Metal Alloy Powders
Table of Contents
Metal alloy powders enable manufacturing of high performance parts using powder metallurgy pressing and sintering or additive manufacturing methods across transportation, industrial, medical and energy industries. This guide covers various alloy options, powder production processes, key specifications, use cases, quality considerations and sourcing advisory.
Types of metal alloy powders
Common categories:
Type | Examples | Key Properties |
---|---|---|
Nickel Alloys | Inconel, Monel, Hastelloy | Corrosion resistance, heat resistance |
Cobalt Alloys | MP35N, Haynes 25, Stellite | Wear resistance, biocompatibility |
Titanium Alloys | CP Grade, Ti-6Al-4V, Ti-6Al-7Nb | High strength, low weight |
Stainless Steels | 316, 17-4PH, 15-5PH | Corrosion resistance, strength |
Tool Steels | H13, M2, M4, P20 | Wear resistance, toughness |
Copper Alloys | Chrome copper, Brass, Bronze | Electrical & thermal conductivity |
Match alloy material properties to critical part performance requirements like heat tolerance, hardness, fatigue life etc driving powder grade selection.
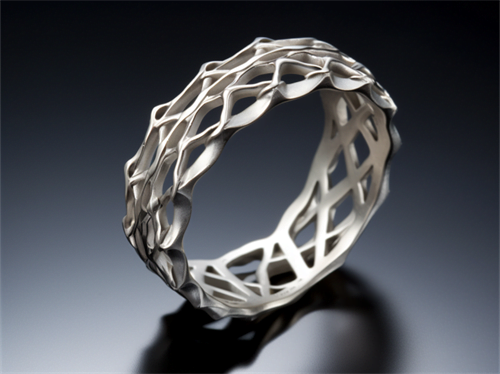
Metal Powder Production Methods
Key commercial scale manufacturing processes:
- Gas Atomization – High pressure inert gas breaks up molten metal stream into fine droplets. Achieves spherical powders with good flow and packing properties. Different nozzles generate desired size ranges.
- Plasma Atomization – High energy plasma arc melts feedstock. Powerful induction coils generate droplets that solidify into spherical powders with tight particle distributions.
- Rotating Electrode – Centrifugal forces acting on spinning molten alloy subjected to inert gas jets causes disintegration into fine droplets resulting in spherical powders.
- Electrolysis – Metal ions from solution plate out on cathodes as fine powder particles. Used for reactive materials like aluminum, magnesium, titanium.
Controlling process parameters like temperature, atmosphere and cooling rates result in quality powder feedstock for part fabrication using additive manufacturing or powder metallurgy compaction.
Typical Specifications
Parameter | Description | Test Method |
---|---|---|
Purity | >99%, minimize impurities | ICP analysis |
Particle shape | Spherical >80% | Microscopy |
Particle Size Distribution | Tight ranges as required | Laser diffraction |
Tap density | Material dependent | Hall flowmeter |
Apparent density | Material dependent | Pycnometry |
Flow rates | Standardized for each nominal size | Hall flowmeter |
Surface oxides | <3000 ppm; oxide thickness | Inert gas fusion; XRD |
Review statistical batch data from manufacturer against these metrics specific to your target grade confirming quality and consistency relative to standards.
Applications
Metal alloy powder applications span:
Aerospace – Engine components like blades, nozzles; airframe fittings, landing gear parts; on-board systems
Industrial – Natural gas/petroleum pumps, valves, drill bits; tooling inserts; nuclear reactors; heat exchangers
Automotive – Engine components, turbocharger rotors, gears; chassis, drivetrain parts
Medical – Implants for knees, hips, dental; surgical tools; imaging instruments
Consumer – High end watches, sports equipment like bicycles, golf clubs etc requiring strength, aesthetics
Energy – Solar cell contacts, electrodes; generators; battery components; wind turbines
Taking advantage oftailorable materials properties with design freedom and precision.
Industrial Standards
Key specifications applicable to metal alloy powders:
Standard | Description |
---|---|
ASTM B213 | Standard classification system for metal powders |
ISO 4490 | Chemical analysis, sampling procedures |
ASTM B822 | Apparent density and flow rate measurement |
MPIF 04 | Statistical methods for metal powder analysis |
Review statistically validated certifications showing conformance to grade composition limits and production quality consistency relative to applicable standards.
Common Metal Powder Grades
Alloy | Trade Names | Specifications | |
---|---|---|---|
Nickel Alloys | Inconel 718, 625; Hastelloy X; Monel K500 | AMS 5662, 5663 etc. | |
Cobalt Alloys | MP35N, Haynes 25, Stellite 21 | ASTM F90, F1537 etc. | |
Titanium Alloys | Ti-6Al-4V Grade 5; Ti-6Al-7Nb ; CP Ti Grade 2 | AMS 4911, ASTM B348 etc. | |
Stainless Steels | SS 316L; 17-4PH; 15-5 PH; | ASTM A240, B945 etc. | |
Tool Steels | H13; M2; M4; P20+Ni | AISI types | ASTM A681 |
Copper Alloys | C18150, C19500, C95810 | UNS No., ASTM B194 etc. |
Match target grade to applicable alloy specifications that align with finished part functionality needs across strength, conductivity, corrosion resistance parameters.
Quality Considerations
Metric | Purpose | Test Method |
---|---|---|
Composition | Verify grade purity | ICP analysis |
Particle size distribution | AM compatibility, sintering response | Laser diffraction |
Hall flow rate | Powder packing density, layer uniformity | Hall flowmeter |
Tap density | Indicates final part density | Weigh measured volume |
Apparent density | Powder system density | Gas pycnometry |
Particle shape | Sphericity optimizes properties | Microscopy |
Surface oxides | Impacts powder reuse | Inert gas fusion analyzer |
Consistent quality across these metrics is directly correlated with consistent final part performance meeting specifications.
Sourcing Considerations
Parameter | Importance |
---|---|
Batch Data Sheets | High |
Sampling Support | High |
Lead Time | Medium |
Customization | Low |
Price Factors | Low |
Try powder samples first before large purchases to qualify printing or compression responses relative to application needs.
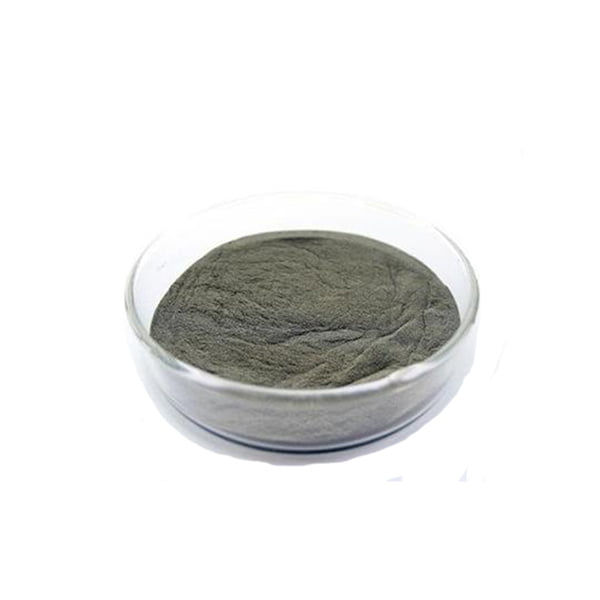
FAQs
Q: What is the difference between pre-alloyed and blended elemental powders?
A: Pre-alloyed powders have uniform composition throughout each spherical particle. Blended elemental mixes may have slight composition differences between particles that can create inhomogeneities in final parts.
Q: Should metal powders be stored under special conditions?
A: Store sealed with dessicant away from moisture and oxygen which causes deterioration. Limit temperature variation to 10-30°C. Discard if severe discoloration, caking or significant loss of flow. Shelf life is typically over a year if properly stored.
Q: What are common metal powder blend mixes?
A: Cobalt-chrome, stainless steel-17-4PH, and nickel alloy-stainless steel powder blends offer ways to tailor final part material properties like strength, wear resistance or corrosion resistance at lower costs than high purity grades.
Q: What precautions are needed when handling metal powders?
A: Use appropriate PPE and avoid skin contact or inhalation during powder handling. Passivated powders pose fewer health hazards compared to atomized powders which can be more reactive. Review SDS sheets on flammability, reactivity and exposure protocols.
Share On
MET3DP Technology Co., LTD is a leading provider of additive manufacturing solutions headquartered in Qingdao, China. Our company specializes in 3D printing equipment and high-performance metal powders for industrial applications.
Inquiry to get best price and customized Solution for your business!
Related Articles
About Met3DP
Recent Update
Our Product
CONTACT US
Any questions? Send us message now! We’ll serve your request with a whole team after receiving your message.
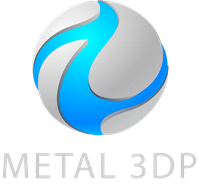
Metal Powders for 3D Printing and Additive Manufacturing