Inconel 3D Printing:Advantages,Types,Applications
Table of Contents
Overview of Inconel 3D Printing
Inconel 3D printing, also known as additive manufacturing with Inconel alloys, refers to the fabrication of components from Inconel metal powders using 3D printing technologies. Inconel is a family of nickel-chromium-based superalloys known for their high strength, corrosion resistance and heat resistance properties. Some of the key features of Inconel 3D printing are:
- Allows fabrication of complex, lightweight geometries not possible with conventional manufacturing
- Good mechanical properties and material performance comparable to wrought Inconel parts
- Parts can be printed on-demand without need for dies, molds or special tooling
- Reduced lead time and costs for small batch production
- Ability to create optimized shapes and designs by topology optimization
- Wide range of industries using Inconel 3D printing parts include aerospace, automotive, oil and gas, medical, chemical processing
Some advantages and limitations of Inconel 3D printing to consider:
Advantages of Inconel 3D Printing
- Complex geometries and lightweight structures
- Customized, optimized designs
- Reduced waste – only use required amount of material
- Shorter lead times, reduced costs for small batches
- Easy to make design changes and iterations
- Consolidated assemblies and reduced part count
- Buy parts on-demand without minimum order quantities
Limitations of Inconel 3D Printing
- Higher costs for large production volumes
- Slower build speeds than other metals like stainless steels
- Post-processing may be required to achieve desired surface finish
- Anisotropic material properties
- Qualification and certification requirements in regulated industries
- Limited number of qualified Inconel alloy grades for 3D printing
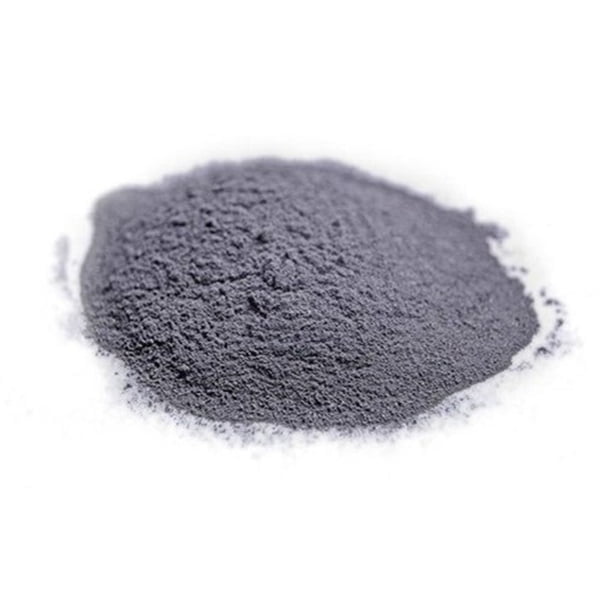
Types of Inconel Alloys Used in 3D Printing
Several Inconel superalloys grades have been developed for use in 3D printing processes. The most common Inconel alloys used are:
Inconel Alloy | Key Features |
---|---|
Inconel 718 | Excellent strength and corrosion resistance up to 700°C. Most popular for aerospace components. |
Inconel 625 | Outstanding corrosion resistance, good weldability and strength to 980°C. Used for chemical processing, marine applications. |
Inconel 825 | Good oxidation and corrosion resistance. Used for oil and gas components, power plants. |
Inconel 939 | High strength nickel alloy stable up to 1095°C . Used for gas turbine engine parts. |
Other Inconel alloys with potential for 3D printing:
- Inconel X-750
- Inconel 909
- Inconel 939ER
3D Printing Processes for Inconel
Several additive manufacturing processes are used for printing Inconel superalloys:
Process | How it Works | Benefits | Limitations |
---|---|---|---|
Powder Bed Fusion – Laser | Laser selectively melts powder layers | Good accuracy, surface finish | Relatively slow |
Powder Bed Fusion – Electron Beam | Electron beam melts powder layers | Faster build speeds than laser | Requirement of vacuum chamber |
Directed Energy Deposition (DED) | Focused thermal energy source melts metal powder or wire feedstock during deposition | Can repair and coat parts by adding material | Rougher surface finish, post processing required |
Binder Jetting | Liquid bonding agent selectively joins powder particles | Relatively fast, low cost | Lower density and strength, infiltration required |
Key process parameters: Laser power, scan speed, hatch spacing, layer thickness, build orientation, support structures, preheating temperature, and post-processing steps. Process parameters need to be optimized for each Inconel alloy to obtain desired properties.
Applications of Inconel 3D Printing
Key industries using additively manufactured Inconel parts and their applications:
Industry | Typical Applications |
---|---|
Aerospace | Turbine blades, impellers, combustor liners, valves, housings, brackets |
Oil and Gas | Downhole tools, valves, wellhead components, pipe fittings |
Power Generation | Heat exchangers, turbine blades, casings, fasteners |
Automotive | Turbocharger housings, engine valves, exhaust components |
Chemical Processing | Process vessel internals, heat exchanger parts, valves, pumps |
Medical | Dental implants, prosthetics, surgical instruments |
Unique capabilities of 3D printing make it suitable for fabricating complex Inconel parts with optimized shapes and designs. Lightweighting of components can be achieved.
Specifications for Inconel 3D Printed Parts
Important parameters and specifications to consider for Inconel 3D printed parts:
Parameter | Typical Range/Values |
---|---|
Dimensional Accuracy | ± 0.1-0.2% or ± 50 μm |
Surface Roughness (Ra) | As-printed: 8-15 μm <br> Post-processed: 1-4 μm |
Porosity | 0.5-2% for laser PBF <br> 5-10% for binder jetting before infiltration |
Wall Thickness | 0.3-0.5 mm minimum |
Mechanical Properties | Strength within 15% of wrought material <br> Elongation 10-35% |
Operating Temperatures | Up to 700°C for Inconel 718 <br> Over 1000°C for Inconel 939 |
Critical design principles for Inconel 3D printing:
- Minimum wall thickness for self-supporting features
- Angled surfaces greater than 45 degrees may require supports
- Generous fillet radii recommended for complex geometries
Post-Processing Methods for Inconel Printed Parts
Common post-processing steps for as-printed Inconel parts:
- Removal from build plate: Cutting, wire EDM
- Support removal: Mechanical removal, thermal stress relieving, chemical dissolution
- Stress relieving: Heat treatment below solutionizing temperature to remove residual stresses
- Surface finishing: Machining, grinding, polishing, abrasive flow machining, vibratory finishing
- Hot isostatic pressing (HIP): Applies heat and isostatic pressure to close internal voids and improve material properties
Post-processing is critical for improving final part quality and performance. The methods used depend on application requirements.
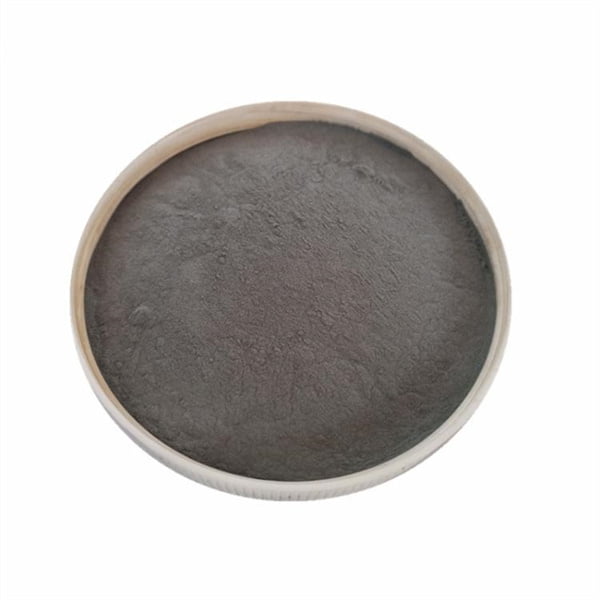
Design Principles and Recommendations
Key design recommendations for optimizing Inconel 3D printed parts:
- Minimize overhanging features requiring supports
- Orient parts to reduce support structures
- Avoid thin protruding features prone to deformation
- Use generous internal radii to relieve stresses
- Allow for thermal expansion in designs – Inconel has coefficient of thermal expansion of 13 x 10<sup>-6</sup> m/m°C
- Account for anisotropic material properties based on build orientation
- Design appropriate datums, tolerances, surface finishes for post-processing
- Simulate builds and thermal stresses using CAE tools before printing
Performing topology optimization and redesigning parts specifically for 3D printing leads to maximum benefits in terms of weight savings, performance improvements and cost reduction.
Suppliers for Inconel 3D Printing Services
Many service bureaus offer Inconel 3D printing services using a variety of processes:
Company | Processes | Inconel Grades | Industries Served |
---|---|---|---|
Materialise | Laser PBF, Binder Jetting | 718, 625, 800 | Aerospace, automotive, general industry |
3D Systems | Laser PBF, DED | 718, 625, 939 | Oil and gas, aerospace, automotive |
GE Additive | Laser PBF, Binder Jetting | 718, 625, 800H, 939 | Aerospace, oil and gas, power generation |
Voestalpine | Laser PBF, DED | 718, 625, 800H | Aerospace, oil and gas, automotive |
Hoganas | Binder Jetting | 718, 625 | Aerospace, automotive, general industry |
Many printer OEMs also offer Inconel printing services including EOS, Velo3D, SLM Solutions, Renishaw, and AddUp. Both laser PBF and DED processes are commonly available.
Cost Analysis for Inconel 3D Printing
Process | Build Rate | Part Size | Lead Time | Cost per Part |
---|---|---|---|---|
Laser PBF | 5-15 cm3/hr | 50 cm3 | 1-2 weeks | $250-$1000 |
DED | 25-100 cm3/hr | 500 cm3 | 1 week | $100-$500 |
Binder Jetting | 20-50 cm3/hr | 1000 cm3 | 1 week | $50-$200 |
Costs vary based on:
- Part size, geometry complexity, production volumes
- Material costs – Inconel powder is expensive
- Labor for design, post-processing steps
- Qualification and certification requirements
For prototyping and small production volumes, 3D printing Inconel is very cost effective compared to machining or casting. DED is the most economical process.
How to Select a Vendor for Inconel 3D Printing
Key considerations when selecting a vendor for Inconel 3D printing services:
- Experience: Number of years working with Inconel alloys, industries served, case studies
- Technical capabilities: Processes offered, Inconel grades printed, part size limits, secondary operations
- Quality certifications: ISO 9001, AS9100, Nadcap approvals demonstrate quality management
- Part validation: Material testing, process validation, quality checks performed
- Post-processing: Stress relieving, Hot Isostatic Pressing, machining, finishing services
- Lead times: Ability to deliver parts quickly is essential
- Client support: Design for AM guidance, topology optimization, print monitoring, part inspections
- Cost: Printing and material costs, labor rates, volume discounts, certifications
Contact multiple vendors, compare capabilities, request test coupons to qualify suppliers before starting full-scale production with Inconel 3D printing.
Pros vs Cons of Inconel 3D Printing
Advantages | Disadvantages |
---|---|
Complex geometries not possible with other processes | Relatively high material costs for Inconel powder |
Lightweighting and optimization of designs | Lower dimensional accuracy and higher surface roughness than machining |
Parts consolidation and reduced assemblies | Limited number of qualified Inconel grades |
Reduced lead times and costs for low volume production | Post-processing often required to achieve desired material properties |
Minimal material waste | Anisotropic material properties |
On-demand manufacturing, no minimum order quantities | Qualification and certification requirements in regulated industries |
Easy to modify and iterate designs | Thermal stresses may cause part distortions |
The Role of Inconel 3D Printing in Manufacturing
Key roles that Inconel 3D printing is fulfilling in manufacturing:
- Prototype Production: Quick and low-cost prototyping of Inconel components for design verification
- Bridge Tooling: Producing molds, fixtures, jigs quickly during the transition from prototyping to full-scale manufacturing
- Part Consolidation: Redesigning assemblies and consolidating parts for reduced weight and cost
- Mass Customization: Facilitating personalized Inconel parts tailored to customer requirements
- Spare Parts: On-demand manufacturing of replacement parts as needed rather than batch production and stocking
- Supply Chain Flexibility: Allows shifting production across locations easily and mitigates supply chain disruptions
- Short Runs: Economical production of small Inconel part batches needed in low volumes
The unique capabilities of additive manufacturing make it a valuable complement to conventional manufacturing processes for fabricating complex Inconel components.
The Future of Inconel 3D Printing
Inconel 3D printing is expected to grow significantly in the coming years driven by:
- Development of new Inconel superalloys optimized for AM processes
- Improved printers with higher levels of automation and repeatability
- Faster build speeds and higher production throughput
- Expanded part size capabilities
- Hybrid manufacturing combining AM and subtractive processes
- Software enhancements enabling optimization of support structures
- Increased adoption in highly regulated sectors like aerospace and medical
- Applications in emerging areas like tooling, molds, jigs and fixtures
- Use of AM for part repairs and aftermarket services
As the technology matures further, Inconel 3D printing will become mainstream in more industries due to its ability to produce high-performance metal parts on-demand.
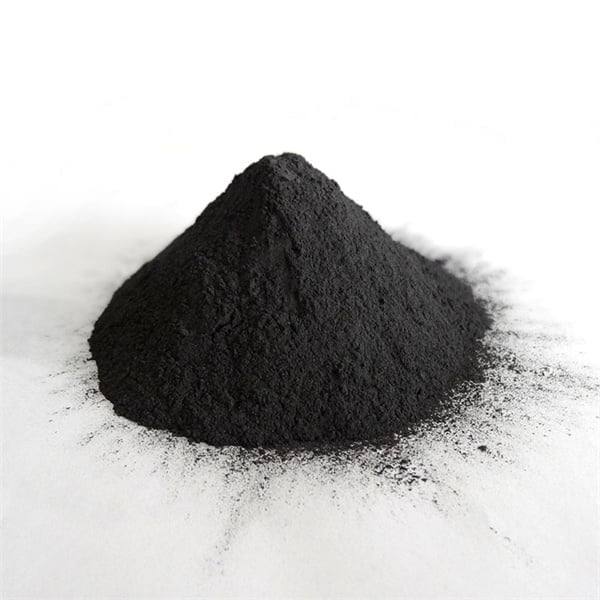
FAQ
Q: What are the different types of Inconel alloys used in 3D printing?
A: The most common Inconel alloys used in 3D printing are Inconel 718, 625, 800 and 939. Each has specific temperature, corrosion and oxidation resistance properties suitable for different applications.
Q: How do the mechanical properties of 3D printed Inconel compare to wrought Inconel parts?
A: When optimized process parameters are used, 3D printed Inconel components exhibit tensile strength within 15% of wrought material. However, ductility in terms of elongation at break is lower for AM Inconel parts, in the range of 10-35% versus 40-50% for wrought.
Q: What post-processing methods are used on Inconel 3D printed parts?
A: Common post-processing steps include support removal, stress relieving heat treatment, Hot Isostatic Pressing (HIP), machining, grinding, polishing and other finishing processes. This helps improve surface finish, dimensional accuracy and material properties.
Q: Does Inconel 3D printing require any special equipment or infrastructure?
A: Printing Inconel alloys requires specialized powder bed fusion or directed energy deposition printers equipped with inert gas chambers, high powered lasers or electron beams, and vacuum systems. Handling fine Inconel powder also needs special precautions and procedures.
Q: What are some examples of industries using Inconel 3D printing?
A: Key industries using Inconel 3D printing include aerospace, oil and gas, power generation, chemical processing, automotive, and medical. Parts like turbine blades, heat exchanger components, valves, and prosthetics are commonly 3D printed in Inconel.
Q: Is it feasible to 3D print large Inconel parts?
A: While size capabilities are expanding, most Inconel 3D printed parts are currently less than 1 cubic foot in volume. For very large parts, directed energy deposition (DED) offers greater build size flexibility than powder bed fusion processes. Hybrid manufacturing combining AM and subtractive processes also enables larger Inconel parts.
Q: Does Inconel 3D printing require any special design considerations?
A: Key design principles include minimizing overhangs, allowing for thermal stresses, using appropriate tolerances and surface finishes, and orienting parts optimally to reduce supports. Topology optimization and redesigning for AM leads to maximum benefits.
Q: What are the main benefits of Inconel 3D printing?
A: The key benefits of Inconel 3D printing are the ability to produce complex geometries not possible with casting or forging, reduced lead times and costs for low volume production, optimized lightweight designs, part consolidation, and on-demand manufacturing capability.
Q: How does the cost of Inconel 3D printing compare to other metal AM processes?
A: Inconel powders are more expensive than other metals like stainless steel and titanium. Combined with challenging print parameters, this makes Inconel 3D printing costlier on a per part basis compared to printing steels or titanium alloys.
Share On
MET3DP Technology Co., LTD is a leading provider of additive manufacturing solutions headquartered in Qingdao, China. Our company specializes in 3D printing equipment and high-performance metal powders for industrial applications.
Inquiry to get best price and customized Solution for your business!
Related Articles
About Met3DP
Recent Update
Our Product
CONTACT US
Any questions? Send us message now! We’ll serve your request with a whole team after receiving your message.
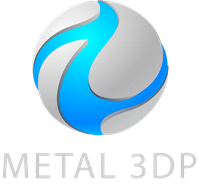
Metal Powders for 3D Printing and Additive Manufacturing