High Velocity Oxy-Fuel (HVOF) Spraying
Table of Contents
Introduction
Have you ever wondered how some materials can withstand extreme conditions while others fail miserably? The secret often lies in advanced coating technologies, and one of the most remarkable among them is High Velocity Oxy-Fuel (HVOF) spraying. But what exactly is HVOF spraying? How does it work? What makes it so special? Let’s dive into this fascinating world where science meets high performance.
Overview of High Velocity Oxy-Fuel (HVOF) Spraying
High Velocity Oxy-Fuel (HVOF) spraying is a thermal spray coating process that produces exceptionally strong, dense, and wear-resistant coatings. Unlike other coating methods, HVOF spraying uses a high-speed jet of gas to accelerate powdered coating materials to supersonic speeds, which are then deposited onto a substrate. This results in coatings that are not only incredibly durable but also highly precise and uniform.
Key Features of HVOF Spraying
- Supersonic Speeds: Coating materials are accelerated to speeds up to Mach 2.
- Dense Coatings: Low porosity levels lead to strong and durable coatings.
- Versatility: Can be used with a wide range of materials, including metals, ceramics, and carbides.
- High Adhesion: Strong bond between the coating and the substrate.
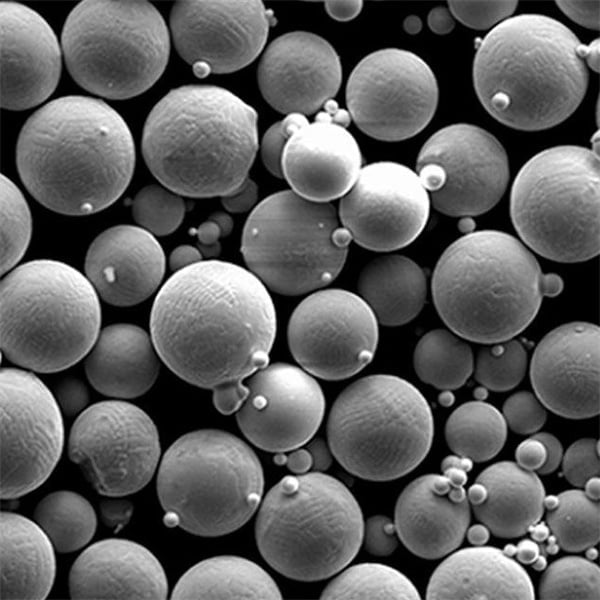
Composition and Properties of HVOF Metal Powders
Different metal powders are used in HVOF spraying, each with unique properties tailored to specific applications. Let’s explore some of the most popular ones:
Metal Powder | Composition | Properties | Applications |
---|---|---|---|
Tungsten Carbide (WC) | WC-Co, WC-CoCr | Extremely hard, wear-resistant, high melting point | Cutting tools, wear parts, aerospace components |
Chromium Carbide (CrC) | Cr3C2-NiCr, CrC-NiCr | High temperature resistance, corrosion resistance | Gas turbines, engines, chemical processing |
Aluminum Oxide (Al2O3) | Pure Al2O3 | High hardness, electrical insulation, wear resistance | Electrical components, insulating coatings |
Nickel-Chromium (NiCr) | NiCr, NiCrMo | High corrosion resistance, thermal stability | Marine equipment, industrial machinery |
Molybdenum (Mo) | Pure Mo, Mo-NiCr | High melting point, excellent thermal conductivity | Aerospace, automotive, electronics |
Stellite | Co-Cr-W, Co-Cr-Mo | High wear resistance, good corrosion resistance | Valves, bearings, cutting tools |
Inconel | Ni-Cr-Fe, Ni-Cr-Mo | Excellent high-temperature strength, corrosion resistance | Turbine blades, heat exchangers, rocket engines |
Stainless Steel | 316L, 304 | Corrosion resistance, good mechanical properties | Medical devices, food processing, marine applications |
Titanium Dioxide (TiO2) | Pure TiO2 | High hardness, chemical stability | Optical coatings, wear-resistant coatings |
Zirconium Dioxide (ZrO2) | Pure ZrO2 | High fracture toughness, thermal insulation | Thermal barrier coatings, structural ceramics |
Detailed Descriptions of Selected Metal Powders
- Tungsten Carbide (WC): Composed primarily of tungsten carbide and cobalt (WC-Co) or tungsten carbide and chromium (WC-CoCr), this powder is renowned for its hardness and wear resistance. It’s a top choice for applications demanding extreme durability, such as cutting tools and aerospace components.
- Chromium Carbide (CrC): With compositions like Cr3C2-NiCr, this powder excels in high-temperature and corrosive environments, making it ideal for gas turbines and engines.
- Aluminum Oxide (Al2O3): Known for its high hardness and electrical insulation properties, aluminum oxide is widely used in electrical components and insulating coatings.
- Nickel-Chromium (NiCr): NiCr alloys offer superb corrosion resistance and thermal stability, perfect for marine equipment and industrial machinery.
- Molybdenum (Mo): Pure molybdenum or Mo-NiCr blends provide excellent thermal conductivity and a high melting point, suitable for aerospace and automotive applications.
- Stellite: A cobalt-based alloy, Stellite is highly wear-resistant and corrosion-resistant, often used in valves, bearings, and cutting tools.
- Inconel: This nickel-chromium alloy is known for its strength at high temperatures and resistance to oxidation and corrosion. It’s widely used in turbines, heat exchangers, and rocket engines.
- Stainless Steel: Common grades like 316L and 304 offer a balance of corrosion resistance and mechanical properties, making them suitable for medical devices and marine applications.
- Titanium Dioxide (TiO2): With its high hardness and chemical stability, TiO2 is used in optical coatings and wear-resistant applications.
- Zirconium Dioxide (ZrO2): Known for its high fracture toughness and thermal insulation properties, ZrO2 is ideal for thermal barrier coatings and structural ceramics.
Applications of High Velocity Oxy-Fuel (HVOF) Spraying
HVOF spraying’s versatility makes it suitable for a wide range of applications across various industries. Let’s explore where this technology is making a significant impact:
Industry | Applications | Benefits |
---|---|---|
Aerospace | Turbine blades, landing gear, engine components | Enhanced wear resistance, high-temperature performance |
Automotive | Engine parts, pistons, turbochargers | Improved durability, reduced friction |
Oil & Gas | Drill pipes, valves, pumps | Corrosion resistance, extended service life |
Power Generation | Turbine components, boiler tubes | Thermal barrier coatings, oxidation resistance |
Medical | Orthopedic implants, surgical instruments | Biocompatibility, improved wear resistance |
Chemical Processing | Reactor vessels, heat exchangers | Corrosion resistance, chemical stability |
Marine | Propeller shafts, rudders, offshore structures | Corrosion protection, reduced maintenance |
Electronics | Semiconductor equipment, electrical connectors | Electrical insulation, wear resistance |
Mining | Drill bits, crushers, conveyor components | Increased wear resistance, reduced downtime |
Manufacturing | Molds, dies, cutting tools | Enhanced tool life, improved precision |
Benefits of HVOF Coatings in Different Industries
- Aerospace: HVOF coatings are essential for enhancing the performance and longevity of turbine blades, landing gear, and engine components, providing resistance to wear and high temperatures.
- Automotive: Engine parts, pistons, and turbochargers benefit from HVOF coatings by achieving improved durability and reduced friction, leading to better fuel efficiency and performance.
- Oil & Gas: In this industry, HVOF coatings protect drill pipes, valves, and pumps from corrosion, significantly extending their service life and reducing maintenance costs.
- Power Generation: Turbine components and boiler tubes coated with HVOF materials exhibit superior thermal barrier properties and oxidation resistance, improving overall efficiency.
- Medical: Orthopedic implants and surgical instruments coated with biocompatible HVOF materials experience enhanced wear resistance and longevity, ensuring better patient outcomes.
- Chemical Processing: Reactor vessels and heat exchangers benefit from HVOF coatings due to their excellent corrosion resistance and chemical stability, ensuring safe and efficient operations.
- Marine: HVOF coatings protect propeller shafts, rudders, and offshore structures from the harsh marine environment, reducing maintenance needs and extending service life.
- Electronics: Semiconductor equipment and electrical connectors benefit from the electrical insulation and wear resistance provided by HVOF coatings, ensuring reliable performance.
- Mining: Drill bits, crushers, and conveyor components coated with HVOF materials exhibit increased wear resistance, reducing downtime and improving productivity.
- Manufacturing: Molds, dies, and cutting tools with HVOF coatings enjoy enhanced tool life and improved precision, resulting in higher quality products and lower operational costs.
Advantages and Disadvantages of High Velocity Oxy-Fuel (HVOF) Spraying
Advantages | Disadvantages |
---|---|
High wear resistance | High initial setup cost |
Excellent bond strength | Requires skilled operators |
Low porosity coatings | Equipment maintenance can be complex |
Versatile material options | Limited to line-of-sight application |
High thermal and corrosion resistance | Potential for thermal stresses in some materials |
Precise control over coating thickness | Requires thorough substrate preparation |
Environmentally friendly compared to other methods | Not suitable for very large parts |
Minimal surface preparation needed for some coatings | Process can be noisy and produce fumes |
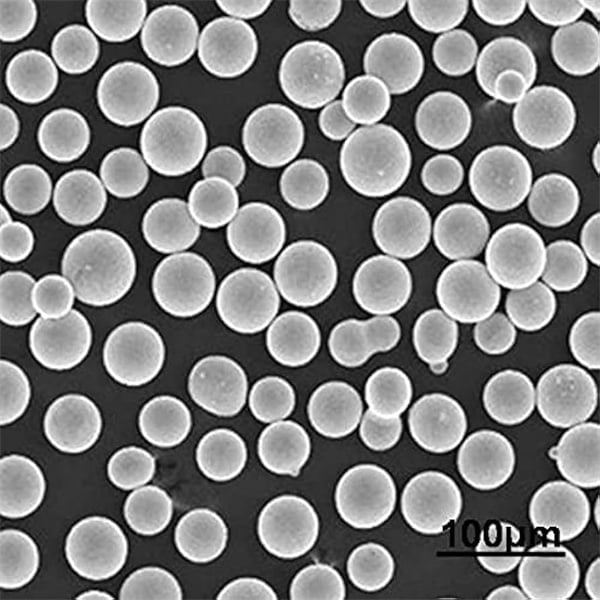
Detailed Analysis of HVOF Spraying
- Advantages:
- High Wear Resistance: HVOF coatings are known for their exceptional wear resistance, making them ideal for applications subjected to high abrasion and friction.
- Excellent Bond Strength: The supersonic speeds achieved in HVOF spraying result in coatings with excellent bond strength, ensuring they adhere well to the substrate.
- Low Porosity Coatings: The process produces coatings with low porosity, enhancing their durability and resistance to environmental factors.
- Versatile Material Options: HVOF spraying can be used with a wide range of materials, including metals, ceramics, and carbides, making it suitable for diverse applications.
- High Thermal and Corrosion Resistance: HVOF coatings provide superior resistance to high temperatures and corrosive environments, extending the lifespan of coated components.
- Precise Control Over Coating Thickness: The process allows for precise control over the thickness of the coating, ensuring uniformity and consistency.
- Environmentally Friendly: Compared to some other coating methods, HVOF spraying is relatively environmentally friendly, producing fewer pollutants.
- Minimal Surface Preparation: For some coatings, minimal surface preparation is needed, simplifying the application process.
- Disadvantages:
- High Initial Setup Cost: The equipment and setup required for HVOF spraying can be expensive, which may be a barrier for some businesses.
- Skilled Operators Required: The process requires skilled operators to ensure the quality and consistency of the coatings.
- Complex Equipment Maintenance: Maintaining HVOF spraying equipment can be complex and requires regular attention to ensure optimal performance.
- Limited to Line-of-Sight Application: HVOF spraying is limited to line-of-sight applications, which may restrict its use on certain complex geometries.
- Potential for Thermal Stresses: Some materials may experience thermal stresses during the HVOF spraying process, which can affect their performance.
- Thorough Substrate Preparation Required: Thorough substrate preparation is often necessary to achieve the best coating results, adding to the process time.
- Not Suitable for Very Large Parts: The process may not be suitable for very large parts, limiting its use in certain applications.
- Noisy and Fume-Producing: HVOF spraying can be noisy and produce fumes, necessitating proper safety measures and ventilation.
Specifications and Standards for HVOF Spraying
Specification | Details |
---|---|
Coating Thickness | Typically ranges from 50 microns to several millimeters |
Porosity | Generally less than 1% |
Bond Strength | Exceeds 10,000 psi (68.95 MPa) |
Hardness | Varies based on material, e.g., WC-Co coatings can reach up to 1500 HV |
Surface Finish | Achievable Ra values as low as 0.5 microns |
Deposition Rate | Typically 1-10 kg/hour, depending on material and parameters |
Maximum Operating Temperature | Can exceed 1000°C, depending on the material |
Environmental Resistance | Excellent resistance to corrosion, oxidation, and wear |
Application Tolerances | Can be controlled within ±0.025 mm for critical dimensions |
Standards Compliance | Meets standards such as ASTM, ISO, AMS, and specific industry requirements |
Standards and Certifications for HVOF Coatings
Standard | Description |
---|---|
ASTM C633 | Standard Test Method for Adhesion or Cohesion Strength of Thermal Spray Coatings |
ISO 14922 | Thermal Spraying – Quality Requirements for Manufacturers |
AMS 2447 | Thermal Spraying Coatings, General Requirements for Aerospace Applications |
DIN EN 657 | Thermal Spraying – Equipment, Processes, and Tests |
NACE RP0502 | Pipeline External Corrosion Direct Assessment Methodology |
SAE J2237 | High-Velocity Oxy-Fuel (HVOF) Thermal Spray Processes |
Suppliers and Pricing of HVOF Metal Powders
Supplier | Metal Powder | Price (per kg) | Region | Contact Details |
---|---|---|---|---|
Praxair Surface Technologies | Tungsten Carbide (WC) | $150 – $200 | North America, Europe | [email protected], +1-800-772-9247 |
Oerlikon Metco | Chromium Carbide (CrC) | $120 – $170 | Global | [email protected], +41-58-360-9600 |
Höganäs AB | Aluminum Oxide (Al2O3) | $50 – $80 | Global | [email protected], +46-10-516-5000 |
Kennametal Stellite | Stellite | $200 – $250 | North America, Europe | [email protected], +1-800-446-7738 |
Carpenter Technology | Inconel | $180 – $220 | Global | [email protected], +1-610-208-2000 |
HC Starck | Molybdenum (Mo) | $100 – $150 | North America, Europe | [email protected], +1-617-630-5800 |
AMETEK Specialty Metals | Nickel-Chromium (NiCr) | $130 – $170 | North America | [email protected], +1-610-647-2121 |
Sandvik Materials | Stainless Steel (316L, 304) | $80 – $120 | Global | [email protected], +46-8-456-1100 |
Treibacher Industrie AG | Titanium Dioxide (TiO2) | $70 – $110 | Europe | [email protected], +43-42-77-2666-0 |
Saint-Gobain | Zirconium Dioxide (ZrO2) | $90 – $140 | Global | [email protected], +33-1-47-62-30-00 |
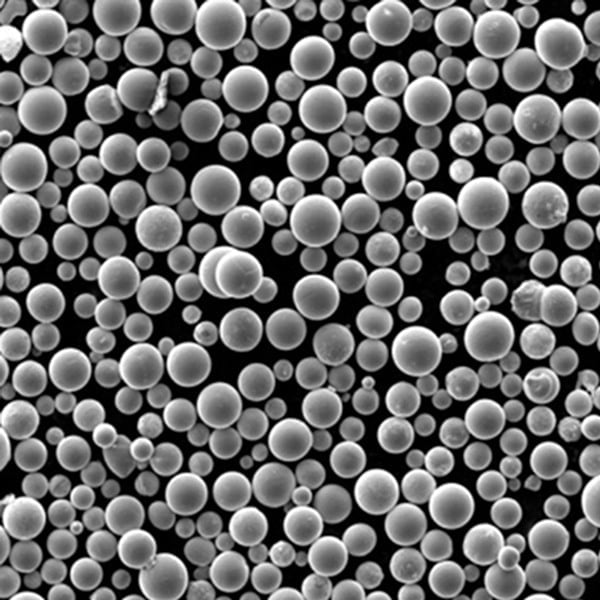
Comparing HVOF Spraying with Other Coating Methods
Coating Method | Advantages | Disadvantages |
---|---|---|
HVOF Spraying | High wear resistance, low porosity, versatile | High initial cost, skilled operators required |
Plasma Spraying | Can achieve higher temperatures, good for ceramics | Higher porosity, lower bond strength |
Cold Spraying | Minimal oxidation, low thermal stress | Lower bond strength, limited material options |
Flame Spraying | Cost-effective, simple equipment | Higher porosity, lower bond strength |
Detonation Spraying | Extremely high velocities, very dense coatings | Complex process, high cost |
Electroplating | Excellent for corrosion resistance, cost-effective | Limited to conductive materials, environmental concerns |
Physical Vapor Deposition (PVD) | High precision, thin coatings | Expensive, limited thickness |
Chemical Vapor Deposition (CVD) | Good for complex shapes, uniform coatings | High temperature process, expensive |
Galvanizing | Excellent corrosion resistance, cost-effective | Limited to zinc and alloys, thickness control issues |
HVOF vs. Plasma Spraying
- Advantages: HVOF spraying provides denser coatings with lower porosity compared to plasma spraying, resulting in superior wear resistance and bond strength.
- Disadvantages: Plasma spraying can achieve higher temperatures, making it better suited for certain ceramic coatings. However, plasma-sprayed coatings often have higher porosity and lower bond strength.
HVOF vs. Cold Spraying
- Advantages: HVOF spraying offers higher bond strength and a broader range of material options compared to cold spraying.
- Disadvantages: Cold spraying induces minimal thermal stress and oxidation, making it suitable for sensitive materials, but it generally provides lower bond strength.
FAQs
Question | Answer |
---|---|
What is HVOF spraying? | High Velocity Oxy-Fuel (HVOF) spraying is a thermal spray coating process that uses high-speed gas jets to apply durable, dense coatings. |
What materials can be used in HVOF spraying? | A variety of materials including metals, ceramics, and carbides such as tungsten carbide, chromium carbide, aluminum oxide, and more. |
What are the benefits of HVOF coatings? | Benefits include high wear resistance, excellent bond strength, low porosity, and high thermal and corrosion resistance. |
What industries use HVOF spraying? | Industries such as aerospace, automotive, oil & gas, power generation, medical, chemical processing, marine, electronics, and mining. |
How does HVOF spraying compare to other methods? | HVOF offers denser coatings and superior wear resistance compared to methods like plasma spraying, though it has higher initial costs. |
What are the limitations of HVOF spraying? | Limitations include |
Share On
MET3DP Technology Co., LTD is a leading provider of additive manufacturing solutions headquartered in Qingdao, China. Our company specializes in 3D printing equipment and high-performance metal powders for industrial applications.
Inquiry to get best price and customized Solution for your business!
Related Articles
About Met3DP
Recent Update
Our Product
CONTACT US
Any questions? Send us message now! We’ll serve your request with a whole team after receiving your message.
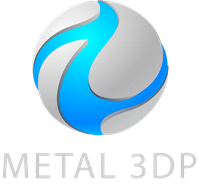
Metal Powders for 3D Printing and Additive Manufacturing