Gas Atomization
Table of Contents
Have you ever wondered how those intricate parts in your car engine or the lightweight components in your laptop are made? The answer might lie in a fascinating process called gas atomization, a technology that transforms molten metal into a sea of tiny, perfectly-shaped spheres – metal powders. Buckle up, because we’re diving deep into the world of gas atomization, exploring its intricacies, the wonders it creates, and how it shapes the world around us.
Process Principle of Gas Atomization
Imagine a molten metal stream, hot and fiery, like lava flowing from a volcano. In gas atomization, this molten metal meets its match – a high-velocity gas jet, typically nitrogen or argon. This jet, moving at supersonic speeds, collides with the metal stream, shattering it into a fine mist of droplets. These droplets, suspended in mid-air, rapidly cool and solidify into individual metal powder particles.
The key to this process lies in the finesse of the gas jet. By carefully controlling its pressure and flow rate, engineers can manipulate the size and distribution of the resulting powder particles. Think of it like adjusting the spray on a garden hose – a wide spray creates larger droplets, while a concentrated stream produces finer ones. This control allows for the creation of metal powders with specific properties, tailored for various applications.
Process Characteristics of Gas Atomization
Gas atomization boasts several advantages that make it a preferred method for producing high-quality metal powders. Here’s a closer look at what sets it apart:
- Highly Spherical Powders: Unlike other methods that can produce irregularly shaped particles, gas atomization yields near-perfect spheres. These spherical shapes offer several benefits, including:
- Improved Flowability: Spherical particles flow freely, making them ideal for automated powder handling systems used in additive manufacturing (3D printing) and metal injection molding (MIM).
- Packing Density: Spheres pack together more efficiently, allowing for a higher powder volume in a given space. This translates to better material utilization and potentially lower overall costs.
- Uniform Properties: Spherical particles have a more consistent surface area-to-volume ratio, leading to more predictable material behavior during processing.
- Tight Control Over Particle Size: As mentioned earlier, the gas jet allows for precise control over particle size distribution. This is crucial for various applications. For instance, finer powders are better suited for intricate 3D printing jobs, while coarser powders might be preferred for thermal spraying processes.
- High Purity: Gas atomization takes place in a controlled environment, minimizing contamination from the surrounding atmosphere. This results in high-purity metal powders, essential for applications demanding exceptional material properties.
- Scalability: Gas atomization systems can be designed for various production capacities, making them suitable for both small-scale research and development projects and large-scale industrial production.
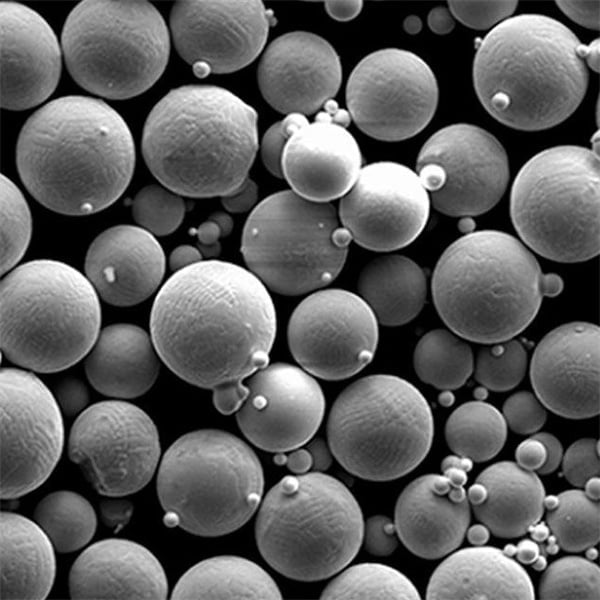
Unveiling the Metal Powder Menagerie
Gas atomization breathes life into a diverse range of metal powders, each with unique properties and applications. Let’s delve into the fascinating world of these microscopic marvels:
- Stainless Steel Powders (316L, 17-4PH): The workhorses of the metal powder world, these versatile powders offer excellent corrosion resistance, making them ideal for applications in the medical, aerospace, and automotive industries.
- Titanium Powders (Ti-6Al-4V, Grade 2): Renowned for their high strength-to-weight ratio and biocompatibility, titanium powders are extensively used in aerospace components, medical implants, and sporting goods.
- Nickel-based Superalloy Powders (Inconel 625, Inconel 718): These high-performance alloys can withstand extreme temperatures and harsh environments, making them perfect for jet engine components, turbine blades, and other demanding applications.
- Aluminum Powders (AlSi10Mg, AA2024): Offering a good balance of strength, weight, and formability, aluminum powders are finding increasing use in automotive components, aerospace structures, and consumer electronics.
- Copper Powders: With their excellent electrical conductivity and thermal properties, copper powders are used in electrical connectors, heat sinks, and even for creating conductive tracks in 3D printed circuits.
- Tool Steel Powders (H13, AISI M2): These hard and wear-resistant powders are ideal for creating cutting tools, molds, and dies that can withstand high pressures and abrasive environments.
- Cobalt Chrome Powders (CoCrMo): Biocompatible and wear-resistant, these powders are increasingly used in manufacturing prosthetics and other medical implants.
- Tungsten Powders: Known for their high density and melting point, tungsten powders are used in a variety of applications, including:
- Molybdenum Powders: Similar to tungsten, molybdenum powders offer excellent high-temperature performance and are used in:
- Heating elements: Their ability to withstand extreme heat makes them ideal for furnace components.
- Electronic applications: Used in electrodes and other components due to their good electrical conductivity.
- Missile components: Their high melting point makes them suitable for parts exposed to high temperatures.
- Precious Metal Powders (Gold, Silver, Platinum): Finely crafted gas-atomized powders of these precious metals find applications in:
- Jewelry manufacturing: Used for creating intricate and delicate jewelry pieces through 3D printing or MIM.
- Electronics: Employed in electrical contacts and other components due to their superior conductivity.
- Biomedical devices: Used for their biocompatibility and corrosion resistance in certain medical implants.
A Note on Variety: This list merely scratches the surface of the vast array of metal powders produced via gas atomization. From specialty alloys for nuclear reactors to exotic materials for aerospace applications, the possibilities are constantly expanding.
Applications of Gas Atomized Powders
Gas-atomized metal powders are revolutionizing various industries by enabling the creation of complex and high-performance components. Here’s a glimpse into some of their key applications:
Application Area | Description | Example |
---|---|---|
Additive Manufacturing (3D Printing) | Powders are used to build intricate 3D objects layer-by-layer. | Lightweight aircraft components, complex medical implants, customized prosthetics. |
Metal Injection Molding (MIM) | Powders are mixed with a binder, molded into desired shapes, and then debindered and sintered. | Gears, small engine components, intricate electronic parts. |
Thermal Spraying | Powders are melted and sprayed onto surfaces to create coatings with specific properties. | Wear-resistant coatings for machine components, corrosion-resistant coatings for pipes, thermal barrier coatings for engines. |
Cold Spraying | Powders are accelerated at high velocities and deposited onto a substrate in a solid state, creating dense coatings. | Repairing damaged parts, creating conductive layers for electronics. |
Beyond the Obvious: Gas atomized powders are also finding their way into some surprising applications. For instance, they’re used in:
- Catalytic converters: Certain metal powders act as catalysts to reduce harmful emissions in car exhaust.
- Pyrotechnics: Specific powders can create vibrant colors and effects in fireworks displays.
- Dental fillings: Specialized metal powders can be used to create strong and durable dental fillings.
The versatility of gas-atomized powders is truly remarkable, and their applications continue to expand as technology advances.
Specifications, Sizes, Grades, and Standards
When it comes to gas-atomized metal powders, a world of specifications, sizes, grades, and standards exists. Here’s a breakdown to help you navigate this intricate landscape:
Factor | Description | Example |
---|---|---|
Particle Size | Measured in microns (µm) and typically ranging from 4 to 150 µm. | Stainless steel 316L powder: 15-45 µm for 3D printing, 45-100 µm for thermal spraying. |
Particle Size Distribution (PSD) | Indicates the spread of particle sizes within a powder batch. | A narrow PSD is preferred for some applications, while a broader one might be suitable for others. |
Apparent Density | The bulk density of the powder, measured in grams per cubic centimeter (g/cm³). | Influences powder handling and flowability. |
Flowability | The ease with which powder flows. | Crucial for automated powder handling systems. |
Chemical Composition | The specific elements and their weight percentages in the powder. | Must meet specific industry standards for optimal performance. |
Grade | Indicates the level of purity and additional elements present in the powder. | Higher grades offer better performance but might come at a higher cost. |
Standards | Industry-established guidelines for powder properties, ensuring consistency and quality. | Examples include ASTM International (ASTM) and International Organization for Standardization (ISO) standards. |
Understanding the Nuances: The specific requirements for particle size, size distribution, and other properties will vary depending on the intended application. For instance, powders used in 3D printing often require a tighter size distribution for consistent layer formation, while thermal spraying might allow for a broader range of particle sizes.
Material Safety Data Sheet (MSDS): It’s crucial to consult the MSDS for any gas-atomized metal powder before handling it. The MSDS provides information on the powder’s safety hazards, handling precautions, and disposal guidelines.
Suppliers and Pricing
The global market for gas-atomized metal powders is vast and ever-evolving. Here’s a look at some key players and pricing considerations:
Supplier | Reputation | Material Focus | Example Pricing (per kg) |
---|---|---|---|
Höganäs AB (Sweden) | Leading global supplier | Wide range of metal powders | Stainless steel 316L: $15-25 |
AP Powder Company (USA) | Renowned for high-purity powders | Titanium, aluminum, nickel alloys | Titanium Ti-6Al-4V: $40-60 |
Norsk Hydro (Norway) | Major supplier of aluminum powders | Aluminum powders for various applications | Aluminum AA2024: $10-15 |
Carpenter Additive (USA) | Focus on specialty powders for additive manufacturing | Nickel-based superalloys, tool steels | Inconel 625: $50-70 |
Pricing Nuances: The price of gas-atomized metal powders can vary significantly depending on several factors, including:
- Material type: Exotic and high-performance materials like titanium and nickel alloys generally command a higher price than common metals like aluminum.
- Powder purity: Higher purity grades typically come at a premium.
- Particle size and distribution: Powders with tighter size control might be more expensive.
- Order quantity: Bulk purchases often negotiate lower prices compared to smaller orders.
Finding the Right Supplier: When selecting a gas-atomized metal powder supplier, consider factors like the company’s reputation, material expertise, quality control procedures, and pricing competitiveness. It’s also important to ensure the supplier offers the specific powder type, size, and grade required for your application.
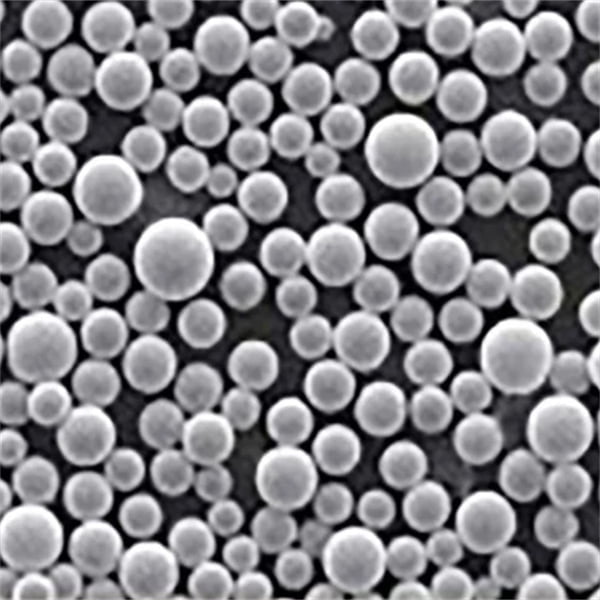
Pros and Cons of Gas Atomization
Gas atomization offers a multitude of advantages, but it’s not without limitations. Here’s a balanced perspective:
Advantage | Description |
---|---|
High-quality powders: Produces spherical powders with consistent properties. | High capital cost: Setting up a gas atomization system requires a significant initial investment. |
Tight control over size: Allows for precise control over particle size distribution. | Energy consumption: The process can be energy-intensive. |
Scalability: Systems can be designed for various production capacities. | Limited material selection: Not all metals are suitable for gas atomization. |
High purity: Minimizes contamination for demanding applications. | Environmental considerations: Proper dust collection and waste management are essential. |
Making an Informed Decision: Gas atomization is a powerful tool for producing high-quality metal powders. However, it’s essential to weigh the advantages and disadvantages against your specific needs and budget constraints. Consider consulting with a gas atomization expert to determine if this process is the right fit for your application.
FAQ
Q: What are the advantages of gas atomized powders over other powder production methods?
A: Gas atomization offers several advantages, including:
- Highly spherical powders: This improves flowability, packing density, and consistency.
- Tight control over particle size: Allows for tailoring powders to specific applications.
- High purity: Minimizes contamination for demanding applications.
Q: What are some of the limitations of gas atomization?
A: Some limitations of gas atomization include:
- High capital cost: Setting up a gas atomization system requires a significant investment.
- Energy consumption: The process can be energy-intensive.
- Limited material selection: Not all metals are suitable for gas atomization.
Q: What are some of the safety considerations when handling gas-atomized metal powders?
A: Gas-atomized metal powders can be fine and airborne, posing potential health risks. Here are some safety considerations:
- Always consult the Material Safety Data Sheet (MSDS): This document provides information on the specific hazards associated with the powder you’re handling, including inhalation risks, flammability, and reactivity.
- Wear appropriate personal protective equipment (PPE): This may include safety glasses, gloves, respirators, and protective clothing depending on the powder type and handling procedures.
- Maintain a clean work environment: Minimize dust generation and ensure proper ventilation to prevent airborne particles.
- Dispose of waste properly: Follow recommended disposal guidelines outlined in the MSDS to avoid environmental contamination.
Q: What are the future trends in gas atomization technology?
A: The future of gas atomization is bright, with several exciting trends emerging:
- Development of new materials: Ongoing research focuses on gas atomizing new and exotic materials for advanced applications in aerospace, energy, and bioprinting.
- Improved process efficiency: Advancements are being made to optimize energy consumption and minimize waste generation during the gas atomization process.
- Nanoparticle production: The ability to produce gas-atomized metal nanoparticles opens doors for innovative applications in nanotechnology and biomaterials.
- Integration with additive manufacturing: As 3D printing technology continues to evolve, gas atomization will play a crucial role in providing high-quality powders for complex and high-performance parts.
Share On
MET3DP Technology Co., LTD is a leading provider of additive manufacturing solutions headquartered in Qingdao, China. Our company specializes in 3D printing equipment and high-performance metal powders for industrial applications.
Inquiry to get best price and customized Solution for your business!
Related Articles
About Met3DP
Recent Update
Our Product
CONTACT US
Any questions? Send us message now! We’ll serve your request with a whole team after receiving your message.
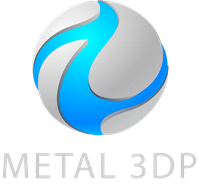
Metal Powders for 3D Printing and Additive Manufacturing