Gas Atomizer Equipment
Table of Contents
Gas atomizer equipment is a vital component in the production of high-quality metal powders used across various industries, including aerospace, automotive, medical, and electronics. This equipment utilizes high-pressure gas streams to atomize molten metal, creating fine, uniform particles that can be used in a range of applications, from additive manufacturing to surface coatings. In this guide, we will explore the intricacies of gas atomizer equipment, delve into specific metal powder models, and provide a detailed overview of their properties, applications, specifications, and more.
Overview of Gas Atomizer Equipment
Gas atomizer equipment is designed to produce metal powders by disintegrating molten metal into fine droplets using a high-pressure gas stream. This method is preferred for producing powders with a spherical shape and narrow particle size distribution, which are essential for achieving high performance in various applications.
Key Features of Gas Atomizer Equipment
- High Efficiency: Capable of producing large quantities of metal powders quickly.
- Uniform Particle Size: Ensures consistency in the final product.
- Versatility: Can be used with a wide range of metals and alloys.
- Scalability: Suitable for both small-scale and industrial-scale production.
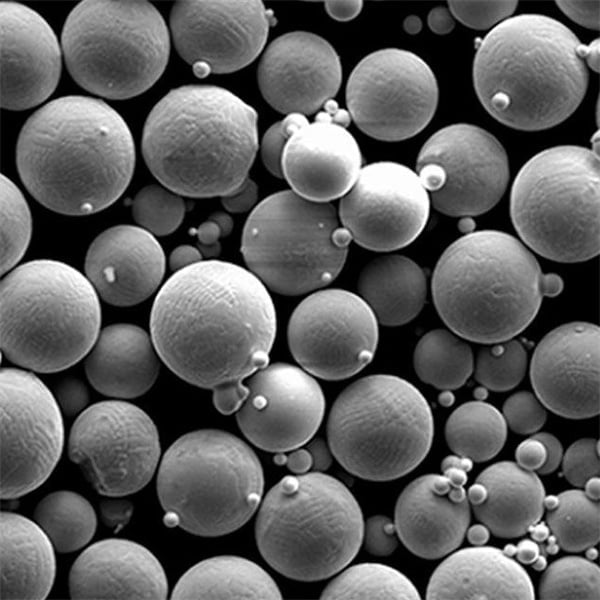
Types of Gas Atomizer Equipment
Gas atomizers come in various configurations and are used for different types of metals and applications. Here, we’ll look at ten specific metal powder models produced using gas atomizer equipment.
Specific Metal Powder Models
- Aluminum (Al) Powder
- Composition: Pure Aluminum
- Properties: Lightweight, high corrosion resistance, excellent electrical and thermal conductivity.
- Applications: Aerospace components, automotive parts, electrical contacts.
- Titanium (Ti) Powder
- Composition: Pure Titanium
- Properties: High strength-to-weight ratio, biocompatibility, excellent corrosion resistance.
- Applications: Medical implants, aerospace structures, chemical processing equipment.
- Stainless Steel (316L) Powder
- Composition: Iron, Chromium, Nickel, Molybdenum
- Properties: High corrosion resistance, good mechanical properties, weldability.
- Applications: Medical devices, food processing equipment, marine applications.
- Cobalt-Chrome (CoCr) Powder
- Composition: Cobalt, Chromium
- Properties: High wear resistance, excellent corrosion resistance, biocompatibility.
- Applications: Dental implants, orthopedic implants, turbine blades.
- Inconel (625) Powder
- Composition: Nickel, Chromium, Molybdenum, Niobium
- Properties: High strength, excellent oxidation and corrosion resistance, stability at high temperatures.
- Applications: Aerospace engines, chemical processing, marine applications.
- Copper (Cu) Powder
- Composition: Pure Copper
- Properties: Excellent electrical and thermal conductivity, good corrosion resistance.
- Applications: Electrical components, thermal management systems, antimicrobial surfaces.
- Nickel (Ni) Powder
- Composition: Pure Nickel
- Properties: High corrosion resistance, good mechanical properties, stability at high temperatures.
- Applications: Battery electrodes, aerospace components, chemical processing.
- Tool Steel (M2) Powder
- Composition: Iron, Carbon, Tungsten, Molybdenum, Chromium, Vanadium
- Properties: High hardness, wear resistance, good toughness.
- Applications: Cutting tools, molds, dies.
- Magnesium (Mg) Powder
- Composition: Pure Magnesium
- Properties: Lightweight, good mechanical properties, high thermal conductivity.
- Applications: Aerospace components, automotive parts, electronics.
- Tungsten (W) Powder
- Composition: Pure Tungsten
- Properties: High density, high melting point, excellent wear resistance.
- Applications: Radiation shielding, aerospace components, electrical contacts.
Applications of Gas Atomizer Equipment
Gas atomizer equipment is indispensable in industries where high-performance metal powders are required. The following table summarizes the key applications of different metal powders produced using gas atomizer equipment.
Applications Table
Metal Powder | Applications |
---|---|
Aluminum (Al) | Aerospace components, automotive parts, electrical contacts |
Titanium (Ti) | Medical implants, aerospace structures, chemical processing equipment |
Stainless Steel (316L) | Medical devices, food processing equipment, marine applications |
Cobalt-Chrome (CoCr) | Dental implants, orthopedic implants, turbine blades |
Inconel (625) | Aerospace engines, chemical processing, marine applications |
Copper (Cu) | Electrical components, thermal management systems, antimicrobial surfaces |
Nickel (Ni) | Battery electrodes, aerospace components, chemical processing |
Tool Steel (M2) | Cutting tools, molds, dies |
Magnesium (Mg) | Aerospace components, automotive parts, electronics |
Tungsten (W) | Radiation shielding, aerospace components, electrical contacts |
Advantages of Gas Atomizer Equipment
Gas atomizer equipment offers several advantages that make it a preferred choice for producing metal powders.
Advantages
- High Purity: The process produces high-purity metal powders with minimal contamination.
- Controlled Particle Size: Enables precise control over particle size distribution, essential for specific applications.
- Scalability: Suitable for both small-scale and large-scale production needs.
- Versatility: Can be used with a wide range of metals and alloys.
- High Yield: Capable of producing a high yield of fine metal powders efficiently.
Disadvantages of Gas Atomizer Equipment
Despite its numerous advantages, gas atomizer equipment has some limitations.
Disadvantages
- High Cost: The equipment and operational costs can be high, especially for small-scale production.
- Complex Operation: Requires skilled operators and precise control to achieve optimal results.
- Maintenance: Regular maintenance is necessary to ensure consistent performance and prevent downtime.
Specifications and Standards
When selecting gas atomizer equipment, it’s crucial to consider various specifications and standards to ensure it meets the required performance criteria.
Specifications Table
Specification | Details |
---|---|
Gas Pressure | 20-100 bar |
Nozzle Type | Convergent-divergent, Laval |
Particle Size Range | 1-200 microns |
Production Capacity | 10-1000 kg/h |
Materials | Wide range of metals and alloys |
Standards | ISO 9001, ASTM B212, ASTM B215 |
Suppliers and Pricing Details
Several suppliers offer gas atomizer equipment with varying features and price points. Below is a table listing some of the leading suppliers and their pricing details.
Suppliers Table
Supplier | Model | Price Range | Contact Information |
---|---|---|---|
Company A | GA-1000 | $50,000 – $100,000 | www.companya.com |
Company B | Atomizer Pro | $70,000 – $120,000 | www.companyb.com |
Company C | PowderMaster X1 | $60,000 – $110,000 | www.companyc.com |
Company D | GasFlow 9000 | $80,000 – $130,000 | www.companyd.com |
Comparing Gas Atomizer Equipment Models
When choosing gas atomizer equipment, it’s essential to compare different models based on their features, performance, and cost. Below is a comparison table highlighting the pros and cons of popular gas atomizer models.
Comparison Table
Model | Advantages | Limitations |
---|---|---|
GA-1000 | High efficiency, large production capacity | High initial cost, complex operation |
Atomizer Pro | Versatility, precise particle size control | Requires skilled operators, regular maintenance |
PowderMaster X1 | Affordable, suitable for various metals | Lower production capacity compared to others |
GasFlow 9000 | Advanced features, high purity output | Higher operational cost, complex setup |
Understanding the Production Process
The production process of metal powders using gas atomizer equipment involves several steps, each crucial for achieving the desired quality and properties.
Production Steps
- Melting: The metal or alloy is melted in a crucible at high temperatures.
- Atomization: The molten metal is then disintegrated into fine droplets using a high-pressure gas stream.
- Cooling: The droplets solidify into fine metal powders as they cool down.
- Collection: The metal powders are collected and further processed if necessary (e.g., sieving, classification).
- Quality Control: The final product undergoes rigorous quality control to ensure it meets the required specifications.
Technical Insights and Innovations
Gas atomizer equipment has seen significant advancements over the years, improving efficiency, precision, and versatility. Here are some recent innovations in the field:
Recent Innovations
- Advanced Nozzle Designs: Improved nozzle designs for better control over particle size distribution.
- Automated Systems: Integration of automation for enhanced precision and reduced manual intervention.
- Hybrid Technologies: Combining gas atomization with other techniques (e.g., plasma atomization) for superior results.
- Environmental Control: Enhanced control over environmental conditions to reduce contamination and improve purity.
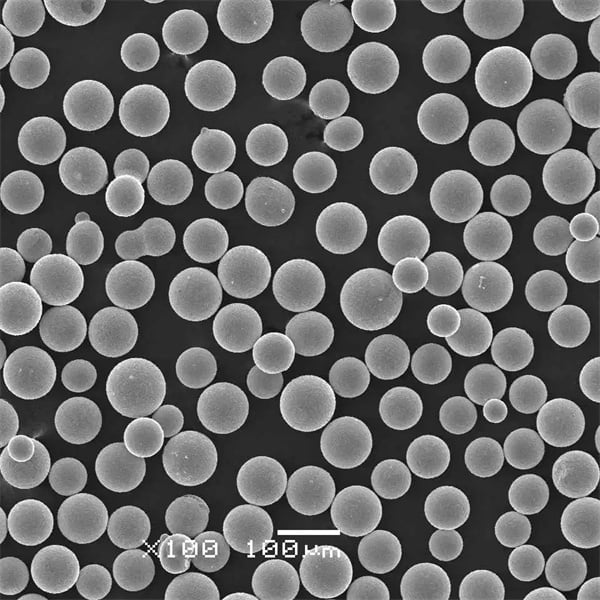
FAQ
Question | Answer |
---|---|
What is gas atomization? | A process of producing metal powders by disintegrating molten metal using a high-pressure gas stream. |
What are the advantages of gas atomization? | High purity, uniform particle size, scalability, and versatility. |
Which metals can be processed using gas atomization? | A wide range of metals and alloys including aluminum, titanium, stainless steel, and more. |
How is particle size controlled? | By adjusting gas pressure, nozzle design, and other parameters. |
What are the main applications of metal powders? | Aerospace, automotive, medical, electronics, and more. |
How much does gas atomizer equipment cost? | Prices range from $50,000 to $130,000 depending on the model and features. |
What are the maintenance requirements? | Regular maintenance is required to ensure consistent performance and prevent downtime. |
Can gas atomizer equipment be used for small-scale production? | Yes, it is suitable for both small-scale and industrial-scale production. |
What standards apply to gas atomizer equipment? | Common standards include ISO 9001, ASTM B212, and ASTM B215. |
What are the recent innovations in gas atomization? | Advanced nozzle designs, automated systems, hybrid technologies, and enhanced environmental control. |
Conclusion
Gas atomizer equipment plays a crucial role in producing high-quality metal powders essential for various industrial applications. By understanding the types, properties, applications, and specifications of different metal powders, as well as the advantages and limitations of gas atomizer equipment, manufacturers can make informed decisions to optimize their production processes. With continuous advancements and innovations, the future of gas atomization technology looks promising, paving the way for more efficient and versatile metal powder production.
Share On
MET3DP Technology Co., LTD is a leading provider of additive manufacturing solutions headquartered in Qingdao, China. Our company specializes in 3D printing equipment and high-performance metal powders for industrial applications.
Inquiry to get best price and customized Solution for your business!
Related Articles
About Met3DP
Recent Update
Our Product
CONTACT US
Any questions? Send us message now! We’ll serve your request with a whole team after receiving your message.
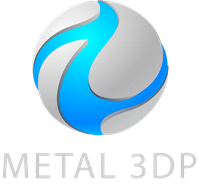
Metal Powders for 3D Printing and Additive Manufacturing
COMPANY
PRODUCT
cONTACT INFO
- Qingdao City, Shandong, China
- [email protected]
- [email protected]
- +86 19116340731