, and fatigue resistance of the printed part. |
Surface roughness | The smoothness of the part’s surface, influenced by factors like powder size and layer thickness. |
Microstructure | The grain size and distribution within the metal, affecting its overall properties. |
Residual stress | Internal stresses present within the part due to the thermal cycling during the printing process. Post-processing techniques can help minimize residual stress. |
Suppliers and Pricing of EBM Metal Powders
The availability and pricing of EBM metal powders vary depending on the specific material, particle size, and supplier. Here’s a general overview:
- Material: Exotic and high-performance alloys like Inconel or tantalum typically command a higher price compared to common materials like titanium or stainless steel.
- Particle size: Finer powders often carry a premium due to the increased processing costs associated with their production.
- Supplier: Reputable manufacturers with stringent quality control measures might have slightly higher prices compared to lesser-known suppliers. However, the guaranteed quality and consistency of the powder justify the cost.
Finding the Right EBM Metal Powder Supplier
When sourcing EBM metal powders, consider these factors:
- Reputation and experience: Choose a supplier with a proven track record in supplying high-quality EBM metal powders.
- Material availability: Ensure the supplier offers the specific metal powder material and particle size required for your application.
- Quality control procedures: Inquire about the supplier’s quality control measures to guarantee the powder’s purity, chemical composition, and consistency.
- Pricing and lead times: Compare pricing from various suppliers and factor in lead times for powder availability.
- Technical support: Look for a supplier that offers technical support to assist you with choosing the right powder and troubleshooting any printing issues.
EBM Pros and Cons: Weighing the Options
Advantages of EBM:
- Unmatched design freedom: Complex geometries, internal features, and intricate lattice structures.
- High-performance parts: Excellent mechanical properties, near-net-shape parts, and superior surface finish.
- Material versatility: Wide range of metals, including reactive and refractory materials.
- Minimal material waste: Sustainable and cost-efficient compared to subtractive manufacturing.
- Biocompatible options: Ideal for medical implants due to biocompatible metal powders.
Limitations of EBM:
- Build speed: Slower process compared to some 3D printing methods.
- Machine cost: EBM systems tend to be expensive.
- Surface roughness: May require post-processing for some applications.
- Limited color options: Typically limited to the natural color of the metal powder.
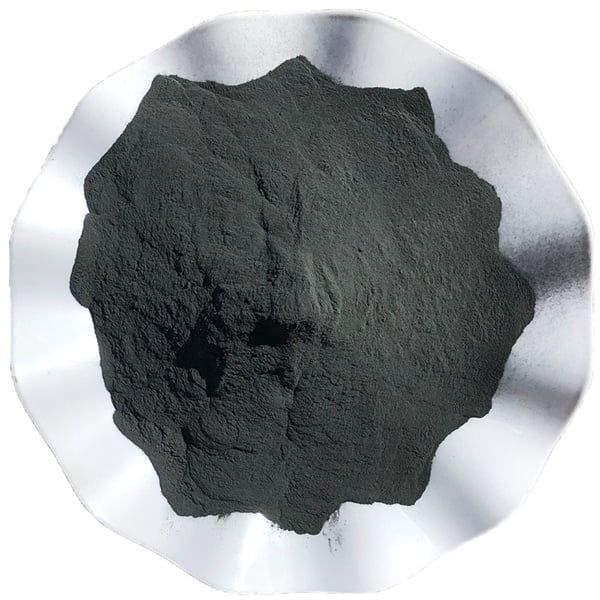
Safety Precautions When Handling EBM Metal Powders
EBM metal powders, like most fine metal particles, can pose health and safety risks if not handled properly. Here are some essential safety precautions to follow:
- Wear personal protective equipment (PPE): This includes safety glasses, gloves, and a respirator to prevent inhalation of powder particles.
- Proper ventilation: Ensure adequate ventilation in the workspace to minimize airborne powder dust.
- Safe handling: Avoid direct skin contact with the powder and minimize airborne dust generation during handling.
- Proper disposal: Dispose of waste powder according to local regulations to avoid environmental contamination.
- Training: Personnel handling EBM metal powders should receive proper training on safe handling procedures.
EBM: A Catalyst for Innovation
EBM technology is rapidly transforming various industries, enabling the creation of complex, high-performance parts that were previously impossible to manufacture. As EBM systems become more affordable and accessible, we can expect even wider adoption and groundbreaking applications across diverse fields. From aerospace components pushing the boundaries of flight to medical implants improving patient lives, EBM is undoubtedly a catalyst for innovation shaping the future of manufacturing.
Share On
MET3DP Technology Co., LTD is a leading provider of additive manufacturing solutions headquartered in Qingdao, China. Our company specializes in 3D printing equipment and high-performance metal powders for industrial applications.
Inquiry to get best price and customized Solution for your business!
Related Articles
About Met3DP
Recent Update
Our Product
CONTACT US
Any questions? Send us message now! We’ll serve your request with a whole team after receiving your message.
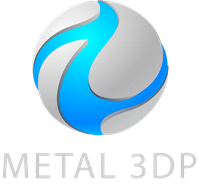
Metal Powders for 3D Printing and Additive Manufacturing