Introduction to Material Jetting
Table of Contents
Imagine a 3D printer that works like a high-tech inkjet, meticulously building objects layer-by-layer with incredible detail and precision. That’s the magic of material jetting, a revolutionary additive manufacturing (AM) process taking the prototyping and production world by storm. Buckle up, because we’re diving deep into this fascinating technology, exploring its inner workings, advantages, applications, and even some of the metal powder materials that fuel its creations.
The Working Principle of Material Jetting
Think of a standard inkjet printer spitting out colored dots of ink to form an image on paper. Now, replace the ink with photopolymer resin and the paper with a 3D printing platform. That’s the essence of material jetting. A printhead, armed with an arsenal of tiny nozzles, precisely jets droplets of photopolymer resin onto the platform, building up the desired object layer by layer. Each layer is then cured using ultraviolet (UV) light, solidifying the resin and transforming the digital blueprint into a tangible 3D masterpiece.
Here’s a closer look at the choreography behind this process:
- Digital Slicing: The 3D model is sliced into ultrathin layers using specialized software. Think of slicing a loaf of bread – each slice represents a layer that the printer will build upon.
- Material Jetting: The printhead, like a tireless conductor, orchestrates the deposition of resin droplets. Different materials can be jetted simultaneously, enabling the creation of objects with varying properties and even color combinations.
- Curing: Each deposited layer is bathed in UV light, triggering a chemical reaction that hardens the resin, locking it into place.
- Layer by Layer: This meticulous dance of jetting, curing, and platform lowering continues until the entire object is meticulously built.
- Post-Processing: Once the printing is complete, the final object might require support removal and additional finishing touches, depending on the material and application.
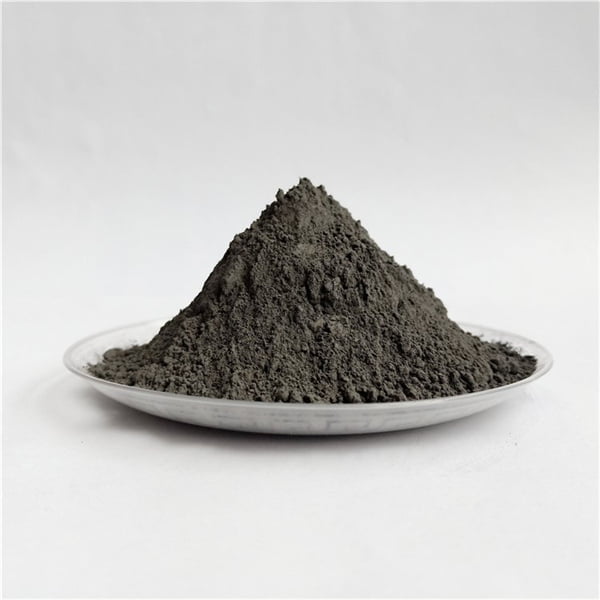
Advantages of Material Jetting
Material jetting isn’t just another pretty face in the 3D printing world. It boasts a unique set of advantages that make it a compelling choice for a wide range of applications. Let’s delve into some of its key benefits:
- Unmatched Precision and Detail: Material jetting produces parts with exceptional surface quality and fine feature resolution. Imagine printing miniature gears with intricate teeth or detailed anatomical models – material jetting handles these challenges with remarkable finesse.
- Multi-Material Capabilities: Unlike many 3D printing methods, material jetting allows the use of multiple materials within a single build. This opens doors to creating objects with varying properties, like rigid and flexible sections within the same part. Think of a phone case with a soft, grippy edge and a hard, impact-resistant back – material jetting can make it happen.
- High Color Fidelity: Material jetting isn’t just about greyscale; it can produce vibrant and photorealistic colors. This makes it ideal for prototyping products with specific color requirements, creating eye-catching marketing models, or even producing realistic architectural models.
- Broad Material Range: From rigid engineering plastics to flexible elastomers, material jetting offers a diverse selection of materials to cater to various functional needs. This allows designers and engineers to choose the perfect material for the job, ensuring optimal performance in the final product.
- Fast Turnarounds: Compared to some AM techniques, material jetting can offer relatively faster printing times. This is particularly beneficial for rapid prototyping iterations and getting products to market quicker.
Remember, no technology is perfect. While material jetting shines in many areas, it also has some limitations to consider.
Applications of Material Jetting
The versatility of material jetting makes it a valuable tool across various industries. Here are some prominent applications where this technology demonstrates its prowess:
- Prototyping: The ability to create high-fidelity prototypes with intricate details and multi-material capabilities makes material jetting a favorite for product designers and engineers. This allows for rapid testing and refinement of design concepts before committing to full-scale production.
- Medical Prototyping: The ability to produce biocompatible models with fine detail makes material jetting ideal for creating medical prototypes, such as anatomical models for surgical planning or customized prosthetics.
- Jewelry and Design: The high-resolution printing and multi-material capabilities of material jetting open doors for creating intricate jewelry pieces, design prototypes, and even lost-wax casting patterns.
- Functional Prototyping: Material jetting allows for the creation of functional prototypes with properties similar to the final product. This enables testing of form, fit, and function in a pre-production stage.
- End-Use Parts: In some cases, material jetting can be used to directly manufacture end-use parts, particularly for low-volume production runs or applications requiring high precision and unique material properties. This eliminates the need for traditional manufacturing techniques and their associated tooling costs.
Beyond these core applications, material jetting is also finding its way into other exciting areas, such as:
- Microfluidics: The ability to print with high resolution and multi-materials makes material jetting suitable for creating microfluidic devices used in medical diagnostics, lab-on-a-chip applications, and inkjet printing technology.
- Dental Applications: Material jetting is being explored for creating custom dental crowns, bridges, and even surgical guides with biocompatible materials.
As material jetting technology continues to evolve, we can expect to see even more innovative applications emerge in the future.
Exploring Metal Powders for Material Jetting
While the discussion so far has focused on photopolymer resins, material jetting isn’t limited to just plastics. A fascinating development in this technology is the use of metal powders to create intricate metal parts directly from a 3D model. Here, we’ll delve into some of the metal powder options used in material jetting:
1. Stainless Steel 316L: This versatile and biocompatible steel is a popular choice for applications requiring strength, corrosion resistance, and biocompatibility. It’s commonly used in medical implants, aerospace components, and functional prototypes.
2. Inconel 625: Known for its high-temperature strength and oxidation resistance, Inconel 625 is ideal for jetting parts for use in harsh environments, such as jet engines, turbine blades, and components exposed to extreme heat.
3. Titanium 6Al-4V: This lightweight and high-strength titanium alloy finds favor in aerospace, automotive, and medical applications. It offers a good balance of strength, weight, and biocompatibility, making it suitable for jetting aircraft parts, prosthetics, and surgical instruments.
4. Kovar: This iron-nickel-cobalt alloy boasts excellent thermal expansion properties that closely match those of glass. This makes it ideal for creating glass-to-metal seals used in electronics, lighting, and scientific instruments.
5. Nickel Alloy 718: Offering exceptional strength and high-temperature capabilities, Nickel Alloy 718 is a premium metal powder used for jetting parts in demanding applications like aerospace components, mold tooling, and parts exposed to significant stress.
6. Copper: The high electrical conductivity of copper makes it suitable for creating electrical components, heat exchangers, and antennas using material jetting.
7. Gold: Beyond its aesthetic appeal, gold offers excellent electrical conductivity and corrosion resistance. This makes it valuable for jetting electrical contacts, connectors, and components for the electronics industry.
8. Silver: Similar to copper, silver boasts high electrical conductivity and thermal conductivity. This makes it a valuable material for jetting electrical components, heat sinks, and even RFID tags.
9. Multi-Material Metal Powders: The future of material jetting is brimming with possibilities, including the development of multi-material metal powders. Imagine jetting a part with sections of different metals, each chosen for its specific properties – this opens doors for creating complex functional components with tailored performance.
10. Exotic and Experimental Metal Powders: Research is ongoing in the exploration of even more exotic and experimental metal powders for material jetting. This includes materials like tungsten for its high density and melting point, or even precious metals like platinum for its exceptional chemical resistance.
It’s important to note that the availability and specific properties of metal powders for material jetting can vary depending on the manufacturer. However, this list provides a glimpse into the exciting possibilities this technology offers for creating intricate and functional metal parts.
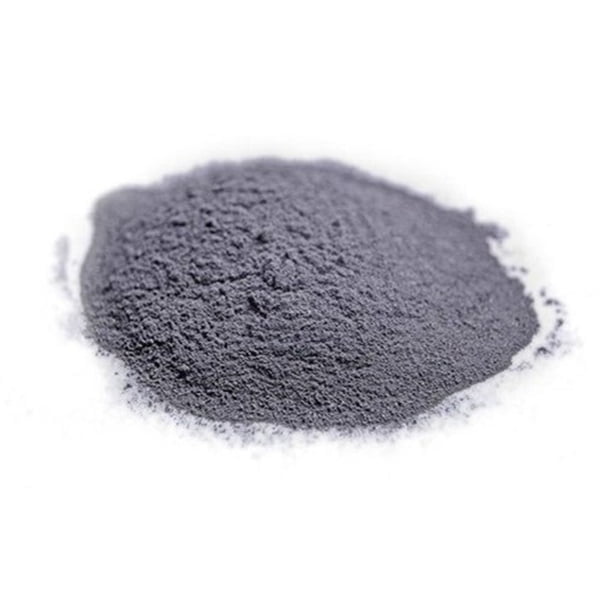
Pros and Cons of Material Jetting
We’ve explored the advantages and applications of material jetting, but like any technology, it has its own set of pros and cons to consider. Here’s a breakdown to help you decide if material jetting is the right fit for your needs:
Pros:
- Unmatched Precision and Detail: Creates parts with exceptional surface quality and fine features, ideal for intricate designs.
- Multi-Material Capabilities: Allows for the use of multiple materials within a single build, enabling objects with varying properties.
- High Color Fidelity: Produces vibrant and photorealistic colors, perfect for prototypes and design models.
- Broad Material Range: Offers a diverse selection of materials to cater to various functional needs.
- Fast Turnarounds: Provides relatively faster printing times compared to some AM techniques.
Cons:
- Limited Build Volume: Build volumes for material jetting systems can be smaller compared to some other AM technologies. This might limit the size of parts you can produce.
- Material Cost: Material jetting can involve higher material costs compared to some AM methods, particularly when using specialty materials or metal powders.
- Post-Processing: Depending on the material and application, post-processing steps like support removal and finishing might be required, adding time and potentially increasing costs.
- Support Structures: Material jetting often relies on support structures to build complex geometries. These supports need to be removed after printing, which can leave marks or require additional finishing.
Overall, material jetting is a powerful AM technology that excels in creating high-precision, multi-material parts with exceptional detail. However, it’s crucial to consider the limitations of build volume, material costs, and post-processing requirements when evaluating its suitability for your project.
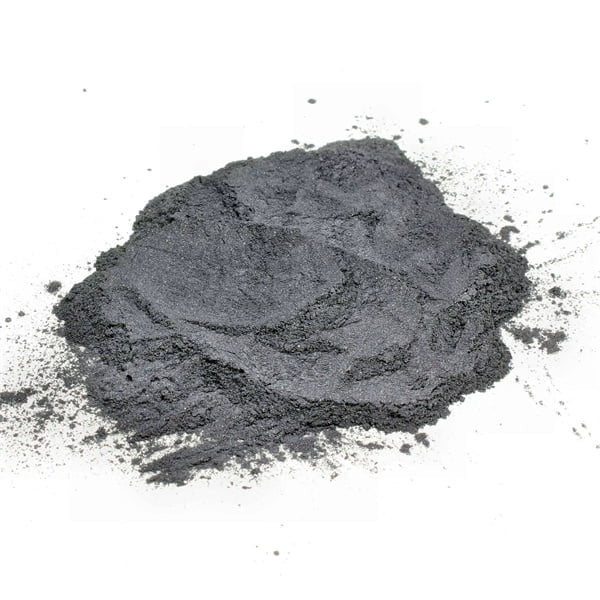
FAQ
Here are some frequently asked questions about material jetting to shed some light on this fascinating technology:
Question | Answer |
---|---|
What are the different types of material jetting systems? | There are two main types of material jetting systems: photopolymer jetting and metal jetting. Photopolymer jetting uses liquid resins, while metal jetting utilizes metal powders. |
What is the difference between material jetting and other 3D printing methods? | Material jetting offers superior resolution and detail compared to many other AM techniques. Additionally, its multi-material capabilities and ability to produce high-fidelity colors set it apart. |
What software is used for material jetting? | The process typically involves 3D modeling software to create the initial design and specialized slicing software to prepare the model for material jetting. |
Is material jetting suitable for mass production? | While material jetting is becoming faster, it’s generally not considered ideal for mass production due to factors like material costs and limited build volume. However, it excels in prototyping, low-volume production runs, and applications requiring high precision. |
What are the future prospects of material jetting? | The future of material jetting is bright! Advancements in materials, multi-material capabilities, and even larger build volumes are on the horizon. This technology has the potential to revolutionize how we design, prototype, and manufacture a wide range of products. |
By understanding the potential and limitations of material jetting, you can determine if this innovative AM technology is the perfect tool to bring your next project to life.
I hope this comprehensive exploration of material jetting has equipped you with valuable insights into this remarkable 3D printing technology. If you have any further questions, feel free to delve deeper into the resources available online or consult with a material jetting expert. Remember, the world of 3D printing is constantly evolving, and material jetting stands poised to play a pivotal role in shaping the future of manufacturing and design.
Share On
MET3DP Technology Co., LTD is a leading provider of additive manufacturing solutions headquartered in Qingdao, China. Our company specializes in 3D printing equipment and high-performance metal powders for industrial applications.
Inquiry to get best price and customized Solution for your business!
Related Articles
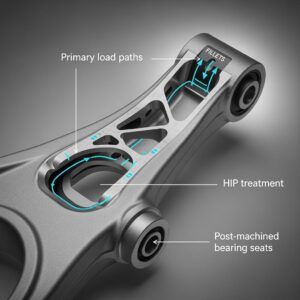
Metal 3D Printing for U.S. Automotive Lightweight Structural Brackets and Suspension Components
Read More »About Met3DP
Recent Update
Our Product
CONTACT US
Any questions? Send us message now! We’ll serve your request with a whole team after receiving your message.