Metal 3D Printing for Car Engines in Detroit: A Game-Changer for Automotive Manufacturing
Table of Contents
1. Introduction: The Role of Metal 3D Printing in Automotive Manufacturing
Metal 3D printing is revolutionizing the way automotive manufacturers design and produce car engine components. Traditionally, car engines were manufactured using expensive casting and machining processes, requiring long lead times and high material waste. However, with the advent of additive manufacturing (AM), companies can now create complex, high-performance engine parts with reduced costs and improved efficiency.
Benefits of Metal 3D Printing for Car Engines
✅ Lightweight Design: 3D printing allows for intricate lattice structures, reducing weight without compromising strength.
✅ Enhanced Performance: Engine components can be optimized for better airflow and heat resistance.
✅ Faster Prototyping: AM significantly reduces the time needed to develop and test new engine designs.
✅ Cost Savings: Less material waste and fewer production steps lead to lower overall manufacturing costs.
✅ Customization: Custom engine parts can be produced on demand, accommodating unique designs and performance needs.
Detroit, known as the Motor City, is at the forefront of this transformation, with leading automotive companies investing heavily in metal 3D printing technologies.
2. Market Trends: Why Detroit is Leading in 3D Printing for Car Engines
Detroit is home to many of the world’s largest automotive manufacturers, including General Motors, Ford, and Stellantis, all of which are actively adopting 3D printing for car engine production. The region has become a hub for automotive additive manufacturing, thanks to its strong industrial base and access to cutting-edge research institutions.
Key Market Trends in Detroit
Trend | Impact on Automotive Manufacturing |
---|---|
Increased Adoption of Metal AM | Auto companies are integrating 3D printing into engine production lines to reduce lead times. |
Advancements in Metal Powders | High-performance superalloys and titanium powders enable stronger, heat-resistant engine components. |
Sustainability Focus | 3D printing cuts material waste and improves fuel efficiency by reducing engine weight. |
Collaborations with Tech Startups | Detroit automakers are partnering with AM specialists to accelerate innovation. |
Expansion of 3D Printing Facilities | Increased investment in AM production centers across the region. |
The growing demand for efficient, lightweight, and high-performance engines is pushing Detroit-based manufacturers to explore new metal 3D printing solutions.
Key Metal 3D Printing Technologies Used in Detroit
- Selective Electron Beam Melting (SEBM): Ideal for high-strength titanium and nickel-based alloys.
- Laser Powder Bed Fusion (LPBF): Offers precision and excellent material properties for engine components.
- Direct Energy Deposition (DED): Used for repairing and enhancing existing engine parts.
For manufacturers looking to stay ahead, investing in high-quality metal powders and advanced printing systems is essential. Metal3DP offers state-of-the-art metal powder solutions and high-precision 3D printing technology tailored for automotive applications.
3. Key Factors to Consider When Choosing a Metal 3D Printing Supplier
When selecting a metal 3D printing supplier for car engine components, automotive manufacturers must evaluate several critical factors:
1. Quality of Metal Powders
The strength and durability of printed engine parts depend on the quality of the metal powder used. Suppliers like Metal3DP provide high-purity powders such as titanium alloys, nickel-based superalloys, and stainless steel, optimized for automotive applications.
2. Printing Technology Capabilities
Different 3D printing methods offer varying levels of precision, strength, and material compatibility. Ensure the supplier has expertise in LPBF, SEBM, and DED technologies, which are commonly used for high-performance engine components.
3. Production Capacity & Lead Times
For large-scale automotive manufacturing, a supplier must offer consistent production capabilities and fast turnaround times. Look for companies with industrial-grade 3D printers and efficient supply chains.
4. Cost Efficiency
While metal 3D printing can be cost-effective, pricing varies depending on material selection, print complexity, and post-processing requirements. Choose a supplier that provides competitive pricing without compromising on quality and performance.
5. Industry Certifications & Compliance
Automotive engine components must meet strict safety and performance standards. Ensure the supplier complies with ISO 9001, AS9100 (for aerospace-grade parts), and IATF 16949 (automotive quality management standards).
6. Post-Processing & Finishing Services
3D printed metal parts often require heat treatment, surface finishing, and machining to meet final specifications. A full-service supplier should offer post-processing capabilities to enhance the quality and performance of printed parts.
7. Customer Support & Technical Expertise
A reliable supplier should provide technical consulting, material recommendations, and prototyping support to help manufacturers optimize their engine designs for 3D printing.
Key Supplier Evaluation Criteria | Importance |
---|---|
Metal Powder Quality | High |
Advanced Printing Technologies | High |
Production Capacity | Medium to High |
Cost Efficiency | Medium |
Certifications & Compliance | High |
Post-Processing Services | Medium to High |
Customer Support & Expertise | High |
By partnering with a trusted metal 3D printing supplier, automotive manufacturers can ensure high-quality, high-performance engine components while reducing production costs and lead times.
For top-tier metal powders and advanced 3D printing solutions, Metal3DP is a leading provider of automotive-grade additive manufacturing materials and equipment.
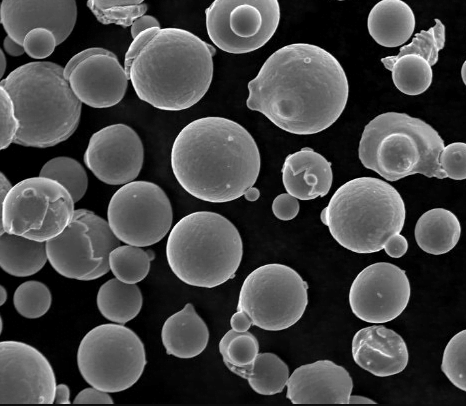
4. Top Metal 3D Printing Suppliers for Car Engines in Detroit
Detroit is home to several leading metal 3D printing suppliers specializing in automotive engine components. These companies provide high-quality metal powders, advanced additive manufacturing technologies, and post-processing services.
Top Metal 3D Printing Suppliers in Detroit
Company Name | Specialization | Key Strengths |
---|---|---|
EOS North America | Laser Powder Bed Fusion (LPBF) | High-precision printing for automotive and aerospace applications |
3D Systems | DMP (Direct Metal Printing) | Offers scalable solutions for engine components |
GE Additive | Electron Beam Melting (EBM) & LPBF | Advanced metal powders and industrial-grade printers |
Stratasys | Multi-Material 3D Printing | Strong focus on prototyping and low-volume production |
Metal3DP | SEBM & High-Performance Metal Powders | Industry-leading metal powders and full-service AM solutions |
Among these suppliers, Metal3DP stands out due to its high-quality metal powders, advanced Selective Electron Beam Melting (SEBM) technology, and comprehensive additive manufacturing solutions tailored for automotive engine production.
5. Why More Automotive Manufacturers Are Turning to Metal 3D Printing
The automotive industry is undergoing a major transformation, with 3D printing becoming a standard process for manufacturing high-performance engine components.
Key Reasons Why Automakers Are Adopting Metal 3D Printing
1. Weight Reduction for Improved Fuel Efficiency
- Lightweight titanium and aluminum alloys reduce overall engine weight.
- Lattice structures and topology optimization enhance fuel efficiency.
2. Faster Prototyping and Design Iterations
- Traditional casting and machining take weeks, while 3D printing reduces lead times to days.
- Engineers can rapidly test and refine new engine designs without high tooling costs.
3. Enhanced Performance and Durability
- 3D printed metal parts offer higher strength, heat resistance, and wear resistance.
- Materials like nickel-based superalloys improve engine efficiency and longevity.
4. Cost Savings in Production & Material Waste
- Additive manufacturing uses only the required materials, reducing waste.
- Eliminates the need for expensive molds and traditional tooling.
5. Supply Chain Flexibility & On-Demand Manufacturing
- Reduces dependency on overseas suppliers, improving local production capabilities.
- Spare parts can be printed on demand, reducing inventory costs.
Key Benefit | Impact on Car Engine Manufacturing |
---|---|
Lightweight Materials | Increased fuel efficiency and lower emissions |
Faster Prototyping | Accelerated engine development cycles |
Higher Strength Components | Enhanced durability and heat resistance |
Cost Reduction | Lower material waste and production costs |
On-Demand Production | Reduced supply chain risks and inventory needs |
Detroit-based companies like Ford, GM, and Stellantis are investing heavily in metal 3D printing technologies to gain a competitive edge in next-generation automotive manufacturing.
6. Why Choose Metal3DP for Your Car Engine 3D Printing Needs
Metal3DP is a leading provider of metal additive manufacturing solutions, offering high-performance metal powders and industrial-grade 3D printing systems for automotive, aerospace, and medical applications.
Key Advantages of Metal3DP for Car Engine 3D Printing
1. Industry-Leading Metal Powders
- Offers a wide range of high-performance alloys:
- Titanium Alloys (Ti6Al4V, TiAl) → Ideal for lightweight, high-strength engine components.
- Nickel-Based Superalloys (Inconel 718, Inconel 625) → Excellent heat resistance for turbochargers and exhaust systems.
- Stainless Steels (316L, 17-4PH) → Strong, corrosion-resistant materials for engine housings.
2. Advanced 3D Printing Technologies
- Selective Electron Beam Melting (SEBM):
- Produces high-density, defect-free metal parts.
- Ideal for complex automotive engine components requiring superior mechanical properties.
- Reduces post-processing time compared to LPBF.
3. High Accuracy & Reliability
- Metal3DP’s 3D printers offer industry-leading precision, ensuring tight tolerances for engine blocks, pistons, and turbocharger components.
4. Comprehensive Solutions: From Powder to Finished Parts
- Metal3DP provides end-to-end additive manufacturing services, including:
✅ Metal Powder Production → High-quality, spherical powders for AM applications.
✅ 3D Printing Services → Custom automotive engine components.
✅ Post-Processing & Finishing → Heat treatment, machining, and surface finishing.
5. Trusted by Leading Automotive Manufacturers
- Metal3DP has worked with global automotive and aerospace companies, helping them integrate metal 3D printing into their manufacturing processes.
Key Metal3DP Advantage | Benefit for Automotive Manufacturing |
---|---|
High-Quality Metal Powders | Stronger, more reliable engine components |
Advanced SEBM Technology | High-density, defect-free metal parts |
Comprehensive AM Solutions | From powder production to finished components |
Industry Expertise | Trusted by leading automotive manufacturers |
For automotive companies in Detroit looking to leverage the power of metal 3D printing, Metal3DP is the ideal partner to deliver high-quality, cost-effective, and high-performance engine components.
7. How to Order High-Quality Metal 3D Printing for Car Engine Parts
Ordering high-performance metal 3D printed engine components requires careful consideration of materials, printing technology, and post-processing requirements. Here’s a step-by-step guide to ensure a seamless ordering process:
Step 1: Define Your Requirements
Before placing an order, determine the following:
- Component Type: Engine block, pistons, turbocharger housing, exhaust manifold, etc.
- Material Selection: Titanium, nickel-based superalloys, stainless steel, or aluminum alloys.
- Printing Method: Selective Electron Beam Melting (SEBM) for high-strength components or Laser Powder Bed Fusion (LPBF) for precision parts.
- Quantity & Lead Time: Small-batch production or large-scale manufacturing.
Step 2: Choose a Trusted Supplier
Selecting a reliable metal 3D printing provider is crucial. Metal3DP offers:
✅ High-quality metal powders optimized for automotive applications.
✅ Advanced printing technologies for superior mechanical properties.
✅ Comprehensive post-processing services to meet final specifications.
Step 3: Submit a Request for Quotation (RFQ)
- Provide CAD files or technical drawings of your engine component.
- Specify material, surface finish, and dimensional tolerances.
- Request a cost estimate and lead time.
Step 4: Prototyping & Testing
- A prototype is printed for performance testing and validation.
- Engineers can refine the design before full-scale production.
Step 5: Full-Scale Production & Delivery
Once the design is finalized:
- Batch production begins using industrial-grade 3D printers.
- Components undergo quality control, heat treatment, and finishing.
- Final parts are inspected and shipped to the customer.
Ordering Process Step | Key Considerations |
---|---|
Define Requirements | Material, printing method, and quantity |
Select Supplier | Expertise, technology, and reliability |
Request Quotation | CAD file submission and pricing |
Prototype & Testing | Design validation and performance testing |
Full-Scale Production | Quality control and delivery |
For a seamless ordering experience, Metal3DP provides custom consultation and end-to-end additive manufacturing solutions.
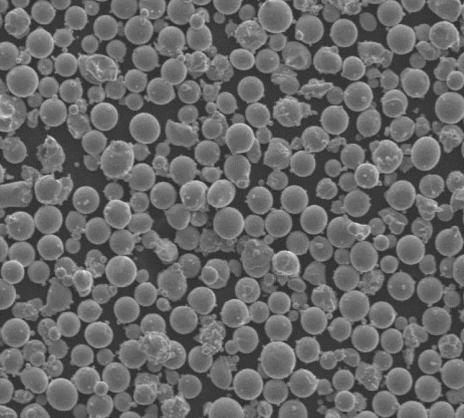
8. Case Studies: Successful Applications of 3D Printed Car Engine Components
Case Study 1: 3D Printed Turbocharger for High-Performance Vehicles
Challenge:
A leading Detroit-based automaker needed a lightweight, high-temperature-resistant turbocharger to improve engine efficiency.
Solution:
- Used Nickel-based Inconel 718 superalloy for heat resistance and durability.
- Printed with Selective Electron Beam Melting (SEBM) for high-density, defect-free parts.
- Optimized internal cooling channels using complex lattice structures.
Results:
✅ 30% weight reduction → Improved fuel efficiency.
✅ Increased durability → Higher resistance to extreme temperatures.
✅ Faster production time → Reduced lead time from 6 months to 3 weeks.
Case Study 2: Lightweight Titanium Pistons for Racing Engines
Challenge:
A performance racing team sought ultra-lightweight pistons to enhance engine efficiency.
Solution:
- Used Titanium Ti-6Al-4V alloy for lightweight, high-strength properties.
- Printed using Laser Powder Bed Fusion (LPBF) for precise control over piston dimensions.
- Implemented hollow structures to reduce weight without compromising strength.
Results:
✅ 40% weight reduction → Improved acceleration and fuel efficiency.
✅ Enhanced durability → Increased resistance to high-speed engine stress.
✅ Customization → Ability to fine-tune piston shape for performance optimization.
Case Study 3: On-Demand Production of Spare Engine Parts
Challenge:
A Detroit-based truck manufacturer faced supply chain delays for critical engine components.
Solution:
- Used stainless steel 316L for corrosion-resistant, durable parts.
- Printed engine components on demand, eliminating inventory costs.
Results:
✅ Reduced supply chain dependency → Faster access to parts.
✅ Lower costs → No need for large spare part inventories.
✅ Increased uptime → Faster repairs and maintenance.
Metal3DP has successfully helped automotive manufacturers implement metal 3D printing for engine components, reducing costs and improving performance.
9. FAQs: Common Questions About Metal 3D Printing for Car Engines
Q1: What materials are best for 3D printing car engine components?
The best materials depend on the engine part:
- Titanium (Ti-6Al-4V) → Lightweight pistons, valves.
- Nickel-based superalloys (Inconel 718, 625) → Turbochargers, exhaust manifolds.
- Stainless steel (316L, 17-4PH) → Engine housings, brackets.
Q2: Is metal 3D printing cost-effective for automotive manufacturing?
Yes! While initial setup costs may be higher, benefits include:
✅ Lower material waste.
✅ Faster prototyping & production.
✅ On-demand manufacturing without expensive tooling.
Q3: How strong are 3D printed metal engine parts?
Metal 3D printed parts can be as strong or stronger than traditionally machined components, especially when using high-performance alloys like titanium and Inconel.
Q4: Can 3D printing replace traditional casting for engine components?
Yes, for low to medium-volume production, 3D printing offers better flexibility, weight reduction, and performance optimization. However, casting may still be used for large-scale production.
Q5: How long does it take to produce a 3D printed engine component?
- Prototyping: ~1-2 weeks.
- Full-scale production: 3-6 weeks, depending on complexity.
- Traditional manufacturing: ~3-6 months (longer lead times).
Q6: Where can I order high-quality 3D printed car engine parts?
Metal3DP offers end-to-end solutions for automotive manufacturers looking for high-performance, cost-effective 3D printed engine components.
Conclusion: The Future of Metal 3D Printing in Detroit’s Automotive Industry
Metal 3D printing is revolutionizing car engine manufacturing, offering lighter, stronger, and more efficient components. Detroit’s leading automakers are rapidly adopting additive manufacturing to stay ahead in the competitive automotive industry.
Why Choose Metal3DP?
🚀 Industry-leading metal powders & 3D printing solutions.
🚀 Advanced Selective Electron Beam Melting (SEBM) for high-performance engine components.
🚀 Trusted by top automotive manufacturers.
🚀 End-to-end solutions → From material selection to final part production.
🔗 Explore Metal3DP’s metal 3D printing solutions today to revolutionize your engine manufacturing process!
This concludes our comprehensive guide on metal 3D printing for car engines in Detroit. Ready to integrate additive manufacturing into your automotive production? Contact Metal3DP today for a custom consultation!
Share On
MET3DP Technology Co., LTD is a leading provider of additive manufacturing solutions headquartered in Qingdao, China. Our company specializes in 3D printing equipment and high-performance metal powders for industrial applications.
Inquiry to get best price and customized Solution for your business!
Related Articles
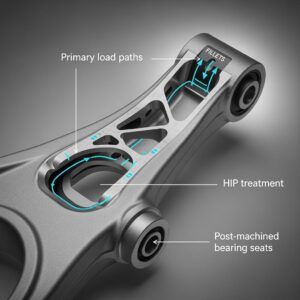
Metal 3D Printing for U.S. Automotive Lightweight Structural Brackets and Suspension Components
Read More »About Met3DP
Recent Update
Our Product
CONTACT US
Any questions? Send us message now! We’ll serve your request with a whole team after receiving your message.