Metal Alloy Powder Material
Table of Contents
Metal alloy powders refer to fine particulate blends of metal elements that when consolidated create high performance components exploiting customized mechanical, thermal, electrical and corrosion properties unavailable in single metal forms. This guide details composition, production methods, characteristics, applications, specifications and comparisons for widely used nickel, aluminum, steel and titanium alloy powders.
Overview of Metal Alloy Powders
Alloying combines beneficial attributes of two or more metals – strength from one, corrosion resistance from another and high temperature stability from a third metal into a customized matrix engineered for targeted applications.
Pre-alloyed metal powders produced with properties like:
- Inherent high strength from precipitates
- Thermal stability retaining strength at high temperatures
- Oxidation and wear resistance for longevity
- Biological inertness for medical device safety
- Controlled particle size/shape aiding advanced manufacturing
- Consolidated into net shape components minimizing machining
Powder metallurgy technique facilitates large volume production of small precision parts supporting diverse industries.
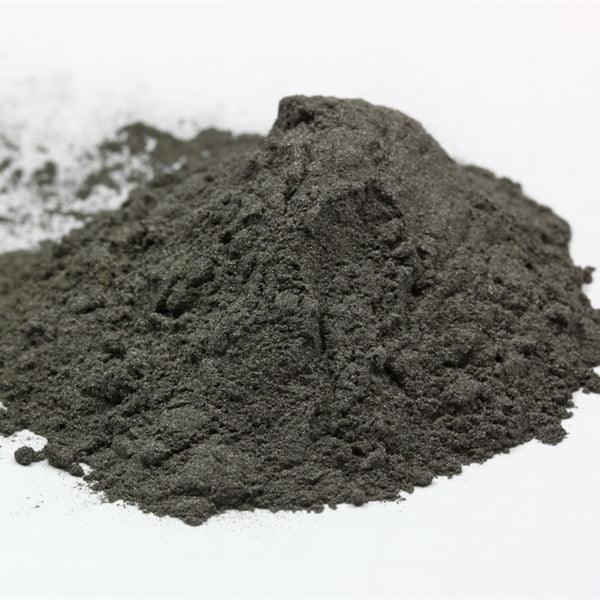
Types of Metal Alloy Powder Compositions
Widely used alloy powder variants include:
Table 1: Common metal alloy powder compositions and characteristics
Alloy | Elements | Properties Leveraged | Applications |
---|---|---|---|
Nickel alloys | Ni, Cr, Fe, Nb etc | Corrosion + heat resistance | Aerospace, marine hardware |
Aluminum alloys | Al, Cu, Mg, Si etc | Lightweight strength | Automotive parts, gears |
Tool steel alloys | Fe, Mo, Cr, V etc | Hardness retention at high temps | Extrusion dies, molds |
Titanium alloys | Ti, Al, V, Cu etc | Strength + biocompatibility | Surgical implants, aerospace |
Refractory alloys | W, Mo, Ta, Nb etc | Very high melting point | Military, space, nuclear |
Customized combinations of iron, aluminum and titanium with alloying elements like chromium, nickel, copper etc. help tweak galvanic compatibility, magnetism, conductivity for targeted product needs.
Key Production Methods for Alloy Powders
Table 2: Overview of leading commercial scale alloy powder production routes
Method | Process | Characteristics |
---|---|---|
Gas atomization | Inert gas breaks up molten metal stream into fine droplets | Spherical powders with smooth distribution |
Water atomization | High pressure water jet disintegrates metal melt | Irregular powder morphology |
Plasma atomization | Plasma arc melts feedstock into finer droplets | Very fine, spherical powders |
Mechanical alloying | Repeated cold welding and fracturing of powder feedstocks | Multiple alloys customized |
Electrolysis | Controllable stratified metal deposits from aqueous solutions | Porous irregular powders |
Gas atomization allows best impurity control suited for reactive alloy chemistries like titanium and aluminum grades. Water atomization offers higher throughputs for cost sensitive steel alloy volumes. Plasma atomization reaches sub 20 micron sizes.
Characteristics and Properties
Table 3: Typical properties exhibited by commercial metal alloy powders
Property | Characteristics |
---|---|
Composition | Custom alloying possible with >2 metals |
Particle size | 15-150 micron sizes typical |
Particle shape | Varies – spherical, irregular, dendritic |
Tap density | Alloys have higher tap density >3 g/cc aiding compaction |
Flow rates | Effects spreadability; >25 s/50 g assists layering |
Apparent density | Narrow distribution improves density consistency |
Compressibility | Alloys have higher green and sintered density |
Permeability | Depends on magnetic state of finished alloy |
Hardness | Alloying enhances hardenability versus pure metals |
Besides chemical synthesis, powder morphology plays an equally important role in determining consolidation behavior, and in turn, successful adoption by powder bed fusion, binder jetting and metal injection molding application technologies where free flowing characteristics are vital.
Applications and Uses of Metal Alloy Powders
With expanded customization freedom unavailable in traditional billets, key product categories utilizing alloys powders include:
Table 4: Major application areas for metal alloy powders
Sector | Applications |
---|---|
Aerospace | Turbine blades, airframe fittings, gears |
Automotive | Connecting rods, drive gear shafts |
Medical | Dental crowns, implants, prosthetics |
Marine | Pump impellers, propellers, saltwater piping |
Oil and Gas | Downhole couplings, valves, well site spares |
3D printing | Lightweight lattices, bionic shapes with high hardened strength |
The tailored balance of hardness, corrosion resistance and dimensional accuracy possible makes alloy powders attractive for producing critical rotating components across defense, space, biomedical and transportation equipment products.
Metal Alloy Powder Specifications
Alloy powder compositions conform to certified specifications ensuring reliable performance.
Table 5: Alloy powder specifications in industrial, aerospace and defense sectors
Alloy | Common Specifications |
---|---|
Nickel alloys | AMS 4777, 4779 etc |
Steels | Custom H and D tool steel blends |
Aluminum | AMS 4010, AMS 4000 series etc |
Titanium alloys | AMS 7001, 7004 etc |
Cobalt alloys | AMS 5887, ASTM B776 etc |
These specifications prescribe acceptable testing methods, sampling procedures, acceptance criteria ranges and powder batch documentation protocols.
Both ASTM International and individual manufacturers define related size grading, chemical analysis, particle characteristics plus post-consolidation mechanical and physical property limits for critical applications.
Global Suppliers and Pricing Information
Table 6: Leading international alloy powder producers and price ranges:
Company | Alloy Grades | Price Range per Kg | |
---|---|---|---|
Höganäs | Steel, Nickel | $5-15 | |
Sandvik | Osprey | Titanium, Nickel, Cobalt | $50-150 |
Carpenter | Titanium, Cobalt, Steel | $40-100 | |
Praxair | Nickel, Steel, Cobalt | $15-60 | |
ATI Powder Metals | Titanium, Nickel, Iron | $30-90 |
Prices depend on product certification needs, purchased volumes, specialty of composition involved and extent of atomization sophistication in powder fabrication and post-processing.
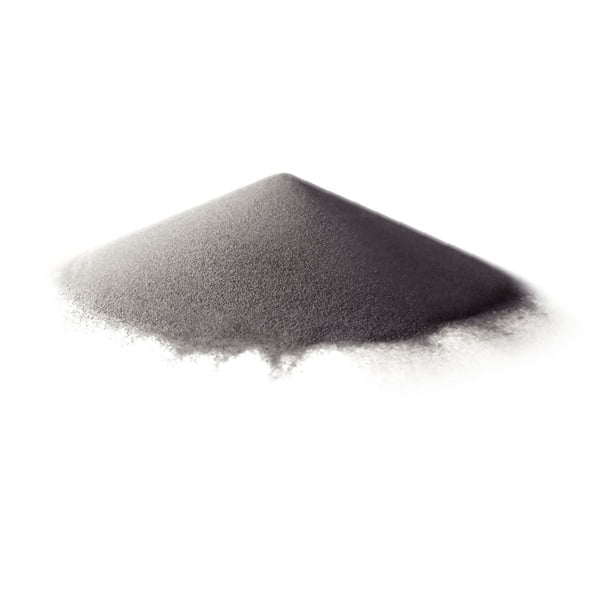
Comparative Pros and Cons
Table 7: Pros and cons relative to cast or wrought metal counterparts
Advantages | Disadvantages |
---|---|
More versatile | Extra steps needed for consolidation |
Excellent uniformity | Lower toughness without HIP |
Components customizable | Maximum size limited |
Reduced waste from net shape forming | Higher cost presently |
Heat treat flexibility | Surface finish challenges |
For complex or integrated multi-material designs made in lower volumes like orthopedic knee joints involving polymers and metal alloys together, readiness for additive manufacturing provides faster and cheaper routes.
Frequently Asked Questions
Q: What is the benefit of using pre-alloyed powder over mixing element powders separately?
Pre-alloying ensures uniformity of desired chemistry through the xyz, reduces likelihood of component performance variability from batch to batch, and prevents variation caused by improper blending ratios.
Q: What consolidation processes transform alloy powders into solid components?
Main methods include – sintering, metal injection molding, hot isostatic pressing and additive manufacturing techniques like laser powder bed fusion followed by infiltration. Choice depends on industry, product size, complexity needs and economics.
Share On
MET3DP Technology Co., LTD is a leading provider of additive manufacturing solutions headquartered in Qingdao, China. Our company specializes in 3D printing equipment and high-performance metal powders for industrial applications.
Inquiry to get best price and customized Solution for your business!
Related Articles
About Met3DP
Recent Update
Our Product
CONTACT US
Any questions? Send us message now! We’ll serve your request with a whole team after receiving your message.
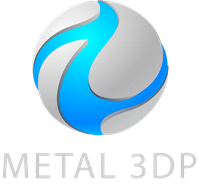
Metal Powders for 3D Printing and Additive Manufacturing