The Difference Between EBM Technology And DMLS Technology
Table of Contents
Imagine building complex metal objects layer by layer, with each layer meticulously fused to create a final, three-dimensional masterpiece. This isn’t science fiction; it’s the magic of metal additive manufacturing, also known as 3D printing. But within this realm of creation lie two titans: Electron Beam Melting (EBM) and Direct Metal Laser Sintering (DMLS). While both utilize metal powders to bring digital designs to life, they differ in their approach, much like two skilled artists wielding different tools. Let’s delve into the intricate dance of these technologies, exploring their nuances and identifying the ideal choice for your next project.
Different Energy Sources
EBM harnesses the power of a focused electron beam, acting like a miniature particle accelerator. This high-energy beam melts metal powder particles within a high-vacuum chamber, creating a molten pool that fuses with surrounding layers. Think of it as a tiny, supercharged paintbrush meticulously melting metal powder to build your design.
On the other hand, DMLS employs a powerful fiber laser as its heat source. This laser beam scans across the metal powder bed, selectively melting particles to form the desired geometry. Imagine using a laser cutter on a sheet of metal powder, but with incredible precision, building the object layer by layer.
Here’s a table summarizing the key differences in energy sources:
Feature | Electron Beam Melting (EBM) | Direct Metal Laser Sintering (DMLS) |
---|---|---|
Energy Source | Electron Beam | High-powered Fiber Laser |
Environment | High-Vacuum Chamber | Inert Gas Atmosphere |
What does this difference mean? The high-vacuum environment of EBM minimizes oxidation, making it ideal for reactive metals like titanium and tantalum. Conversely, DMLS utilizes an inert gas atmosphere, offering a wider range of metal powder compatibility.
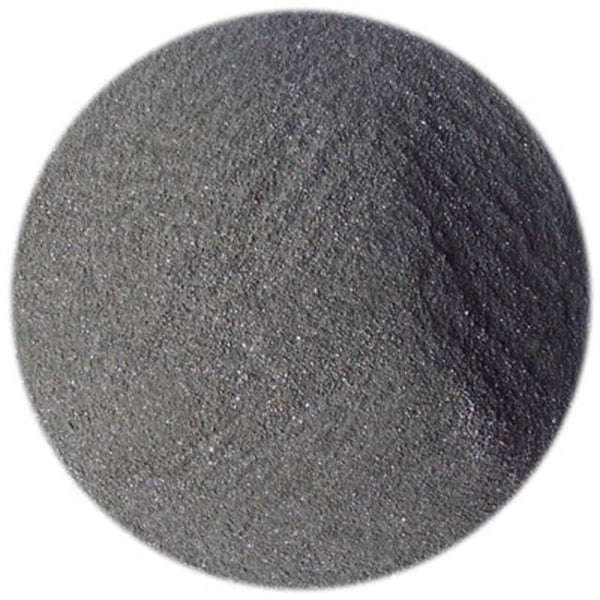
Two Production have different Forming Speed
EBM boasts impressive forming speeds due to the highly focused and powerful electron beam. This translates to faster build times, particularly for larger components. Imagine a skilled artist working swiftly with a powerful tool, completing the artwork in a shorter timeframe.
DMLS, while slower than EBM, offers more precise control over the laser beam. This allows for the creation of intricate features and finer details. Think of a patient artist meticulously carving intricate details with a laser-sharp tool.
Here’s a table summarizing the key differences in forming speed:
Feature | Electron Beam Melting (EBM) | Direct Metal Laser Sintering (DMLS) |
---|---|---|
Forming Speed | Faster | Slower |
Detail Accuracy | Lower | Higher |
The takeaway? If speed is your priority, EBM might be the better choice. However, if intricate details and high-precision features are paramount, DMLS might be the way to go.
The Forming Accuracy is different
As mentioned earlier, DMLS excels in forming accuracy due to the precise control over the laser beam. This allows for the creation of parts with finer features and tighter tolerances. Imagine a master jeweler meticulously crafting a delicate piece of jewelry with pinpoint accuracy.
EBM, while not as precise as DMLS, can still produce parts with good dimensional accuracy. However, due to the nature of the electron beam melting process, the layer thickness tends to be slightly thicker compared to DMLS. Think of a skilled sculptor working with slightly larger tools, resulting in a slightly less precise final product compared to a delicate jeweler.
Here’s a table summarizing the key differences in forming accuracy:
Feature | Electron Beam Melting (EBM) | Direct Metal Laser Sintering (DMLS) |
---|---|---|
Forming Accuracy | Good | Excellent |
Layer Thickness | Slightly Thicker | Thinner |
The bottom line? If dimensional accuracy and intricate features are crucial, DMLS stands out. However, EBM offers sufficient accuracy for many applications, particularly those prioritizing speed over extreme precision.
Materials Used of EBM And DMLS are different
While both technologies utilize metal powders, the specific materials compatible with each system differ slightly.
EBM excels at processing reactive metals like:
- Titanium (Ti): A lightweight and strong metal commonly used in aerospace, medical implants, and high-performance components.
- Tantalum (Ta): A biocompatible and corrosion-resistant metal used in medical implants and chemical processing equipment.
- Zirconium (Zr): A corrosion-resistant metal used in nuclear reactors and chemical processing equipment.
DMLS offers a wider range of compatible materials, including:
Specifications, Sizes, Grades & Standards
Transitioning from a conversational tone to a more professional approach, we’ll delve into the critical world of metal powders used in both EBM and DMLS. These finely-granular materials act as the building blocks for 3D printed metal components, and their characteristics significantly influence the final properties of the part. Unlike its role in baking a cake, where minor variations in flour might affect texture, even slight inconsistencies in metal powders can dramatically impact the strength, surface finish, and overall quality of the printed object. Here’s a comprehensive table outlining key specifications, sizes, grades, and standards for metal powders used in additive manufacturing:
Feature | Description |
---|---|
Particle Size Distribution | Metal powders are meticulously manufactured to achieve specific particle size distributions, typically ranging from 15 to 100 microns. Imagine a precisely calibrated sieve; the chosen particle size directly correlates to the achievable surface finish on the printed part. Finer powders, akin to sifted flour, generate smoother surfaces. However, there’s a crucial trade-off. Powders that are excessively fine can exhibit poorer flowability, hindering their even distribution during the printing process. This can lead to inconsistencies and defects in the final product. Conversely, coarser powders might flow more readily but may result in a rougher surface finish and potential porosity (tiny air gaps) within the printed component. Selecting the optimal particle size distribution necessitates careful consideration of the specific application and desired outcome. |
Particle Morphology | The shape of the powder particles plays a critical role in packing density and flowability. Spherical particles, akin to microscopic ball bearings, are generally preferred for optimal printing performance. They exhibit superior flow characteristics, pack tightly together, and minimize voids within the powder bed. This translates to better dimensional accuracy, improved mechanical properties, and a smoother surface finish on the printed part. However, producing perfectly spherical metal powders can be challenging and expensive. Equiaxed particles, although not perfect spheres, offer a good balance between flowability and packing density. Irregularly shaped particles can be problematic. They can flow poorly, create gaps within the powder bed, and negatively impact the structural integrity of the final product. |
Powder Chemistry | The precise composition of the powder, including trace elements and alloying additions, significantly influences the final properties of the printed part. Just as the exact ingredients in a pharmaceutical formulation determine its efficacy, the chemical makeup of the metal powder dictates the characteristics of the printed component. For instance, titanium powder for aerospace applications might have slightly different levels of oxygen and nitrogen compared to medical-grade titanium powder for implants. These seemingly minor variations can influence factors like strength, corrosion resistance, biocompatibility, and overall performance of the printed part. Metal powder manufacturers employ rigorous quality control measures to ensure their powders meet specific industry standards and application requirements. |
Powder Flowability | The ability of the powder to flow freely is crucial for even distribution during the printing process. Imagine pouring sand for an hourglass; it should flow smoothly and consistently. Good flowability allows for the formation of a uniform powder bed, a critical step in both EBM and DMLS. Powders with poor flowability can cause uneven deposition, leading to inconsistencies and defects in the final printed part. Manufacturers measure flowability using standardized tests to ensure their powders meet the specific requirements of each printing technology. |
Powder Purity | The purity of the metal powder directly affects the mechanical properties and performance of the printed part. Impurities like oxygen, nitrogen, and other elements can hinder the bonding process between metal particles during printing. This can result in weaker parts with increased susceptibility to cracks and fractures. Metal powder manufacturers employ strict quality control measures to minimize impurities and ensure their powders meet the required purity standards for various applications. |
Industry Standards for Metal Powders in Additive Manufacturing:
Several established industry standards govern the specifications and quality of metal powders for additive manufacturing:
- ASTM International (ASTM): A globally recognized organization that develops and publishes technical standards for a wide range of materials, including metal powders for AM. ASTM standards define requirements for particle size distribution, chemical composition, flowability, and other critical parameters.
- American Society for Materials and Testing (AMSTM): A US-based society dedicated to the advancement of testing, materials science, and technologies like additive manufacturing. AMSTM develops specifications and standards for metal powders used in AM processes.
- EOS GmbH: A leading manufacturer of metal 3D printing systems. EOS also publishes application-specific material data sheets for various metal powders, outlining their properties and recommended printing parameters.
- Material Manufacturers: Reputable metal powder suppliers often provide detailed datasheets for their products, including particle size distribution, chemical composition, flowability, and other relevant specifications.
A World of Metal Powders: Unveiling Specific Examples
Now that we’ve explored the key characteristics of metal powders for additive manufacturing, let’s delve into some specific examples commonly used in both EBM and DMLS. This will provide a practical perspective on the available options and their suitability for various applications.
Metal Powders for EBM:
Due to the high-vacuum environment within the EBM chamber, the chosen metal powders need to exhibit exceptional outgassing properties. Outgassing refers to the release of trapped gases within the powder particles during the melting process. Excessive outgassing can disrupt the vacuum environment and negatively impact the quality of the printed part. Here are some commonly used metal powders for EBM:
- Gas-Atomized Titanium Powder (Ti-6Al-4V): This workhorse material is a titanium alloy containing 6% aluminum and 4% vanadium. It offers an excellent combination of strength, weight savings, and corrosion resistance. Widely used in aerospace, medical implants, and high-performance automotive components due to its biocompatibility and favorable mechanical properties when processed via EBM.
- Gas-Atomized Inconel 718: This nickel-chromium-based superalloy boasts exceptional high-temperature strength and resistance to harsh environments. Its ability to withstand extreme temperatures makes it ideal for applications in gas turbine engines, heat exchangers, and other components exposed to high thermal loads. EBM processing offers minimal contamination risk, preserving the desirable properties of Inconel 718.
- Gas-Atomized Copper (Cu): Pure copper powder finds use in applications requiring high thermal and electrical conductivity. EBM allows for the creation of intricate heat sinks and electrical components with minimal oxidation due to the vacuum environment.
Metal Powders for DMLS:
DMLS offers a wider material compatibility compared to EBM due to the inert gas atmosphere. Here are some commonly used metal powders for DMLS:
- Gas-Atomized Stainless Steel 316L: This versatile stainless steel grade offers excellent corrosion resistance and biocompatibility. Widely used in medical implants, chemical processing equipment, and applications requiring resistance to harsh environments. DMLS processing allows for the creation of intricate geometries with good mechanical properties.
- Gas-Atomized Aluminum Alloys (AlSi10Mg, etc.): Aluminum alloys offer a good balance of strength, weight savings, and affordability. The addition of silicon (Si) and magnesium (Mg) improves casting characteristics and mechanical properties. Commonly used in aerospace, automotive, and consumer electronics applications due to their lightweight nature. DMLS processing allows for the creation of complex, lightweight components with good surface finish.
- Gas-Atomized Tool Steel (H13, etc.): Tool steels are known for their exceptional wear resistance and hardness. H13 is a popular choice for molds and dies due to its ability to withstand high temperatures and mechanical stresses. DMLS processing allows for the creation of complex tool inserts with good dimensional accuracy.
Here’s a table summarizing some key characteristics of these metal powders:
Metal Powder | Typical Applications (EBM) | Typical Applications (DMLS) | Key Considerations |
---|---|---|---|
Gas-Atomized Ti-6Al-4V | Aerospace, Medical Implants | Aerospace, Medical Implants | Excellent strength-to-weight ratio, biocompatible |
Gas-Atomized Inconel 718 | Gas Turbine Engines, Heat Exchangers | Gas Turbine Engines, Heat Exchangers | High-temperature strength, resistance to harsh environments |
Gas-Atomized Copper (Cu) | Heat Sinks, Electrical Components | Heat Sinks, Electrical Components | High thermal & electrical conductivity |
Gas-Atomized Stainless Steel 316L | Medical Implants, Chemical Processing | Medical Implants, Chemical Processing | Corrosion resistance, biocompatible |
Gas-Atomized Aluminum Alloys (AlSi10Mg) | Aerospace, Automotive, Consumer Electronics | Aerospace, Automotive, Consumer Electronics | Lightweight, good strength-to-weight ratio |
Gas-Atomized Tool Steel (H13) | Molds & Dies | Molds & Dies | Exceptional wear resistance, hardness |
Remember, this is not an exhaustive list. Manufacturers offer a vast selection of metal powders for additive manufacturing, each with unique properties and certifications. Consulting with reputable metal powder suppliers and understanding your specific application requirements are crucial for selecting the most suitable material for your 3D printing project.
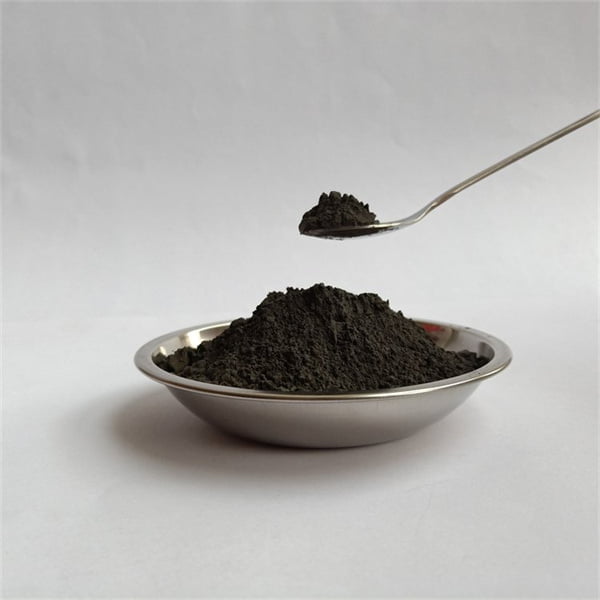
A Comparison of EBM and DMLS
Having explored the intricacies of both EBM and DMLS technologies, along with the world of metal powders used in each process, it’s time to directly compare these two titans of 3D printing. This will help you make an informed decision based on your specific project needs.
Here’s a table summarizing the key differences between EBM and DMLS:
Feature | Electron Beam Melting (EBM) | Direct Metal Laser Sintering (DMLS) |
---|---|---|
Energy Source | Electron Beam | High-powered Fiber Laser |
Environment | High-Vacuum Chamber | Inert Gas Atmosphere |
Forming Speed | Faster | Slower |
Forming Accuracy | Good | Excellent |
Material Compatibility | Limited (Reactive Metals) | Wider Range of Materials |
Surface Finish | Slightly Rougher | Smoother |
Porosity | Lower | Potentially Higher |
Pros | Faster build times, good for reactive metals, minimal oxidation | Higher precision, wider material compatibility, good surface finish |
Cons | Lower accuracy, limited material options, higher energy consumption | Slower build times, potential for higher porosity, may require post-processing for some materials |
Let’s delve deeper into these key differences to understand which technology might be a better fit for your project:
- Build Speed: If speed is a critical factor, EBM might be the better choice. Its high-powered electron beam allows for faster melting and quicker build times, especially for larger components. However, if intricate details and dimensional accuracy are paramount, DMLS might be a better option, even if it takes slightly longer to print.
- Material Compatibility: EBM excels at processing reactive metals like titanium and tantalum due to the high-vacuum environment that minimizes oxidation. DMLS, on the other hand, offers a broader range of material compatibility, including stainless steel, aluminum alloys, and tool steels. This wider selection allows for greater design flexibility in DMLS.
- Part Accuracy and Surface Finish: DMLS reigns supreme in terms of forming accuracy and surface finish. The precise control over the laser beam enables the creation of highly detailed parts with a smooth surface finish. EBM offers good accuracy, but the nature of the electron beam melting process can result in a slightly rougher surface finish compared to DMLS.
- Porosity: Porosity refers to tiny air gaps within the printed metal. EBM generally produces parts with lower porosity due to the high-vacuum environment, which minimizes the presence of trapped gases. DMLS, while offering good overall quality, can have a slightly higher chance of porosity, particularly when using certain materials or printing parameters. In some cases, DMLS parts might require post-processing techniques like hot isostatic pressing (HIP) to eliminate any internal voids.
- Cost Considerations: The cost of 3D printing a metal part using either EBM or DMLS depends on several factors, including the chosen material, part complexity, and required post-processing. However, in general, EBM can have higher energy consumption due to the need for a high-vacuum environment. DMLS might be a more cost-effective option for some applications, especially when considering the potential need for post-processing with EBM.
Choosing the Right Weapon: EBM vs. DMLS – The Final Verdict
There’s no single “winner” in the battle between EBM and DMLS. The ideal technology depends on the specific needs of your project. Here are some concluding thoughts to guide your decision:
- For projects requiring high-speed printing of reactive metals like titanium, and where a slightly rougher surface finish is acceptable, EBM might be a good choice.
- For projects demanding intricate details, exceptional dimensional accuracy, a wider range of material options, and a smooth surface finish, DMLS might be the better option, even if it takes slightly longer to print.
- Carefully consider the cost implications of each technology, including material cost, energy consumption, and potential post-processing needs.
It’s always advisable to consult with experienced 3D printing professionals to discuss your specific project requirements and determine which technology, EBM or DMLS, would be the most suitable choice for optimal results.
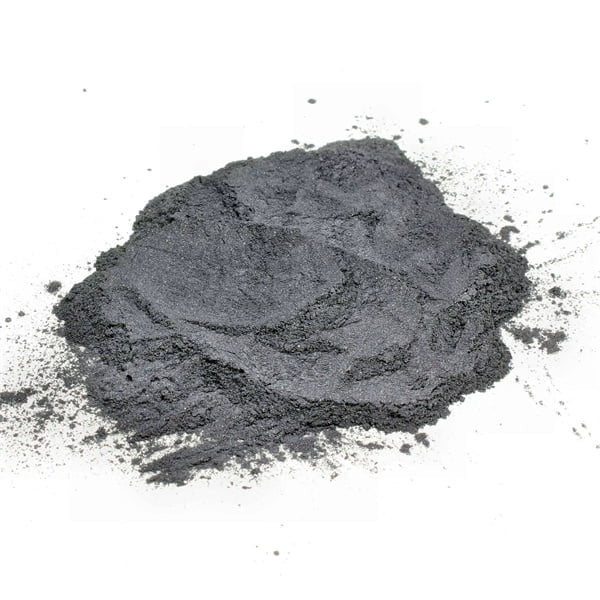
FAQ
Q: Which technology is stronger, EBM or DMLS?
A: Both EBM and DMLS can produce high-strength metal parts. The actual strength depends on the chosen metal powder and the specific printing parameters used. However, due to the high-vacuum environment and potentially lower porosity, EBM-printed parts might exhibit slightly higher strength for certain reactive metals like titanium.
Q: Can I use EBM or DMLS for printing colored metal parts?
A: While both EBM and DMLS primarily focus on creating functional metal parts, there are some limited post-processing techniques that can introduce color to the surface. These techniques typically involve applying a thin layer of colored coating or infiltration with a colored resin. However, achieving vibrant or consistent colors can be challenging, and the long-term durability of such color applications might be limited. If color is a critical requirement, other 3D printing technologies like binder jetting or Multi Jet Fusion might be more suitable, as they offer a wider range of color options directly in the printing process.
Q: Are EBM or DMLS printed parts environmentally friendly?
A: The environmental impact of EBM and DMLS depends on several factors, including the chosen metal powder, energy consumption during the printing process, and any required post-processing steps. Metal powder production itself can be energy-intensive. EBM, due to its high-vacuum environment, might have a slightly higher energy footprint compared to DMLS. However, both technologies offer significant advantages in terms of part complexity and material usage compared to traditional subtractive manufacturing techniques like machining. This can lead to less material waste and potentially a more sustainable manufacturing approach for certain applications.
Q: What are the future advancements expected in EBM and DMLS technologies?
A: The realm of EBM and DMLS is constantly evolving. Here are some exciting possibilities on the horizon:
- Faster printing speeds: Researchers are developing techniques to enhance the speed of both EBM and DMLS without compromising part quality. This could involve advancements in energy source technology or improved powder handling mechanisms.
- Expanded material compatibility: The range of metals suitable for EBM and DMLS printing is expected to grow. This would offer designers even greater flexibility in selecting the optimal material for their specific needs.
- Multi-material printing: Techniques are being explored to enable the printing of parts with different metals or even combinations of metal and other materials within a single build. This could open doors for the creation of highly functional and complex components.
- Improved surface finish: Advancements in laser and electron beam control technology could lead to even smoother surface finishes for DMLS-printed parts, potentially reducing the need for post-processing in some applications.
As these innovative technologies continue to develop, EBM and DMLS are poised to play an increasingly significant role in revolutionizing the way we design and manufacture metal parts across various industries.
Conclusion
The intricate dance between EBM and DMLS technologies offers a powerful toolset for creating complex and functional metal objects. Understanding the strengths and weaknesses of each approach, along with the vast world of metal powders used as building blocks, empowers you to make informed decisions for your 3D printing projects. Whether prioritizing speed for reactive metals with EBM or seeking exceptional detail and a wider material selection with DMLS, both technologies push the boundaries of what’s possible in metal manufacturing. As these technologies continue to evolve, the future holds immense potential for even greater design freedom, material innovation, and a more sustainable approach to metal part creation.
Share On
MET3DP Technology Co., LTD is a leading provider of additive manufacturing solutions headquartered in Qingdao, China. Our company specializes in 3D printing equipment and high-performance metal powders for industrial applications.
Inquiry to get best price and customized Solution for your business!
Related Articles
About Met3DP
Recent Update
Our Product
CONTACT US
Any questions? Send us message now! We’ll serve your request with a whole team after receiving your message.
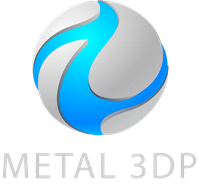
Metal Powders for 3D Printing and Additive Manufacturing