HIP metal powders
Table of Contents
HIP or hot isostatic pressing uses heat and pressure to consolidate biocompatible metal powders into complex shapes suitable for hip replacement implants needing a balance of strength, longevity and bone integration ability. This guide covers key alloy types, production methods, characteristics, applications, specifications and comparisons of HIP metal powders for hip implants.
Overview of HIP Metal Powders for Orthopedics
Hot isostatic pressing provides near net shape consolidation of precursor metal powders while retaining customizable material properties necessary in joint replacement implant components needing to support human biomechanical forces.
Standard alloys pressed into hip socket shells, femoral stems/heads and acetabular cup liners via the HIP technique include:
- Cobalt chromium alloys – high strength with metallic biocompatibility
- Titanium alloys like Ti6Al4V ELI – lower modulus than steel matching bone
- Stainless steel powders – highest ductility and fracture toughness
- Tantalum alloys – enhanced bone in-growth with porous constructs
These alloy powders are compacted into complex shapes using combinations of elevated temperature exposure (up to 2000°C) and isostatic pressure (100 to 300 MPa) in specially designed HIP vessels to produce precise medical hardware.
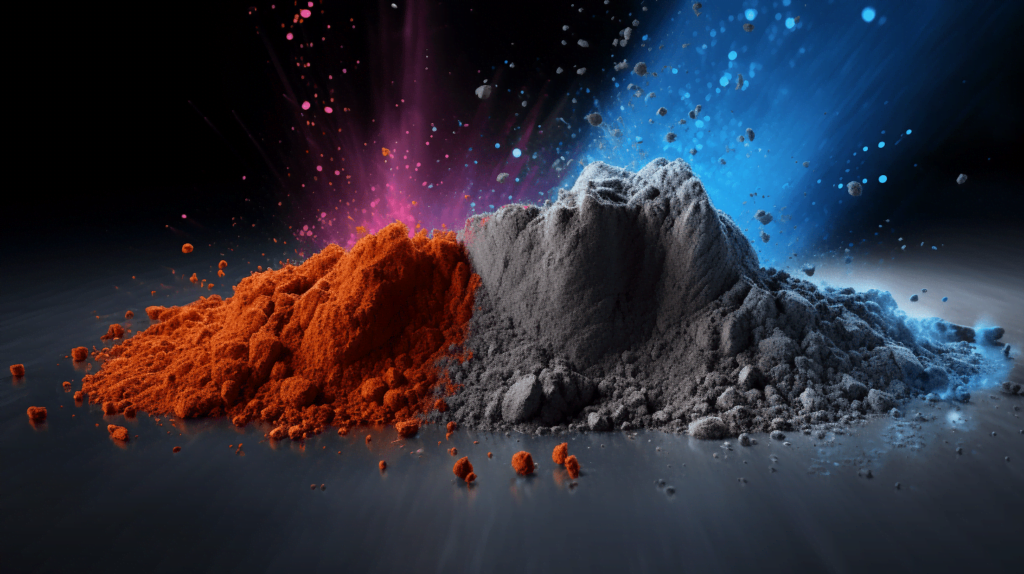
Types of HIP Metal Powder Alloy Compositions
Table 1: Common standard compositions and material attributes
Alloy Type | Typical Composition | Key Properties |
---|---|---|
Cobalt Alloys | Co-28Cr-6Mo Extra low carbon grade | Excellent wear resistance; high UTS and hardness |
Titanium Alloys | Ti-6Al-4V Vanadium free grade | Low density; moderate strength; bio-inertness |
Stainless Steel | Custom 316L blends Nitrogen enhanced | High ductility and fracture toughness; Biocompatible |
Tantalum Alloys | Ta-10W | Porous bone in-growth ability; bio-inert; radio-opaque |
Strict controls during powder production and hot pressing ensures high purity, essential for long term implant performance without accelerated wear or corrosion.
Production Methods for HIP Metal Powders
Table 2: Key powder fabrication techniques to make raw materials
Method | Description | Characteristics |
---|---|---|
Gas Atomization | Inert gas breaks up metal stream | Spherical particle shape distribution |
Plasma Atomization | Plasma energy used for disintegration | Finer <50 micron powder sizes |
Hydrogenation-Dehydriding | Alloying via hydrogen absorption-removal | Softer powder fabricability |
Electrolytic | Controlled uneven metal electrolytic deposition | Resultant porous structure |
Metal Injection Molding | Binder mixing and shaping before HIP | Complex net shape capability |
While gas atomized pre-alloys offer moderate production rates and control over impurities like oxygen, the newer plasma atomization and metal injection molding with binders allow smaller size distributions for finer medical hardware geometries needed.
Characteristics and Properties
Table 3: Typical technical properties for HIP orthopedic implant metal powders
Property | Measurement | Description |
---|---|---|
Composition | Makrowser Spectrometer | Verifies alloying percentages |
Particle size | Laser diffraction | Distribution P80% level |
Particle shape | SEM imaging | Sphericity consistency affects press density |
Flow rates | Hall flowmeter | Angle of repose indicates cohesiveness |
Tap density | >90% theoretical achievable | Higher values improve consolidation |
Surface oxide | Energy dispersive X-ray spectroscopy | Minimized for biocompatibility |
Hardness | Post sintered Rockwell | 54-65 HRC for hip alloys |
Tensile strength | 750-1300 MPa | Needed to support body dynamic loads |
Elastic modulus | 50-200 GPa | Matching natural bone avoids stress shielding |
Grain size | 1-5 microns | Finer is better; indicates uniformity |
Besides chemical purity, the factors critically determining performance – optimum particle packing during HIP runs, avoidance of internal porosity in finished hardware, fine microstructural uniformity assisting surface finishing.
Applications of HIP Metal Powders in Orthopedics
Table 4: Major implant device applications
Components | Alloy Choices |
---|---|
Femoral heads | Cobalt alloys, stainless steel |
Acetabular cups | Titanium alloys, tantalum porous constructs |
Stems, sockets | Titanium alloys, cobalt alloys |
Bone plates, Screws | Stainless steel powders |
Dental implants | Titanium alloy and Ta-W alloy powders |
Spinal, maxillofacial sections | Cobalt alloys, tantalum alloys |
HIPping enables fabrication of monolithic one-piece implants not possible through forging, casting or machining – improving reliability and osseo-integration.
The tailored combinations of strength, ductility, corrosion resistance bio-compatibility and imaging characteristics make hot isostatic pressing the technique of choice for producing complex joint replacement devices.
ISO Standards for HIP Orthopedic Alloy Powders
Table 5: Key global standards followed by orthopedic HIP metal powder specifications:
Standard | Materials | Validation Aspects |
---|---|---|
ASTM F75 | Cobalt alloys | Chemistry, mechanical properties |
ISO 5832-4 | Cobalt alloys | F75 equivalence verified |
ASTM F1108 | Cobalt alloys | Loose powder testing methods |
ISO 5832-11 | Titanium/tantalum alloys | Chemistry, toxicity |
ASTM F1580 | Titanium alloys | Powder production method focus |
ASTM F138 | Stainless steels | Steel chemistry, grain sizes |
ISO 5832-1 | Stainless steels | Specification for surgical grade |
These give guide target chemistry ranges, permissible impurities, porosity limits, advisable powder production routes, raw material traceability needs, plus post-HIP performance benchmarks and biological reactivity thresholds ensuring patient safety and device efficacy over long implanted lifespan.
Supplier Landscape
Table 6: Major global suppliers and powder price ranges:
Company | Materials | Price per kg |
---|---|---|
Carpenter Technologies | Cobalt, Titanium | $90-120 |
ATI | Titanium, Tantalum, Cobalt | $100-150 |
Praxair | Cobalt, Titanium | $70-100 |
OSAKA Titanium Technologies | Titanium, Tantalum alloys | $80-130 |
As hip replacement demand rises with aging populations, additional plasma atomization capacity is expected to come online lowering powder costs. Currently dollar value kilo prices depend on order volumes and exact composition.
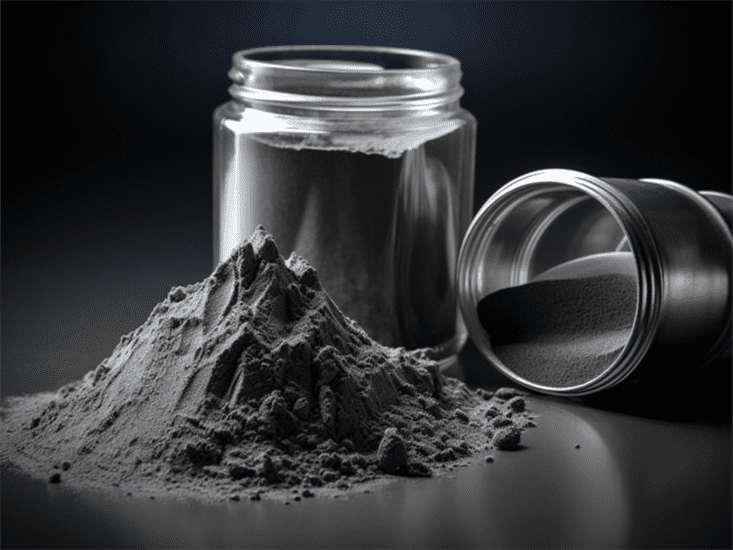
Comparative Pros and Cons vs Alternatives
Table 7: HIP implant alloys versus other material options like polymers and ceramics
Pros | Cons |
---|---|
Higher fatigue strength and fracture resistance | Metal corrosion/ion risks needing mitigation |
Withstand cyclic biomechanical stresses | Limited for younger more active patients |
No toxic debris; stable interface | Costlier than other options |
Work better for larger patients | Can interfere with medical imaging |
For the elderly with lower activity levels, the advantages of long term metallic construct survivability and bone in-growth offered by hip alloys outweigh potential downsides relative to other material choices still evolving for reliability over decades.
FAQ
Q: How often are HIP metal powder based hip implants used relative to other materials?
Metallic alloys still constitute almost 70% of total hip arthroplasties in patients over 60 years old given clinical history, though use of polymer and ceramic alternatives is rising in younger more active recipients.
Q: What post-HIP finishing steps prepare powders for medical device integration?
Typical post-HIP steps include – support removal via machining/polishing, passivation and sterilization techniques like Ethylene Oxide or gamma irradiation required for sterile surgical integration into patient anatomy.
Share On
MET3DP Technology Co., LTD is a leading provider of additive manufacturing solutions headquartered in Qingdao, China. Our company specializes in 3D printing equipment and high-performance metal powders for industrial applications.
Inquiry to get best price and customized Solution for your business!
Related Articles
About Met3DP
Recent Update
Our Product
CONTACT US
Any questions? Send us message now! We’ll serve your request with a whole team after receiving your message.
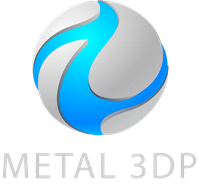
Metal Powders for 3D Printing and Additive Manufacturing