High Purity Iron Powder
Table of Contents
Overview of High Purity Iron Powder
High purity iron powder is a highly versatile material with applications spanning various industries, from automotive to pharmaceuticals. Its unique properties, including its purity and specific particle size distributions, make it indispensable in manufacturing processes that require precision and consistency. But what exactly makes high purity iron powder so special? Let’s dive into the details and explore everything there is to know about this fascinating material.
What is High Purity Iron Powder?
High purity iron powder is a fine metallic substance with an iron content typically exceeding 99%. This high level of purity is achieved through meticulous production processes that remove impurities and ensure uniform particle size. The result is a powder that offers exceptional performance characteristics in a range of applications.
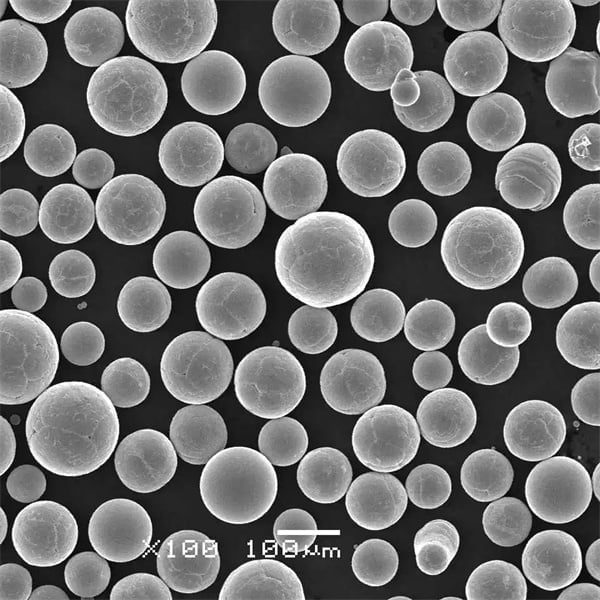
Types of High Purity Iron Powder
High purity iron powder comes in various forms, each tailored to specific uses. Here’s a closer look at some of the most common types:
Type | Composition | Properties | Applications |
---|---|---|---|
Atomized Iron Powder | Fe ≥ 99% | High compressibility, good flowability | Powder metallurgy, magnetic materials |
Reduced Iron Powder | Fe ≥ 99.5% | High surface area, irregular shape | Welding, chemical reduction |
Electrolytic Iron Powder | Fe ≥ 99.9% | Very high purity, dendritic structure | Electronics, high-density parts |
Carbonyl Iron Powder | Fe ≥ 99.5%, C ≤ 0.1% | Spherical particles, high purity | Magnetic inks, inductors, pharmaceuticals |
Ultrafine Iron Powder | Fe ≥ 99.9%, particle size <1 µm | Extremely fine particles, high surface area | Catalysts, medical applications |
Spherical Iron Powder | Fe ≥ 99.5%, spherical shape | Excellent flowability, uniform particles | Additive manufacturing, MIM |
Spray-Formed Iron Powder | Fe ≥ 99.5% | Fine particles, uniform distribution | Surface coatings, sintering |
Hydrogen Reduced Iron Powder | Fe ≥ 99.8% | High purity, fine particles | Powder metallurgy, magnetic applications |
Pre-Alloyed Iron Powder | Fe alloyed with other metals | Tailored properties, versatile | Specialized parts, high-strength applications |
High Purity Iron Granules | Fe ≥ 99.8%, granular form | High bulk density, easy handling | Casting, dense parts manufacturing |
Applications of High Purity Iron Powder
High purity iron powder’s versatility makes it a valuable component across a myriad of industries. Here are some key applications:
Industry | Application |
---|---|
Automotive | Powder metallurgy parts, brake pads, clutches |
Electronics | Magnetic cores, inductors, EMI shielding |
Pharmaceuticals | Iron supplements, magnetic drug delivery |
Chemical | Catalysts, reducing agents |
Additive Manufacturing | 3D printing, metal injection molding (MIM) |
Welding | Welding electrodes, flux-cored wires |
Surface Coatings | Protective coatings, wear-resistant layers |
Environmental | Water treatment, soil remediation |
Food Fortification | Nutritional iron additives |
Aerospace | Lightweight structural components |
Automotive Industry
In the automotive sector, high purity iron powder is indispensable for creating powder metallurgy parts that offer high strength and wear resistance. These components are essential for manufacturing durable and efficient engines, transmissions, and braking systems.
Electronics
The unique magnetic properties of high purity iron powder make it ideal for producing magnetic cores and inductors. These components are crucial for the efficient functioning of various electronic devices, from transformers to sensors.
Pharmaceuticals
In the pharmaceutical industry, high purity iron powder is used to create iron supplements that are easily absorbed by the body. Additionally, its magnetic properties are leveraged in innovative drug delivery systems, where magnetic fields guide the drug to its target site.
Chemical Industry
As a reducing agent and catalyst, high purity iron powder plays a critical role in various chemical processes. Its high surface area and reactivity make it suitable for producing chemicals efficiently and safely.
Additive Manufacturing
The rise of 3D printing and metal injection molding (MIM) has opened new avenues for high purity iron powder. Its uniform particle size and excellent flowability ensure precise and repeatable production of complex parts, making it a staple in modern manufacturing.
Advantages of High Purity Iron Powder
High purity iron powder offers several advantages that make it a preferred choice in numerous applications. Here’s a closer look:
Advantage | Description |
---|---|
High Purity | Minimizes contamination, ensuring consistent quality and performance. |
Excellent Compressibility | Facilitates the production of dense and strong parts in powder metallurgy. |
Superior Flowability | Enhances process efficiency in additive manufacturing and MIM. |
High Surface Area | Boosts reactivity in chemical applications and catalysis. |
Tailored Particle Size Distribution | Allows customization for specific applications and performance needs. |
Versatility | Suitable for a wide range of industries and uses. |
High Purity
One of the standout features of high purity iron powder is its extremely low level of impurities. This high purity level ensures that the powder can be used in sensitive applications without compromising performance or quality.
Excellent Compressibility
High purity iron powder’s excellent compressibility is crucial in powder metallurgy, where it’s pressed into complex shapes. This property allows for the creation of strong, durable parts that can withstand rigorous use.
Superior Flowability
The powder’s superior flowability is a significant advantage in additive manufacturing and metal injection molding. It ensures smooth and consistent feeding of the powder into molds or printers, resulting in high-quality, defect-free parts.
Disadvantages of High Purity Iron Powder
Despite its many benefits, high purity iron powder also has some drawbacks that need to be considered:
Disadvantage | Description |
---|---|
Cost | High purity iron powder is more expensive than lower purity alternatives. |
Sensitivity to Contamination | Requires careful handling and storage to maintain purity levels. |
Limited Availability | May not be as readily available as other types of iron powder. |
Specific Processing Requirements | Needs specialized equipment and processes for optimal performance. |
Cost
The primary disadvantage of high purity iron powder is its cost. Due to the extensive purification processes required, it is more expensive than standard iron powders, which can be a limiting factor for some applications.
Sensitivity to Contamination
Maintaining the high purity of iron powder necessitates stringent handling and storage procedures. Even minor contamination can significantly impact its performance, making careful management essential.
Limited Availability
High purity iron powder is not as widely available as lower purity variants. This can pose supply chain challenges, especially for industries requiring large volumes of the material.
Specific Processing Requirements
Utilizing high purity iron powder to its full potential often requires specialized equipment and processes. This can entail additional investment and expertise, which may not be feasible for all users.
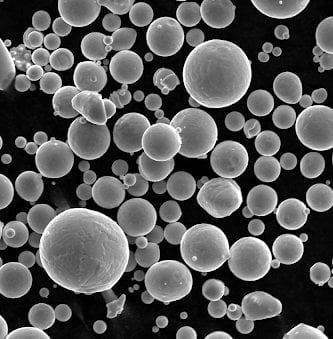
Comparison of High Purity Iron Powder Models
When selecting high purity iron powder, it’s crucial to compare different models based on specific parameters. Here’s a detailed comparison:
Model | Particle Size | Purity (%) | Shape | Applications | Advantages | Disadvantages |
---|---|---|---|---|---|---|
Atomized Iron Powder | 10-150 µm | ≥ 99% | Spherical | Powder metallurgy, magnetic materials | Good flowability, compressibility | Higher cost compared to reduced powder |
Reduced Iron Powder | 45-150 µm | ≥ 99.5% | Irregular | Welding, chemical reduction | High surface area | Irregular shape affects flowability |
Electrolytic Iron Powder | 2-50 µm | ≥ 99.9% | Dendritic | Electronics, high-density parts | Very high purity | Costly, sensitive to contamination |
Carbonyl Iron Powder | 1-10 µm | ≥ 99.5% | Spherical | Magnetic inks, pharmaceuticals | High purity, spherical shape | Expensive production process |
Ultrafine Iron Powder | <1 µm | ≥ 99.9% | Spherical | Catalysts, medical applications | Extremely fine particles | Handling and storage challenges |
Spherical Iron Powder | 10-150 µm | ≥ 99.5% | Spherical | Additive manufacturing, MIM | Excellent flowability | Higher production cost |
Spray-Formed Iron Powder | 5-50 µm | ≥ 99.5% | Irregular | Surface coatings, sintering | Fine particles, uniform distribution | Irregular shape affects flowability |
Hydrogen Reduced Iron Powder | 20-100 µm | ≥ 99.8% | Irregular | Powder metallurgy, magnetic applications | High purity, fine particles | Irregular shape affects flowability |
Pre-Alloyed Iron Powder | 10-150 µm | Fe alloyed | Variable | Specialized parts | Tailored properties | Complexity in production |
High Purity Iron Granules | 100-500 µm | ≥ 99.8% | Granular | Casting, dense parts manufacturing | Easy handling, high bulk density | Limited to specific applications |
Specifications and Standards
Understanding the specifications and standards for high purity iron powder is crucial for ensuring it meets the requirements of your application. Here’s a detailed look at the specifications:
Specification | Description |
---|---|
Particle Size Distribution | Range of particle sizes within the powder |
Purity Level | Percentage of iron content |
Shape | Morphology of the particles (spherical, irregular, dendritic) |
Bulk Density | Weight per unit volume of the powder |
Flow Rate | Speed at which powder flows |
Compressibility | Ability to be compacted into a solid form |
Apparent Density | Density of the powder when loosely packed |
Green Strength | Strength of the compacted powder before sintering |
Detailed Specifications
Property | Value Range |
---|---|
Particle Size | 1 µm to 150 µm |
Purity | 99% to 99.99% |
Bulk Density | 2.5 g/cm³ to 5.0 g/cm³ |
Flow Rate | 30 s/50 g to 120 s/50 g |
Compressibility | 6 g/cm³ to 7.5 g/cm³ |
Apparent Density | 2.8 g/cm³ to 4.5 g/cm³ |
Green Strength | 15 MPa to 60 MPa |
Standards
High purity iron powder adheres to various industry standards to ensure quality and performance. Some key standards include:
- ASTM B213: Standard Test Methods for Flow Rate of Metal Powders
- ASTM B328: Standard Test Method for Density of Metal Powders
- ISO 4490: Metallic powders – Determination of flow rate by means of a calibrated funnel (Hall flowmeter)
- ISO 3923-1: Metallic powders – Determination of apparent density – Part 1: Funnel method
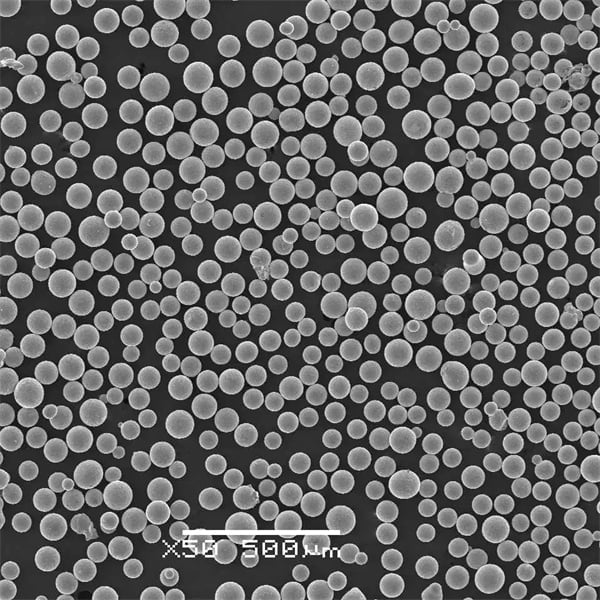
Suppliers and Pricing
The availability and cost of high purity iron powder can vary significantly depending on the supplier and specific model. Here’s a look at some of the leading suppliers and their pricing details:
Supplier | Model | Price (USD/kg) | Notes |
---|---|---|---|
Höganäs AB | Atomized Iron Powder | $15 – $30 | High quality, reliable supplier |
BASF | Carbonyl Iron Powder | $80 – $120 | Very high purity, specialty applications |
Rio Tinto Metal Powders | Reduced Iron Powder | $10 – $25 | Competitive pricing, good availability |
JFE Steel Corporation | Electrolytic Iron Powder | $100 – $150 | Premium quality, high purity |
GKN Hoeganaes | Spherical Iron Powder | $20 – $40 | Excellent flowability, versatile uses |
Sandvik Osprey | Spray-Formed Iron Powder | $50 – $90 | High uniformity, fine particles |
Shanghai CNPC Powder Material | Ultrafine Iron Powder | $200 – $300 | Specialty applications, high surface area |
NIPPON STEEL & SUMITOMO METAL | Pre-Alloyed Iron Powder | $25 – $60 | Customized properties |
Erasteel Kloster AB | High Purity Iron Granules | $10 – $20 | Easy handling, bulk applications |
Carpenter Technology Corporation | Hydrogen Reduced Iron Powder | $30 – $50 | High purity, powder metallurgy focus |
Comparing Advantages and Limitations
Understanding the pros and cons of high purity iron powder helps in making an informed decision. Here’s a comparative overview:
Advantage | Limitation |
---|---|
High Purity | Higher Cost |
Excellent Compressibility | Sensitivity to Contamination |
Superior Flowability | Specific Processing Requirements |
High Surface Area | Limited Availability |
Versatile Applications | Handling and Storage Challenges |
Advantages
The high purity of iron powder ensures minimal contamination and consistent performance, making it suitable for critical applications in industries such as pharmaceuticals and electronics. Its excellent compressibility and superior flowability enhance manufacturing efficiency and product quality.
Limitations
However, these advantages come at a cost. High purity iron powder is more expensive than its lower purity counterparts and requires careful handling to avoid contamination. Additionally, its specific processing requirements and limited availability can pose challenges for some users.
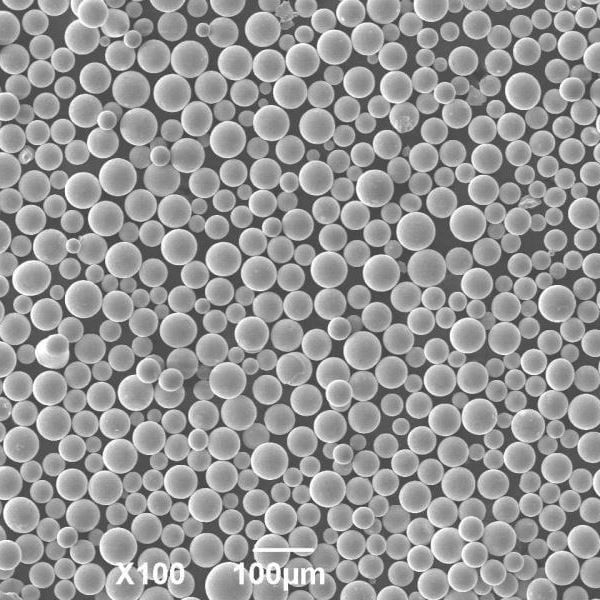
FAQs
Why is high purity important in iron powder?
High purity in iron powder minimizes the risk of contamination, ensuring consistent quality and performance in sensitive applications. This is particularly crucial in industries like pharmaceuticals, where even minor impurities can significantly impact product safety and efficacy.
How is the purity of iron powder measured?
The purity of iron powder is measured using techniques such as:
- X-ray fluorescence (XRF): Determines the elemental composition.
- Inductively coupled plasma (ICP): Analyzes trace elements.
- Carbon-sulfur analysis: Measures carbon and sulfur content.
What are the storage requirements for high purity iron powder?
To maintain its high purity, iron powder should be stored in:
- Sealed containers: To prevent contamination.
- Dry environments: To avoid oxidation and moisture absorption.
- Temperature-controlled areas: To maintain stability and prevent degradation.
Can high purity iron powder be used in 3D printing?
Yes, high purity iron powder is commonly used in 3D printing, particularly for producing high-strength, complex parts. Its excellent flowability and uniform particle size distribution make it ideal for additive manufacturing processes.
What are the environmental impacts of producing high purity iron powder?
The production of high purity iron powder involves energy-intensive processes and can generate emissions. However, advances in manufacturing technology are helping to reduce the environmental footprint, with a focus on improving energy efficiency and implementing sustainable practices.
Is high purity iron powder recyclable?
Yes, high purity iron powder can be recycled. Recycled iron powder can be reprocessed and reused in various applications, contributing to resource conservation and sustainability efforts in the industry.
How does particle size affect the performance of high purity iron powder?
Particle size significantly impacts the performance of high purity iron powder. Finer particles offer a higher surface area, enhancing reactivity in chemical processes. Conversely, larger particles provide better flowability and compressibility, which are crucial for powder metallurgy and additive manufacturing.
What are some common quality control measures for high purity iron powder?
Common quality control measures include:
- Regular purity analysis: Ensuring the powder meets the required purity levels.
- Particle size distribution testing: Confirming uniformity and consistency.
- Flowability and compressibility tests: Verifying the powder’s suitability for specific applications.
How does high purity iron powder compare to other metal powders?
High purity iron powder is often compared to other metal powders like aluminum, copper, and titanium. Each has unique properties and applications:
Property | High Purity Iron Powder | Aluminum Powder | Copper Powder | Titanium Powder |
---|---|---|---|---|
Purity | ≥ 99% | ≥ 99% | ≥ 99% | ≥ 99% |
Density | 7.87 g/cm³ | 2.70 g/cm³ | 8.96 g/cm³ | 4.50 g/cm³ |
Electrical Conductivity | Moderate | High | Very High | Low |
Corrosion Resistance | Moderate | High | Moderate | Very High |
Applications | Powder metallurgy, electronics, pharmaceuticals | Lightweight parts, pyrotechnics | Conductive inks, metallurgy | Aerospace, medical implants |
Conclusion
High purity iron powder is a remarkable material with a broad range of applications and benefits. Its exceptional purity, excellent compressibility, and superior flowability make it an indispensable component in various industries. However, its higher cost, sensitivity to contamination, and specific processing requirements highlight the need for careful consideration when selecting and using this material. By understanding its properties, applications, advantages, and limitations, you can make informed decisions to leverage the full potential of high purity iron powder in your projects.
Share On
MET3DP Technology Co., LTD is a leading provider of additive manufacturing solutions headquartered in Qingdao, China. Our company specializes in 3D printing equipment and high-performance metal powders for industrial applications.
Inquiry to get best price and customized Solution for your business!
Related Articles
About Met3DP
Recent Update
Our Product
CONTACT US
Any questions? Send us message now! We’ll serve your request with a whole team after receiving your message.
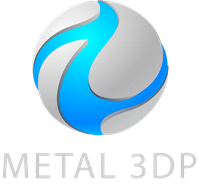
Metal Powders for 3D Printing and Additive Manufacturing