metal powder for electronics
Table of Contents
Imagine a world where electronics are built not from solid slabs of metal, but from tiny, individual particles. These particles, known as metal powder for electronics, are revolutionizing the way we manufacture everything from smartphones to spacecraft. In this comprehensive guide, we’ll delve into the fascinating realm of metal powders for electronics, exploring their properties, applications, advantages, limitations, and various configurations.
An Overview of Metal Powder for electronics
Metal powders are finely-ground metallic particles, typically ranging in size from a few micrometers (millionths of a meter) to hundreds of micrometers. These powders are produced through various techniques like atomization, where molten metal is broken down into droplets that solidify into spherical particles. The resulting metal powders boast several advantages over traditional bulk metals:
- Unparalleled Design Flexibility: Unlike traditional machining, metal powders enable the creation of intricate 3D structures through additive manufacturing techniques like 3D printing. This allows for lighter, more complex components with enhanced functionality.
- Superior Material Properties: Metal powders often possess improved properties compared to their bulk counterparts. For example, some metal powders exhibit higher strength-to-weight ratios and improved thermal conductivity.
- Reduced Waste: Metal powder additive manufacturing processes minimize material waste compared to traditional subtractive techniques like machining.
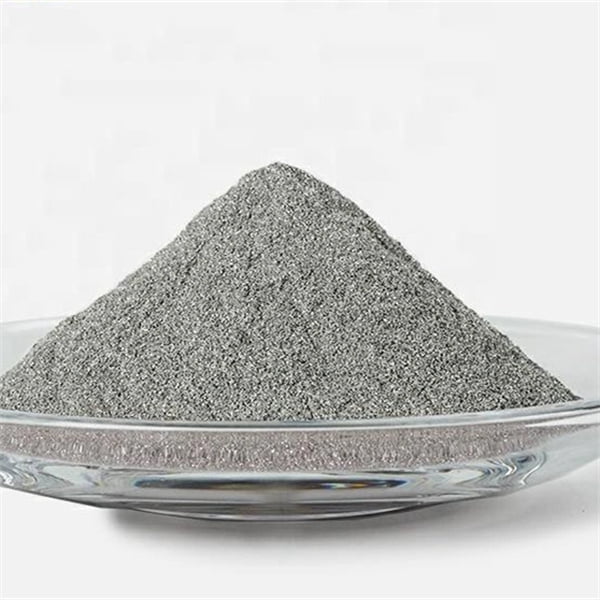
Common Types of Metal Powders for Electronics:
Metal Powder Type | Composition | Properties | Applications in Electronics |
---|---|---|---|
Copper (Cu) | Pure copper or copper alloys | Excellent electrical conductivity, good thermal conductivity, malleable, ductile | Electrical connectors, heat sinks, EMI shielding, electrodes |
Silver (Ag) | Pure silver | Highest electrical and thermal conductivity among metals, excellent solderability | Electrical contacts, bonding wires, high-performance connectors |
Nickel (Ni) | Pure nickel or nickel alloys | Good electrical conductivity, magnetic properties (depending on alloy), corrosion resistance | EMI shielding, electrodes, battery components, magnetic components |
Iron (Fe) | Pure iron or iron alloys (steel, stainless steel) | High strength, magnetic properties (ferromagnetic), good machinability | Magnetic components in inductors and transformers, housings, shielding |
Aluminum (Al) | Pure aluminum or aluminum alloys | Lightweight, good electrical conductivity, good thermal conductivity, corrosion resistance | Heat sinks, housings, bonding wires, EMI shielding |
Tungsten (W) | Pure tungsten or tungsten alloys (e.g., tungsten carbide) | High melting point, high hardness, good wear resistance | Electrical contacts, electrodes, heat sinks, X-ray source components |
Titanium (Ti) | Pure titanium or titanium alloys | High strength-to-weight ratio, good corrosion resistance, biocompatible | Housings for medical implants, EMI shielding |
Cobalt (Co) | Pure cobalt or cobalt alloys | High magnetic permeability, good wear resistance | Magnetic components in inductors and transformers |
Molybdenum (Mo) | Pure molybdenum or molybdenum alloys | High melting point, good thermal conductivity | Heat sinks, electrodes in high-temperature applications |
Gold (Au) | Pure gold or gold alloys | Excellent electrical conductivity, corrosion resistance, good solderability | Electrical connectors, bonding wires in high-performance applications |
Please note: This table presents a selection of commonly used metal powders in electronics. There are many other metal powders and alloys used for specialized applications.
Applications of Metal Powders in Electronics
Metal powders are finding their way into a vast array of electronic components, shaping the future of miniaturization, performance, and design freedom. Here’s a glimpse into some of their key applications:
Application | Metal Powders Typically Used | Benefits of Metal Powders |
---|---|---|
Electrical Connectors & Contacts | Copper, Silver, Nickel Alloys | High conductivity, improved wear resistance, ability to create complex shapes |
Heat Sinks | Copper, Aluminum, Aluminum Alloys | Efficient heat dissipation, lightweight construction |
EMI Shielding | Copper, Nickel, Iron Alloys | Effective electromagnetic interference blockage, design flexibility |
Battery Components | Nickel, Lithium | Improved electrode performance, potential for lighter battery designs |
Magnetic Components | Iron Alloys (steel, ferrites), Nickel Alloys, Cobalt | Precise control of magnetic properties, miniaturization of components |
3D-Printed Electronic Components | Silver, Copper, Gold | Highly customized designs, integration of multiple functionalities |
Emerging Applications | Various | Exploration in areas like printed antennas, biocompatible medical implants, and lightweight aerospace components |
Properties, Advantages, and Limitations of Metal Powders for Electronics
While metal powders offer a treasure trove of benefits for electronics manufacturing, it’s crucial to understand their specific properties and limitations to make informed choices.
Properties to Consider:
- Particle Size and Distribution: The size and distribution of metal powder particles significantly impact their behavior and final product characteristics. Finer powders generally offer better surface area for processes like sintering (bonding particles) but may be more challenging to handle due to increased flowability. Conversely, larger particles can improve flow but might limit resolution in 3D printing applications.
- Particle Shape: The shape of metal powder particles, whether spherical, irregular, or flaky, influences factors like packing density (how tightly particles pack together) and propensity for flow. Spherical particles typically flow more easily and pack more densely, leading to improved product strength.
- Purity: The purity of the metal powder directly affects its electrical conductivity, thermal conductivity, and mechanical properties. High purity powders are often preferred for applications demanding optimal performance.
- Surface Chemistry: The surface chemistry of metal powders, including the presence of oxides or other surface contaminants, can influence factors like sintering behavior and adhesion to other materials.
Advantages of Metal Powders for Electronics
- Unparalleled Design Freedom: Metal powders enable the creation of intricate 3D structures with internal channels, lattices, and other features impossible with traditional machining. This opens doors for lighter, more efficient heat sinks, components with integrated functionalities, and miniaturized designs.
- Enhanced Material Properties: Metal powders can exhibit superior properties compared to their bulk counterparts. For instance, some copper powders boast higher thermal conductivity than bulk copper, leading to more efficient heat dissipation in electronic components. Additionally, metal powders often allow for the creation of composites, combining the properties of different metals to achieve unique functionalities.
- Reduced Waste: Metal powder additive manufacturing processes minimize material waste compared to traditional subtractive techniques like machining. Since metal powder is used only where needed in the final product, there’s significantly less scrap material.
- Mass Customization: Metal powder additive manufacturing allows for on-demand production of electronic components with minimal setup time. This facilitates rapid prototyping, small batch production, and even personalization of electronic devices.
Limitations of Metal Powder for Electronics:
- Powder Cost: Metal powders can be more expensive than bulk metals, especially for high-purity or exotic materials. This can be a limiting factor for high-volume production.
- Process Complexity: Additive manufacturing processes using metal powders can be more complex to set up and operate compared to traditional techniques. They often require specialized equipment and skilled personnel.
- Material Performance: While some metal powders offer improved properties, others may exhibit limitations compared to bulk metals. For instance, the strength of 3D-printed metal components can be lower than their wrought counterparts in some cases.
- Post-Processing: Metal powder additive manufacturing processes often require post-processing steps like heat treatment to achieve desired mechanical properties. This adds to the overall production time and complexity.
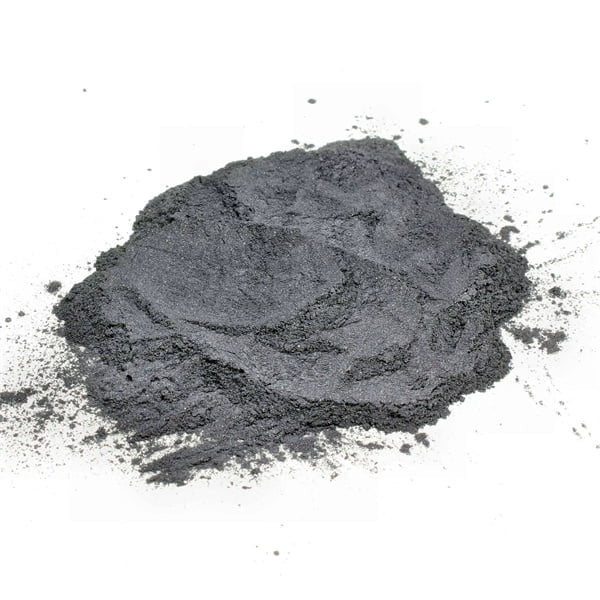
Choosing the Right Powder for the Job
With a diverse array of metal powders available, selecting the optimal choice for your electronic application requires careful consideration of several factors:
- Required Properties: Identify the key properties needed for your application, such as electrical conductivity, thermal conductivity, mechanical strength, and corrosion resistance.
- Processing Method: Consider the specific additive manufacturing technique you’ll be using, as different techniques may have compatibility requirements with regards to particle size, shape, and flowability.
- Cost Constraints: Evaluate the cost of the metal powder in relation to your budget and production volume.
- Availability: Ensure the chosen metal powder is readily available from a reputable supplier.
Here’s a table outlining some specific metal powder model options to consider, along with their key characteristics:
Metal Powder Model | Composition | Key Characteristics | Typical Applications | Supplier Examples | Pricing (estimate) |
---|---|---|---|---|---|
Höganäs AM Copper C100.20 | Pure copper | High purity (>99.5% Cu), spherical particles, good flowability | Electrical connectors, heat sinks | Höganäs AB | ~$50/kg |
Sandvik Osprey Silver IN625 | Silver | High purity (>99.9% Ag), spherical particles, excellent conductivity | High-performance electrical contacts, bonding wires | Sandvik AB | ~$200/kg |
Carpenter Additive AM320 | Nickel-chromium alloy | Good corrosion resistance, high strength, suitable for laser melting | EMI shielding components, housings | Carpenter Technology Corporation | ~$75/kg |
BASF Stainless Steel 17-4 PH | 17-4 PH stainless steel | High strength, good corrosion resistance, biocompatible | Housings for medical implants, aerospace components | BASF SE | ~$100/kg |
LPW Ti-6Al-4V | Ti-6Al-4V titanium alloy | High strength-to-weight ratio, excellent corrosion resistance | Aerospace components, medical implants | LPW Technology Ltd. | ~$250/kg |
GE Additive AM260S | Cobalt-chrome alloy | Biocompatible, good wear resistance | Medical implants, joint replacements | GE Additive | ~$150/kg |
ExOne Molybdenum 400 | Pure molybdenum | High melting point, good thermal conductivity | High-temperature applications, electrodes | ExOne | ~$120/kg |
Nanomakers Nano Gold Ink | Gold nanoparticles | Ultrafine particle size, excellent electrical conductivity | Printed electronics, high-performance connectors | Nanomakers | ~$500/kg (due to extremely fine particle size) |
Please note: Pricing information is indicative and can vary depending on supplier, quantity, and market conditions.
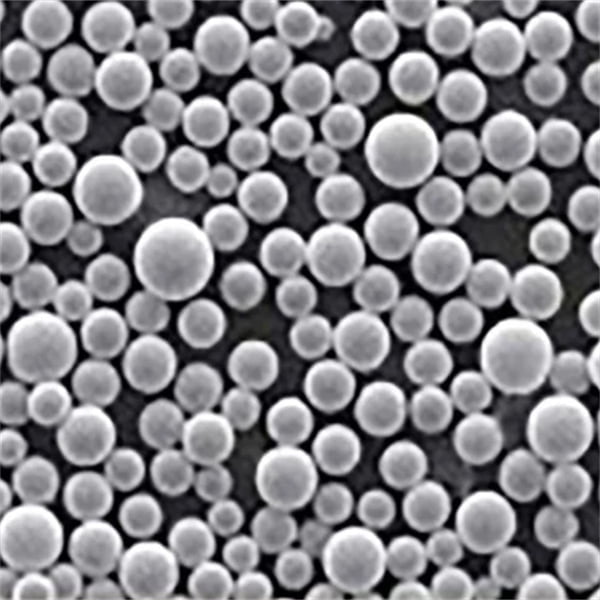
Future Trends of metal powder for electronics
The use of metal powders in electronics offers a more sustainable approach to manufacturing compared to traditional techniques. Metal powder additive manufacturing minimizes material waste and allows for lighter components, potentially reducing energy consumption throughout a product’s life cycle. As research and development efforts continue, we can expect to see advancements in several areas:
- Development of new metal powder alloys: Material scientists are constantly formulating new metal powder alloys with optimized properties for specific electronic applications. This will lead to components with enhanced performance and functionality.
- Improved powder production techniques: Advancements in powder production methods hold promise for more cost-effective and efficient production of high-quality metal powders.
- Hybrid manufacturing techniques: The integration of metal powder additive manufacturing with traditional techniques like machining could enable the creation of complex electronic components with superior properties.
FAQ
Q: Are metal powders safe to handle?
A: Metal powders, like any fine particles, can pose inhalation hazards if not handled properly. It’s crucial to follow safety guidelines and use appropriate personal protective equipment (PPE) when working with metal powders.
Q: How strong are 3D-printed metal components made from powder?
A: The strength of 3D-printed metal components can vary depending on the metal powder used, the printing process, and post-processing techniques. In some cases, 3D-printed components may exhibit lower strength than their wrought counterparts. However, ongoing research is improving the strength and performance of 3D-printed metals.
Q: What are the environmental benefits of using metal powders in electronics?
A: Metal powder additive manufacturing offers several environmental advantages. It minimizes material waste compared to traditional subtractive techniques and allows for the creation of lighter components, potentially reducing energy consumption throughout a product’s life cycle.
Q: What is the future of metal powders in electronics?
The future of metal powders in electronics appears bright. With continued advancements in material science, production techniques, and hybrid manufacturing processes, metal powders hold immense potential for creating next-generation electronic components with enhanced performance, design freedom, and sustainability.
Share On
MET3DP Technology Co., LTD is a leading provider of additive manufacturing solutions headquartered in Qingdao, China. Our company specializes in 3D printing equipment and high-performance metal powders for industrial applications.
Inquiry to get best price and customized Solution for your business!
Related Articles
About Met3DP
Recent Update
Our Product
CONTACT US
Any questions? Send us message now! We’ll serve your request with a whole team after receiving your message.
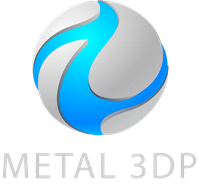
Metal Powders for 3D Printing and Additive Manufacturing