laser powder bed fusion(LPBF)
Table of Contents
Imagine crafting complex metal objects with unparalleled precision, layer by layer, from a pool of metallic dust. This isn’t science fiction; it’s the reality of Laser Powder Bed Fusion (LPBF), a revolutionary 3D printing technology that’s transforming the manufacturing landscape.
LPBF, also known as Selective Laser Melting (SLM) or Direct Metal Laser Sintering (DMLS), has opened doors to creating intricate metal parts with unique geometries and superior properties. But how exactly does it work? Buckle up, because we’re diving deep into the world of LPBF, exploring its potential, the metal powders that fuel this process, and the exciting applications it fosters.
How Does LPBF Work?
Think of LPBF as a sophisticated sculptor wielding a laser beam instead of a chisel. Here’s a breakdown of the process:
- Powder Bed Preparation: A thin layer of fine metal powder is meticulously spread across a platform inside a printer chamber. This powder, the building block of your creation, comes in various metals, each with its unique properties. We’ll delve into the fascinating world of metal powders further down the line.
- Laser Melts & Fuses: A high-powered laser beam acts as the sculptor’s chisel, meticulously tracing the desired cross-section of the first layer onto the powder bed. The laser’s intensity is precisely controlled, melting the powder particles at the designated areas and fusing them together.
- Layer by Layer Creation: Once the first layer solidifies, the platform lowers slightly, and a fresh layer of powder is spread. The laser then dances across this new layer, fusing it with the solidified layer below. This meticulous process repeats itself, building the object layer by layer until the final design is complete.
- Support Removal: After the printing process, the completed object is still encased in unmelted powder. This support powder is then removed through various techniques like sandblasting or bead blasting, revealing the final masterpiece.
LPBF offers unparalleled design freedom. Unlike traditional subtractive manufacturing techniques like machining, where material is removed from a solid block, LPBF allows for the creation of intricate internal features, channels, and hollow structures that would be impossible with conventional methods. Imagine printing a lightweight yet robust heat exchanger with complex internal channels for optimal heat transfer – that’s the power of LPBF at play.
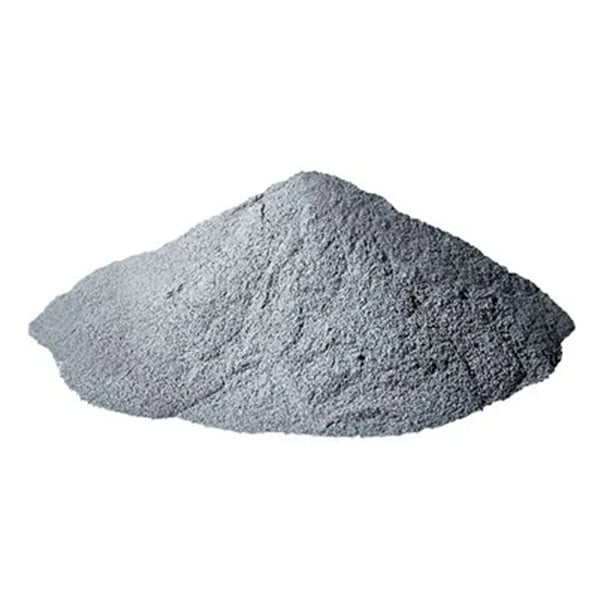
Fueling LPBF Creations
The success of LPBF hinges on the quality and characteristics of the metal powder used. Just like artists have their preferred paints and sculptors their favorite clays, LPBF practitioners rely on a diverse range of metal powders to bring their visions to life. Here are ten commonly used metal powders, each with its own strengths and applications:
Metal Powder | Composition | Properties | Applications |
---|---|---|---|
Stainless Steel 316L | Fe (Iron), Cr (Chromium), Ni (Nickel), Mo (Molybdenum) | Excellent corrosion resistance, high strength, biocompatible | Aerospace components, medical implants, chemical processing equipment |
Titanium Ti6Al4V | Ti (Titanium), Al (Aluminum), V (Vanadium) | High strength-to-weight ratio, excellent biocompatibility, good corrosion resistance | Aerospace components, medical implants, sporting goods |
Inconel 625 | Ni (Nickel), Cr (Chromium), Mo (Molybdenum), Fe (Iron) | Exceptional high-temperature performance, good corrosion resistance | Turbine blades, heat exchangers, chemical processing equipment |
Aluminum AlSi10Mg | Al (Aluminum), Si (Silicon), Mg (Magnesium) | Lightweight, good strength, high corrosion resistance | Automotive components, aerospace structures, heat sinks |
Copper | Cu (Copper) | High electrical and thermal conductivity | Heat exchangers, electrical components, waveguides |
Nickel | Ni (Nickel) | High corrosion resistance, good ductility | Chemical processing equipment, electronics components |
Cobalt Chrome CoCrMo | Co (Cobalt), Cr (Chromium), Mo (Molybdenum) | High wear resistance, biocompatible | Joint replacements, cutting tools, dental implants |
Tool Steel | Varies depending on type (e.g., H13) | High hardness, good wear resistance | Dies, molds, cutting tools |
Inconel 718 | Ni (Nickel), Cr (Chromium), Fe (Iron), Nb (Niobium) | High strength, excellent creep resistance at high temperatures | Turbine disks, rocket engine components, pressure vessels |
Molybdenum | Mo (Molybdenum) | High melting point, good thermal conductivity | Electrodes, crucibles, high-temperature applications |
This table provides a glimpse into the diverse world of metal powders used in LPBF. The choice of powder depends on the desired properties of the final part. For instance, if you’re creating a medical implant that needs to withstand the harsh environment inside the human body, biocompatible materials like Stainless Steel 316L or Titanium Ti6Al4V would be ideal choices. Conversely, if you’re printing a turbine blade that needs to handle extreme temperatures and pressures, a high-temperature performer like Inconel 625 would be a better fit.
Beyond the Basics: Parameters and Considerations
While the core concept of LPBF seems straightforward, achieving consistent, high-quality results requires meticulous control over several parameters:
- Laser Power and Scan Speed: The laser’s power density (a combination of power and scan speed) dictates the depth and width of molten metal. A higher power density creates a deeper melt pool, leading to thicker layers and potentially higher residual stress in the final part. Conversely, a lower power density creates a shallower melt pool, resulting in thinner layers and potentially better mechanical properties. Finding the optimal balance between these factors is crucial.
- Powder Layer Thickness: The thickness of each powder layer significantly impacts the resolution and surface finish of the final part. Thinner layers offer finer detail, but require more printing time and can be more susceptible to defects like porosity. Conversely, thicker layers offer faster printing but can lead to a rougher surface finish.
- Inert Gas Atmosphere: LPBF typically takes place within an enclosed chamber filled with an inert gas like argon or helium. This prevents oxidation of the molten metal during the printing process, ensuring the quality and integrity of the final part.
The Finishing Touches: Post-Processing Techniques
Once the LPBF process is complete, the newly printed object isn’t quite ready for use. Here are some common post-processing techniques employed:
- Support Removal: As mentioned earlier, the printed object is often encased in unmelted support powder. Techniques like sandblasting or bead blasting are used to meticulously remove this powder, revealing the final part.
- Heat Treatment: Heat treatment processes like stress relieving or annealing can be employed to improve the mechanical properties of the finished part by reducing residual stresses and optimizing the microstructure.
- Machining: In some cases, post-machining operations might be necessary to achieve specific dimensional tolerances or surface finishes.
Applications of LPBF
LPBF’s ability to create complex geometries with superior material properties has opened doors to a wide range of groundbreaking applications across various industries:
Aerospace & Defense: LPBF is a game-changer in aerospace, enabling the creation of lightweight yet high-strength components for aircraft, satellites, and spacecraft. Think intricate rocket engine parts, complex heat exchangers, and even lattice structures for weight reduction. In the defense sector, LPBF is used to manufacture custom weapon components and lightweight armor with superior ballistic properties.
Medical & Dental: The biocompatible nature of certain metal powders makes LPBF a valuable tool in the medical and dental fields. LPBF-printed implants like hip replacements, knee joints, and dental crowns offer excellent biocompatibility, improved osseointegration (fusion with bone), and the ability to create custom-designed implants for individual patients.
Automotive: The automotive industry is increasingly leveraging LPBF to create lightweight components for racing cars and high-performance vehicles. Think intricate gear housings, complex cooling channels in pistons, and even customized components for electric vehicle motors.
Consumer Goods: LPBF is making inroads into the consumer goods sector as well. From custom-designed jewelry and sports equipment to lightweight camera components and even personalized prosthetics, the possibilities are endless.
Advantages and Limitations of LPBF
LPBF boasts several compelling advantages that make it a highly attractive manufacturing technology:
- Design Freedom: Unlike traditional subtractive methods, LPBF allows for the creation of complex internal features, channels, and hollow structures, pushing the boundaries of design possibilities.
- Lightweighting: The ability to create intricate lattice structures and optimize part design for minimal material usage makes LPBF ideal for creating lightweight, high-strength components.
- Material Efficiency: LPBF offers minimal material waste compared to traditional methods, making it a more sustainable option.
- Customization: LPBF readily facilitates the creation of custom-designed parts, ideal for applications like medical implants and personalized products.
However, LPBF also has limitations to consider:
- Cost: LPBF machines and metal powders can be expensive, making it a technology suited for high-value applications or production of small batches.
- Surface Finish: While LPBF parts can achieve good surface finishes, they might require additional post-processing for specific applications.
- Build Size Limitations: Current LPBF machines have limitations on the size of parts they can create.
- Process Complexity: LPBF requires careful parameter control and expertise to achieve consistent, high-quality results.
LPBF vs Other 3D Printing Technologies
LPBF occupies a distinct space within the vast world of 3D printing technologies. Here’s a quick comparison of LPBF with other popular methods:
Feature | LPBF | Fused Deposition Modeling (FDM) | Stereolithography (SLA) | Selective Laser Sintering (SLS) |
---|---|---|---|---|
Process | Laser melting of metal powder | Extrusion of molten plastic filament | Vat photopolymerization with a laser | Selective sintering of polymer powder |
Materials | Metals | Thermoplastics | Photopolymers | Thermoplastics |
Part Complexity | High | Moderate | High | Moderate |
Surface Finish | Good (may require post-processing) | Moderate | High | Moderate |
Strength & Durability | High | Moderate | Moderate | Moderate |
Applications | Aerospace, medical, automotive | Prototyping, functional parts | Prototyping, models, medical applications | Prototyping, functional parts |
Cost per Part | High | Low | Moderate | Moderate |
As you can see, LPBF excels in creating high-strength, complex metal parts, making it ideal for demanding applications in industries like aerospace and medicine. However, FDM offers a more cost-effective option for prototyping and creating functional parts from various thermoplastics. SLA and SLS cater well to applications requiring high-resolution details and smooth surface finishes for prototypes or specific functional parts.
So You Want to Dive into LPBF?
If you’re considering incorporating LPBF into your manufacturing process, here are some key factors to consider:
Cost Considerations:
- Machine Cost: LPBF machines can range in price from hundreds of thousands to millions of dollars, depending on factors like build size, laser power, and machine capabilities.
- Material Cost: Metal powders can be expensive, with some exotic alloys costing upwards of $200 per kilogram.
- Operational Costs: The cost of inert gas, electricity, and labor also needs to be factored in.
Technical Specifications to Consider:
- Build Volume: The size of the printer’s chamber determines the maximum dimensions of the parts you can create.
- Laser Power: Higher laser power allows for melting thicker layers and potentially faster printing, but can also impact the final part’s properties.
- Material Compatibility: The printer needs to be compatible with the specific metal powder you intend to use.
Beyond the initial investment, factors like part complexity, desired production volume, and post-processing requirements will also influence the overall cost of using LPBF.
The Future of LPBF
LPBF is a rapidly evolving technology, and experts predict a bright future for this innovative manufacturing method. Here are some key trends to watch:
- Advancements in Metal Powders: The development of new metal powders with improved properties like better flowability and printability will continue to expand the applications of LPBF.
- Reduced Machine Costs: As LPBF technology matures, we can expect a decrease in the cost of LPBF machines, making it more accessible to a wider range of manufacturers.
- Increased Automation: Integration of automation and in-process quality control systems will streamline the LPBF process and improve overall efficiency.
- Hybrid Manufacturing Techniques: The combination of LPBF with other manufacturing methods like machining or additive electroplating will create exciting new possibilities for creating complex, multi-material parts.
In conclusion, LPBF is a revolutionary 3D printing technology that is transforming the way we design and manufacture complex metal parts. With its ability to create intricate geometries, achieve superior material properties, and offer design freedom, LPBF is poised to play a pivotal role in shaping the future of manufacturing across various industries.
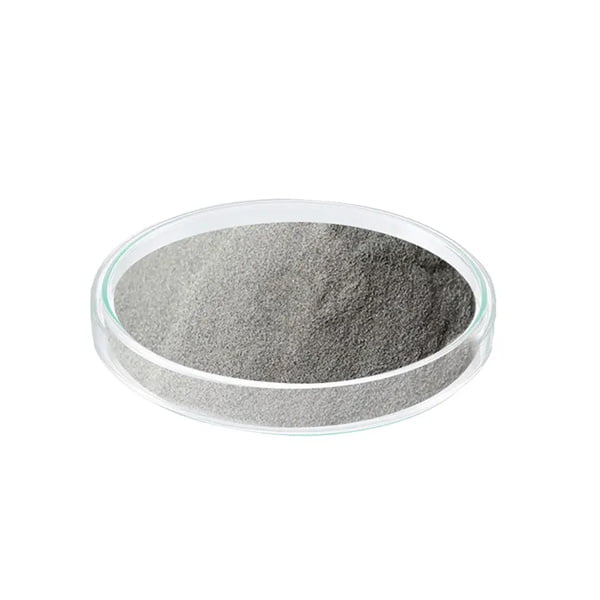
FAQs
Q: What are the advantages of LPBF over traditional manufacturing methods?
A: LPBF offers several advantages, including design freedom for creating complex geometries, lightweighting capabilities, material efficiency, and the ability to create custom parts.
Q: What are the limitations of LPBF?
A: LPBF can be expensive due to the high cost of machines and metal powders. The build size of parts is limited by the machine’s chamber size, and the process requires careful parameter control for consistent results.
Q: What industries are using LPBF?
A: LPBF finds applications in various industries, including aerospace, medical and dental, automotive, and consumer goods.
Q: What are some factors to consider before investing in LPBF technology?
A: Consider the initial cost of the machine, metal powders, and operational expenses. Evaluate the technical specifications like build volume, laser power, and material compatibility based on your desired applications. Finally, factor in the part complexity, production volume, and post-processing needs to determine the overall cost-effectiveness of LPBF for your specific requirements.
Q: Is LPBF safe?
A: LPBF can involve safety hazards like laser radiation and exposure to metal dust. However, proper safety protocols, including using enclosed chambers, personal protective equipment, and proper ventilation systems, can significantly mitigate these risks.
Q: How does LPBF compare to other 3D printing technologies?
A: LPBF excels in creating high-strength, complex metal parts. FDM offers a more cost-effective option for prototyping plastic parts. SLA and SLS cater to applications requiring high-resolution details and smooth finishes for prototypes or specific functional parts.
Q: What are some of the future trends expected in LPBF technology?
A: Advancements in metal powders with improved properties, reduced machine costs, increased automation, and the exploration of hybrid manufacturing techniques combining LPBF with other methods are some exciting trends shaping the future of LPBF.
Q: Where can I find more information about LPBF?
A reputable source for information on LPBF is the American Society for Testing and Materials (ASTM) International. They publish standards and specifications related to LPBF processes and materials. You can find more details on their website: ASTM International: https://www.astm.org/.
Share On
MET3DP Technology Co., LTD is a leading provider of additive manufacturing solutions headquartered in Qingdao, China. Our company specializes in 3D printing equipment and high-performance metal powders for industrial applications.
Inquiry to get best price and customized Solution for your business!
Related Articles
About Met3DP
Recent Update
Our Product
CONTACT US
Any questions? Send us message now! We’ll serve your request with a whole team after receiving your message.
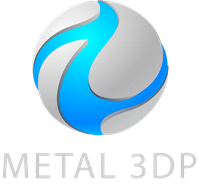
Metal Powders for 3D Printing and Additive Manufacturing