High-Temperature Rocket Engine
Table of Contents
Rocket engines are marvels of engineering, driving humanity’s quest to explore the cosmos. Among them, high-temperature rocket engines stand out for their capability to operate under extreme thermal conditions. This article delves into the complexities of high-temperature rocket engines, exploring the specific metal powder models used, their composition, properties, applications, and much more.
Overview of High-Temperature Rocket Engines
High-temperature rocket engines are designed to function at extremely high temperatures, often exceeding 3,000 degrees Celsius. These engines utilize advanced materials and technologies to withstand and operate efficiently in such harsh conditions. The key to their performance lies in the materials used, particularly specific metal powders that form the core of their structural components.
Key Features:
- High Thermal Resistance: Capable of withstanding temperatures above 3,000 degrees Celsius.
- Enhanced Durability: Resistant to thermal fatigue and oxidation.
- Advanced Materials: Utilizes high-performance metal powders and alloys.
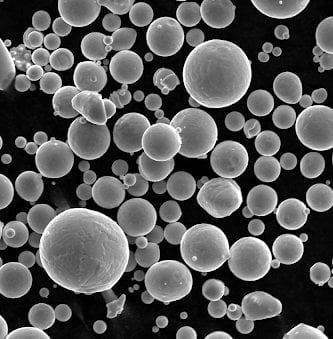
Types of Metal Powders Used in High-Temperature Rocket Engines
1. Nickel-Based Superalloys
Nickel-based superalloys are the backbone of high-temperature applications due to their excellent thermal stability and mechanical strength.
Model | Composition | Properties | Characteristics |
---|---|---|---|
Inconel 718 | Nickel (50-55%), Chromium (17-21%) | High tensile strength, corrosion resistance | Widely used in aerospace applications |
Inconel 625 | Nickel (58%), Chromium (20-23%) | Excellent fatigue and thermal-fatigue properties | Ideal for extreme environments |
Hastelloy X | Nickel (47-52%), Chromium (20-23%) | Exceptional oxidation resistance, high strength | Suitable for high-temperature oxidizing environments |
2. Titanium Alloys
Titanium alloys are known for their high strength-to-weight ratio and resistance to corrosion.
Model | Composition | Properties | Characteristics |
---|---|---|---|
Ti-6Al-4V | Titanium (90%), Aluminum (6%), Vanadium (4%) | High strength, low density, good corrosion resistance | Widely used in aerospace structures |
Ti-6242S | Titanium (90%), Aluminum (6%), Tin (2%) | High temperature stability, creep resistance | Ideal for high-temperature structural applications |
3. Cobalt-Based Alloys
Cobalt-based alloys provide excellent wear resistance and high-temperature stability.
Model | Composition | Properties | Characteristics |
---|---|---|---|
Stellite 21 | Cobalt (60%), Chromium (27-32%) | Excellent wear resistance, high-temperature strength | Used in valve seats and bearing surfaces |
Haynes 188 | Cobalt (39-41%), Chromium (21-23%), Nickel (20-24%) | Good oxidation resistance, high strength | Suitable for gas turbine engines |
4. Tungsten Alloys
Tungsten alloys are utilized for their exceptional high-temperature strength and density.
Model | Composition | Properties | Characteristics |
---|---|---|---|
W-Ni-Fe | Tungsten (90-97%), Nickel, Iron | High density, excellent high-temperature strength | Used in radiation shielding and aerospace components |
W-Ni-Cu | Tungsten (90-97%), Nickel, Copper | High density, good machinability | Suitable for aerospace and defense applications |
5. Molybdenum Alloys
Molybdenum alloys are favored for their high melting point and strength at elevated temperatures.
Model | Composition | Properties | Characteristics |
---|---|---|---|
TZM Alloy | Molybdenum (99%), Titanium, Zirconium | High strength, good thermal conductivity | Ideal for high-temperature structural components |
Mo-Re Alloy | Molybdenum (47.5%), Rhenium (52.5%) | High melting point, excellent thermal stability | Used in aerospace and nuclear applications |
6. Aluminum-Based Alloys
Though not as high temperature-resistant as others, aluminum alloys are used for their lightweight properties in certain applications.
Model | Composition | Properties | Characteristics |
---|---|---|---|
Al-7075 | Aluminum (90%), Zinc (5.6%), Magnesium (2.5%) | High strength-to-weight ratio, good fatigue resistance | Used in aerospace structures and components |
Al-2024 | Aluminum (90%), Copper (4.4%), Magnesium (1.5%) | Good machinability, high strength | Suitable for aircraft and aerospace applications |
Applications of High-Temperature Rocket Engines
High-temperature rocket engines have a variety of applications due to their ability to operate under extreme conditions. Here are some of the most notable applications:
Application | Description |
---|---|
Space Exploration | Used in launch vehicles and spacecraft propulsion systems to explore outer space |
Military Applications | Employed in missiles and defense systems requiring high thrust and performance |
Commercial Spaceflight | Utilized by private companies for launching satellites and human spaceflight missions |
Scientific Research | Applied in research projects that require high-altitude and long-duration flight capabilities |
Satellite Deployment | Used to position satellites in their desired orbits, providing essential communication services |
Specifications and Standards for Metal Powders
When selecting metal powders for high-temperature rocket engines, it’s essential to consider specifications, sizes, grades, and standards.
Metal Powder | Specification | Sizes | Grades | Standards |
---|---|---|---|---|
Inconel 718 | AMS 5662, AMS 5663 | 0.5-20 microns | Grade 1, Grade 2 | ASTM B637 |
Ti-6Al-4V | AMS 4928, AMS 4930 | 10-45 microns | Grade 5 | ASTM F1472 |
Stellite 21 | AMS 5385, AMS 5772 | 15-53 microns | Grade 21 | ASTM F75 |
TZM Alloy | ASTM B386, ASTM B387 | 5-45 microns | TZM | ASTM B386 |
Suppliers and Pricing Details
Choosing the right supplier is crucial for obtaining high-quality metal powders. Here are some leading suppliers along with pricing details.
Supplier | Metal Powder | Price (per kg) | Region | Contact Details |
---|---|---|---|---|
Carpenter Technology | Inconel 718 | $200 | North America | [email protected] |
ATI Metals | Ti-6Al-4V | $150 | Europe | [email protected] |
Haynes International | Hastelloy X | $220 | North America | [email protected] |
HC Starck | TZM Alloy | $180 | Asia | [email protected] |
Comparing Pros and Cons of Metal Powders
To make an informed decision, it’s important to weigh the advantages and disadvantages of each metal powder.
Metal Powder | Advantages | Disadvantages |
---|---|---|
Inconel 718 | High strength, good corrosion resistance | Expensive, difficult to machine |
Ti-6Al-4V | High strength-to-weight ratio, good corrosion resistance | Lower high-temperature resistance compared to nickel-based superalloys |
Stellite 21 | Excellent wear resistance, high-temperature strength | Heavy, expensive |
TZM Alloy | High strength at elevated temperatures, good thermal conductivity | Brittle at room temperature, difficult to fabricate |
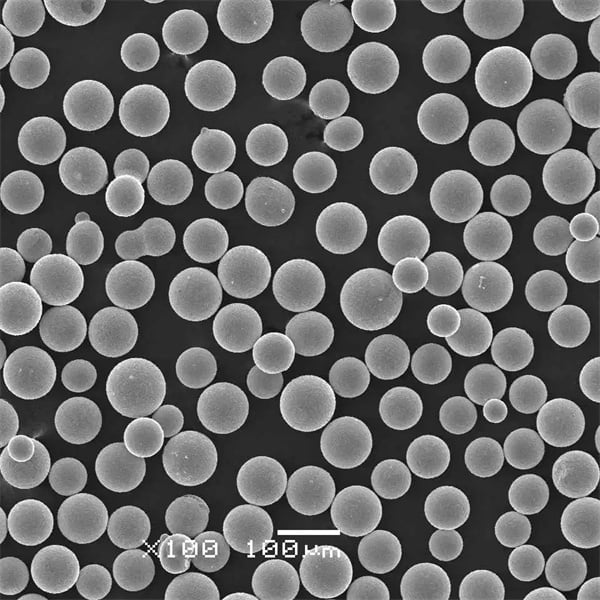
FAQ
Q: What makes high-temperature rocket engines unique?
High-temperature rocket engines are designed to operate at extremely high temperatures, often exceeding 3,000 degrees Celsius. They utilize advanced materials and technologies to maintain performance and structural integrity under such conditions.
What is Plasma Atomization?
Plasma atomization is a process for creating fine, high-purity metal powders. It uses intensely hot plasma torches to melt and atomize metal feedstock, typically wire, into tiny spherical droplets. These droplets rapidly solidify into a metal powder ideal for various applications.
How Does Plasma Atomization Work?
- Feedstock: Metal wire is continuously fed into the system.
- Melting: The wire enters a chamber where it’s struck by high-temperature (around 10,000°C) plasma torches, melting the metal.
- Atomization: The molten metal stream is then broken up into tiny droplets by a gas flow.
- Solidification: The droplets rapidly cool and solidify into spherical metal powder as they fall through an inert gas chamber.
- Collection: The cooled powder is collected and sized to meet specific requirements.
What are the Benefits of Plasma Atomized Powders?
- Highly Spherical Particles: This improves flowability, packing density, and makes them ideal for 3D printing applications (https://met3dp.com/product/).
- Superior Purity: The inert gas environment minimizes contamination and gas entrapment, resulting in high-purity powders.
- Fine Particle Size Control: The process allows for precise control over particle size, enabling creation of intricate features in 3D printing.
What are the Applications of Plasma Atomized Powders?
- Additive Manufacturing (3D Printing): This is the primary application, where plasma-atomized powders are used to build complex metal parts.
- Spray Coating: These powders can be used to create wear-resistant and corrosion-resistant coatings.
- Cold Spray: Powders are used to create dense metallic coatings at lower temperatures.
- Metal Injection Molding (MIM): Powders are mixed with a binder to create a feedstock for intricate metal parts.
What are Some Limitations of Plasma Atomization?
- High Cost: The equipment and process control systems can be expensive.
- Energy Intensive: The high temperatures required consume significant energy.
- Limited Materials: Not all metals are suitable for plasma atomization.
Share On
MET3DP Technology Co., LTD is a leading provider of additive manufacturing solutions headquartered in Qingdao, China. Our company specializes in 3D printing equipment and high-performance metal powders for industrial applications.
Inquiry to get best price and customized Solution for your business!
Related Articles
About Met3DP
Recent Update
Our Product
CONTACT US
Any questions? Send us message now! We’ll serve your request with a whole team after receiving your message.
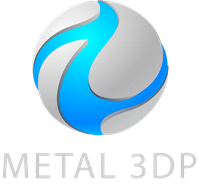
Metal Powders for 3D Printing and Additive Manufacturing