Highly Spherical Powders
Table of Contents
Imagine a world where tiny particles behaved predictably, flowing smoothly and packing tightly together. This isn’t science fiction; it’s the reality of highly spherical powders. These microscopic marvels are revolutionizing various industries, from 3D printing to thermal spraying. But what exactly makes them so special, and what types exist? Buckle up, because we’re diving deep into the fascinating world of highly spherical powders!
Overview of Highly Spherical Powders
Highly spherical powders, as the name suggests, are composed of individual particles that resemble perfect spheres. Unlike irregularly shaped powders, these tiny balls boast several advantages:
- Flowability: Imagine pouring sand versus ball bearings. Spherical powders flow effortlessly, making them ideal for automated processes like 3D printing and metal injection molding.
- Packing Density: Think of packing oranges in a box. Irregular shapes leave gaps, while spheres maximize space utilization. This translates to denser parts with superior mechanical properties in applications like powder metallurgy.
- Uniformity: Spheres are the epitome of consistency. Their uniform size and shape ensure consistent behavior in processes, leading to predictable results.
- Surface Area: While it might seem counterintuitive, a collection of spheres offers a surprisingly high total surface area compared to irregular shapes. This comes in handy for applications like catalysis, where a large surface area is crucial for optimal reactions.
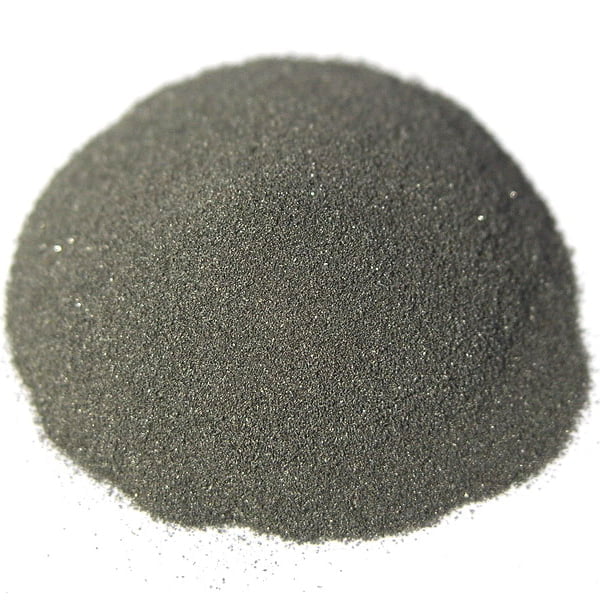
Compositional Variety of Highly Spherical Powders
Not all spheres are created equal. Highly spherical powders come in a diverse range of materials, each with unique properties:
Material | Description | Key Applications |
---|---|---|
Stainless Steel (316L, 17-4PH) | Versatile, corrosion-resistant alloys offering excellent mechanical strength. | 3D Printing, Metal Injection Molding, Thermal Spraying |
Titanium (Ti-6Al-4V, Grade 2) | Lightweight yet incredibly strong, ideal for aerospace and biomedical applications. | 3D Printing, Additive Manufacturing, Medical Implants |
Nickel Alloys (Inconel 625, Inconel 718) | High-temperature resistant with exceptional strength, perfect for demanding environments. | Aerospace Components, Gas Turbines, Heat Exchangers |
Aluminum (AlSi10Mg) | Lightweight and readily available, offering good castability and machinability. | 3D Printing, Automotive Parts, Heat Sinks |
Copper | Excellent thermal and electrical conductivity, making it valuable for electronics and heat transfer applications. | Additive Manufacturing, Electrical Components, Thermal Management Systems |
Tungsten | Incredibly dense and heat-resistant, used in high-performance applications. | Metal Injection Molding, Cutting Tools, Electrodes |
Molybdenum | High melting point and good creep resistance, ideal for high-temperature environments. | Heat Sinks, Furnaces, Rocket Engine Nozzles |
Tantalum | Biocompatible and highly corrosion-resistant, making it valuable for medical implants. | Tantalum Capacitors, Surgical Instruments, Biomedical Devices |
Niobium | Superconducting properties and high strength at cryogenic temperatures. | Superconducting Magnets, Nuclear Reactors, Particle Accelerators |
Cobalt-Chromium (CoCrMo) | Biocompatible and wear-resistant, widely used in artificial joints and implants. | Orthopedic Implants, Surgical Tools, Dental Applications |
This table provides a starting point, but the list of highly spherical powders extends far beyond. Researchers are constantly developing new materials with specific properties to meet the ever-evolving needs of various industries.
Applications of highly spherical powder
Highly spherical powders are finding their way into a multitude of applications, transforming how we design, build, and repair. Here are some key areas where their unique properties hold immense value:
- 3D Printing: Forget clunky, layered prints. Spherical powders enable the creation of smooth, near-net-shape components with exceptional mechanical properties. This technology is revolutionizing industries like aerospace, automotive, and medical.
- Metal Injection Molding (MIM): This process utilizes spherical powders to create complex, high-precision metal parts. Imagine intricate gears or tiny fasteners produced with incredible accuracy – that’s the power of MIM.
- Thermal Spraying: Worn-out parts get a new lease on life with thermal spraying. Spherical powders are melted and sprayed onto surfaces, creating protective coatings that resist wear, corrosion, and high temperatures.
- Powder Metallurgy (PM): This technique compresses and fuses spherical powders to create strong and durable metal parts. Think car parts, gears, and even tools – all potentially made using PM with highly spherical powders.
Specifications & Standards
By adhering to these standards, manufacturers ensure that the highly spherical powders they produce meet the specific needs of their customers. This not only guarantees consistent performance but also allows for easier comparison and selection of the right powder for a particular application.
Suppliers & Pricing: Finding the Right Fit
Sourcing high-quality highly spherical powders is crucial for successful applications. Here’s a breakdown of key considerations:
Supplier Reputation: Choosing a reputable supplier with a proven track record of quality and consistency is paramount. Look for companies with experience in producing spherical powders for your specific industry and desired material.
Material Selection: Ensure the supplier offers the type of spherical powder you need, considering factors like material composition, particle size, and sphericity.
Pricing and Availability: Highly spherical powders typically come with a higher price tag compared to irregular shapes. However, the cost should be weighed against the benefits of superior performance and efficient processing. Compare pricing and availability from different suppliers to find the best value for your needs.
Technical Support: A reliable supplier should offer technical support to assist you in selecting the right powder and optimizing your processes for successful implementation.
Examples of Suppliers:
Several companies specialize in the production and supply of highly spherical powders for various applications. Here are a few prominent examples:
- Höganäs AB: A leading global manufacturer of metal powders, offering a wide range of highly spherical powders in various materials, including steel, stainless steel, and copper.
- APEX Materials Technology: Specializes in high-performance metal powders, including spherical powders for additive manufacturing and thermal spraying applications.
- Sandvik Osprey: Provides a comprehensive selection of spherical powders for additive manufacturing, including titanium, nickel, and cobalt alloys.
- Praxair Surface Technologies: Offers a variety of spherical powders for thermal spraying applications, catering to industries like aerospace, energy, and automotive.
- Desktop Metal: A prominent player in the 3D printing space, also supplies spherical powders specifically optimized for their additive manufacturing systems.
These are just a few examples, and the list of suppliers continues to grow as the demand for highly spherical powders increases. It’s essential to research and compare different suppliers to find one that aligns with your specific needs and budget.
Comparison of Highly Spherical Powders
While all highly spherical powders offer certain advantages, their specific properties cater to different applications. Here’s a comparison of some popular choices:
Feature | Stainless Steel (316L) | Titanium (Ti-6Al-4V) | Nickel Alloy (Inconel 625) | Aluminum (AlSi10Mg) |
---|---|---|---|---|
Material | Versatile stainless steel | Lightweight and strong titanium | High-temperature resistant nickel alloy | Lightweight and castable aluminum |
Applications | 3D printing, MIM, thermal spraying | 3D printing, implants | Aerospace components, heat exchangers | 3D printing, automotive parts |
Advantages | Corrosion resistance, good mechanical strength | High strength-to-weight ratio, biocompatible | Excellent high-temperature performance | Lightweight, readily available |
Disadvantages | Higher cost compared to some options | Higher cost, reactive with some materials | High cost, limited availability in small sizes | Prone to oxidation at high temperatures |
Considerations | Overall balance of properties | Weight reduction and biocompatibility | High-temperature environments | Cost and ease of processing |
Similar comparisons can be made for other highly spherical powders like copper, tungsten, and cobalt-chromium. By carefully considering the material properties, desired application, and cost factors, you can select the most suitable spherical powder for your specific needs.
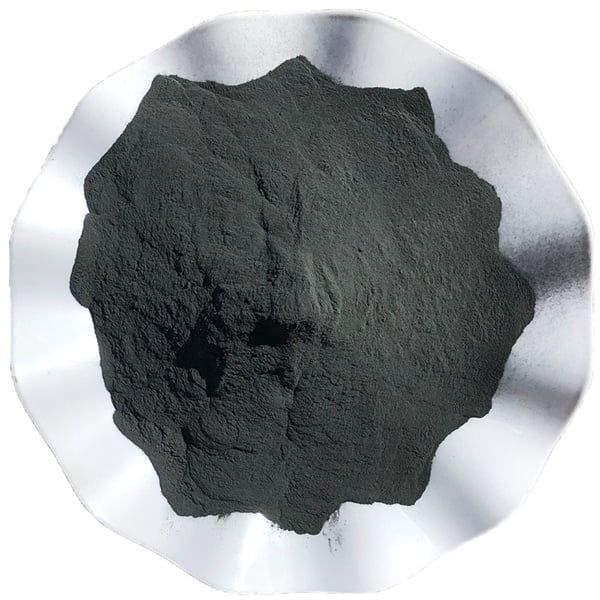
FAQs
Q: What are the benefits of using highly spherical powders compared to irregular shaped powders?
A: Highly spherical powders offer several advantages, including superior flowability, enhanced packing density, improved surface finish, and consistent performance due to their uniform size and shape. These benefits translate to efficient production processes, high-quality parts, and predictable results.
Q: Are highly spherical powders more expensive than irregular shaped powders?
A: Generally, yes. The production of highly spherical powders involves more complex processes, leading to a slightly higher cost compared to irregularly shaped powders. However, the benefits often outweigh the cost, especially in applications where consistent quality and high performance are crucial.
Q: What are some of the applications of highly spherical powders?
A: Highly spherical powders find use in various industries, including 3D printing, metal injection molding, thermal spraying, powder metallurgy, catalysis, battery technology, electronics, and biomedical applications. Their unique properties make them valuable for creating strong, lightweight, and high-precision parts.
Q: How do I choose the right type of highly spherical powder for my application?
A: Selecting the right powder involves considering several factors:
- Material properties: Choose a material that aligns with the desired properties for your final product. Consider factors like strength, weight, corrosion resistance, biocompatibility, and high-temperature performance.
- Application: Different applications have specific needs. For 3D printing, factors like powder flowability and laser compatibility are crucial. Thermal spraying might prioritize high melting point and wear resistance.
- Cost and availability: Highly spherical powders come at a premium compared to irregular shapes. Compare prices from different suppliers and weigh the cost against the benefits for your specific project.
- Particle size and distribution: The size and distribution of the spheres impact the final product’s properties and the chosen manufacturing process.
Consulting with a reputable supplier and researching industry standards for your chosen application can help you make an informed decision.
Q: What are some of the challenges associated with using highly spherical powders?
A: While highly spherical powders offer numerous advantages, some challenges exist:
- Higher cost: As mentioned earlier, the production process typically drives up the cost compared to irregular shapes.
- Limited material selection: The variety of highly spherical powders, while expanding, might not encompass every material needed for niche applications.
- Process optimization: Taking full advantage of these powders might require adjustments to existing manufacturing processes to optimize equipment settings and techniques.
Share On
MET3DP Technology Co., LTD is a leading provider of additive manufacturing solutions headquartered in Qingdao, China. Our company specializes in 3D printing equipment and high-performance metal powders for industrial applications.
Inquiry to get best price and customized Solution for your business!
Related Articles
About Met3DP
Recent Update
Our Product
CONTACT US
Any questions? Send us message now! We’ll serve your request with a whole team after receiving your message.
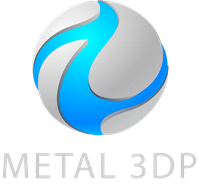
Metal Powders for 3D Printing and Additive Manufacturing