Highly Spherical Powder
Table of Contents
When it comes to advanced manufacturing, materials science, and cutting-edge technology, highly spherical powder is a game-changer. This unique form of powder boasts exceptional properties that make it ideal for various high-performance applications, from 3D printing to aerospace engineering. In this comprehensive article, we’ll delve into the world of highly spherical powder, discussing its characteristics, types, applications, advantages, and more.
Overview of Highly Spherical Powder
Highly spherical powder refers to finely divided particles that are almost perfectly round in shape. These powders are typically produced through advanced atomization techniques that ensure uniformity and consistency. The spherical shape is crucial because it enhances flowability, packing density, and reduces surface area, making these powders highly desirable in various industrial processes.
Key Characteristics of Highly Spherical Powder
- Shape: Nearly perfect spheres.
- Uniformity: Consistent size distribution.
- Flowability: Excellent, due to reduced friction.
- Density: High packing density, leading to better mechanical properties.
- Surface Area: Lower compared to irregular powders, affecting reactivity and sintering behavior.
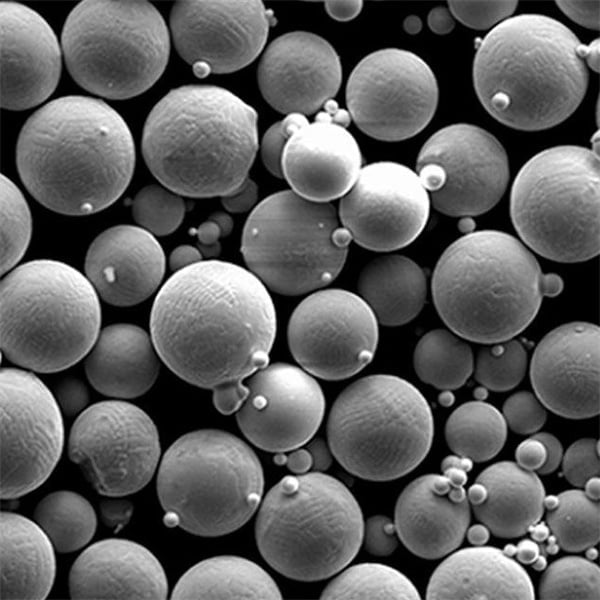
Types of Highly Spherical Powder
Various metals and alloys can be transformed into highly spherical powders. Here, we list ten specific metal powder models, along with their descriptions.
Metal Powder | Description |
---|---|
Aluminum (AlSi10Mg) | An alloy of aluminum with silicon and magnesium, known for its high strength-to-weight ratio and excellent thermal properties, ideal for aerospace and automotive applications. |
Stainless Steel (316L) | A low-carbon, high-chromium stainless steel powder that offers exceptional corrosion resistance and mechanical strength, widely used in medical devices and food processing. |
Titanium (Ti6Al4V) | A titanium alloy with aluminum and vanadium, renowned for its high strength, lightweight, and biocompatibility, commonly used in medical implants and aerospace components. |
Nickel Alloy (IN718) | A nickel-chromium alloy with excellent high-temperature strength and corrosion resistance, making it suitable for turbine blades and high-stress engine parts. |
Cobalt-Chrome (CoCrMo) | An alloy known for its wear resistance and biocompatibility, extensively used in dental and orthopedic implants. |
Copper (Cu) | Pure copper powder with superior electrical and thermal conductivity, used in electronics and heat exchanger components. |
Gold (Au) | Pure gold powder, valued for its conductivity and corrosion resistance, used in electronics, jewelry, and medical devices. |
Silver (Ag) | Pure silver powder, known for its highest electrical conductivity among metals, used in conductive inks and electronics. |
Iron (Fe) | Pure iron powder, used in metal injection molding and as a base material for various alloys. |
Tungsten Carbide (WC) | A hard material used for its wear resistance, often utilized in cutting tools and wear-resistant coatings. |
Composition, Properties, and Characteristics
Understanding the composition and properties of these highly spherical powders is essential for selecting the right material for specific applications. Below is a detailed table presenting the composition, key properties, and characteristics of each type of metal powder.
Metal Powder | Composition | Properties | Characteristics |
---|---|---|---|
Aluminum (AlSi10Mg) | Al, Si (10%), Mg (0.5%) | Lightweight, high strength | Good thermal conductivity, corrosion resistance |
Stainless Steel (316L) | Fe, Cr (16-18%), Ni (10-14%), Mo (2-3%) | High strength, corrosion-resistant | Excellent mechanical properties, biocompatible |
Titanium (Ti6Al4V) | Ti, Al (6%), V (4%) | High strength, lightweight | Biocompatible, corrosion-resistant |
Nickel Alloy (IN718) | Ni, Cr (17-21%), Fe (balance), Nb (4.75-5.5%) | High-temperature strength | Oxidation and corrosion-resistant |
Cobalt-Chrome (CoCrMo) | Co, Cr (27-30%), Mo (5-7%) | Wear-resistant, biocompatible | Excellent hardness and corrosion resistance |
Copper (Cu) | Pure Cu | High conductivity | Excellent electrical and thermal properties |
Gold (Au) | Pure Au | High conductivity, corrosion-resistant | Non-reactive, biocompatible |
Silver (Ag) | Pure Ag | Highest electrical conductivity | Anti-microbial, high reflectivity |
Iron (Fe) | Pure Fe | Magnetic, malleable | Good base for alloys, high strength |
Tungsten Carbide (WC) | WC (with Co binder) | Extremely hard | Wear-resistant, high melting point |
Applications of Highly Spherical Powder
Highly spherical powders are employed in a variety of applications due to their unique properties. Let’s explore the different areas where these powders make a significant impact.
Application | Description |
---|---|
3D Printing (Additive Manufacturing) | Utilized for creating complex and precise components with excellent mechanical properties. Powders like AlSi10Mg, 316L, and Ti6Al4V are commonly used. |
Aerospace | High-performance materials like IN718 and Ti6Al4V are used in critical components due to their strength and lightweight properties. |
Medical Devices | Materials such as 316L stainless steel and CoCrMo are used for their biocompatibility and corrosion resistance in implants and surgical instruments. |
Electronics | Copper and silver powders are essential for their electrical conductivity, used in conductive inks and circuit boards. |
Automotive | Aluminum and stainless steel powders are used to produce lightweight and high-strength parts for improved fuel efficiency and performance. |
Tooling and Wear-resistant Coatings | Tungsten carbide powders are employed for their hardness and durability in cutting tools and protective coatings. |
Jewelry | Gold and silver powders are used to create intricate and high-quality jewelry pieces. |
Energy Sector | Nickel alloys like IN718 are used in turbine blades and other high-stress components due to their resistance to extreme conditions. |
Food Processing | 316L stainless steel is used in equipment and components that require hygiene and corrosion resistance. |
Heat Exchangers | Copper powders are used for their excellent thermal conductivity in heat exchanger components. |
Specifications, Sizes, Grades, and Standards
When selecting highly spherical powders, it’s crucial to consider the specifications, sizes, grades, and standards to ensure optimal performance for your specific application.
Metal Powder | Specification | Size Range (µm) | Grades | Standards |
---|---|---|---|---|
Aluminum (AlSi10Mg) | ASTM B928 | 10-50 | Grade 2 | AMS 4288 |
Stainless Steel (316L) | ASTM A276 | 10-45 | Grade F | ISO 5832-1 |
Titanium (Ti6Al4V) | ASTM F1472 | 15-53 | Grade 23 | AMS 4907 |
Nickel Alloy (IN718) | ASTM B637 | 15-45 | Grade 1 | AMS 5662 |
Cobalt-Chrome (CoCrMo) | ASTM F75 | 10-50 | Grade 2 | ISO 5832-4 |
Copper (Cu) | ASTM B170 | 10-45 | Grade 1 | ASTM F2182 |
Gold (Au) | ASTM B562 | 10-40 | Grade 4N | ISO 9202 |
Silver (Ag) | ASTM B748 | 10-40 | Grade 4N | ISO 9202 |
Iron (Fe) | ASTM B214 | 10-45 | Grade 1 | ISO 3325 |
Tungsten Carbide (WC) | ASTM B777 | 5-30 | Grade 1 | ISO 5755 |
Suppliers and Pricing Details
When it comes to procuring highly spherical powders, understanding the market landscape is essential. Below, we provide a table of prominent suppliers and pricing details for various metal powders.
Metal Powder | Supplier | Pricing (per kg) | Notes |
---|---|---|---|
Aluminum (AlSi10Mg) | AP&C | $120 – $150 | High purity, consistent supply |
Stainless Steel (316L) | Sandvik | $80 – $100 | Widely available, competitive pricing |
Titanium (Ti6Al4V) | Arcam | $200 – $250 | High-quality, aerospace-grade |
Nickel Alloy (IN718) | Carpenter | $180 – $220 | Excellent high-temp performance |
Cobalt-Chrome (CoCrMo) | HC Starck | $150 – $190 | Superior wear resistance |
Copper (Cu) | GKN Powder Metallurgy | $50 – $70 | Excellent conductivity, economical |
Gold (Au) | Materion | $55,000 – $60,000 | High-value, specialized applications |
Silver (Ag) | Ames Goldsmith | $800 – $1,000 | High conductivity, premium pricing |
Iron (Fe) | Höganäs | $10 – $20 | Cost-effective, versatile use |
Tungsten Carbide (WC) | Global Tungsten & Powders | $400 – $500 | High hardness, premium applications |
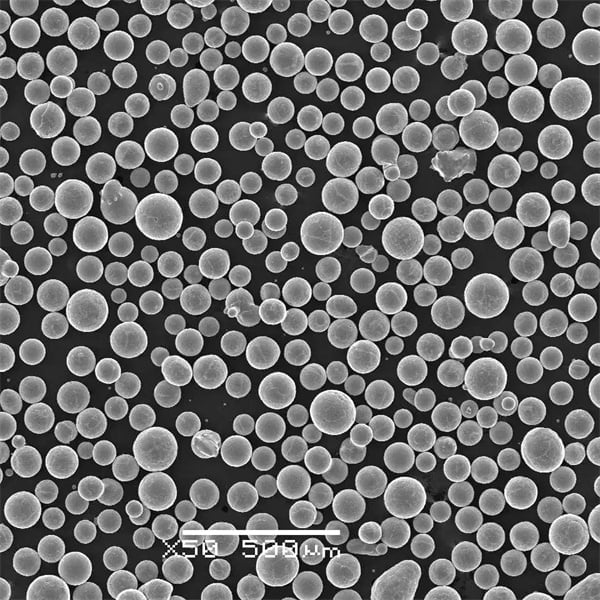
Advantages of Highly Spherical Powder
Highly spherical powders offer numerous benefits that make them superior to irregularly shaped powders in many applications. Here’s a detailed look at their advantages:
- Improved Flowability: The spherical shape reduces interparticle friction, enhancing flowability, which is crucial for applications like 3D printing and powder metallurgy.
- High Packing Density: Spherical powders pack more efficiently, resulting in higher density components with superior mechanical properties.
- Consistent Layering: In additive manufacturing, spherical powders spread more uniformly, leading to better quality and precision in the final product.
- Reduced Oxidation: Lower surface area minimizes oxidation, especially in reactive metals like aluminum and titanium, maintaining the powder’s integrity during processing.
- Enhanced Surface Finish: Components produced with spherical powders often have smoother surfaces, reducing the need for extensive post-processing.
Disadvantages of Highly Spherical Powder
Despite their numerous benefits, highly spherical powders also come with some limitations:
- Higher Production Costs: Advanced atomization techniques required for producing highly spherical powders can be more expensive compared to traditional methods.
- Limited Availability: Not all metals and alloys can be easily converted into highly spherical powders, limiting material options.
- Specialized Equipment Needed: Handling and processing highly spherical powders often require specialized equipment, which can increase initial setup costs.
- Potential for Segregation: In some mixtures, spherical powders might segregate due to differences in size and density, leading to uneven material properties.
Comparing Highly Spherical Powders: Pros and Cons
Aspect | Advantages | Disadvantages |
---|---|---|
Flowability | Improved due to reduced friction | None significant |
Packing Density | Higher, leading to better mechanical properties | None significant |
Production Cost | High-quality final product | Higher initial cost |
Material Options | Excellent for specific high-performance alloys | Limited to certain metals |
Equipment | Specialized for optimal results | Higher setup costs |
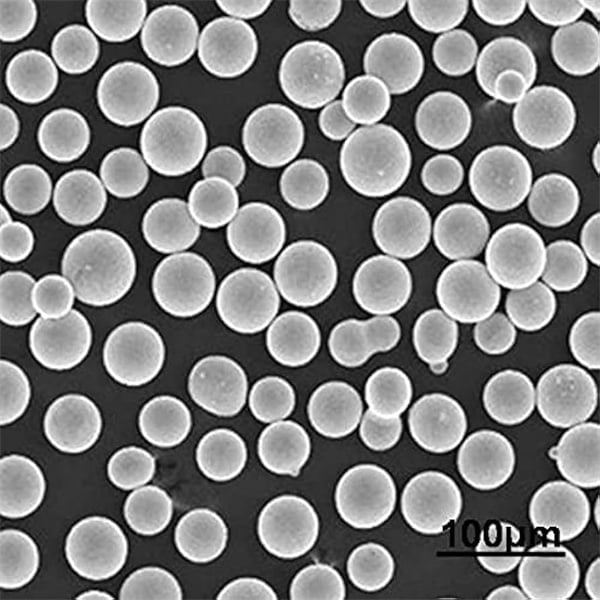
FAQ
Q: What is highly spherical powder?
A: Highly spherical powder consists of finely divided particles that are almost perfectly round, offering superior flowability, packing density, and consistency in various applications.
Q: How are highly spherical powders produced?
A: These powders are typically produced through advanced atomization techniques such as gas atomization, plasma atomization, or centrifugal atomization, ensuring uniformity and spherical shape.
Q: What are the common applications of highly spherical powder?
A: Common applications include 3D printing, aerospace, medical devices, electronics, automotive, tooling, jewelry, energy sector, food processing, and heat exchangers.
Q: What are the advantages of using highly spherical powders in 3D printing?
A: Highly spherical powders improve layer consistency, enhance flowability, and result in smoother surface finishes and better mechanical properties in 3D printed components.
Q: Are there any limitations to using highly spherical powders?
A: Yes, they can be more expensive to produce, may require specialized equipment, and not all metals can be easily converted into highly spherical powders.
Q: Which metals are commonly available as highly spherical powders?
A: Metals like aluminum, stainless steel, titanium, nickel alloys, cobalt-chrome, copper, gold, silver, iron, and tungsten carbide are commonly available as highly spherical powders.
Conclusion
In the ever-evolving landscape of advanced manufacturing and materials science, highly spherical powders play a pivotal role. Their unique properties, ranging from superior flowability to high packing density, make them indispensable in high-performance applications. By understanding the various types of highly spherical powders, their compositions, properties, and applications, industries can make informed decisions to enhance their products and processes. Whether you’re delving into the realm of 3D printing, aerospace engineering, or medical device manufacturing, highly spherical powders are the key to unlocking new possibilities and achieving unparalleled results.
Share On
MET3DP Technology Co., LTD is a leading provider of additive manufacturing solutions headquartered in Qingdao, China. Our company specializes in 3D printing equipment and high-performance metal powders for industrial applications.
Inquiry to get best price and customized Solution for your business!
Related Articles
About Met3DP
Recent Update
Our Product
CONTACT US
Any questions? Send us message now! We’ll serve your request with a whole team after receiving your message.
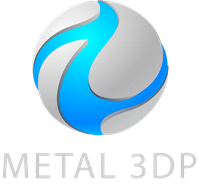
Metal Powders for 3D Printing and Additive Manufacturing