Gas Atomizer for Metal Powder Production
Table of Contents
Overview of Gas Atomizer for Metal Powder Production
Metal powder production is a critical process in modern manufacturing, enabling the creation of advanced materials for a variety of applications. One of the most efficient methods for producing high-quality metal powders is through gas atomization. But what exactly is gas atomization? How does it work? And what makes it such a preferred method in the industry?
Gas atomization involves the use of a high-velocity gas stream to break up molten metal into fine droplets, which then solidify into powder particles. This method is renowned for producing powders with spherical shapes and narrow particle size distributions, which are crucial for applications requiring high flowability and packing density.
Key Details of Gas Atomization
Parameter | Description |
---|---|
Process | Uses high-pressure gas (often argon or nitrogen) to disintegrate molten metal into fine droplets. |
Metal Types | Steel, aluminum, titanium, nickel, cobalt, and other alloys. |
Powder Characteristics | Spherical shape, uniform particle size distribution, high purity, and low oxygen content. |
Applications | Additive manufacturing, powder metallurgy, thermal spraying, metal injection molding, and more. |
Advantages | High-quality powders, precise control over particle size, ability to produce a wide range of metals and alloys. |
Limitations | High equipment cost, energy-intensive process, complexity in handling and controlling gas flows. |
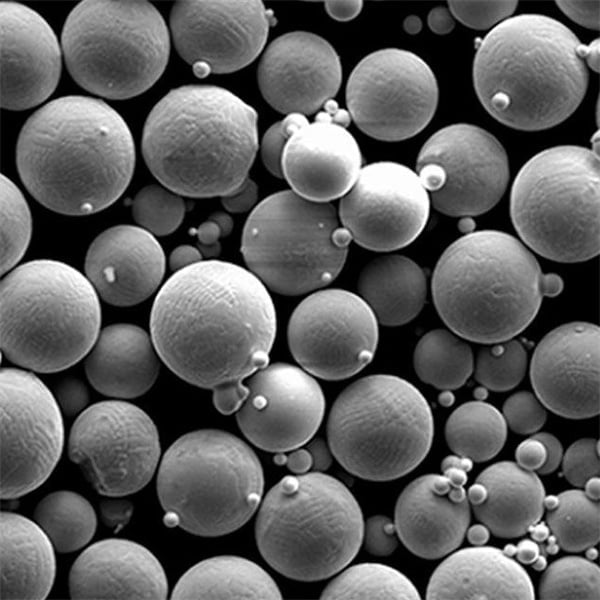
Types of Metal Powders Produced by Gas Atomization
Gas atomization is versatile, enabling the production of various metal powders. Below are specific models of metal powders produced using this method, along with their descriptions.
1. 316L Stainless Steel Powder
316L stainless steel powder is widely used in additive manufacturing due to its excellent corrosion resistance and mechanical properties. This powder is ideal for producing medical devices, aerospace components, and marine applications.
2. Inconel 718 Powder
Inconel 718 is a nickel-chromium alloy known for its high strength and corrosion resistance at elevated temperatures. This powder is commonly used in the aerospace industry for turbine blades and other high-temperature applications.
3. Titanium Ti-6Al-4V Powder
Ti-6Al-4V is a titanium alloy known for its high strength, low density, and excellent biocompatibility. It is widely used in the medical field for implants and in the aerospace industry for lightweight structural components.
4. Aluminum 6061 Powder
Aluminum 6061 is a versatile alloy known for its good mechanical properties and weldability. This powder is used in automotive, aerospace, and general manufacturing for producing lightweight and high-strength parts.
5. Cobalt-Chrome (CoCr) Powder
Cobalt-chrome powders are used in the dental and medical industries due to their excellent wear resistance, biocompatibility, and high strength. They are ideal for producing dental implants and orthopedic devices.
6. Copper Powder
Copper powder produced by gas atomization has high purity and excellent electrical conductivity. It is used in electrical and electronic components, thermal management applications, and in the production of conductive inks and pastes.
7. Maraging Steel Powder
Maraging steel is a high-strength, low-carbon steel known for its superior mechanical properties and ease of machining. This powder is used in tooling, aerospace, and high-performance engineering applications.
8. Nickel Powder
Nickel powder is used in a variety of applications, including battery electrodes, catalysts, and superalloys. It is valued for its corrosion resistance, high-temperature performance, and magnetic properties.
9. Stainless Steel 17-4PH Powder
17-4PH stainless steel is a precipitation-hardening martensitic stainless steel that combines high strength and hardness with excellent corrosion resistance. It is used in aerospace, chemical, and petrochemical industries.
10. Tungsten Carbide Powder
Tungsten carbide powder is known for its extreme hardness and wear resistance. It is used in cutting tools, abrasives, and wear-resistant coatings.
Applications of Gas Atomizer for Metal Powder Production
The applications of metal powders produced by gas atomization are vast and varied, making them essential in numerous industries.
Application Area | Description |
---|---|
Additive Manufacturing | Produces high-quality powders for 3D printing, enabling the creation of complex and precise components. |
Powder Metallurgy | Used in the manufacture of high-performance components through processes like hot isostatic pressing and sintering. |
Thermal Spraying | Coating surfaces with metal powders to enhance wear resistance, corrosion resistance, and thermal barriers. |
Metal Injection Molding | Combines the flexibility of plastic injection molding with the strength and durability of metal powders. |
Electronics | Produces powders for conductive pastes, solder pastes, and components with high electrical and thermal conductivity. |
Medical Devices | Creates biocompatible and corrosion-resistant powders for implants, prosthetics, and surgical instruments. |
Aerospace Components | Manufactures lightweight and high-strength parts capable of withstanding extreme conditions and high temperatures. |
Automotive Parts | Produces components that require high strength, durability, and lightweight properties for improved fuel efficiency and performance. |
Energy Sector | Utilizes metal powders for fuel cells, batteries, and other energy-related applications demanding high purity and performance. |
Tooling and Wear Parts | Provides hard and wear-resistant powders for cutting tools, molds, and dies, extending their service life and performance. |
Specifications, Sizes, Grades, and Standards
Metal powders produced by gas atomization come in various specifications to meet industry standards and application requirements.
Metal Powder | Particle Size (µm) | Purity (%) | Standards |
---|---|---|---|
316L Stainless Steel | 15-45, 45-106 | >99.9 | ASTM F138, F139, F1586 |
Inconel 718 | 15-45, 45-106 | >99.5 | AMS 5662, AMS 5663 |
Ti-6Al-4V | 15-45, 45-106 | >99.7 | ASTM B348, F136, F1472 |
Aluminum 6061 | 15-45, 45-106 | >99.8 | ASTM B209, B221 |
Cobalt-Chrome | 15-45, 45-106 | >99.5 | ASTM F75, F799, F1537 |
Copper | 15-45, 45-106 | >99.9 | ASTM B170, B379 |
Maraging Steel | 15-45, 45-106 | >99.5 | AMS 6514, AMS 6512 |
Nickel | 15-45, 45-106 | >99.9 | ASTM B330, B333 |
17-4PH Stainless Steel | 15-45, 45-106 | >99.5 | ASTM A693, F899, A564 |
Tungsten Carbide | 1-10, 10-45 | >99.5 | ISO 9001, ISO 14001 |
Suppliers and Pricing Details
The availability and pricing of metal powders can vary based on the supplier, quality, and market demand.
Supplier | Metal Powder | Price Range (per kg) | Notes |
---|---|---|---|
Höganäs AB | Stainless Steel, Iron, Copper | $30 – $100 | Leading supplier with a wide range of high-quality powders. |
Carpenter Technology | Nickel, Titanium, Cobalt | $100 – $500 | Specializes in high-performance alloys for critical industries. |
GKN Powder Metallurgy | Various Alloys | $50 – $200 | Extensive global network and custom powder solutions. |
LPW Technology | Aluminum, Steel, Nickel | $75 – $300 | Focus on additive manufacturing powders with consistent quality. |
Sandvik | Titanium, Cobalt-Chrome | $150 – $600 | Renowned for advanced metal powder technologies. |
HC Starck | Tungsten, Molybdenum | $200 – $800 | Offers specialized powders for demanding applications. |
AP&C (GE Additive) | Titanium, Aluminum | $100 – $400 | Known for aerospace and medical-grade powders. |
Arcam AB (GE Additive) | Nickel, Cobalt | $120 – $450 | High-quality powders for additive manufacturing. |
Praxair Surface Technologies | Various Alloys | $80 – $350 | Provides powders for thermal spray and additive manufacturing. |
EOS GmbH | Various Metals | $90 – $380 | Leading supplier of 3D printing metal powders. |
Advantages and Disadvantages of Gas Atomizer for Metal Powder Production
Like any manufacturing process, gas atomization has its strengths and weaknesses.
Aspect | Advantages | Disadvantages |
---|---|---|
Quality of Powder | Produces high-quality powders with spherical shape and uniform size. | Potential for contamination if not properly controlled. |
Particle Size Distribution | Narrow particle size distribution ensures consistent performance. | Limited control over extremely fine or coarse particles. |
Material Versatility | Can produce a wide range of metals and alloys. | Some materials may be difficult to atomize effectively. |
Purity | High purity levels with minimal oxidation. | Requires careful handling to maintain purity levels. |
Cost | High initial investment in equipment. | Energy-intensive process leading to higher operational costs. |
Production Rate | Capable of producing large quantities of powder quickly. | Rate may be limited by the cooling capacity and gas flow control. |
Application Versatility | Suitable for diverse applications including additive manufacturing, powder metallurgy, and thermal spraying. | May require additional processing steps (e.g., sieving, classifying) to achieve desired specifications. |
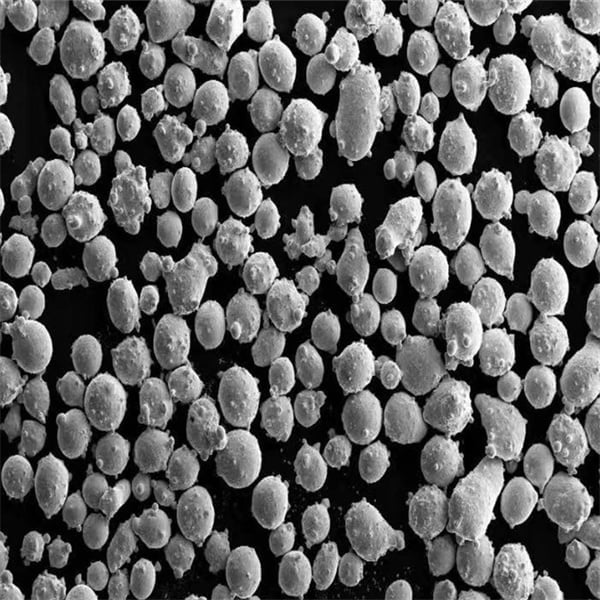
FAQs
What is gas atomization?
Gas atomization is a process where molten metal is disintegrated into fine droplets using a high-velocity gas stream. These droplets solidify into spherical metal powders.
What metals can be produced using gas atomization?
Gas atomization can produce a wide range of metals and alloys, including stainless steel, titanium, aluminum, nickel, cobalt, and more.
What are the key advantages of gas atomization?
The key advantages include high-quality powders with spherical shapes, narrow particle size distributions, high purity, and versatility in producing various metals and alloys.
Are there any limitations to gas atomization?
Yes, gas atomization requires high initial investment, is energy-intensive, and may require careful handling to maintain purity levels. Additionally, controlling extremely fine or coarse particles can be challenging.
How are metal powders used in additive manufacturing?
Metal powders are used in additive manufacturing (3D printing) to create complex and precise components layer by layer, enabling the production of parts with intricate geometries and tailored properties.
Why is particle size important in metal powders?
Particle size affects the flowability, packing density, and final properties of the manufactured part. A narrow particle size distribution ensures consistent performance in various applications.
What is the typical purity level of gas-atomized metal powders?
Gas-atomized metal powders typically have high purity levels, often exceeding 99%, which is crucial for applications requiring high performance and reliability.
How does gas atomization compare to other powder production methods?
Gas atomization is favored for its ability to produce high-quality powders with spherical shapes and uniform size. However, it is more costly and energy-intensive compared to some other methods like water atomization.
Can gas-atomized powders be used in medical applications?
Yes, powders like Ti-6Al-4V and cobalt-chrome produced by gas atomization are widely used in medical applications due to their biocompatibility and high strength.
What factors influence the cost of gas-atomized metal powders?
The cost is influenced by the type of metal or alloy, purity requirements, particle size distribution, and production volume. Supplier pricing and market demand also play significant roles.
In conclusion, gas atomization is a powerful method for producing high-quality metal powders with a wide range of applications. Its ability to create uniform, high-purity powders makes it a valuable process in industries such as additive manufacturing, aerospace, and medical devices. While it comes with higher costs and operational complexities, the benefits often outweigh these challenges, especially for critical applications requiring precise and reliable materials.
Share On
MET3DP Technology Co., LTD is a leading provider of additive manufacturing solutions headquartered in Qingdao, China. Our company specializes in 3D printing equipment and high-performance metal powders for industrial applications.
Inquiry to get best price and customized Solution for your business!
Related Articles
About Met3DP
Recent Update
Our Product
CONTACT US
Any questions? Send us message now! We’ll serve your request with a whole team after receiving your message.
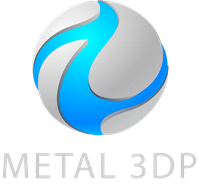
Metal Powders for 3D Printing and Additive Manufacturing