Magic 3D Printing: LPBF process
Table of Contents
Have you ever dreamt of building complex metal objects layer by layer, with nothing but a laser and some metal powder? Well, that’s the magic of LPBF process, a revolutionary 3D printing technology that’s transforming the manufacturing landscape. Imagine the possibilities: crafting intricate medical implants, designing lightweight aerospace components, or even creating bespoke jewelry – all with unparalleled precision and design freedom.
This guide dives deep into the LPBF process, exploring its intricacies, the metallic materials that fuel its potential, and the advantages and limitations that shape its applications. So, buckle up and get ready to unlock the secrets of this fascinating technology!
Decoding the LPBF Process
LPBF, also known as Laser Melting (LM), works like a skilled sculptor meticulously building an object. Here’s a breakdown of its core steps:
- Powder Preparation: The stage is set with a bed of fine metal powder, meticulously spread into a thin layer by a coating mechanism. Think of it like laying the foundation for your 3D masterpiece.
- Laser Magic: A high-powered laser beam takes center stage, selectively melting specific regions of the powder bed according to a digital blueprint. Imagine the laser acting like a paintbrush, drawing the desired design onto the powdery canvas.
- Solidification Symphony: As the laser melts the powder, it rapidly cools and solidifies, bonding with the surrounding material to form a solid layer. This process is akin to the molten lava hardening into rock, but at a much faster pace.
- Layer by Layer: The magic continues as the platform lowers slightly, and a fresh layer of powder is deposited. The laser then dances across this new layer, melting the designated areas and fusing them to the previous layer. This cycle repeats itself tirelessly, building the object one layer at a time.
- The Grand Reveal: Once the final layer is complete, the platform descends, and your 3D-printed metal masterpiece emerges from the chamber, ready for post-processing steps like support removal and surface finishing.
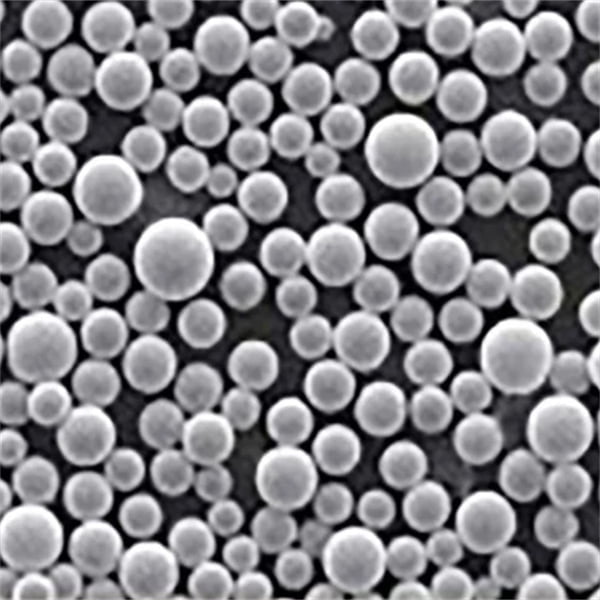
Fueling LPBF’s Potential
The success of the LPBF process hinges on the type of metal powder used. Just like different paints create distinct artistic effects, various metal powders offer unique properties for diverse applications. Let’s delve into some of the most popular metal powders used in LPBF:
Metal Powder | Composition | Properties | Applications |
---|---|---|---|
Stainless Steel 316L | Fe (Iron), Cr (Chromium), Ni (Nickel), Mo (Molybdenum) | Excellent corrosion resistance, biocompatible, high strength | Medical implants, aerospace components, chemical processing equipment |
Titanium Ti6Al4V | Ti (Titanium), Al (Aluminum), V (Vanadium) | High strength-to-weight ratio, good biocompatibility, excellent corrosion resistance | Aerospace components, biomedical implants, sporting goods |
Inconel 625 | Ni (Nickel), Cr (Chromium), Mo (Molybdenum), Fe (Iron) | Exceptional high-temperature performance, excellent corrosion resistance | Turbine blades, heat exchangers, pressure vessels |
Aluminum AlSi10Mg | Al (Aluminum), Si (Silicon), Mg (Magnesium) | High strength, good weldability, lightweight | Automotive components, heat sinks, electronic enclosures |
Copper Cu | Cu (Copper) | Excellent thermal and electrical conductivity | Heat sinks, electrical components, electrodes |
Nickel 718 | Ni (Nickel), Cr (Chromium), Fe (Iron), Mo (Molybdenum) | High strength, good creep resistance, excellent corrosion resistance | Aerospace components, oil and gas exploration equipment |
Cobalt Chrome CoCrMo | Co (Cobalt), Cr (Chromium), Mo (Molybdenum) | High wear resistance, biocompatible | Joint replacements, dental implants, cutting tools |
Tool Steel H13 | Fe (Iron), Cr (Chromium), Mo (Molybdenum), V (Vanadium) | High hardness, good wear resistance | Molds, dies, cutting tools |
Maraging Steel 1.2709 | Fe (Iron), Ni (Nickel), Mo (Molybdenum), Ti (Titanium) | High strength, good ductility, excellent toughness | Aerospace components, defense applications |
Gold Au | Au (Gold) | High corrosion resistance, excellent electrical conductivity | Jewelry, electronic components (limited applications due to high cost) |
Beyond the Table: Unveiling the Nuances
This table provides a glimpse into the vast world of metal powders for LPBF. Each material boasts unique characteristics, making them suitable for specific applications. For instance, Stainless Steel 316L’s biocompatibility makes it ideal for medical implants, while Titanium Ti6Al4V’s strength-to-weight ratio shines in aerospace components. Inconel 625 can withstand scorching temperatures within turbine blades, while Aluminum AlSi10Mg’s lightweight properties make it a favorite for automotive components.
The selection process doesn’t stop there. Factors like powder particle size, flowability, and surface morphology also play a crucial role. Imagine using chunky pebbles instead of fine sand to build a sandcastle – the resulting structure would be weak and unstable. Similarly, using metal powders with inconsistent particle size or poor flowability can lead to irregularities and defects in the final LPBF product.
Here’s a deeper dive into some key considerations when choosing metal powders for LPBF:
- Particle Size and Distribution: Metal powders for LPBF are incredibly fine, typically ranging from 15 to 100 microns in diameter (that’s about 15-100 thousandths of a millimeter!). This fine size ensures smooth layer formation and minimizes the risk of defects. Additionally, a consistent particle size distribution is crucial for optimal flowability and laser melting efficiency.
- Flowability: The powder needs to flow freely and evenly across the build platform to ensure a uniform layer thickness. Poor flowability can lead to inconsistencies in the powder bed density, which can negatively impact the final product’s properties. Imagine trying to spread wet sand – it clumps and creates uneven surfaces. Metal powders with a spherical shape and smooth surface tend to flow better compared to those with irregular shapes or rough surfaces.
- Surface Morphology: The surface characteristics of the powder particles can influence the laser melting process. Powders with a slightly oxidized surface can absorb the laser beam more efficiently, promoting better melting and bonding. However, excessive oxidation can hinder the flowability and lead to the formation of unwanted oxides within the final product.
Material Selection of LPBF process
Choosing the right metal powder for your LPBF project is akin to a matchmaker’s job – you need to find the perfect match between the material properties and the desired application. Here are some guiding principles:
- Strength and Weight: If your application demands a robust component that can withstand high loads, then metal powders like Nickel 718 or Maraging Steel might be ideal choices. However, if weight is a critical factor, consider lightweight options like Aluminum AlSi10Mg or Titanium Ti6Al4V.
- Corrosion Resistance: For components exposed to harsh environments or corrosive elements, material selection becomes even more crucial. Stainless Steel 316L and Inconel 625 excel in corrosion resistance, making them suitable for marine applications or chemical processing equipment.
- Biocompatibility: When it comes to medical implants, biocompatibility reigns supreme. Stainless Steel 316L and Cobalt Chrome CoCrMo are popular choices due to their excellent biocompatibility, minimizing the risk of rejection by the human body.
- Thermal and Electrical Conductivity: If your application requires efficient heat dissipation or superior electrical conductivity, consider materials like Copper Cu or Aluminum AlSi10Mg. These metals excel in these areas, making them suitable for heat sinks or electrical components.
The Importance of Powder Suppliers and Quality Control
Selecting a reputable metal powder supplier is paramount for a successful LPBF project. Consistent powder quality is essential to ensure optimal printability, minimal defects, and consistent mechanical properties in the final product. Look for suppliers who offer powders with well-characterized properties, including chemical composition, particle size distribution, and flowability. Additionally, in-depth quality control measures throughout the manufacturing process are crucial to maintain consistent powder quality.
The Cost Equation: Balancing Performance and Budget
Metal powders for LPBF can vary significantly in cost depending on the material, powder characteristics, and supplier. For instance, precious metals like Gold will naturally be more expensive than common materials like steel. It’s important to strike a balance between the desired performance characteristics and your project budget. Sometimes, exploring alternative materials with similar properties but lower costs can be a viable option.
the LPBF’s Advantages
LPBF has revolutionized the manufacturing landscape by offering a plethora of advantages over traditional techniques:
- Design Freedom: Unlike subtractive manufacturing methods like machining, LPBF allows for the creation of complex geometries with intricate internal features. This design freedom opens doors for innovative and lightweight components that were previously impossible to manufacture.
- Mass Customization: LPBF empowers the creation of customized products without the need for expensive tooling changes. Imagine producing a batch of prosthetic limbs, each tailored to the specific needs of an individual. This level of customization paves the way for personalized medicine and advanced product offerings.
- Reduced Waste: Traditional manufacturing processes often generate significant scrap material. LPBF, on the other hand, utilizes a near-net-shape manufacturing approach, minimizing material waste. This not only reduces costs but also aligns with sustainable manufacturing practices.
- Complex Internal Features: The layer-by-layer nature of LPBF enables the creation of intricate internal channels, lattices, and other features that are difficult or impossible to achieve with traditional techniques. Imagine designing a lightweight heat exchanger with internal channels that maximize heat transfer efficiency. LPBF makes such designs a reality.
- Improved Performance: LPBF can produce components with superior mechanical properties, such as higher strength-to-weight ratios and improved fatigue resistance. This is due to the fine microstructure and minimal heat-affected zone associated with the LPBF process. These performance enhancements can lead to lighter, more efficient products in various industries.
- Inventory Reduction: With LPBF’s ability to produce on-demand, companies can reduce the need for large inventories of spare parts. This translates to lower storage costs and increased flexibility in production planning.
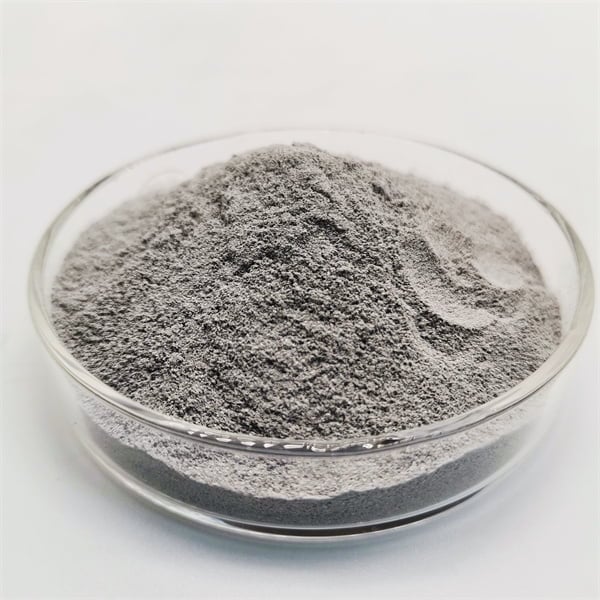
the LPBF’s Limitations
While LPBF offers a multitude of advantages, it’s important to acknowledge its limitations:
- Cost: LPBF machines and metal powders can be expensive compared to traditional manufacturing equipment and materials. This can be a barrier to entry for smaller companies or projects with limited budgets.
- Build Size Limitations: Current LPBF machines have limitations on the size of parts they can produce. While build sizes are steadily increasing, they may not be suitable for large-scale components.
- Surface Roughness: LPBF-produced parts can exhibit a slightly rough surface finish compared to machined components. However, post-processing techniques like polishing or machining can be employed to achieve a smoother surface finish if required by the application.
- Support Structures: Complex geometries often necessitate the use of support structures during the LPBF process. These supports are necessary to prevent overhanging features from collapsing but require removal after printing, which can add time and cost to the process.
- Material Properties: The properties of LPBF-produced parts can vary slightly from their wrought counterparts due to the rapid solidification process. Understanding these potential variations is crucial during the design and material selection stages.
- Residual Stress: The layer-by-layer nature of LPBF can introduce residual stress within the printed part. In some critical applications, post-processing techniques like stress relieving heat treatments may be necessary to mitigate these stresses.
Applications of LPBF process
LPBF’s unique capabilities have opened doors to a vast array of applications across diverse industries:
- Aerospace: The ability to create lightweight, high-strength components makes LPBF ideal for aerospace applications. Components like aircraft engine brackets, satellite parts, and even rocket engine components are being increasingly produced using LPBF.
- Medical: LPBF is transforming the medical field by enabling the creation of customized prosthetics, implants, and surgical instruments. The biocompatibility of certain metal powders allows for the production of implants that integrate seamlessly with the human body.
- Automotive: The automotive industry is leveraging LPBF to create lightweight components for race cars and high-performance vehicles. Additionally, LPBF is being explored for the production of complex heat exchangers and other fuel-efficient components.
- Consumer Goods: LPBF is finding its way into consumer goods as well. From custom-designed jewelry to lightweight camera components, the possibilities are constantly expanding.
- Tooling: Complex conformal cooling channels can be integrated into molds and dies using LPBF, leading to improved cooling efficiency and faster production cycles.
The Future of LPBF: A Canvas of Possibilities
LPBF technology is still evolving, and the future holds immense promise. Here are some exciting possibilities on the horizon:
- Multi-material LPBF: The ability to print with multiple materials within a single build opens doors for components with graded properties or even functionally integrated electronics. Imagine a cutting tool with a wear-resistant tungsten carbide tip bonded to a tough steel body – all printed in one go!
- Larger Build Sizes: As LPBF technology matures, machine build sizes are expected to increase, paving the way for the production of larger and more complex components.
- Process Qualification and Certification: For safety-critical applications, LPBF processes need to meet stringent qualification and certification standards. This can be a complex and time-consuming process, especially for companies new to LPBF technology.
- Environmental Considerations: Metal powder production and the LPBF process itself can have environmental implications. Metal powder handling requires careful measures to minimize dust inhalation risks. Additionally, the energy consumption associated with LPBF needs to be considered for sustainable manufacturing practices.
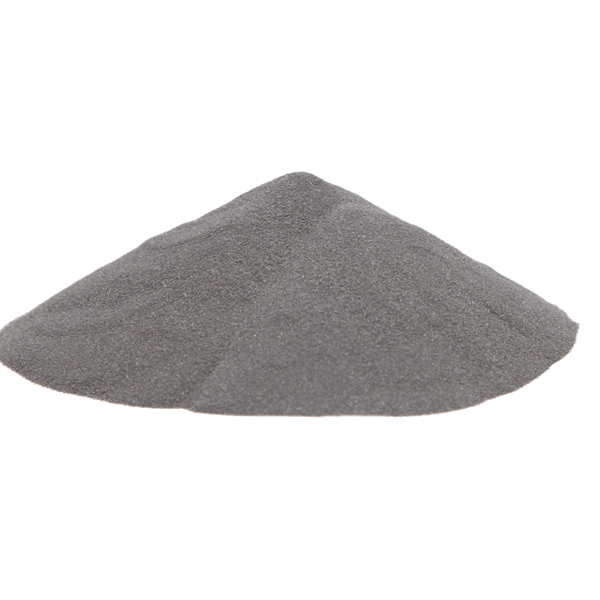
Applications of LPBF process
- Defense: LPBF is being utilized for the production of lightweight armored vehicles, complex weaponry components, and other defense-related applications.
- Energy: LPBF is enabling the creation of intricate components for turbine engines, nuclear reactors, and other energy generation equipment.
- Oil and Gas: The ability to produce high-strength and corrosion-resistant components makes LPBF valuable for oil and gas exploration equipment.
Case Study: LPBF Revolutionizes Aerospace Manufacturing
Let’s delve into a specific example to illustrate the transformative power of LPBF. In the aerospace industry, weight reduction is paramount for fuel efficiency and overall aircraft performance. LPBF has enabled the creation of complex lightweight aerospace components that were previously impossible to manufacture using traditional techniques.
For instance, consider the intricate lattice structures being LPBF-printed for aircraft wing components. These lattices offer exceptional strength-to-weight ratios, significantly reducing weight while maintaining structural integrity. This translates to increased fuel efficiency and greater range for airplanes.
LPBF is also being employed for the production of highly-customized fuel injectors for rocket engines. These complex injectors optimize fuel combustion and contribute to increased engine efficiency and thrust.
These are just a few examples of how LPBF is revolutionizing aerospace manufacturing. As the technology continues to evolve, we can expect even more innovative and lightweight components to take flight.
FAQ
Q: What are the advantages of LPBF over traditional manufacturing methods?
A: LPBF offers several advantages, including design freedom, mass customization, reduced waste, ability to create complex internal features, improved performance, and inventory reduction.
Q: What are the limitations of LPBF?
A: LPBF can be expensive compared to traditional methods, has limitations on build size, can produce parts with a slightly rough surface, requires support structures, and the material properties can differ from wrought counterparts. Additionally, residual stress and environmental considerations need to be addressed.
Q: What are some of the applications of LPBF?
A: LPBF finds applications in aerospace, medical, automotive, consumer goods, tooling, and various other industries.
Q: What is the future of LPBF?
A: The future of LPBF is bright, with possibilities like multi-material printing and larger build sizes on the horizon.
Q: How much does an LPBF machine cost?
A: The cost of an LPBF machine can vary significantly depending on the size, capabilities, and brand. Prices can range from hundreds of thousands of dollars to well over a million dollars.
Q: What are some of the safety precautions when working with LPBF?
A: Metal powder handling requires proper personal protective equipment (PPE) to minimize dust inhalation risks. Additionally, laser safety protocols need to be followed to avoid eye injuries.
Share On
MET3DP Technology Co., LTD is a leading provider of additive manufacturing solutions headquartered in Qingdao, China. Our company specializes in 3D printing equipment and high-performance metal powders for industrial applications.
Inquiry to get best price and customized Solution for your business!
Related Articles
About Met3DP
Recent Update
Our Product
CONTACT US
Any questions? Send us message now! We’ll serve your request with a whole team after receiving your message.
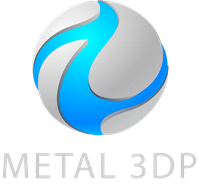
Metal Powders for 3D Printing and Additive Manufacturing