Forging Grade Material
Table of Contents
Forging grade materials are essential in the manufacturing industry, offering unparalleled strength, durability, and precision for various applications. Whether you’re new to the concept or looking to deepen your understanding, this comprehensive guide will walk you through everything you need to know about forging grade materials, their properties, applications, and specific metal powder models.
Overview of Forging Grade Material
Forging grade materials are high-quality metals designed specifically for the forging process. These materials undergo extreme pressure to be shaped into desired forms, resulting in enhanced mechanical properties, such as increased tensile strength, impact resistance, and fatigue life. Common forging materials include various steels, aluminum alloys, titanium, and nickel-based alloys.
Types and Properties of Forging Grade Materials
Material | Composition | Properties | Characteristics |
---|---|---|---|
Carbon Steel | Iron, Carbon (0.05%-1.5%) | High strength, ductility, wear resistance | Cost-effective, widely used, easy to forge |
Alloy Steel | Iron, Carbon, Nickel, Chromium, Molybdenum | Enhanced strength, hardness, toughness, corrosion resistance | Versatile, suitable for high-stress applications |
Stainless Steel | Iron, Carbon, Chromium (min. 10.5%), Nickel | Corrosion resistance, strength, temperature resistance | Aesthetic appeal, high durability, used in corrosive environments |
Aluminum Alloys | Aluminum, Copper, Magnesium, Silicon | Lightweight, high strength-to-weight ratio, corrosion resistance | Excellent for aerospace and automotive industries |
Titanium Alloys | Titanium, Aluminum, Vanadium | Exceptional strength, corrosion resistance, low density | Ideal for aerospace, medical implants, high-performance sports equipment |
Nickel Alloys | Nickel, Chromium, Iron, Molybdenum | High temperature strength, corrosion resistance, oxidation resistance | Used in extreme environments such as turbines, nuclear reactors, and chemical plants |
Tool Steel | Iron, Carbon, Tungsten, Molybdenum, Chromium | High hardness, wear resistance, heat resistance | Essential for cutting tools, molds, and dies |
Copper Alloys | Copper, Zinc (Brass), Tin (Bronze), Nickel | Excellent electrical and thermal conductivity, corrosion resistance | Used in electrical components, marine applications, and decorative items |
Magnesium Alloys | Magnesium, Aluminum, Zinc | Extremely lightweight, good strength-to-weight ratio, corrosion resistance | Applied in automotive, aerospace, and electronics for weight reduction |
Superalloys | Nickel, Chromium, Cobalt | Exceptional strength, heat resistance, corrosion resistance | Critical for aerospace, gas turbines, and high-stress mechanical components |
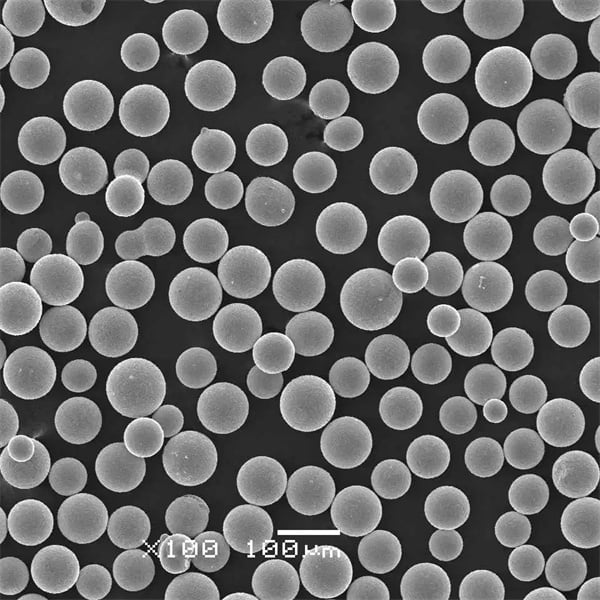
Applications of Forging Grade Materials
Industry | Applications |
---|---|
Automotive | Engine components, transmission parts, axles, gears |
Aerospace | Aircraft frames, turbine blades, landing gear, fasteners |
Construction | Structural beams, bolts, nuts, reinforcement bars |
Medical | Surgical instruments, orthopedic implants, dental prosthetics |
Oil & Gas | Drilling equipment, pipeline fittings, flanges, valves |
Defense | Armored vehicle parts, weapon components, military hardware |
Power Generation | Turbine components, generator parts, nuclear reactor parts |
Marine | Ship hulls, propellers, offshore platform components |
Electronics | Heat sinks, connectors, semiconductor packaging |
Consumer Goods | Hand tools, kitchen utensils, sporting goods |
Specifications, Sizes, Grades, Standards of Forging Grade Materials
Material | Specifications | Sizes | Grades | Standards |
---|---|---|---|---|
Carbon Steel | ASTM A105, AISI 1020 | Bars: 1/2″ to 10″ diameter | 1018, 1045, 1060 | ASTM, SAE, ISO |
Alloy Steel | ASTM A182, AISI 4130 | Bars: 1″ to 12″ diameter | 4140, 4340, 8620 | ASTM, SAE, ISO |
Stainless Steel | ASTM A182, AISI 304, 316 | Bars: 1/4″ to 8″ diameter | 304, 316, 410 | ASTM, SAE, ISO |
Aluminum Alloys | ASTM B221, B209, AA 6061 | Bars: 1/2″ to 6″ diameter | 6061, 7075, 2024 | ASTM, SAE, ISO |
Titanium Alloys | ASTM B348, B381, AMS 4928 | Bars: 1″ to 4″ diameter | Ti-6Al-4V, Ti-3Al-2.5V | ASTM, SAE, ISO, AMS |
Nickel Alloys | ASTM B564, B160, N06625 | Bars: 1″ to 8″ diameter | Inconel 625, 718, Monel 400 | ASTM, SAE, ISO |
Tool Steel | ASTM A681, AISI D2, O1 | Bars: 1/2″ to 6″ diameter | D2, O1, A2, S7 | ASTM, SAE, ISO |
Copper Alloys | ASTM B152, B505, C10100 | Bars: 1/4″ to 4″ diameter | C11000, C17200 | ASTM, SAE, ISO |
Magnesium Alloys | ASTM B107, B94, AZ31 | Bars: 1″ to 4″ diameter | AZ31B, AZ91D | ASTM, SAE, ISO |
Superalloys | ASTM B637, B435, N07718 | Bars: 1″ to 6″ diameter | Inconel 718, Hastelloy C276 | ASTM, SAE, ISO |
Suppliers and Pricing Details of Forging Grade Materials
Supplier | Materials Offered | Pricing (Per Kg) | Location |
---|---|---|---|
Thyssenkrupp Materials | Carbon Steel, Alloy Steel, Stainless Steel | $1.5 – $3.0 | Global |
ArcelorMittal | Carbon Steel, Alloy Steel, Tool Steel | $1.4 – $2.8 | Global |
Boehler Edelstahl | Tool Steel, Stainless Steel, Nickel Alloys | $3.0 – $6.0 | Europe, North America |
ATI Metals | Titanium Alloys, Nickel Alloys, Stainless Steel | $6.5 – $12.0 | Global |
Alcoa | Aluminum Alloys, Nickel Alloys | $2.5 – $5.5 | Global |
Carpenter Technology | Superalloys, Titanium Alloys, Stainless Steel | $7.0 – $15.0 | Global |
Materion Corporation | Copper Alloys, Specialty Alloys | $4.0 – $8.0 | Global |
H.C. Starck | Nickel Alloys, Titanium Alloys, Superalloys | $8.0 – $18.0 | Global |
Sandvik Materials | Stainless Steel, Alloy Steel, Tool Steel | $2.0 – $4.5 | Global |
Precision Castparts Corp | Superalloys, Titanium Alloys, Nickel Alloys | $8.5 – $20.0 | North America, Europe |
Pros and Cons of Forging Grade Materials
Material | Advantages | Disadvantages |
---|---|---|
Carbon Steel | High strength, cost-effective, easy to forge | Lower corrosion resistance compared to stainless steel |
Alloy Steel | Enhanced mechanical properties, versatile | Higher cost than carbon steel |
Stainless Steel | Excellent corrosion resistance, aesthetic appeal | Higher cost, difficulty in forging due to high work hardening rate |
Aluminum Alloys | Lightweight, good strength-to-weight ratio, corrosion resistance | Lower strength compared to steel, higher cost |
Titanium Alloys | Exceptional strength, corrosion resistance, biocompatibility | Very high cost, difficult to forge |
Nickel Alloys | High temperature strength, excellent corrosion resistance | Very high cost, difficulty in forging |
Tool Steel | High hardness, wear resistance, heat resistance | High cost, difficulty in machining and forging |
Copper Alloys | Excellent electrical and thermal conductivity, corrosion resistance | Lower strength, higher cost than common steels |
Magnesium Alloys | Extremely lightweight, good strength-to-weight ratio, corrosion resistance | Lower strength, flammability concerns during machining |
Superalloys | Exceptional mechanical properties at high temperatures | Extremely high cost, very difficult to forge |
Specific Metal Powder Models for Forging Grade Materials
- Carbon Steel Powder AISI 1018
- Composition: Iron, Carbon (0.18%)
- Properties: Good machinability, high strength, ductility
- Applications: Automotive parts, gears, shafts
- Alloy Steel Powder AISI 4140
- Composition: Iron, Carbon, Chromium, Molybdenum
- Properties: High strength, toughness, good fatigue resistance
- Applications: Aircraft components, downhole tools, gears
- Stainless Steel Powder 316L
- Composition: Iron, Chromium (16-18%), Nickel (10-14%), Molybdenum (2-3%)
- Properties: Superior corrosion resistance, high strength
- Applications: Medical implants, marine hardware, chemical processing equipment
- Aluminum Alloy Powder 6061
- Composition: Aluminum, Magnesium (0.8-1.2%), Silicon (0.4-0.8%)
- Properties: Good mechanical properties, excellent corrosion resistance
- Applications: Aerospace components, automotive parts, structural applications
- Titanium Alloy Powder Ti-6Al-4V
- Composition: Titanium, Aluminum (6%), Vanadium (4%)
- Properties: High strength, lightweight, corrosion resistance
- Applications: Aerospace parts, medical implants, high-performance automotive components
- Nickel Alloy Powder Inconel 718
- Composition: Nickel, Chromium, Iron, Molybdenum
- Properties: High temperature strength, corrosion resistance
- Applications: Turbine blades, nuclear reactors, oil & gas industry components
- Tool Steel Powder AISI D2
- Composition: Iron, Carbon, Chromium, Vanadium
- Properties: High wear resistance, toughness, heat resistance
- Applications: Cutting tools, dies, molds
- Copper Alloy Powder C11000
- Composition: Copper (99.99%)
- Properties: Excellent electrical conductivity, corrosion resistance
- Applications: Electrical connectors, heat exchangers, marine components
- Magnesium Alloy Powder AZ31B
- Composition: Magnesium, Aluminum, Zinc
- Properties: Lightweight, good strength-to-weight ratio, corrosion resistance
- Applications: Automotive parts, aerospace components, electronic housings
- Superalloy Powder Hastelloy X
- Composition: Nickel, Chromium, Iron, Molybdenum
- Properties: High temperature strength, oxidation resistance
- Applications: Gas turbine components, industrial furnace parts, chemical processing equipment
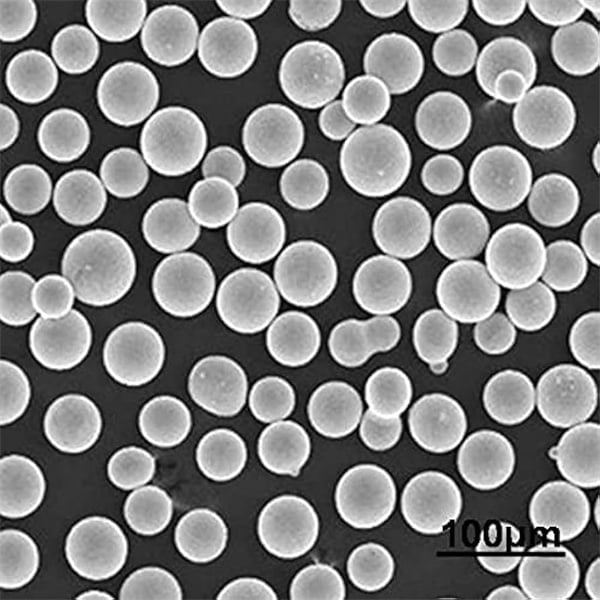
Comparing Advantages and Limitations of Forging Grade Materials
Material | Advantages | Limitations |
---|---|---|
Carbon Steel | Affordable, widely available, high strength | Prone to rust without coating or treatment, lower corrosion resistance compared to stainless steel |
Alloy Steel | Better mechanical properties than carbon steel, suitable for high-stress applications | Higher cost than carbon steel, may require heat treatment for optimal properties |
Stainless Steel | Excellent corrosion resistance, long-lasting, aesthetically pleasing | More expensive, challenging to work with due to work hardening properties |
Aluminum Alloys | Lightweight, good corrosion resistance, easy to machine | Lower strength compared to steel, more expensive |
Titanium Alloys | Extremely strong, lightweight, excellent corrosion resistance, biocompatible | Very expensive, difficult to forge and machine |
Nickel Alloys | Exceptional performance at high temperatures, excellent corrosion resistance | Extremely expensive, difficult to work with |
Tool Steel | High hardness and wear resistance, essential for tool making | High cost, can be brittle, challenging to machine |
Copper Alloys | Excellent electrical and thermal conductivity, good corrosion resistance | Not as strong as other forging materials, more expensive |
Magnesium Alloys | Extremely lightweight, good mechanical properties | Lower strength, more challenging to handle due to flammability concerns during machining |
Superalloys | Outstanding performance in extreme conditions, high temperature and corrosion resistance | Very high cost, very difficult to forge and machine |
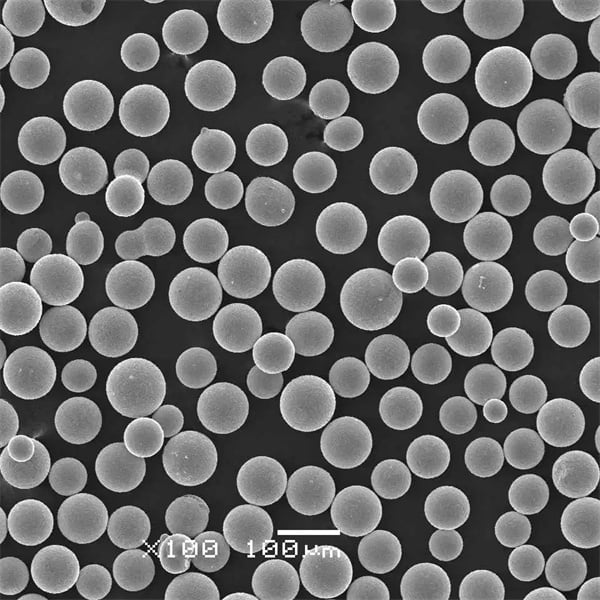
FAQs
Question | Answer |
---|---|
What are forging grade materials? | Forging grade materials are high-quality metals specifically designed for the forging process, providing enhanced mechanical properties. |
Why is carbon steel popular in forging? | Carbon steel is popular due to its high strength, cost-effectiveness, and ease of forging. |
What makes titanium alloys suitable for aerospace? | Titanium alloys offer exceptional strength, lightweight, and corrosion resistance, making them ideal for aerospace applications. |
Are aluminum alloys better than steel for automotive parts? | Aluminum alloys are better in terms of weight reduction and corrosion resistance, but steel provides higher strength. |
How are superalloys used in extreme environments? | Superalloys are designed to maintain high strength and corrosion resistance at very high temperatures, making them suitable for turbines and reactors. |
Can stainless steel be forged easily? | Stainless steel can be challenging to forge due to its work hardening properties, but it offers excellent corrosion resistance and strength. |
What are the main advantages of alloy steel? | Alloy steel provides enhanced strength, toughness, and resistance to wear and corrosion, making it suitable for demanding applications. |
How is copper alloy powder used in electronics? | Copper alloy powder is used in electronics for its excellent electrical and thermal conductivity, essential for connectors and heat exchangers. |
Why are magnesium alloys used in aerospace? | Magnesium alloys are extremely lightweight, providing significant weight savings, which is crucial in aerospace applications. |
What are the cost implications of using superalloys? | Superalloys are very expensive due to their complex composition and superior properties, but they are essential for high-performance applications in extreme conditions. |
Conclusion
Forging grade materials play a pivotal role in modern manufacturing, offering unmatched strength, durability, and performance for a wide range of applications. From the automotive and aerospace industries to medical and electronics fields, these materials are essential for producing high-quality, reliable components. By understanding the specific properties, advantages, and limitations of different forging grade materials, manufacturers can make informed decisions to optimize their production processes and achieve the best results.
Share On
MET3DP Technology Co., LTD is a leading provider of additive manufacturing solutions headquartered in Qingdao, China. Our company specializes in 3D printing equipment and high-performance metal powders for industrial applications.
Inquiry to get best price and customized Solution for your business!
Related Articles
About Met3DP
Recent Update
Our Product
CONTACT US
Any questions? Send us message now! We’ll serve your request with a whole team after receiving your message.
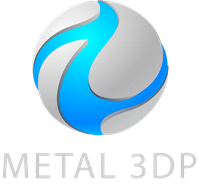
Metal Powders for 3D Printing and Additive Manufacturing