Metal Powders for Aerospace
Table of Contents
Aerospace engineering stands at the forefront of technological advancements, demanding materials that combine strength, lightweight properties, and durability. Metal powders have emerged as vital components in this domain, offering a wide array of benefits that propel aerospace innovations. In this article, we’ll delve into the world of metal powders used in aerospace, exploring their types, compositions, applications, and more.
Overview of Metal Powders in Aerospace
Metal powders are finely ground metals that can be used in various manufacturing processes, including additive manufacturing, powder metallurgy, and thermal spraying. These powders are critical in aerospace due to their ability to create complex, high-strength components that are lighter than those made with traditional manufacturing methods. The result is improved fuel efficiency, enhanced performance, and increased lifespan of aerospace components.
Key Attributes of Metal Powders for Aerospace
- Strength-to-Weight Ratio: Essential for reducing the overall weight of aircraft and spacecraft while maintaining structural integrity.
- Durability: Resistance to extreme temperatures and harsh environments.
- Versatility: Ability to form intricate shapes and designs that traditional methods cannot achieve.
- Consistency: Uniform particle size and composition ensure reliable performance.
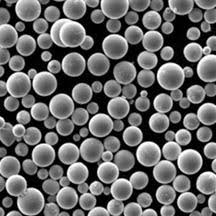
Types of Metal Powders Used in Aerospace
1. Titanium Alloys (Ti6Al4V)
Titanium alloys are renowned for their excellent strength-to-weight ratio and corrosion resistance, making them ideal for critical aerospace components.
Composition:
- Titanium (Ti)
- Aluminum (Al)
- Vanadium (V)
Properties:
- High strength
- Lightweight
- Excellent corrosion resistance
Applications:
- Jet engine components
- Structural parts
- Landing gear
2. Inconel 718
Inconel 718 is a nickel-based superalloy known for its exceptional high-temperature strength and oxidation resistance.
Composition:
- Nickel (Ni)
- Chromium (Cr)
- Iron (Fe)
- Niobium (Nb)
Properties:
- Excellent high-temperature performance
- Oxidation and corrosion resistance
Applications:
- Turbine blades
- Exhaust systems
- High-temperature fasteners
3. Aluminum Alloys (AlSi10Mg)
Aluminum alloys, such as AlSi10Mg, offer a good balance of strength, lightweight, and cost-effectiveness.
Composition:
- Aluminum (Al)
- Silicon (Si)
- Magnesium (Mg)
Properties:
- Lightweight
- Good thermal conductivity
- Moderate strength
Applications:
- Airframe components
- Heat exchangers
- Lightweight structural parts
4. Stainless Steel (316L)
Stainless steel 316L is favored for its corrosion resistance and good mechanical properties.
Composition:
- Iron (Fe)
- Chromium (Cr)
- Nickel (Ni)
- Molybdenum (Mo)
Properties:
- Excellent corrosion resistance
- Good mechanical properties
- Biocompatibility
Applications:
- Structural components
- Engine parts
- Fasteners
5. Cobalt-Chrome Alloys (CoCrMo)
Cobalt-chrome alloys are known for their high wear resistance and ability to withstand harsh environments.
Composition:
- Cobalt (Co)
- Chromium (Cr)
- Molybdenum (Mo)
Properties:
- High wear resistance
- Excellent biocompatibility
- High temperature stability
Applications:
- Turbine blades
- Combustion chamber parts
- Wear-resistant components
6. Maraging Steel (18Ni300)
Maraging steel is a high-strength steel with excellent toughness and ductility.
Composition:
- Iron (Fe)
- Nickel (Ni)
- Cobalt (Co)
- Molybdenum (Mo)
Properties:
- High strength
- Good toughness
- Easy machinability
Applications:
- Tooling
- Structural components
- Landing gear
7. Copper Alloys (CuCrZr)
Copper alloys, such as CuCrZr, are prized for their high thermal and electrical conductivity.
Composition:
- Copper (Cu)
- Chromium (Cr)
- Zirconium (Zr)
Properties:
- High thermal conductivity
- Good electrical conductivity
- Moderate strength
Applications:
- Electrical components
- Heat exchangers
- Thermal management systems
8. Nickel-Based Alloys (Hastelloy X)
Nickel-based alloys like Hastelloy X offer excellent oxidation resistance and high-temperature strength.
Composition:
- Nickel (Ni)
- Chromium (Cr)
- Iron (Fe)
- Molybdenum (Mo)
Properties:
- High temperature stability
- Oxidation resistance
- Good mechanical properties
Applications:
- Combustor parts
- Turbine components
- High-temperature fasteners
9. Magnesium Alloys (AZ91D)
Magnesium alloys are the lightest structural metals available, providing excellent strength-to-weight ratios.
Composition:
- Magnesium (Mg)
- Aluminum (Al)
- Zinc (Zn)
Properties:
- Lightweight
- Good strength
- Excellent machinability
Applications:
- Structural components
- Gearbox casings
- Lightweight frames
10. Tantalum Alloys (Ta-10W)
Tantalum alloys are used in aerospace applications requiring high melting points and excellent corrosion resistance.
Composition:
- Tantalum (Ta)
- Tungsten (W)
Properties:
- High melting point
- Excellent corrosion resistance
- Good mechanical properties
Applications:
- High-temperature components
- Corrosion-resistant parts
- Structural parts in harsh environments
Applications of Metal Powders for Aerospace
Metal powders are used in a variety of aerospace applications, each leveraging their unique properties to enhance performance and durability.
Application | Metal Powder Used | Benefits |
---|---|---|
Jet Engine Components | Titanium Alloys, Inconel 718 | High strength, lightweight, high-temperature resistance |
Structural Parts | Aluminum Alloys, Titanium Alloys | Lightweight, high strength, corrosion resistance |
Turbine Blades | Inconel 718, Cobalt-Chrome | High-temperature performance, oxidation resistance |
Heat Exchangers | Aluminum Alloys, Copper Alloys | Excellent thermal conductivity, lightweight |
Fasteners | Stainless Steel, Nickel-Based Alloys | Corrosion resistance, high strength |
Electrical Components | Copper Alloys | High electrical conductivity, thermal management |
Landing Gear | Titanium Alloys, Maraging Steel | High strength, good toughness, lightweight |
Combustor Parts | Hastelloy X, Tantalum Alloys | High temperature stability, corrosion resistance |
Gearbox Casings | Magnesium Alloys | Lightweight, good machinability |
Wear-Resistant Components | Cobalt-Chrome Alloys | High wear resistance, durability |
Advantages of Metal Powders for Aerospace
1. Enhanced Design Flexibility
Metal powders allow for intricate and complex designs that are difficult or impossible to achieve with traditional manufacturing methods. This flexibility leads to components that are optimized for performance and weight.
2. Superior Material Properties
Components made from metal powders often exhibit superior material properties, such as improved mechanical strength, thermal resistance, and corrosion resistance. This is crucial in the harsh and demanding environment of aerospace applications.
3. Lightweight Solutions
The aerospace industry constantly seeks to reduce weight without compromising strength. Metal powders, particularly those used in additive manufacturing, offer a solution by producing lightweight yet strong components.
4. Cost-Effectiveness
Despite the high initial cost of metal powders and additive manufacturing technology, the overall cost can be lower due to reduced material waste, shorter production times, and less need for complex tooling.
5. Sustainability
Additive manufacturing with metal powders can be more environmentally friendly than traditional methods, as it generates less waste and often uses materials more efficiently.
Disadvantages of Metal Powders for Aerospace
1. High Initial Costs
The equipment and materials for producing and processing metal powders can be expensive, making the initial investment high.
2. Material Limitations
Not all metals can be effectively turned into powders, and some metal powders may not possess the desired properties for specific aerospace applications.
3. Quality Control
Ensuring the consistent quality of metal powders can be challenging. Variations in particle size, shape, and composition can affect the final product’s performance.
4. Technical Challenges
Additive manufacturing with metal powders requires specialized knowledge and skills, which can be a barrier for some companies to adopt this technology.
Comparison of Advantages and Disadvantages
Advantages | Disadvantages |
---|---|
Enhanced design flexibility | High initial costs |
Superior material properties | Material limitations |
Lightweight solutions | Quality control challenges |
Cost-effectiveness over time | Technical challenges |
Sustainability and reduced waste | High initial investment |
Detailed Specifications of Metal Powders
Specifications, Sizes, Grades, and Standards
Metal Powder | Specifications | Sizes | Grades | Standards |
---|---|---|---|---|
Titanium Alloys (Ti6Al4V) | ASTM F2924 | 15-45 microns | Grade 5 | AMS 4998, ASTM B348 |
Inconel 718 | AMS 5662 | 15-45 microns | Grade | 718 | AMS 5663, ASTM B637 |
Aluminum Alloys (AlSi10Mg) | ASTM F3318 | 20-63 microns | Grade 10Mg | AMS 4289, ASTM B209 |
Stainless Steel (316L) | ASTM F138 | 15-53 microns | Grade 316L | AMS 5648, ASTM A276 |
Cobalt-Chrome Alloys (CoCrMo) | ASTM F75 | 15-45 microns | Grade F75 | ISO 5832-12, ASTM F1537 |
Maraging Steel (18Ni300) | ASTM A538 | 20-63 microns | Grade 300 | AMS 6521, ASTM A579 |
Copper Alloys (CuCrZr) | ASTM B124 | 20-63 microns | Grade C18150 | AMS 4590, ASTM B937 |
Nickel-Based Alloys (Hastelloy X) | AMS 5536 | 15-53 microns | Grade X | AMS 5587, ASTM B435 |
Magnesium Alloys (AZ91D) | ASTM B107 | 20-63 microns | Grade AZ91D | AMS 4377, ASTM B93 |
Tantalum Alloys (Ta-10W) | ASTM B708 | 15-45 microns | Grade Ta10W | ASTM F560, ASTM B365 |
Suppliers and Pricing Details
Supplier | Metal Powder | Average Price (per kg) | Region |
---|---|---|---|
Carpenter Technology | Titanium Alloys (Ti6Al4V) | $300 – $350 | North America |
Höganäs AB | Inconel 718 | $250 – $300 | Europe |
Sandvik Materials | Aluminum Alloys (AlSi10Mg) | $150 – $200 | Global |
EOS GmbH | Stainless Steel (316L) | $100 – $150 | Europe |
Praxair Surface Technologies | Cobalt-Chrome Alloys (CoCrMo) | $350 – $400 | North America |
Oerlikon AM | Maraging Steel (18Ni300) | $200 – $250 | Global |
Materion Corporation | Copper Alloys (CuCrZr) | $75 – $125 | North America |
Haynes International | Nickel-Based Alloys (Hastelloy X) | $250 – $300 | Global |
Magnesium Elektron | Magnesium Alloys (AZ91D) | $50 – $100 | Europe |
H.C. Starck Tantalum and Niobium GmbH | Tantalum Alloys (Ta-10W) | $400 – $450 | Global |
Comparing Pros and Cons of Various Metal Powders
Metal Powder | Pros | Cons |
---|---|---|
Titanium Alloys (Ti6Al4V) | High strength-to-weight ratio, corrosion resistance | High cost, challenging to process |
Inconel 718 | High-temperature performance, oxidation resistance | High cost, difficult to machine |
Aluminum Alloys (AlSi10Mg) | Lightweight, good thermal conductivity | Lower strength compared to other aerospace materials |
Stainless Steel (316L) | Corrosion resistance, good mechanical properties | Heavier than other aerospace alloys |
Cobalt-Chrome Alloys (CoCrMo) | High wear resistance, biocompatibility | High cost, challenging to process |
Maraging Steel (18Ni300) | High strength, good toughness | Requires aging treatment, expensive |
Copper Alloys (CuCrZr) | High thermal and electrical conductivity | Lower strength, prone to oxidation |
Nickel-Based Alloys (Hastelloy X) | High temperature stability, oxidation resistance | High cost, difficult to machine |
Magnesium Alloys (AZ91D) | Lightweight, good machinability | Lower strength, flammability |
Tantalum Alloys (Ta-10W) | High melting point, corrosion resistance | Very high cost, limited availability |
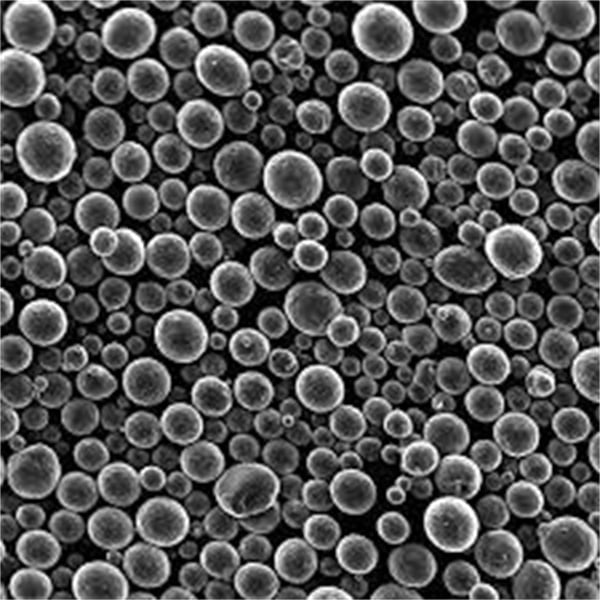
FAQs
Question | Answer |
---|---|
What are the primary benefits of using metal powders in aerospace? | Metal powders offer enhanced design flexibility, superior material properties, lightweight solutions, cost-effectiveness, and sustainability. |
Which metal powder is best for high-temperature applications? | Inconel 718 and Hastelloy X are excellent choices for high-temperature applications due to their exceptional high-temperature strength and oxidation resistance. |
How does additive manufacturing benefit from metal powders? | Additive manufacturing allows for complex designs, reduced material waste, shorter production times, and the ability to create lightweight, strong components. |
What are the challenges of using metal powders in aerospace? | High initial costs, material limitations, quality control challenges, and technical complexities are some of the challenges associated with using metal powders in aerospace. |
Can metal powders be used for all aerospace components? | While metal powders are versatile, not all components are suitable for production with metal powders due to specific material properties and performance requirements. |
What factors influence the cost of metal powders? | The type of metal, particle size, production method, and supplier can all influence the cost of metal powders. |
Are there environmental benefits to using metal powders? | Yes, metal powders can be more environmentally friendly due to reduced waste and more efficient use of materials in additive manufacturing processes. |
What standards apply to aerospace metal powders? | Standards such as ASTM, AMS, and ISO apply to various metal powders, ensuring consistency, quality, and performance in aerospace applications. |
How important is quality control for metal powders? | Quality control is crucial as variations in particle size, shape, and composition can significantly impact the performance and reliability of the final product. |
What are some emerging trends in the use of metal powders in aerospace? | Emerging trends include the development of new alloys, improved additive manufacturing techniques, and greater integration of metal powders in mainstream aerospace production. |
Conclusion
Metal powders are revolutionizing the aerospace industry by enabling the production of high-performance, lightweight, and complex components. As technology advances, the role of metal powders will only become more significant, driving innovations and enhancing the capabilities of aerospace engineering. Whether it’s the high strength of titanium alloys or the exceptional temperature resistance of Inconel 718, each metal powder brings unique benefits and challenges, making the choice of material a critical factor in aerospace manufacturing.
Share On
MET3DP Technology Co., LTD is a leading provider of additive manufacturing solutions headquartered in Qingdao, China. Our company specializes in 3D printing equipment and high-performance metal powders for industrial applications.
Inquiry to get best price and customized Solution for your business!
Related Articles
About Met3DP
Recent Update
Our Product
CONTACT US
Any questions? Send us message now! We’ll serve your request with a whole team after receiving your message.
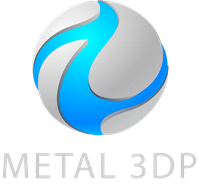
Metal Powders for 3D Printing and Additive Manufacturing