Metal Additive Manufacturing: A Comprehensive Guide
Table of Contents
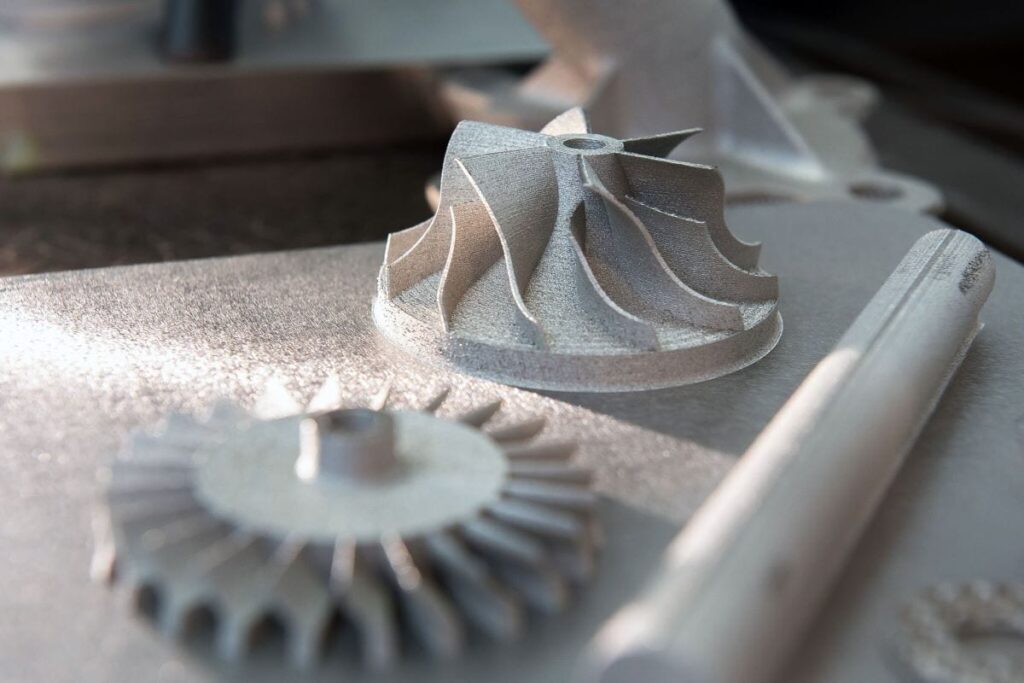
Overview of Metal Additive Manufacturing
Metal additive manufacturing, also known as metal 3D printing, is a transformative technology for rapidly producing metal parts directly from 3D model data. In contrast to subtractive manufacturing methods like CNC machining that remove material, additive manufacturing builds up components layer-by-layer using metals like stainless steel, aluminum, titanium, nickel alloys, and more.
Compared to traditional manufacturing, metal AM enables greater design freedom, customization, and optimization that can reduce weight, material usage, and lead times. Parts can be consolidated into one piece, embedded with conformal cooling channels, or designed with organic shapes not possible with casting or machining. Metal 3D printing brings new potential for innovation across industries like aerospace, medical, automotive, and energy.
This comprehensive guide provides technical details on the various metal AM processes, materials, applications, benefits, and limitations. Key information is presented in easy-to-compare tables to highlight the capabilities and trade-offs of different metal 3D printing technologies. Read on for an in-depth look at how additive manufacturing is revolutionizing metal fabrication.
Main Highlights of Metal Additive Manufacturing:
- Produces fully dense, end-use metal parts from digital 3D CAD models
- Adds material layer-by-layer unlike subtractive methods like machining
- Enables complex, optimized geometries not possible with casting or machining
- Reduces waste, energy use, and lead times versus traditional techniques
- Facilitates rapid prototyping as well as direct part production
- Expanding applications across aerospace, medical, automotive, and other sectors
Types of Metal Additive Manufacturing Processes
There are several approaches to printing metal parts additively. The main metal AM process categories include powder bed fusion, directed energy deposition, binder jetting, and sheet lamination. Each has unique capabilities in terms of materials, accuracy, costs, and more.
Table 1: Overview of Major Metal Additive Manufacturing Processes
Process | Description | Materials | Accuracy | Post-Processing |
---|---|---|---|---|
Powder Bed Fusion | Uses thermal energy to selectively fuse regions of a powder bed. Includes selective laser melting (SLM), direct metal laser sintering (DMLS), and electron beam melting (EBM). | Aluminum, steel, titanium, nickel alloys | High, ± 0.1-0.2mm | Some machining and heat treatment |
Directed Energy Deposition | Focuses thermal energy to fuse materials by melting feedstock as it is being deposited. Includes laser engineered net shaping (LENS) and laser metal deposition (LMD). | Aluminum, steel, titanium, cobalt-chrome | Medium, ± 0.5mm | More machining and finishing |
Binder Jetting | Liquid bonding agent selectively joins powder material layers together. Parts are sintered after printing. | Stainless steel, some alloys | Low, ± 2mm | Requires debinding, sintering and infiltration |
Sheet Lamination | Layers of sheet metal are bonded to shape parts and then trimmed using lasers or CNC machining. | Aluminum, steel, titanium | Medium, ± 0.5mm | Laser cutting or CNC machining after lamination |
Powder bed fusion techniques like selective laser melting (SLM) and electron beam melting (EBM) are currently the most widely used metal AM processes. They offer high resolution on par with machining, good material properties, and a broad range of metals from stainless steels to nickel-based alloys. The raw material is a fine metal powder that is spread in layers and selectively melted by a focused heat source in a controlled atmosphere chamber.
Directed energy deposition methods like laser engineered net shaping (LENS) focus a melt pool onto a substrate, adding material continuously. This allows larger sized parts to be built up by depositing melted powder or wire feedstock. Resolution is lower but build size is not limited like powder bed methods. Less post-processing is required but surface finish is poorer.
Binder jetting uses liquid binding agent to join layers of metal powder together. The resulting “green” parts must then be sintered and infiltrated with copper or bronze to achieve full density. Though material options are currently limited, binder jetting can produce large numbers of small intricate metal parts more affordably.
Sheet lamination bonds thin layers of sheet metal together using adhesive or welding. Lasers or CNC machining then cut the stack into a 3D shape. It provides good accuracy but has geometry limitations based on the sheet thickness.
Each process has its advantages and best fit applications. Choosing the right metal AM technology depends on factors like material requirements, precision, surface finish, batch size, and cost.
Materials for Metal Additive Manufacturing
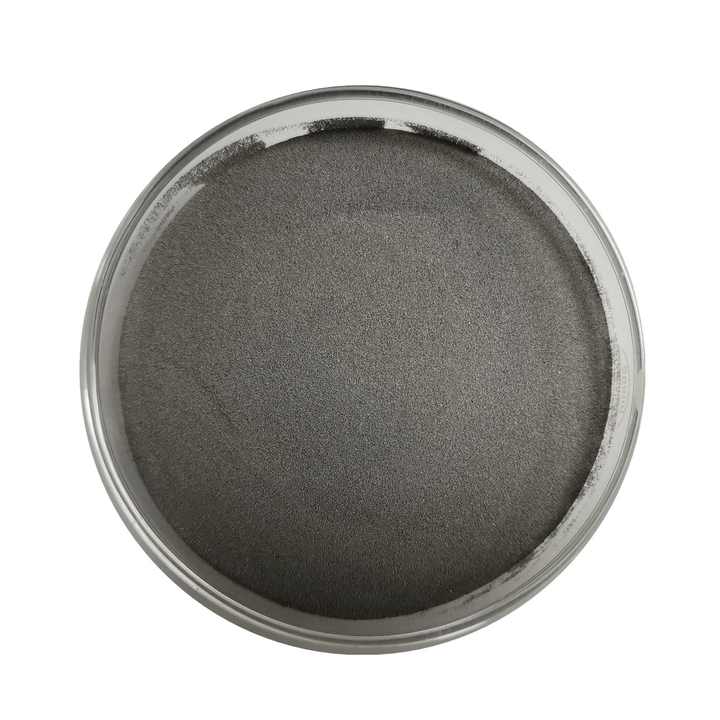
A wide range of metals from stainless steel to superalloys can be printed using powder bed fusion, directed energy deposition, binder jetting, and sheet lamination methods. The most commonly used metal AM materials include:
Table 2: Common Metal Additive Manufacturing Materials
Material | Processes | Properties | Applications |
---|---|---|---|
Stainless Steel | PBF, BJ | High strength, corrosion resistance | Aerospace, automotive, medical |
Aluminum Alloys | PBF, DED | Lightweight, good thermal conductivity | Automotive, aerospace |
Titanium Alloys | PBF, DED | High strength-to-weight ratio | Aerospace, medical implants |
Nickel Alloys | PBF | Heat and corrosion resistance | Aerospace, energy |
Cobalt Chrome | DED | Biocompatibility, wear resistance | Medical implants, tooling |
Tool Steel | PBF, BJ | High hardness, thermal stability | Tooling, molds, dies |
Stainless steels like 316L and 17-4PH are widely used across industries thanks to their strength, corrosion resistance, and relative ease of printing and post-processing.
Aluminum alloys like AlSi10Mg enable lightweight aerospace and automotive parts that are difficult to machine or cast.
Titanium alloys like Ti64 possess a high strength-to-weight ratio ideal for structural components along with biocompatibility.
Nickel superalloy powder such as Inconel 718 and 625 have excellent mechanical properties at high temperatures for demanding applications.
Cobalt chrome alloy powder boast high stiffness, biocompatibility and wear resistance suited for medical implants and tooling.
Tool steels including H13, D2, and Maraging Steel offer very high hardness, strength, and thermal stability for tooling like injection molds or forging dies.
R&D efforts are expanding the roster of metals compatible with AM processes. More exotic alloys like precious gold or platinum are also being adopted for specialized applications like jewelry or electronics.
Metal Additive Manufacturing Specifications
Key factors that define the capabilities of any metal AM machine are build volume, layer resolution, precision, and materials supported. Requirements like accuracy, surface finish, and heat treatment will depend on the specific application.
Table 3: Metal AM Equipment Specifications and Capabilities
Parameter | Typical Specification |
---|---|
Build Volume | 50-500mm x 50-500mm x 50-500mm |
Layer Thickness | 20-100 microns |
Precision | ±0.1-0.2mm for PBF, ±0.5mm for DED |
Surface Finish | Ra 10-25 microns, Rz 20-100 microns |
Materials | Stainless steels, aluminum alloys, titanium alloys, tool steels, nickel alloys |
Process Environment | Vacuum or inert argon atmosphere |
Supports Needed | Yes, removed post-process |
Heat Treatment | Stress relief, solution annealing, aging |
Build volume for most powder bed and directed energy systems ranges from a few cubic inches up to approximately one cubic foot. Larger equipment is available for binder jetting or sheet lamination processes.
Layer thickness during the build process can be varied from 20-100 microns for fine resolution on the order of a machinist’s finish. Thinner layers improve surface finish but also increase build time.
Precision attainable is ±0.1-0.2mm for powder bed fusion and ±0.5mm for directed energy deposition depending on the specific AM machine used.
Achievable surface finish in the as-built state ranges from 10-25 microns (Ra) and 20-100 microns (Rz) but will require post-processing like abrasive finishing to improve.
Virtually any metallic alloy from stainless steels to titanium and nickel alloys can be printed, with material choices doubling in recent years.
Suppliers of Metal Additive Manufacturing Equipment
A range of companies provide industrial metal AM systems as well as printing services. The leading vendors offering powder bed fusion, directed energy deposition, binder jetting, and sheet lamination equipment include:
Table 4: Major Suppliers of Metal Additive Manufacturing Systems
Company | AM Process | Metals | Build Volume | Cost Range |
---|---|---|---|---|
EOS | Powder bed fusion (DMLS) | Al, Ti, Ni alloys | 250 x 250 x 325 mm | $150,000-$1,000,000 |
SLM Solutions | Powder bed fusion (SLM) | Al, Ti, tool steel | 250 x 250 x 300 mm | $200,000-$1,000,000 |
HP | Binder jetting | Stainless steel | 380 x 285 x 380 mm | $100,000-$500,000 |
Desktop Metal | Binder jetting | Stainless steel, alloy steels | 160 x 160 x 250 mm | $100,000-$500,000 |
Sciaky | Directed energy deposition | Ti, Inconel, stainless | 1500 x 750 x 750 mm | $500,000-$2,500,000 |
Optomec | Directed energy deposition | Al, Ti, CoCr | 610 x 610 x 610 mm | $250,000-$750,000 |
Fabrisonic | Ultrasonic AM | Al, steel, Ti | 600 x 900 x 600 mm | $250,000-$500,000 |
German company EOS pioneered direct metal laser sintering (DMLS) technology and offers a wide range of industrial printers for metals like titanium, aluminum, and nickel alloys.
SLM Solutions also provides powder bed fusion equipment that can process steels, titanium, aluminum, and more metals with build volumes up to 500 cubic inches.
HP, Desktop Metal, and ExOne leverage binder jetting focused on high-volume production of small, complex stainless steel or alloy steel components.
Sciaky and Optomec supply directed energy deposition systems for large-scale metal printing using titanium, aluminum, and nickel superalloys.
Fabrisonic uses patented ultrasonic additive manufacturing able to embed wiring, sensors, and more inside metal parts.
Metal AM equipment typically ranges from $100,000 to $1 million+ in initial capital investment depending on production capacity, although prices are falling rapidly. Material costs vary widely based on the specific alloy used.
Metal Additive Manufacturing Applications
Metal additive manufacturing brings new design freedom and capabilities well-suited for aerospace, medical, automotive, and general industrial applications such as:
Aerospace: Lightweight brackets and complex structures, engine components with conformal cooling, and parts consolidation to reduce weight, material usage, and lead times
Medical: Customized orthopedic implants, surgical instruments with thin walls and lattice structures to improve osseointegration with bone, dental restorations
Automotive: Lightweight lattice structures, mass customization of components, tooling like jigs and fixtures to improve factory workflows
Industrial/Consumer: Lighting, furniture, sporting goods, and musical instruments leveraging organic shapes, mass customization and lightweight lattice structures
Tooling: Conformal cooling channels can be embedded into injection molds, dies, and tooling inserts to reduce cycle times. Quick turnaround of spare tooling parts.
Oil & Gas: Custom pipeline fittings, structural components like rigs and valve blocks for high pressure/corrosive environments.
The technology is also used for rapid tooling, fixtures, and prototyping in product development across many industries. Below are some examples of metal AM applications and benefits versus conventional manufacturing:
Table 5: Metal Additive Manufacturing Applications and Benefits
Application | Benefits vs Traditional Processes |
---|---|
Aircraft Brackets | Weight reduction, part consolidation |
Hip Implants | Customized shapes, accelerated design iterations |
Heat Exchangers | Complex internal channels improve heat transfer |
Injection Molds | Conformal cooling to reduce cycle times |
Automotive Parts | Mass customization, lightweight optimization |
Additive manufacturing empowers engineers with unprecedented design freedom to fabricate metal components not possible or economical with casting, machining, or other conventional manufacturing techniques.
Advantages and Disadvantages of Metal AM
Compared to subtractive fabrication and other traditional metal manufacturing methods, AM offers several key advantages but also limitations to consider:
Table 6: Metal Additive Manufacturing – Pros vs Cons
Advantages | Disadvantages |
---|---|
Design freedom, complex geometries | Small build volumes limit part sizes |
Weight reduction, material savings | Lower material properties than wrought metals |
Reduced lead times, tooling costs | Lower dimensional accuracy and surface finish |
Consolidated assemblies, embedded features | Higher equipment costs, material costs |
Mass customization, on-demand production | Post-processing often required |
Minimal material waste | Limited size and alloy availability |
Rapid prototyping, accelerated development | anisotropic properties of some printed materials |
The main benefits of metal AM are design freedom, part consolidation, customization, and faster product development cycles. Lightweighting and material savings are also possible for industries like aerospace and automotive.
However, the smaller build volumes, higher costs, and lack of material availability at commercial scale remain barriers versus traditional manufacturing. Most metal AM applications are best suited for low to mid production volumes where the benefits of customization and lead time reduction outweigh higher printed part costs today.
As metal AM equipment and material prices decline, production volumes and applications will continue expanding across more industries. With advancements in quality and larger build sizes, adoption will accelerate for high-volume manufacturing.
The Future of Metal Additive Manufacturing
While still an emerging technology, metal additive manufacturing is poised for significant growth in coming years. Expanding applications, new players, and increased adoption across supply chains will drive market expansion.
- The global metal AM market is projected to surpass $15 billion by 2028, more than doubling since 2021. Aerospace and medical sectors are anticipated to account for over 50% of demand.
- System manufacturers are developing larger build volume machines, multi-laser and higher productivity equipment focused on serial production applications.
- Expanded materials are becoming available beyond nickel superalloys including higher strength aluminum and steels, precious metals, magnesium, tool steel, and more.
- Quality and repeatability continue improving with advanced machine controls, software, and streamlined workflows to minimize trial and error.
- Supply chain optimization via AM is gaining traction across industries as lead times shrink and the technology becomes more cost effective for end-use components versus just prototyping.
- Customized, decentralized manufacturing could reduce supply chain risks and logistics costs. On-demand localized production will grow.
- Governments are investing significantly in industrial metal AM research, workforce development programs, and advancing regional manufacturing ecosystems around the technology.
While still maturing, metal additive has demonstrated clear benefits over conventional manufacturing across diverse applications from aerospace engines to patient-matched implants. As more stakeholders across supply chains adopt AM, it is positioned to transform manufacturing and enable a new era of design innovation.
Metal AM Frequently Asked Questions
Q: What materials are compatible with metal 3D printing?
A: Most industrial metals can be printed including stainless steels, aluminum alloys, titanium, tool steels, nickel superalloys, and more. Some processes also support precious metals like gold, silver, and platinum.
Q: How accurate is metal additive manufacturing?
A: Dimensional accuracy for most powder bed fusion processes is around ±0.1-0.2mm, similar to CNC machining. Directed energy deposition is ±0.5mm or more.
Q: Does metal AM require any post-processing?
A: Some post-processing like surface finishing and heat treatment is typically needed. Support structures are removed and the surface is machined, sanded, or chemically treated to smoothen and finish the parts.
Q: What are some advantages of metal AM over casting or machining?
A: Benefits include design freedom, lightweight structures, part consolidation, reduced tooling, faster lead times, mass customization, and more. AM enables optimized shapes not possible with subtractive techniques.
Q: What industries are driving adoption of metal 3D printing?
A: Aerospace, medical/dental, automotive, and industrial sectors are the largest adopters today. The technology is ideal for complex, low-volume production where customization and weight reduction are benefits.
Q: How expensive is metal AM compared to conventional manufacturing?
A: Printed metal parts remain more expensive for mass production. For small batch sizes under 1000 units, AM can be cost competitive and offset by the benefits of design flexibility, faster time-to-market, part consolidation, and customization.
Share On
MET3DP Technology Co., LTD is a leading provider of additive manufacturing solutions headquartered in Qingdao, China. Our company specializes in 3D printing equipment and high-performance metal powders for industrial applications.
Inquiry to get best price and customized Solution for your business!
Related Articles
About Met3DP
Recent Update
Our Product
CONTACT US
Any questions? Send us message now! We’ll serve your request with a whole team after receiving your message.
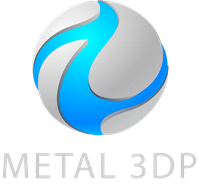
Metal Powders for 3D Printing and Additive Manufacturing