Laser Beam Powder Bed Fusion (PBF-LB)
Table of Contents
Laser Beam Powder Bed Fusion (PBF-LB) is a cutting-edge additive manufacturing technology that’s revolutionizing industries. This article delves deep into the specifics of PBF-LB, including the various metal powders used, their properties, applications, advantages, and disadvantages. Let’s embark on this journey to understand the complexities and opportunities presented by PBF-LB.
Overview of Laser Beam Powder Bed Fusion (PBF-LB)
Laser Beam Powder Bed Fusion (PBF-LB) is an advanced 3D printing technology that uses a high-powered laser to fuse metal powder particles layer by layer, creating intricate and precise metal parts. It’s widely used in aerospace, automotive, medical, and other high-tech industries.
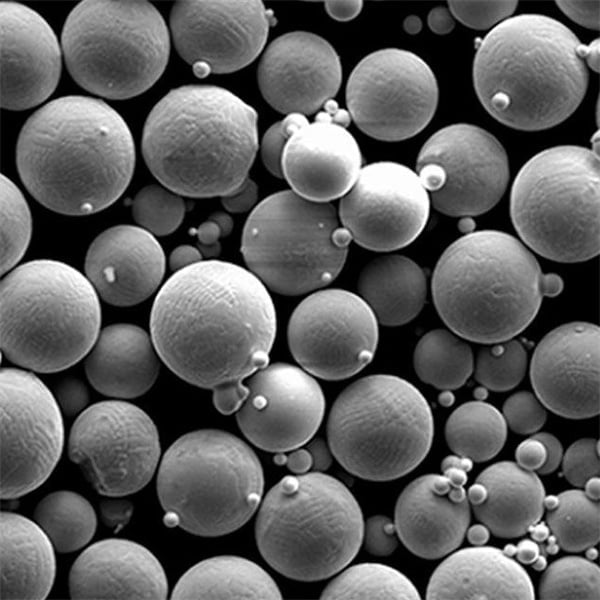
Metal Powder Models for PBF-LB
- Inconel 718
- Composition: Nickel-based superalloy with significant amounts of chromium, iron, and niobium.
- Properties: Excellent tensile strength, creep resistance, and corrosion resistance.
- Applications: Turbine blades, aerospace components, and nuclear reactors.
- Ti-6Al-4V (Titanium Alloy)
- Composition: Titanium alloy with 6% aluminum and 4% vanadium.
- Properties: High strength-to-weight ratio, biocompatibility, and corrosion resistance.
- Applications: Medical implants, aerospace components, and high-performance automotive parts.
- 316L Stainless Steel
- Composition: Iron alloy with chromium, nickel, and molybdenum.
- Properties: Superior corrosion resistance, good weldability, and high ductility.
- Applications: Surgical instruments, chemical processing equipment, and marine applications.
- AlSi10Mg (Aluminum Alloy)
- Composition: Aluminum alloy with silicon and magnesium.
- Properties: Lightweight, high thermal conductivity, and good mechanical properties.
- Applications: Automotive parts, aerospace components, and heat exchangers.
- CoCr (Cobalt-Chromium Alloy)
- Composition: Cobalt alloy with significant chromium content.
- Properties: High wear resistance, biocompatibility, and good mechanical properties.
- Applications: Dental implants, orthopedic implants, and turbine blades.
- H13 Tool Steel
- Composition: Chromium hot-work steel with molybdenum and vanadium.
- Properties: High hardness, thermal fatigue resistance, and toughness.
- Applications: Injection molds, die-casting dies, and extrusion tools.
- Copper
- Composition: Pure copper or copper alloys.
- Properties: Excellent thermal and electrical conductivity.
- Applications: Heat sinks, electrical components, and plumbing fixtures.
- Maraging Steel
- Composition: Iron-nickel alloy with cobalt, molybdenum, and titanium.
- Properties: Ultra-high strength, toughness, and good weldability.
- Applications: Aerospace components, tooling, and high-performance gears.
- Nickel Alloy 625
- Composition: Nickel-based superalloy with chromium, molybdenum, and niobium.
- Properties: Outstanding corrosion resistance and high strength.
- Applications: Marine applications, chemical processing, and aerospace components.
- 316L Stainless Steel
- Composition: Iron alloy with chromium, nickel, and molybdenum.
- Properties: Superior corrosion resistance, good weldability, and high ductility.
- Applications: Surgical instruments, chemical processing equipment, and marine applications.
Table of Metal Powders for PBF-LB
Metal Powder | Composition | Properties | Applications |
---|---|---|---|
Inconel 718 | Nickel, Chromium, Iron, Niobium | Tensile strength, creep resistance, corrosion resistance | Turbine blades, aerospace, nuclear reactors |
Ti-6Al-4V | Titanium, Aluminum, Vanadium | Strength-to-weight ratio, biocompatibility, corrosion resistance | Medical implants, aerospace, automotive |
316L Stainless Steel | Iron, Chromium, Nickel, Molybdenum | Corrosion resistance, weldability, ductility | Surgical instruments, chemical equipment, marine |
AlSi10Mg | Aluminum, Silicon, Magnesium | Lightweight, thermal conductivity, mechanical properties | Automotive, aerospace, heat exchangers |
CoCr | Cobalt, Chromium | Wear resistance, biocompatibility, mechanical properties | Dental implants, orthopedic implants, turbine blades |
H13 Tool Steel | Chromium, Molybdenum, Vanadium | Hardness, thermal fatigue resistance, toughness | Injection molds, die-casting dies, extrusion tools |
Copper | Pure Copper or Copper Alloys | Thermal and electrical conductivity | Heat sinks, electrical components, plumbing fixtures |
Maraging Steel | Iron, Nickel, Cobalt, Molybdenum, Titanium | Ultra-high strength, toughness, weldability | Aerospace components, tooling, high-performance gears |
Nickel Alloy 625 | Nickel, Chromium, Molybdenum, Niobium | Corrosion resistance, high strength | Marine applications, chemical processing, aerospace |
316L Stainless Steel | Iron, Chromium, Nickel, Molybdenum | Corrosion resistance, weldability, ductility | Surgical instruments, chemical equipment, marine |
Applications of Laser Beam Powder Bed Fusion (PBF-LB)
PBF-LB technology is highly versatile and finds applications across various industries. Here’s a detailed look at where and how this technology is used:
Industry | Applications |
---|---|
Aerospace | Turbine blades, structural components, engine parts, fuel nozzles |
Automotive | Engine components, lightweight structures, exhaust systems |
Medical | Implants (dental, orthopedic), surgical instruments, prosthetics |
Dental | Crowns, bridges, dental implants |
Tooling | Injection molds, die-casting dies, extrusion tools |
Energy | Turbine components, heat exchangers, drilling tools |
Defense | Lightweight armor, structural components, weapon parts |
Electronics | Heat sinks, housings, connectors |
Jewelry | Custom designs, intricate patterns, high-quality finishes |
Advantages of Laser Beam Powder Bed Fusion (PBF-LB)
- Complex Geometries
- PBF-LB allows for the creation of intricate and complex geometries that would be impossible or extremely costly to produce using traditional manufacturing methods.
- Material Efficiency
- This technology is highly material-efficient as it uses only the necessary amount of metal powder, minimizing waste and reducing costs.
- Customization and Flexibility
- PBF-LB offers unparalleled customization, making it ideal for producing bespoke parts tailored to specific requirements.
- High-Quality Output
- The parts produced by PBF-LB are of high quality with excellent mechanical properties, ensuring durability and performance.
- Reduction in Production Time
- The ability to produce parts directly from digital designs significantly reduces the time from design to production.
Disadvantages of Laser Beam Powder Bed Fusion (PBF-LB)
- High Initial Costs
- The setup costs for PBF-LB machines are high, which can be a barrier for small and medium-sized enterprises.
- Material Limitations
- Not all materials can be processed using PBF-LB, limiting its applicability in some cases.
- Post-Processing Requirements
- Parts often require extensive post-processing, such as heat treatment and surface finishing, adding to the overall production time and cost.
- Powder Handling Challenges
- Handling and recycling metal powders can be challenging and require strict safety protocols to prevent contamination and health hazards.
Specifications and Standards for PBF-LB
When working with PBF-LB, it’s essential to adhere to specific standards and specifications to ensure quality and consistency. Here’s a look at some key parameters:
Specification | Details |
---|---|
Layer Thickness | Typically ranges from 20 to 100 microns |
Laser Power | Varies from 200 to 1000 watts |
Build Volume | Depends on the machine, commonly 250x250x300 mm to 400x400x400 mm |
Material Density | Near 100% density achievable |
Surface Roughness | Typically requires post-processing for smooth finishes |
Standards | ASTM F2924 (Ti-6Al-4V), ASTM F3055 (Inconel 625), ASTM F3184 (CoCr) |
Suppliers and Pricing Details
Selecting the right supplier is crucial for obtaining high-quality metal powders and PBF-LB machines. Here’s a list of notable suppliers and indicative pricing:
Supplier | Products | Pricing (Approx.) |
---|---|---|
EOS | Metal powders, PBF-LB machines | Metal powders: $300-600/kg, Machines: $200,000+ |
SLM Solutions | Metal powders, PBF-LB machines | Metal powders: $250-500/kg, Machines: $250,000+ |
Renishaw | Metal powders, PBF-LB machines | Metal powders: $200-550/kg, Machines: $300,000+ |
GE Additive | Metal powders, PBF-LB machines | Metal powders: $350-700/kg, Machines: $500,000+ |
Carpenter Additive | Metal powders | Metal powders: $400-800/kg |
Praxair Surface Technologies | Metal powders | Metal powders: $300-600/kg |
Sandvik | Metal powders | Metal powders: $350-650/kg |
Höganäs | Metal powders | Metal powders: $250-500/kg |
3D Systems | Metal powders, PBF-LB machines | Metal powders: $300-600/kg, Machines: $350,000+ |
Materialise | Metal powders, PBF-LB machines | Metal powders: $250-550/kg, Machines: $250,000+ |
Comparison of Pros and Cons
Pros of Laser Beam Powder Bed Fusion (PBF-LB)
- Design Flexibility
- Create complex shapes that are not possible with traditional manufacturing.
- Material Efficiency
- Minimize waste by using only the needed amount of powder.
- Customization
- Easily produce custom parts tailored to specific needs.
- High-Quality Parts
- Achieve excellent mechanical properties and high precision.
Cons of Laser Beam Powder Bed Fusion (PBF-LB)
- High Costs
- Expensive initial setup and material costs.
- Material Limitations
- Not all materials are suitable for PBF-LB.
- Post-Processing
- Parts often need significant post-processing.
- Powder Handling
- Requires careful handling and safety measures.
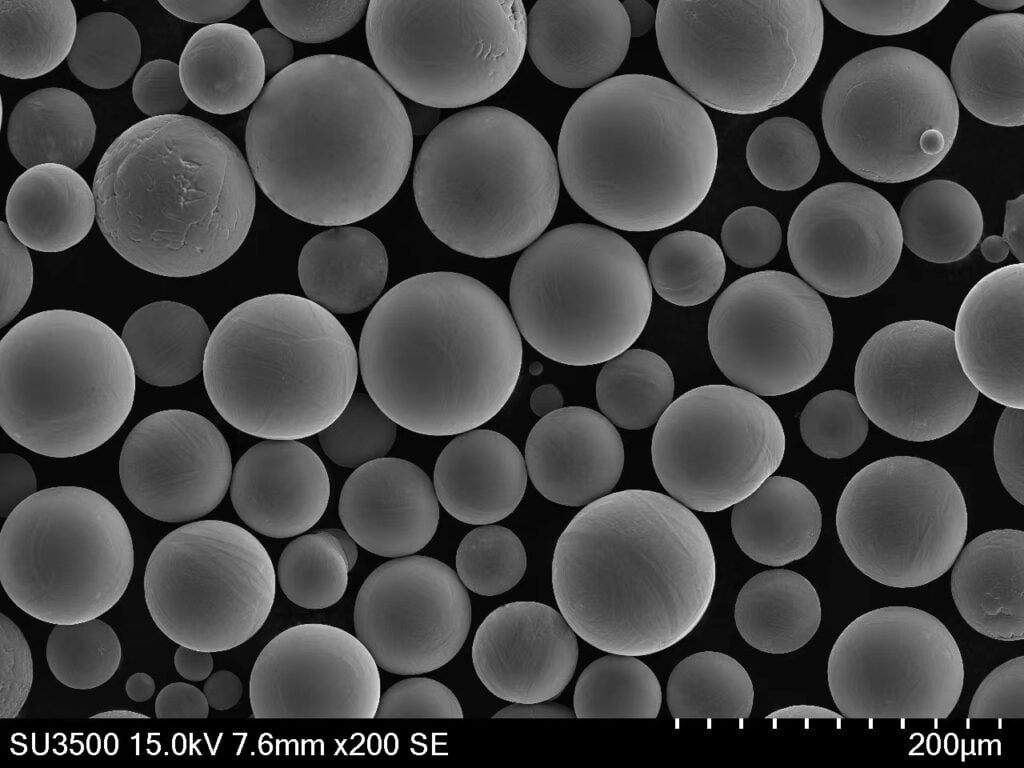
FAQ
Question | Answer |
---|---|
What is PBF-LB? | PBF-LB is a 3D printing technology that uses a laser to fuse metal powder layer by layer to create metal parts. |
What materials can be used in PBF-LB? | Common materials include Inconel 718, Ti-6Al-4V, 316L stainless steel, AlSi10Mg, CoCr, H13 tool steel, copper, maraging steel, and nickel alloy 625. |
What industries use PBF-LB? | Aerospace, automotive, medical, dental, tooling, energy, defense, electronics, and jewelry industries use PBF-LB. |
What are the benefits of PBF-LB? | Benefits include the ability to create complex geometries, high material efficiency, customization options, and high-quality parts. |
What are the limitations of PBF-LB? | Limitations include high initial costs, material restrictions, the need for post-processing, and challenges in powder handling. |
How does PBF-LB compare to traditional methods? | PBF-LB offers more design flexibility and material efficiency but comes with higher costs and requires post-processing compared to traditional methods. |
What is the typical layer thickness in PBF-LB? | The typical layer thickness ranges from 20 to 100 microns. |
Are there standards for PBF-LB materials? | Yes, standards include ASTM F2924 for Ti-6Al-4V, ASTM F3055 for Inconel 625, and ASTM F3184 for CoCr. |
What post-processing is required? | Common post-processing steps include heat treatment, surface finishing, and machining to achieve the desired properties and finish. |
How to choose a supplier for PBF-LB materials? | Look for reputable suppliers who offer high-quality materials and PBF-LB machines, considering factors like pricing, availability, and support services. |
Conclusion
Laser Beam Powder Bed Fusion (PBF-LB) is a transformative technology in the additive manufacturing landscape. Its ability to produce highly complex, custom parts with superior material properties makes it a favorite among industries requiring precision and performance. However, the high initial costs and post-processing requirements are notable challenges. As technology advances, we can expect further improvements in efficiency, material options, and overall accessibility, paving the way for even broader adoption.
Feel free to dive deeper into each section and explore the tables provided to understand the specifics of PBF-LB and how it can benefit various applications. Whether you’re an engineer, designer, or manufacturer, understanding PBF-LB is essential for leveraging its full potential in your projects.
Share On
MET3DP Technology Co., LTD is a leading provider of additive manufacturing solutions headquartered in Qingdao, China. Our company specializes in 3D printing equipment and high-performance metal powders for industrial applications.
Inquiry to get best price and customized Solution for your business!
Related Articles
About Met3DP
Recent Update
Our Product
CONTACT US
Any questions? Send us message now! We’ll serve your request with a whole team after receiving your message.
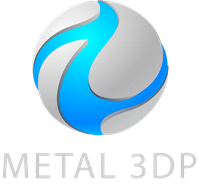
Metal Powders for 3D Printing and Additive Manufacturing