Overview of IN625 Powder
Table of Contents
IN625 is a nickel-based superalloy powder widely used in various high-temperature applications due to its exceptional strength, oxidation resistance, and corrosion resistance. This advanced engineering material finds applications in industries such as aerospace, chemical processing, and energy production. The unique composition and properties of IN625 powder make it an excellent choice for manufacturing components through additive manufacturing processes like selective laser melting (SLM) and direct metal laser sintering (DMLS).
IN625 Powder Composition
Element | Weight % |
---|---|
Nickel (Ni) | 58 min |
Chromium (Cr) | 20 – 23 |
Molybdenum (Mo) | 8 – 10 |
Niobium (Nb) + Tantalum (Ta) | 3.15 – 4.15 |
Iron (Fe) | 5 max |
Silicon (Si) | 0.5 max |
Aluminum (Al) | 0.4 max |
Titanium (Ti) | 0.4 max |
Cobalt (Co) | 1 max |
Carbon (C) | 0.1 max |
Manganese (Mn) | 0.5 max |
IN625 is a nickel-chromium alloy with significant additions of molybdenum and niobium. The high nickel content provides excellent resistance to a wide range of corrosive environments, while chromium enhances oxidation resistance and improves strength at elevated temperatures. Molybdenum contributes to resistance against pitting and crevice corrosion, and niobium improves the alloy’s strength through solid solution strengthening and precipitation hardening.
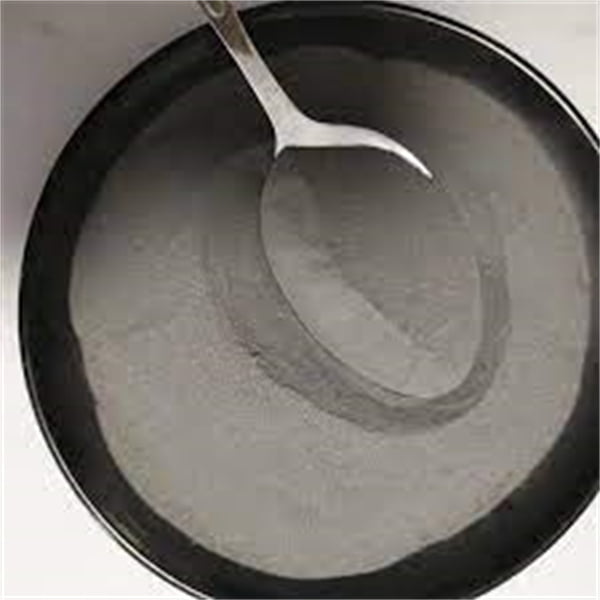
Key Properties of IN625 Powder
IN625 powder isn’t your average metallic dust. This nickel-based superhero boasts a unique blend of properties that make it a true champion in demanding environments. Let’s delve into its key characteristics:
Unwavering Strength at High Temperatures: Imagine a material that thrives where others melt. IN625 powder does just that, retaining its remarkable strength even at scorching temperatures reaching 1300°F (700°C). This makes it the go-to choice for jet engine components, gas turbines, and other applications where heat is no joke.
Corrosion Resistance Like a Boss: Harsh chemicals, salty environments, acidic baths – IN625 powder shrugs them all off with nonchalant ease. Its exceptional resistance to corrosion ensures longevity and reliability in challenging chemical processing plants, oil and gas pipelines, and marine applications.
Welding Made Easy: Unlike some finicky materials, IN625 powder readily welcomes the welder’s touch. Various techniques can be employed to seamlessly join pieces, making it ideal for fabricating intricate components with ease.
Biocompatibility: A Friend to the Body: IN625 powder plays nice with human tissue, making it a promising candidate for medical devices. This biocompatible nature opens doors for advancements in prosthetics, implants, and other applications where safety and integration with the body are paramount.
But wait, there’s more! IN625 powder also boasts impressive ductility and malleability, allowing it to be shaped and formed into complex geometries. Additionally, its resistance to oxidation further enhances its durability in diverse environments.
Industrial Applications of IN625 Powder
Application Area | Examples |
---|---|
Aerospace | Turbine blades, combustion chambers, exhaust systems |
Chemical Processing | Piping, valves, pump components, reactor vessels |
Oil & Gas | Well-head equipment, subsea components, drilling tools |
Power Generation | Heat exchangers, boiler tubing, steam turbine components |
Nuclear Energy | Control rod assemblies, steam generator tubing |
Medical | Implants, surgical instruments |
The exceptional properties of IN625 superalloy powder make it suitable for a wide range of demanding applications, particularly in high-temperature environments or corrosive atmospheres. Its high strength at elevated temperatures, combined with excellent oxidation and corrosion resistance, allow for the production of components that can withstand harsh operating conditions.
IN625 Powder Specifications and Standards
Specification | Description |
---|---|
AMS 5666 | Nickel alloy composition for forgings and rings |
AMS 5837 | Nickel alloy composition for castings |
AMS 5599 | Nickel alloy composition for powder metallurgy and additive manufacturing |
ASTM B443 | Standard specification for nickel-chromium-molybdenum-columbium alloy and nickel-chromium-molybdenum-silicon alloy plate, sheet, and strip |
ASME SB-443 | Nickel-chromium-molybdenum-columbium alloy and nickel-chromium-molybdenum-silicon alloy plate, sheet, and strip |
These specifications outline the chemical composition, mechanical properties, and quality requirements for IN625 alloy in various product forms, including powder, castings, forgings, and wrought products.
IN625 Powder Suppliers and Pricing
Several reputable suppliers offer IN625 superalloy powder for additive manufacturing and other applications. The pricing can vary based on factors such as particle size distribution, chemistry, and quantity. Here are a few examples of suppliers and their approximate pricing:
Supplier | Price Range ($/kg) | Particle Size (μm) |
---|---|---|
Carpenter Additive | $75 – $150 | 15 – 53 |
Sandvik Osprey | $80 – $160 | 15 – 45 |
EOS GmbH | $90 – $170 | 20 – 63 |
LPW Technology | $85 – $155 | 15 – 53 |
Praxair Surface Technologies | $70 – $140 | 15 – 45 |
Please note that these prices are approximate and may vary based on specific requirements, order quantities, and market conditions.
Pros and Cons of IN625 Powder
Pros | Cons |
---|---|
High strength at elevated temperatures | Relatively expensive compared to some other alloys |
Excellent oxidation and corrosion resistance | Limited availability of powder sizes and chemistries |
Good weldability and fabricability | Potential health and safety concerns due to nickel content |
Resistance to stress corrosion cracking | May require post-processing for certain applications |
Retention of properties after prolonged exposure | Limited formability in wrought form |
While IN625 powder offers exceptional high-temperature strength and corrosion resistance, its relatively high cost and potential health concerns due to its nickel content should be considered. Additionally, the availability of specific powder sizes and chemistries may be limited compared to other alloys.
How does IN625 powder compare to other superalloy powders?
When it comes to high-temperature strength and oxidation resistance, IN625 is often compared to other nickel-based superalloys like Inconel 718 and Hastelloy X. Let’s take a closer look at how IN625 stacks up against these alloys:
IN625 vs. Inconel 718
Compared to Inconel 718, IN625 offers superior oxidation resistance and better resistance to stress corrosion cracking. However, Inconel 718 has higher strength at temperatures below 650°C, making it a better choice for applications in this temperature range. IN625 is typically more expensive than Inconel 718.
IN625 vs. Hastelloy X
Both IN625 and Hastelloy X exhibit excellent oxidation resistance and corrosion resistance, but IN625 has better weldability and fabricability. Hastelloy X is often preferred for its resistance to high-temperature sulfidation, making it a popular choice for petrochemical applications. However, IN625 is generally stronger at elevated temperatures.
IN625 vs. Other Alloys
When compared to cobalt-based superalloys like Haynes 188 or Stellite 6, IN625 offers better resistance to oxidation and corrosion, but these cobalt alloys may have superior wear resistance and higher hot hardness. Compared to stainless steels, IN625 has significantly better high-temperature strength and oxidation resistance, but at a higher cost.
It’s important to carefully evaluate the specific application requirements, operating conditions, and cost considerations when selecting the most suitable superalloy powder for a given application.
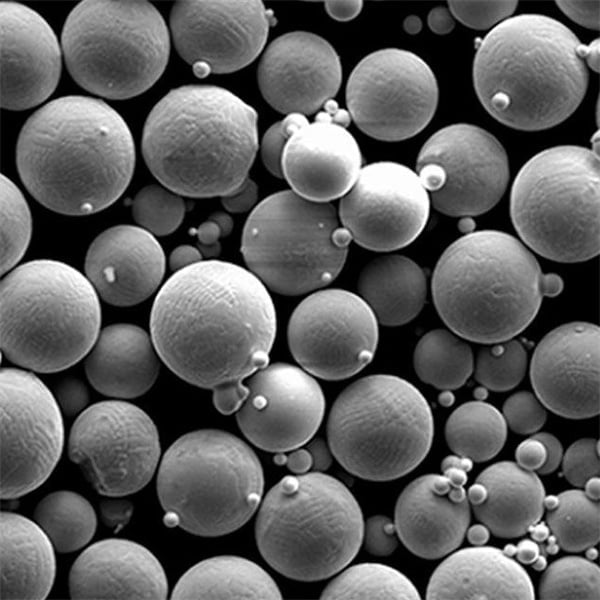
FAQ
Question | Answer |
---|---|
What is the melting point of IN625 powder? | The melting point of IN625 alloy is approximately 1290-1350°C (2350-2460°F). |
Can IN625 powder be used for welding applications? | Yes, IN625 powder can be used for various welding processes, including gas tungsten arc welding (GTAW), gas metal arc welding (GMAW), and plasma arc welding (PAW). |
How does the particle size distribution affect the properties of IN625 powder? | Smaller particle sizes generally result in better packing density and higher resolution in additive manufacturing processes. However, very fine powders may be more prone to oxidation and handling issues. |
Is IN625 powder suitable for high-temperature corrosive environments? | Yes, IN625 powder is an excellent choice for components that will be exposed to high temperatures and corrosive environments, such as those found in chemical processing, oil and gas, and power generation industries. |
What are the typical post-processing techniques for IN625 powder components? | Common post-processing techniques for IN625 powder components include hot isostatic pressing (HIP), heat treatment, machining, and surface finishing operations like grinding or polishing. |
Share On
MET3DP Technology Co., LTD is a leading provider of additive manufacturing solutions headquartered in Qingdao, China. Our company specializes in 3D printing equipment and high-performance metal powders for industrial applications.
Inquiry to get best price and customized Solution for your business!
Related Articles
About Met3DP
Recent Update
Our Product
CONTACT US
Any questions? Send us message now! We’ll serve your request with a whole team after receiving your message.
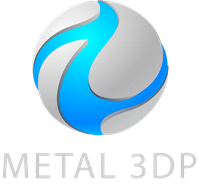
Metal Powders for 3D Printing and Additive Manufacturing