HDH Titanium Powder
Table of Contents
Titanium powder produced via the Armstrong process, also known as HDH (hydride-dehydride) titanium powder, is a high purity titanium powder used across various industries. This article provides a comprehensive technical overview of HDH titanium powder, including its properties, manufacturing process, applications, specifications, selection guidelines, suppliers, and more.
Introduction to HDH Titanium Powder
HDH titanium powder is composed almost entirely of titanium metal, with low oxygen and iron content. It has a high degree of sphericity and flowability. Key properties and characteristics of HDH titanium powder are summarized below:
Table 1. Overview of HDH Titanium Powder
Properties | Details |
---|---|
Composition | ≥99.5% titanium |
Impurities | Low oxygen, iron, nitrogen, carbon, and hydrogen |
Particle shape | Highly spherical |
Particle size distribution | Typically 10-45 μm |
Apparent density | 2.2-2.7 g/cm3 |
Tap density | 3.0-3.7 g/cm3 |
Flow rate | 25-35 s/50g |
Color | Dark gray |
The high purity and spherical morphology make HDH powder suitable for additive manufacturing, metal injection molding, pressing and sintering, thermal spraying, welding, and other fabrications that require high density and quality.
Key benefits over other titanium powder varieties:
- Higher purity with lower interstitial elements
- Improved flowability due to spherical shape
- Better packing density and sinterability
- Excellent mechanical properties
- Good chemical stability at high temperatures
However, HDH powder can be more expensive than other varieties due to the extensive processing required to achieve the purity levels.
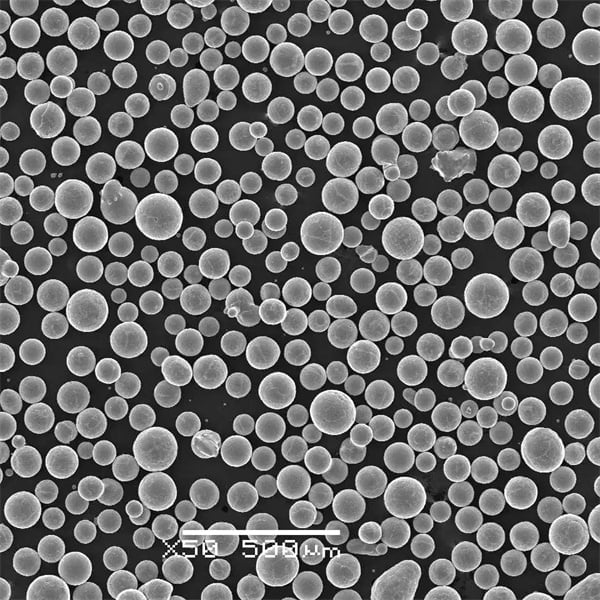
Manufacturing Process
HDH titanium powder is produced via the Armstrong process, which involves multiple stages:
1. Melting: Commercially pure titanium ingots are melted into liquid form. Common feedstocks are titanium sponge, scrap, and alloy ingots.
2. Hydriding: The molten titanium reacts with hydrogen gas to produce titanium hydride (TiH2). Cooling and crushing creates brittle titanium hydride chunks.
3. Dehydriding: The TiH2 is treated in a vacuum at temperatures above 600°C, decomposing it back into titanium powder and releasing hydrogen. This powder has high oxygen content.
4. Vacuum Purification: Multiple vacuum distillation cycles are used to reduce oxygen, nitrogen and hydrogen levels to ≤0.2%, achieving high purity HDH titanium powder.
The HDH process allows precise control over powder characteristics like particle size distribution, morphology, purity level, and microstructure. The powder can be tailored to meet application requirements.
Table 2. Overview of HDH Titanium Powder Manufacturing
Stage | Details |
---|---|
Melting | Ingots melted into liquid titanium form |
Hydriding | Liquid titanium reacts with hydrogen to form titanium hydride (TiH2) |
Dehydriding | TiH2 decomposed into titanium powder under vacuum at >600°C |
Vacuum purification | Multiple vacuum distillation cycles to reduce impurities |
Composition and Properties
HDH titanium powder contains ≥99.5% titanium with low impurity levels, as highlighted in the composition table below:
Table 3. Typical composition of HDH titanium powder
Element | Weight % |
---|---|
Titanium (Ti) | ≥ 99.5 |
Oxygen (O) | ≤ 0.13 |
Carbon (C) | ≤ 0.08 |
Nitrogen (N) | ≤ 0.05 |
Hydrogen (H) | ≤ 0.015 |
Iron (Fe) | ≤ 0.20 |
The purity, spherical morphology, and small particle size distribution result in exceptional properties that make HDH powder suitable for various advanced applications:
Table 4. Overview of HDH titanium powder properties
Property | Details |
---|---|
Particle shape | Highly spherical morphology |
Particle size distribution | Typically 10-45 μm |
Apparent density | 2.2-2.7 g/cm3 |
Tap density | 3.0-3.7 g/cm3 |
Flow rate | 25-35 s/50g |
Purity | ≥99.5% titanium content |
Oxygen content | ≤0.13% |
The properties like increased flowability, higher tap density, and purity enable usage in additive manufacturing, powder metallurgy parts production, thermal spraying, and more applications.
Classification and Specifications
HDH titanium powder is available in a range of particle size distributions categorized as fine, medium, and coarse grades. Finer grades have better sinterability while coarser grades improve flowability.
Table 5. Classification of HDH titanium powder by particle size
Grade | Particle Size (μm) | Typical Use |
---|---|---|
Fine | 10-25 μm | Additive manufacturing, pressing & sintering |
Medium | 25-45 μm | Pressing & sintering, thermal spray |
Coarse | 45-106 μm | Thermal spray, welding |
Common specifications as per established standards:
- ASTM B299: Specification for titanium powder metallurgy shapes
- ASTM B817: Specification for powder metallurgy titanium alloy impeller components
- ISO 23301: Sintered titanium materials and products for surgical implants
HDH titanium powder can also be customized as per application requirements in terms of particle size distribution, morphology, impurity levels, and other attributes.
Applications and Uses
The unique properties of high purity HDH titanium powder make it suitable for the following advanced applications across industries:
Table 6. Overview of applications and uses for HDH titanium powder
Industry | Applications |
---|---|
Additive manufacturing | 3D printing of end-use titanium parts with complex geometry |
Powder metallurgy | Pressing & sintering to create net shape components like impellers |
Thermal spray | Wear and corrosion resistant coatings |
Metal injection molding | Small, complex parts like fasteners, gears |
Welding | Excellent weldability for titanium fusion welding |
Aerospace | Engine components, airframes, turbines |
Medical | Implants, surgical instruments |
Automotive | Valves, connecting rods, springs |
The high purity, spherical morphology, and good flow of HDH powder make it an excellent choice for small, complex parts with high quality requirements. The excellent mechanical properties like strength and corrosion resistance expand the application possibilities across industries.
HDH titanium parts offer the perfect balance of strength, low weight, corrosion resistance, fatigue performance, and biocompatibility – making it the top choice over stainless steel or cobalt alloys for critical components in the aerospace, automotive, oil & gas, chemical, and medical sectors.
Comparison with Other Titanium Powders
HDH titanium provides significantly better powder flowability, density, and purity over other commercially available titanium powder varieties.
Table 7. Comparison of HDH titanium powder with other types
Parameter | HDH Titanium Powder | Plasma Atomized | Gas Atomized (GA) |
---|---|---|---|
Particle shape | Highly spherical | Rough, irregular | Rounded |
Flowability | Excellent | Low | Moderate |
Purity | ≥99.5% titanium | ≤98% titanium | ≤98% titanium content |
Oxygen content | ≤0.13% | 0.18-0.35% | 0.15-0.30% |
Cost | High | Low | Moderate |
While plasma atomized and gas atomized titanium powders can provide cost benefits, HDH powder is vastly superior in meeting requirements for critical applications like medical implants, aerospace components, etc. where quality standards are much more stringent.
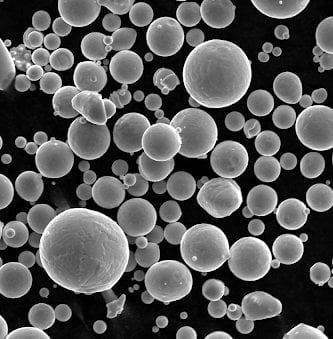
Selection Guidelines
Key considerations for selecting HDH grade titanium powder:
Table 8. HDH titanium powder selection guidelines
Parameter | Guidelines |
---|---|
Particle size | Match to requirements of manufacturing process and part dimensions |
Particle shape | Spherical preferred for flowability |
Purity levels | ≥ 99.5% titanium content based on application |
Oxygen/nitrogen | Ultra low ≤ 0.13% oxygen for mechanical properties |
Supplier | Reputable supplier meeting international quality standards |
Work with powder producers to customize HDH powder properties like particle size distribution, morphology, density, and impurity levels based on end application requirements.
Finer 10-25 μm grades suit small, complex components. Coarser 45-106 μm grades preferred for thermal spray coatings.
FAQ
1. What is HDH Titanium Powder?
HDH Titanium Powder is a fine-grade titanium powder produced using the Hydride-Dehydride (HDH) process. It is a common feedstock material for additive manufacturing, also known as 3D printing.
2. How is HDH Titanium Powder Produced?
The HDH process involves the hydrogenation of titanium sponge, followed by its dehydrogenation. This process results in the formation of titanium powder with desired characteristics.
3. What are the Applications of HDH Titanium Powder?
HDH Titanium Powder is used in various applications, including aerospace, medical implants, automotive parts, and sports equipment. It is particularly valued for its lightweight, high-strength properties.
4. What Are the Advantages of Using HDH Titanium Powder in Additive Manufacturing?
HDH Titanium Powder is preferred in additive manufacturing for its excellent flowability and packing characteristics, making it suitable for creating intricate and complex 3D-printed components.
5. What Particle Size Ranges are Available for HDH Titanium Powder?
HDH Titanium Powder is available in various particle size distributions, typically ranging from a few micrometers to several tens of micrometers, depending on the specific requirements of the application.
Share On
MET3DP Technology Co., LTD is a leading provider of additive manufacturing solutions headquartered in Qingdao, China. Our company specializes in 3D printing equipment and high-performance metal powders for industrial applications.
Inquiry to get best price and customized Solution for your business!
Related Articles
About Met3DP
Recent Update
Our Product
CONTACT US
Any questions? Send us message now! We’ll serve your request with a whole team after receiving your message.
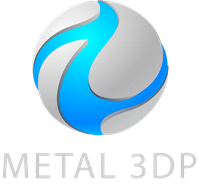
Metal Powders for 3D Printing and Additive Manufacturing
COMPANY
PRODUCT
cONTACT INFO
- Qingdao City, Shandong, China
- [email protected]
- [email protected]
- +86 19116340731