Gas Atomization:High-Quality 3D Printing Metal Powders
Table of Contents
Imagine a world where crafting intricate metal objects is no longer confined to factories and massive machinery. A world where you, with the click of a button and a pinch of magic dust (well, almost), can materialize custom-designed metal parts right in your workshop or even your home. This, my friend, is the power of 3D printing technology, and gas atomization plays a crucial role in making this futuristic vision a reality.
But before we delve deeper into the fascinating world of gas atomized metal powders, let’s take a step back and understand the critical role they play in 3D printing.
The Building Blocks of 3D Printing Metal Powders
Think of 3D printing for metals as akin to baking a delicious cake. Just like a cake requires the perfect blend of flour, sugar, and other ingredients, successful 3D printing relies heavily on the quality of the “building blocks” used – in this case, metal powders. These fine, metallic particles are meticulously layered upon each other during the printing process, gradually forming the desired 3D object.
However, not all metal powders are created equal. Traditional methods of powder production often result in irregularly shaped particles, leading to inconsistencies in the printing process and the final product. This is where gas atomization steps in as a game-changer.
Detailed Process of Gas Atomization: Transforming Molten Metal into Perfect Spheres
Imagine a molten pot of metal, brimming with potential. Gas atomization takes this molten metal and, through a series of precisely controlled steps, transforms it into a cascade of perfectly spherical metal particles. Here’s a glimpse into the magic behind this process:
- Melting: The chosen metal is heated to its melting point, transforming it from a solid state into a liquid form.
- Atomization: The molten metal is then forced through a narrow nozzle under high pressure. This creates a thin stream of liquid metal that breaks up into tiny droplets due to the force of the gas, typically nitrogen or argon.
- Rapid Solidification: As these droplets fall through a cooling chamber, they rapidly solidify in mid-air, forming near-perfect spheres. This rapid cooling process helps to trap any unwanted gases within the metal, preventing the formation of internal defects.
- Collection and Sieving: The cooled metal spheres are then collected and sieved to achieve the desired particle size distribution, catering to specific 3D printing requirements.
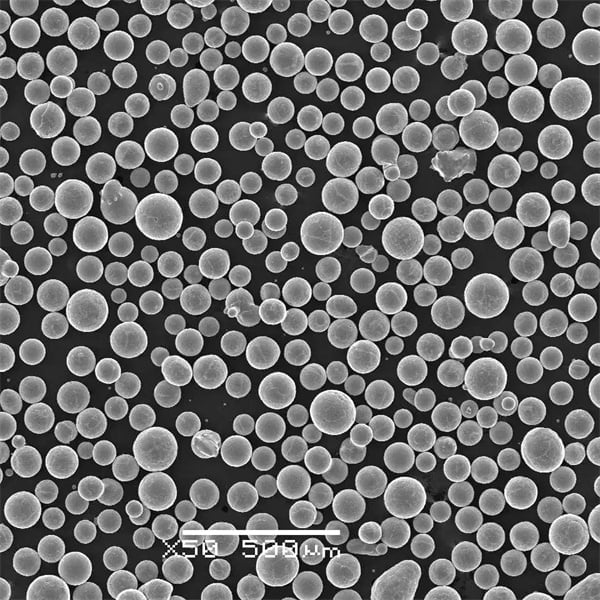
Why Gas Atomization Can Produce High-Quality 3D Printing Metal Powders: A Winning Formula
So, what makes gas atomized metal powders the gold standard for 3D printing? Here are some key reasons:
- Spherical Shape: Unlike irregularly shaped particles, the near-perfect spheres produced through gas atomization ensure smooth flowability during the printing process. This allows for consistent layer formation and ultimately, a stronger and more uniform final product.
- High Density: The rapid solidification process in gas atomization minimizes the formation of internal voids, leading to denser metal powders. This translates to stronger and more durable 3D printed parts.
- Controlled Particle Size Distribution: By adjusting the process parameters, gas atomization allows for the production of powders with a narrow and precise particle size distribution. This is crucial for achieving optimal packing density during printing, ensuring consistent material properties throughout the 3D printed object.
- Improved Flowability: The smooth, spherical shape and narrow size distribution of gas atomized powders contribute to superior flowability. This translates to efficient powder handling during the printing process, which minimizes waste and ensures consistent printing quality.
- Reduced Impurities: The controlled atmosphere of the gas atomization process helps to minimize the introduction of impurities into the metal powder. This leads to cleaner and higher-purity final products with improved mechanical properties.
Simply put, gas atomization delivers the perfect combination of size, shape, density, and flowability, making it the preferred method for producing high-quality metal powders for 3D printing.
Comparison of Gas Atomization with Other Metal Powder Production Techniques:
Technique | Advantages | Disadvantages |
---|---|---|
Gas Atomization | Spherical shape, high density, controlled particle size, improved flowability, reduced impurities | High energy consumption, relatively expensive |
Water Atomization | Lower cost | Irregularly shaped particles, lower density, wider size distribution, higher oxygen content |
Crushing and Milling | Can handle a wider range of materials | Irregularly shaped particles, broad size distribution, potential contamination |
Applications of Gas Atomized Metal Powders: Where the Magic Happens
The exceptional qualities of gas atomized metal powders have opened doors to a vast and ever-expanding world of applications in 3D printing. Here are some prominent examples:
Aerospace & Defense: The demanding requirements of the aerospace and defense industries necessitate lightweight yet robust materials. Gas atomized metal powders, particularly those made of titanium alloys, aluminum alloys, and Inconel, are extensively used in the production of:
- Aircraft components: Engine parts, landing gear components, and lightweight airframes.
- Spacecraft components: Rocket engine parts, satellite structures, and heat shields.
- Defense applications: Armor components, weapon systems, and drone parts.
Medical & Dental: The biocompatible nature of certain gas atomized metal powders, such as titanium and cobalt-chromium, has revolutionized the medical and dental fields. These powders are used in the creation of:
- Prosthetic implants: Hip and knee replacements, dental implants, and cranial implants.
- Surgical instruments: Custom-designed surgical tools with intricate geometries.
- Biomedical devices: Bone screws, plates, and other implants for bone repair and reconstruction.
Automotive: The automotive industry is constantly striving for lighter and more fuel-efficient vehicles. Gas atomized metal powders, including aluminum alloys, magnesium alloys, and steel alloys, are finding increasing use in the production of:
- Engine components: Pistons, connecting rods, and cylinder heads.
- Body panels: Lightweight and crash-resistant components.
- Electric vehicle components: Battery casings and heat sinks.
Consumer Goods: Beyond industrial applications, gas atomized metal powders are making their way into the consumer goods market as well. Examples include:
- Sporting goods: Custom-designed golf clubs, bicycle frames, and sports equipment.
- Jewelry: Intricate and personalized jewelry pieces with unique designs.
- Consumer electronics: Lightweight and heat-dissipating components for electronics.
These are just a few examples, and as 3D printing technology continues to evolve, we can expect to see even more innovative applications for gas atomized metal powders emerge in the future.
Specifications and Standards: Understanding the Numbers Game
When it comes to gas atomized metal powders, several factors like particle size, size distribution, and chemical composition are critically important. These factors directly impact the printability and performance of 3D printed parts. Here’s a breakdown of some key specifications and standards:
Particle Size:
- Measured in micrometers (µm)
- Affects flowability, packing density, and surface finish of the printed part
- Typically ranges from 10 µm to 150 µm for 3D printing applications
Size Distribution:
- Measured by the distribution of particle sizes within the powder
- Ideally, a narrow size distribution leads to better packing density and consistent material properties
- Often expressed using statistical methods like D10, D50, and D90, which represent the size at which 10%, 50%, and 90% of the particles are smaller, respectively.
Chemical Composition:
- Expressed as the percentage of different elements present in the powder
- Varies depending on the desired material properties
- Needs to adhere to specific industry standards to ensure compatibility with 3D printing processes and desired final product properties.
Standards:
- Several international and national standards govern the production and properties of gas atomized metal powders for 3D printing.
- Examples include ASTM International (ASTM) and the International Organization for Standardization (ISO).
- These standards define requirements for particle size, size distribution, chemical composition, and other important parameters.
It’s crucial to choose gas atomized metal powders that meet the specific requirements of your intended 3D printing application. Consulting with a qualified supplier and adhering to relevant standards can ensure the success of your 3D printing project.
Suppliers and Pricing: Finding the Right Partner for Your 3D Printing
The global market for gas atomized metal powders is experiencing significant growth, driven by the increasing adoption of 3D printing technology. Here’s a glimpse into the supplier landscape and pricing considerations:
Suppliers:
- Numerous companies worldwide specialize in the production and supply of gas atomized metal powders.
- These suppliers offer a wide range of materials, including common metals like titanium, aluminum, and steel, as well as more exotic materials like nickel alloys and precious metals.
- Choosing the right supplier depends on factors like the specific material needed, required powder specifications, and desired delivery volumes.
Pricing:
- The price of gas atomized metal powders can vary significantly depending on several factors:
- Material: Exotic materials like precious metals typically command higher prices compared to common metals.
- Particle size and size distribution: Powders
Pros and Cons of Gas Atomized Metal Powders: Weighing the Options
While gas atomization offers numerous advantages for 3D printing applications, it’s essential to be aware of its limitations as well.
Pros:
- Superior powder characteristics: Spherical shape, high density, controlled particle size distribution, and improved flowability contribute to consistent and high-quality 3D printed parts.
- Wide range of materials: Gas atomization can handle a vast array of metals, including exotic and high-performance alloys, expanding the design possibilities for 3D printing.
- Reduced waste: The controlled nature of the gas atomization process minimizes powder waste, leading to increased efficiency and cost-effectiveness.
- Improved mechanical properties: The superior powder characteristics translate to stronger, more durable, and fatigue-resistant 3D printed parts.
Cons:
- Higher cost: Compared to other powder production methods, gas atomization requires a significant investment in equipment and operation, making the powders more expensive.
- Energy consumption: The process is energy-intensive, contributing to a higher environmental footprint.
- Limited production capacity: Compared to some alternative methods, gas atomization has a lower production capacity, making it less suitable for large-scale applications.
Ultimately, the decision of whether to use gas atomized metal powders depends on your specific needs and priorities. If you require high-quality, precision parts and can justify the higher cost, gas atomization is an excellent choice. However, if cost is a major concern or you need large volumes of powder, alternative methods might be worth exploring.
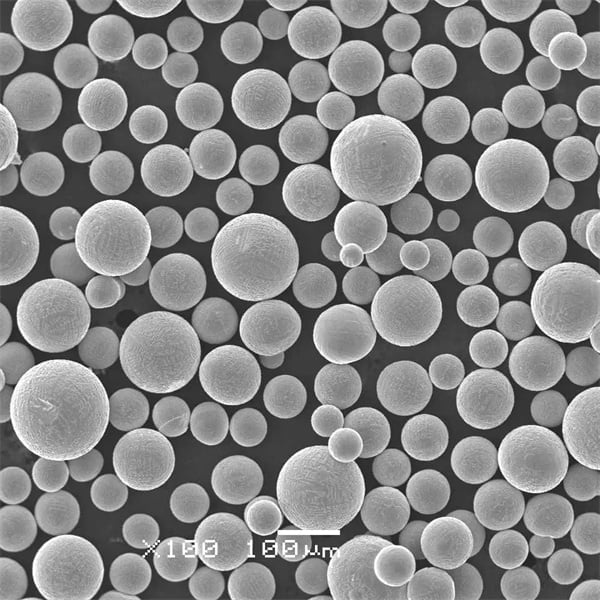
FAQ
Q: What are the different types of gas atomization used for metal powders?
There are two main types of gas atomization used for metal powders:
- Inert Gas Atomization: This method utilizes inert gases like nitrogen or argon to prevent oxidation during the atomization process.
- Vacuum Atomization: This method takes place in a vacuum chamber, minimizing contamination and allowing for the production of highly pure metal powders.
Q: Can gas atomized metal powders be recycled?
Yes, gas atomized metal powders can be recycled to a certain extent. However, the recycling process may introduce impurities and affect the powder properties. The feasibility of recycling depends on various factors, including the specific material and the intended application of the recycled powder.
Q: What are the future trends for gas atomization in 3D printing?
The future of gas atomization in 3D printing is expected to be driven by several trends:
- Development of new and improved atomization technology: This will lead to increased production efficiency, lower costs, and the ability to produce even finer and more precise powders.
- Expansion into new material applications: Advancements in gas atomization technology will enable the production of powders from a wider range of materials, opening doors to innovative 3D printing applications.
- Growing adoption of 3D printing: As 3D printing technology becomes more widespread, the demand for high-quality metal powders like those produced through gas atomization is expected to rise significantly.
In conclusion, gas atomization stands as a cornerstone technology in the realm of 3D printing for metal. Its ability to produce high-quality, spherical metal powders with exceptional characteristics paves the way for the creation of robust, intricate, and innovative 3D printed parts across diverse industries. As technology continues to evolve and the demand for 3D printing grows, gas atomization is poised to play a vital role in shaping the future of this transformative technology.
Share On
MET3DP Technology Co., LTD is a leading provider of additive manufacturing solutions headquartered in Qingdao, China. Our company specializes in 3D printing equipment and high-performance metal powders for industrial applications.
Inquiry to get best price and customized Solution for your business!
Related Articles
About Met3DP
Recent Update
Our Product
CONTACT US
Any questions? Send us message now! We’ll serve your request with a whole team after receiving your message.
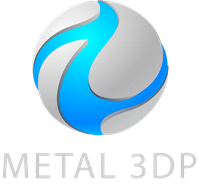
Metal Powders for 3D Printing and Additive Manufacturing