Inert Gas Atomisation
Table of Contents
In the ever-evolving world of metallurgy and material science, the production of high-quality metal powders is crucial for various advanced manufacturing processes. One method that stands out for its precision and efficiency is Inert Gas Atomisation (IGA). This technique is widely used to produce fine, spherical metal powders with uniform particle sizes, essential for applications in additive manufacturing, powder metallurgy, and other high-tech industries.
In this article, we’ll dive deep into the world of Inert Gas Atomisation, exploring its process, benefits, applications, and more. We’ll also look at specific metal powder models, their properties, and applications, all presented in a detailed and structured format to ensure a comprehensive understanding.
Overview of Inert Gas Atomisation
Inert Gas Atomisation (IGA) is a process used to create fine metal powders. The process involves melting a metal or alloy and then disintegrating the molten stream into tiny droplets by impinging it with a high-velocity jet of inert gas, such as argon or nitrogen. These droplets solidify into spherical particles, forming a powder with excellent flow properties and uniform particle size distribution.
Key Details:
- Process: Melting and disintegration of metal into powder
- Gas Used: Inert gases (Argon, Nitrogen)
- Output: Spherical metal powders
- Applications: Additive manufacturing, powder metallurgy, thermal spraying
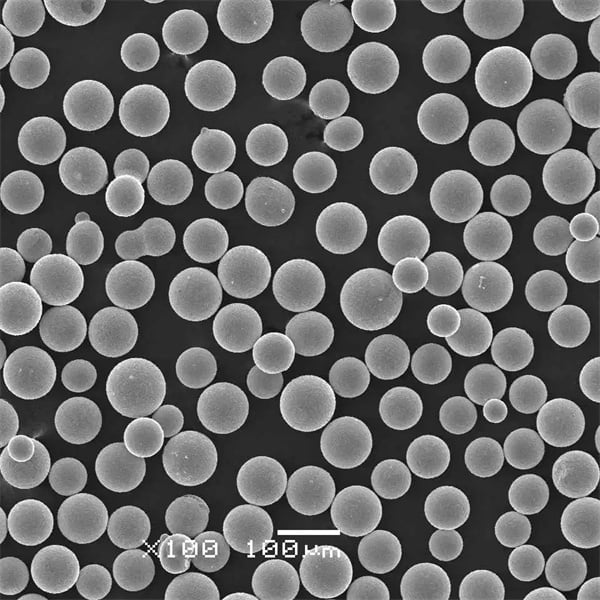
Metal Powder Models Produced by Inert Gas Atomisation
Below is a list of specific metal powder models produced through Inert Gas Atomisation, highlighting their unique properties and applications.
Metal Powder Model | Composition | Properties | Applications |
---|---|---|---|
316L Stainless Steel | Fe-Cr-Ni-Mo | Corrosion resistance, high strength | Medical implants, aerospace components |
Ti-6Al-4V | Ti-Al-V | High strength-to-weight ratio, biocompatibility | Medical implants, aerospace parts |
Inconel 718 | Ni-Cr-Fe | High temperature resistance, oxidation resistance | Gas turbines, aerospace components |
AlSi10Mg | Al-Si-Mg | Lightweight, good thermal properties | Automotive parts, aerospace components |
CoCrMo | Co-Cr-Mo | High wear resistance, biocompatibility | Medical implants, dental prosthetics |
CuSn10 | Cu-Sn | High wear resistance, good conductivity | Bearings, bushings, electrical connectors |
316 Stainless Steel | Fe-Cr-Ni | Corrosion resistance, good mechanical properties | Chemical processing, marine applications |
Hastelloy X | Ni-Cr-Fe-Mo | Excellent high-temperature strength, oxidation resistance | Industrial gas turbines, petrochemical processing |
Maraging Steel | Fe-Ni-Co-Mo-Ti | High strength, toughness | Tooling, aerospace components |
NiCrMo | Ni-Cr-Mo | Excellent corrosion resistance, high strength | Marine applications, chemical processing |
Process of Inert Gas Atomisation
The process of Inert Gas Atomisation involves several critical steps to ensure the production of high-quality metal powders.
- Melting: The metal or alloy is melted in a crucible using induction heating or another suitable method.
- Disintegration: The molten metal stream is disintegrated into fine droplets by a high-velocity jet of inert gas.
- Solidification: The droplets solidify rapidly into spherical particles as they cool down.
- Collection: The solidified metal powder is collected and processed for further use.
Advantages of Inert Gas Atomisation
Inert Gas Atomisation offers several benefits that make it a preferred method for producing metal powders.
- Uniform Particle Size: The process produces powders with a consistent particle size distribution.
- High Purity: Using inert gases prevents oxidation and contamination of the metal.
- Spherical Particles: The resulting powders have a spherical shape, enhancing their flow properties.
- Versatility: Can be used with a wide range of metals and alloys.
Disadvantages of Inert Gas Atomisation
Despite its advantages, Inert Gas Atomisation also has some limitations.
- Cost: The equipment and gases used can be expensive.
- Complexity: The process requires precise control and expertise.
- Energy Consumption: High energy is required to melt the metals and maintain the gas flow.
Applications of Inert Gas Atomisation
Inert Gas Atomisation is used in various industries due to its ability to produce high-quality metal powders.
Application | Details |
---|---|
Additive Manufacturing | Produces powders for 3D printing with excellent flowability and uniformity. |
Powder Metallurgy | Used to create parts with high density and strength. |
Thermal Spraying | Produces coatings with high wear and corrosion resistance. |
Metal Injection Molding (MIM) | Creates fine powders for intricate and high-performance parts. |
Biomedical Implants | Produces biocompatible powders for medical devices and implants. |
Specifications, Sizes, Grades, and Standards
The specifications and standards for metal powders produced by Inert Gas Atomisation vary based on the application and industry requirements.
Powder | Size Range (µm) | Grade | Standard |
---|---|---|---|
316L Stainless Steel | 15-45 | ASTM F138 | ISO 5832-1 |
Ti-6Al-4V | 20-50 | ASTM B348 | ISO 5832-3 |
Inconel 718 | 10-63 | AMS 5662 | ASTM B637 |
AlSi10Mg | 20-60 | EN 1706 | ISO 3522 |
CoCrMo | 15-45 | ASTM F75 | ISO 5832-4 |
CuSn10 | 20-50 | EN 1982 | ISO 1338 |
316 Stainless Steel | 10-45 | ASTM A276 | ISO 4957 |
Hastelloy X | 15-50 | AMS 5754 | ASTM B572 |
Maraging Steel | 20-63 | AMS 6514 | ASTM A579 |
NiCrMo | 10-50 | UNS N10276 | ASTM B575 |
Suppliers and Pricing Details
Several suppliers offer metal powders produced through Inert Gas Atomisation. Pricing varies based on the metal, powder grade, and quantity.
Supplier | Metal Powder | Price (per kg) | Notes |
---|---|---|---|
Carpenter Technology | 316L Stainless Steel | $50 | Bulk discounts available |
Arcam AB | Ti-6Al-4V | $100 | High-quality medical grade |
Höganäs AB | Inconel 718 | $200 | Available in various particle sizes |
Sandvik Osprey | AlSi10Mg | $70 | Customized size distribution |
LPW Technology | CoCrMo | $150 | Premium biocompatible grade |
GKN Hoeganaes | CuSn10 | $40 | High conductivity applications |
AP&C | 316 Stainless Steel | $55 | Consistent quality |
ATI Powder Metals | Hastelloy X | $250 | Industrial applications |
Eramet | Maraging Steel | $180 | Aerospace and tooling |
Kennametal | NiCrMo | $220 | Chemical processing applications |
Comparing Pros and Cons of Inert Gas Atomisation
Pros | Cons |
---|---|
Uniform particle size distribution | High equipment and gas costs |
High purity powders | Complex process control |
Spherical particles enhance flow | High energy consumption |
Suitable for various metals and alloys | Requires expertise and precise control |
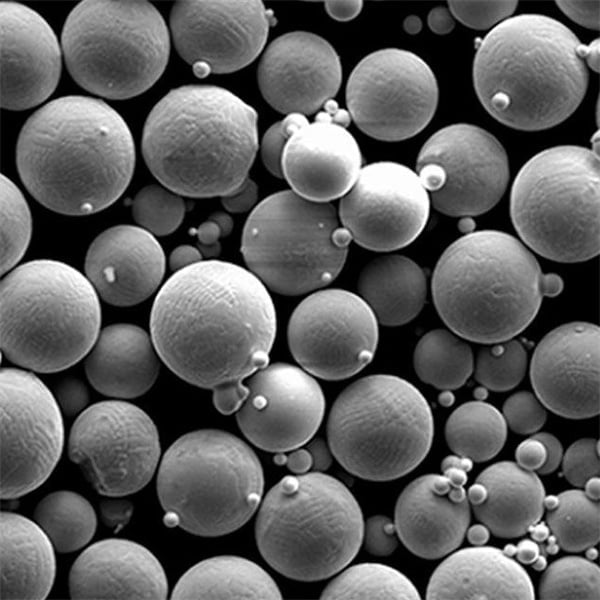
FAQs
Question | Answer |
---|---|
What is Inert Gas Atomisation? | A process to produce fine metal powders by disintegrating molten metal with inert gas jets. |
Which metals can be processed? | Stainless steel, titanium alloys, nickel-based superalloys, aluminum alloys, cobalt-chromium alloys, and more. |
Why use inert gases? | Inert gases prevent oxidation and contamination of the metal during the process. |
What are the main applications? | Additive manufacturing, powder metallurgy, thermal spraying, metal injection molding, biomedical implants. |
What are the advantages? | Uniform particle size, high purity, spherical particles, versatility. |
What are the disadvantages? | High cost, complexity, energy consumption. |
How are the powders collected? | The solidified particles are collected in a chamber and processed for further use. |
What sizes are available? | Particle sizes typically range from 10 µm to 63 µm, depending on the application. |
Who are the leading suppliers? | Carpenter Technology, Arcam AB, Höganäs AB, Sandvik Osprey, LPW Technology, GKN Hoeganaes, AP&C, ATI Powder Metals, Eramet, Kennametal. |
Share On
MET3DP Technology Co., LTD is a leading provider of additive manufacturing solutions headquartered in Qingdao, China. Our company specializes in 3D printing equipment and high-performance metal powders for industrial applications.
Inquiry to get best price and customized Solution for your business!
Related Articles
About Met3DP
Recent Update
Our Product
CONTACT US
Any questions? Send us message now! We’ll serve your request with a whole team after receiving your message.
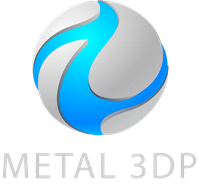
Metal Powders for 3D Printing and Additive Manufacturing