Laser-Based Powder Bed Fusion
Table of Contents
Laser-Based Powder Bed Fusion (PBF) is revolutionizing the manufacturing industry, offering unprecedented precision, efficiency, and flexibility. But what exactly is it, and why should you care? Let’s dive deep into this innovative technology, exploring its intricacies, applications, and why it’s becoming a game-changer in the world of production.
Overview of Laser-Based Powder Bed Fusion
Laser-Based Powder Bed Fusion is an additive manufacturing process that uses a high-powered laser to fuse metal powder particles layer by layer to create a solid, three-dimensional object. It’s a technique that falls under the umbrella of 3D printing but is specifically tailored for producing high-quality metal components.
Key Features of Laser-Based Powder Bed Fusion:
- Precision: Achieves intricate details and complex geometries with high accuracy.
- Material Efficiency: Minimizes waste by using only the necessary amount of powder.
- Customization: Allows for the creation of bespoke parts tailored to specific needs.
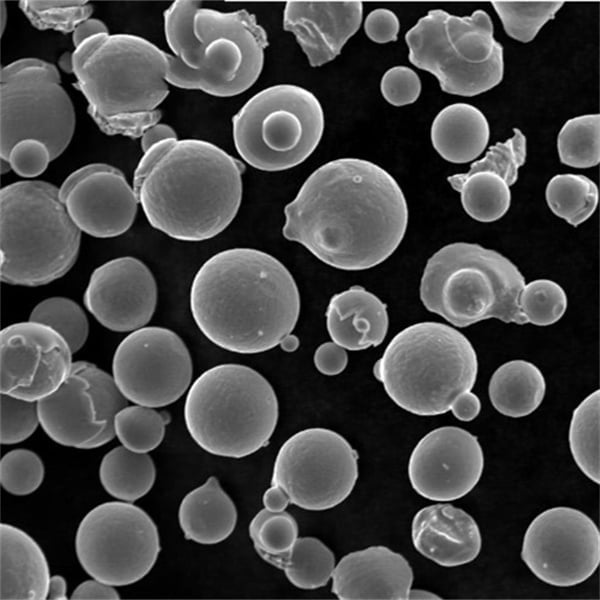
Types of Metal Powders for Laser-Based Powder Bed Fusion
Choosing the right metal powder is crucial for the success of the PBF process. Here’s a rundown of some popular metal powders used in PBF, along with their descriptions:
Metal Powder | Description |
---|---|
Titanium Ti-6Al-4V | Known for its high strength-to-weight ratio, excellent corrosion resistance, and biocompatibility, making it ideal for aerospace, medical implants, and automotive industries. |
Aluminum AlSi10Mg | Combines lightweight properties with good mechanical strength and thermal conductivity, perfect for automotive and aerospace components. |
Stainless Steel 316L | Offers excellent corrosion resistance, strength, and ductility, widely used in medical, marine, and chemical processing applications. |
Inconel 718 | A nickel-chromium superalloy with high-temperature resistance and good tensile strength, used in aerospace, gas turbines, and nuclear reactors. |
Cobalt-Chrome | High wear resistance, biocompatibility, and strength, commonly used for dental and orthopedic implants, as well as in aerospace applications. |
Maraging Steel (1.2709) | Known for its excellent strength and toughness after heat treatment, used in tooling, aerospace, and high-stress components. |
Copper (Cu) | Exceptional thermal and electrical conductivity, suitable for electrical components and heat exchangers. |
Nickel Alloy (625) | Offers excellent corrosion and oxidation resistance, high strength, used in marine, chemical, and aerospace industries. |
Tool Steel (H13) | Known for its hardness, strength, and resistance to abrasion, often used in mold making, die casting, and tooling applications. |
Titanium (Ti-5Al-2.5Sn) | Good high-temperature performance and creep resistance, utilized in aerospace and high-performance automotive applications. |
Properties and Characteristics of Metal Powders
Metal Powder | Composition | Properties | Applications |
---|---|---|---|
Titanium Ti-6Al-4V | Ti, Al, V | High strength-to-weight ratio, corrosion resistance, biocompatibility | Aerospace, medical implants, automotive |
Aluminum AlSi10Mg | Al, Si, Mg | Lightweight, good mechanical strength, thermal conductivity | Automotive, aerospace |
Stainless Steel 316L | Fe, Cr, Ni, Mo | Corrosion resistance, strength, ductility | Medical, marine, chemical processing |
Inconel 718 | Ni, Cr, Fe, Nb, Mo, Ti | High-temperature resistance, tensile strength | Aerospace, gas turbines, nuclear reactors |
Cobalt-Chrome | Co, Cr, Mo | Wear resistance, biocompatibility, strength | Dental, orthopedic implants, aerospace |
Maraging Steel (1.2709) | Fe, Ni, Co, Mo | Strength, toughness after heat treatment | Tooling, aerospace, high-stress components |
Copper (Cu) | Cu | Thermal and electrical conductivity | Electrical components, heat exchangers |
Nickel Alloy (625) | Ni, Cr, Mo, Nb | Corrosion and oxidation resistance, high strength | Marine, chemical, aerospace |
Tool Steel (H13) | Fe, Cr, Mo, Si, V | Hardness, strength, abrasion resistance | Mold making, die casting, tooling |
Titanium (Ti-5Al-2.5Sn) | Ti, Al, Sn | High-temperature performance, creep resistance | Aerospace, high-performance automotive |
Applications of Laser-Based Powder Bed Fusion
Laser-Based PBF is making waves across various industries, thanks to its versatility and precision. Here’s a look at where it’s being applied and why it’s so effective:
Industry | Applications |
---|---|
Aerospace | Engine components, structural parts, lightweight brackets |
Medical | Custom implants, prosthetics, surgical instruments |
Automotive | Lightweight components, custom parts, performance enhancements |
Tooling | Injection molds, die-casting molds, custom tooling |
Jewelry | Custom designs, intricate patterns, rapid prototyping |
Energy | Turbine blades, heat exchangers, fuel nozzles |
Electronics | Heat sinks, electrical components, custom enclosures |
Dental | Crowns, bridges, dental implants |
Marine | Corrosion-resistant parts, lightweight components |
Architecture | Custom fixtures, design prototypes |
Advantages of Laser-Based Powder Bed Fusion
Why is Laser-Based Powder Bed Fusion gaining so much attention? Here are some compelling reasons:
- Precision and Detail: Capable of producing intricate and complex geometries that are challenging for traditional manufacturing methods.
- Material Efficiency: Minimizes waste by using only the required amount of metal powder.
- Customization: Easily create bespoke parts tailored to specific requirements.
- Speed and Efficiency: Faster production times compared to conventional methods.
- Strength and Durability: Produces parts with excellent mechanical properties.
Disadvantages of Laser-Based Powder Bed Fusion
Despite its many benefits, Laser-Based PBF also has some limitations:
- Cost: High initial investment in equipment and materials.
- Complexity: Requires specialized knowledge and skills to operate effectively.
- Size Limitations: Typically restricted to smaller parts due to build chamber size.
- Surface Finish: May require post-processing to achieve desired surface quality.
Specifications, Sizes, Grades, and Standards
Metal Powder | Specifications | Sizes | Grades | Standards |
---|---|---|---|---|
Titanium Ti-6Al-4V | ASTM B348, ASTM F1472 | 15-45 µm, 45-106 µm | Grade 5 | ISO 5832-3, AMS 4928 |
Aluminum AlSi10Mg | EN AC-43400 | 20-63 µm, 45-90 µm | ||
Stainless Steel 316L | ASTM A276, ASTM F138 | 15-45 µm, 45-106 µm | ISO 5832-1 | |
Inconel 718 | AMS 5662, ASTM B637 | 15-45 µm, 45-106 µm | ||
Cobalt-Chrome | ASTM F75, ASTM F1537 | 15-45 µm, 45-106 µm | ||
Maraging Steel (1.2709) | DIN 1.2709, AMS 6514 | 15-45 µm, 45-106 µm | ||
Copper (Cu) | ASTM B170 | 20-63 µm, 45-90 µm | ||
Nickel Alloy (625) | AMS 5666, ASTM B443 | 15-45 µm, 45-106 µm | ||
Tool Steel (H13) | ASTM A681 | 15-45 µm, 45-106 µm | ||
Titanium (Ti-5Al-2.5Sn) | ASTM B348 | 15-45 µm, 45-106 µm |
Suppliers and Pricing Details
Supplier | Metal Powders Available | Pricing (per kg) | Location |
---|---|---|---|
Carpenter Technology | Titanium, Aluminum, Stainless Steel, Inconel, Cobalt-Chrome | $200 – $600 | USA |
Sandvik | Titanium, Aluminum, Stainless Steel, Inconel, Cobalt-Chrome | $250 – $700 | Sweden |
GKN Additive | Titanium, Aluminum, Stainless Steel, Inconel, Cobalt-Chrome | $220 – $650 | Germany |
LPW Technology | Titanium, Aluminum, Stainless Steel, Inconel, Cobalt-Chrome | $230 – $680 | UK |
Höganäs | Titanium, Aluminum, Stainless Steel, Inconel, Cobalt-Chrome | $240 – $690 | Sweden |
AP&C | Titanium, Aluminum, Stainless Steel, Inconel, Cobalt-Chrome | $210 – $620 | Canada |
Aubert & Duval | Titanium, Aluminum, Stainless Steel, Inconel, Cobalt-Chrome | $220 – $640 | France |
Praxair Surface Technologies | Titanium, Aluminum, Stainless Steel, Inconel, Cobalt-Chrome | $230 – $660 | USA |
Advanced Powders & Coatings (AP&C) | Titanium, Aluminum, Stainless Steel, Inconel, Cobalt-Chrome | $220 – $650 | Canada |
Renishaw | Titanium, Aluminum, Stainless Steel, Inconel, Cobalt-Chrome | $230 – $670 | UK |
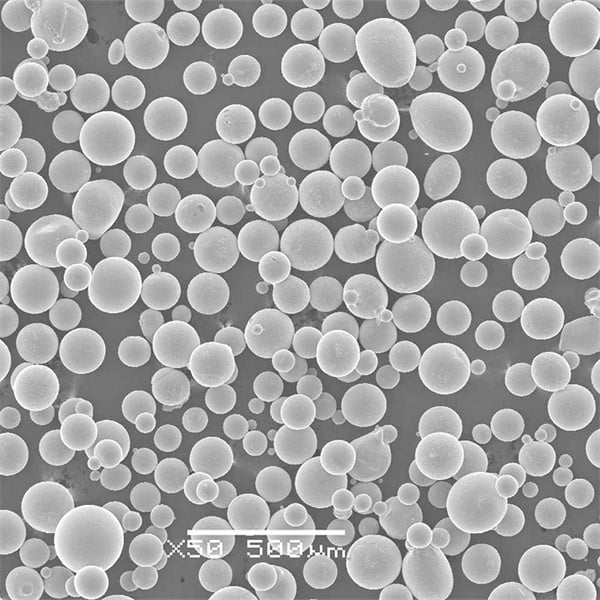
Comparing Pros and Cons of Laser-Based Powder Bed Fusion
Aspect | Advantages | Limitations |
---|---|---|
Precision and Detail | High accuracy and ability to produce complex geometries | May require post-processing for surface finish |
Material Efficiency | Minimal waste, only necessary amount of powder used | High cost of metal powders |
Customization | Easily create bespoke parts tailored to specific needs | Complexity in design and operation |
Speed and Efficiency | Faster production times compared to traditional methods | Initial setup time and calibration |
Strength and Durability | Produces parts with excellent mechanical properties | Size limitations due to build chamber constraints |
Cost | Long-term cost savings in material and production efficiency | High initial investment in equipment and materials |
FAQ
What is Laser-Based Powder Bed Fusion?
Laser-Based Powder Bed Fusion (PBF) is an additive manufacturing process that uses a high-powered laser to fuse metal powder particles layer by layer to create a solid, three-dimensional object.
What types of metal powders can be used in PBF?
Various metal powders such as Titanium Ti-6Al-4V, Aluminum AlSi10Mg, Stainless Steel 316L, Inconel 718, Cobalt-Chrome, Maraging Steel, Copper, Nickel Alloy 625, Tool Steel H13, and Titanium Ti-5Al-2.5Sn can be used.
What are the advantages of Laser-Based Powder Bed Fusion?
The advantages include high precision and detail, material efficiency, customization, speed and efficiency, and the production of parts with excellent mechanical properties.
What are the limitations of Laser-Based Powder Bed Fusion?
Limitations include high initial costs, complexity in operation, size limitations, and the need for post-processing to achieve desired surface finishes.
Which industries benefit from Laser-Based Powder Bed Fusion?
Industries such as aerospace, medical, automotive, tooling, jewelry, energy, electronics, dental, marine, and architecture benefit from PBF due to its versatility and precision.
How does PBF compare to traditional manufacturing methods?
PBF offers faster production times, higher precision, and the ability to create complex geometries that are challenging for traditional methods. However, it involves higher initial costs and operational complexity.
Conclusion
Laser-Based Powder Bed Fusion is paving the way for the future of manufacturing. Its ability to produce high-precision, customized parts with minimal waste is transforming industries from aerospace to medical. While it comes with its set of challenges, the advantages far outweigh the limitations, making it a valuable addition to the modern manufacturing toolkit. Whether you’re an engineer, designer, or manufacturer, understanding and leveraging the power of PBF can open new doors of innovation and efficiency in your work.
Share On
MET3DP Technology Co., LTD is a leading provider of additive manufacturing solutions headquartered in Qingdao, China. Our company specializes in 3D printing equipment and high-performance metal powders for industrial applications.
Inquiry to get best price and customized Solution for your business!
Related Articles
About Met3DP
Recent Update
Our Product
CONTACT US
Any questions? Send us message now! We’ll serve your request with a whole team after receiving your message.
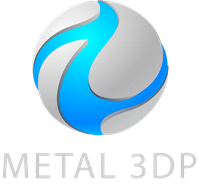
Metal Powders for 3D Printing and Additive Manufacturing