metal powder for engine
Table of Contents
Imagine a world where engine parts are crafted with microscopic precision, boasting complex shapes and exceptional strength. This isn’t science fiction; it’s the reality of metal powder for engine technology. Metal powder for engine are transforming the automotive industry, offering a treasure trove of benefits for engine performance, design flexibility, and even sustainability. But before we delve into the nitty-gritty, let’s get a grip on what metal powders are and how they’re changing the game.
Metal Powders 101: From Granules to Powerhouse Parts
metal powder for engine are finely-ground metal particles, ranging in size from microns (thousandths of a millimeter) to millimeters. These tiny grains are meticulously crafted from various metals and alloys, each offering unique properties that translate into exceptional performance in engine components.
The magic lies in a process called powder metallurgy (PM). Think of it as baking a cake, but instead of flour and sugar, we use metal powders. The powder is compressed into a mold, then subjected to high heat and pressure (sintering) to fuse the particles into a solid form. This technique unlocks a universe of possibilities for engine design.
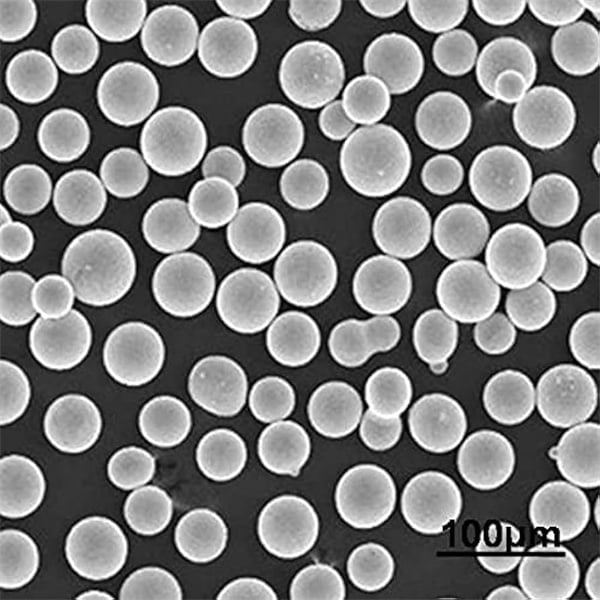
A smorgasbord of metal powder for engine
The world of metal powders for engines is teeming with options, each boasting its own strengths. Here are 10 of the most prominent players:
1. Iron-based Powders:
The workhorses of the bunch, iron-based powders like Fe-Cu (iron-copper) and Fe-Ni (iron-nickel) offer a compelling blend of affordability, good machinability, and decent wear resistance. They’re ideal for non-critical engine components like gears, brackets, and housings.
2. Steel Powders:
Taking things up a notch, steel powders like AISI 4600 and 4640 provide superior strength and wear resistance compared to their iron-based counterparts. These tougher materials are prime candidates for high-stress applications like connecting rods and camshafts.
3. Nickel-based Powders:
When the heat is on (literally!), nickel-based powders like Inconel 625 and 718 step up to the plate. These superstars boast exceptional resistance to high temperatures, oxidation, and corrosion, making them perfect for components like turbocharger housings and exhaust manifolds.
4. Aluminum Powders:
Aluminum powders like AA2014 and AA6061 bring the lightweight advantage to the table. Compared to steel, they offer significant weight reduction, which translates into better fuel efficiency. However, their trade-off is slightly lower strength.
5. Copper Powders:
Copper powders like Cu-Sn (copper-tin) shine when it comes to thermal conductivity. This property allows for efficient heat dissipation, a crucial factor for optimal engine performance. Copper powders are often used in heat sinks and oil galleries.
6. Molybdenum Powders:
Molybdenum powders like Mo-Ni (molybdenum-nickel) are the high-performance athletes of the metal powder world. They offer exceptional strength at elevated temperatures, making them ideal for demanding applications like piston rings and valve seats.
7. Titanium Powders:
For the ultimate in strength-to-weight ratio, titanium powders like Ti-6Al-4V take the crown. These lightweight powerhouses are used in high-end racing applications where every ounce counts. However, their high cost makes them less common in mass-produced engines.
8. Tungsten Powders:
Tungsten powders like W-Ni (tungsten-nickel) are density champions. Their incredible density makes them suitable for applications requiring high inertia, such as crankshafts and balance shafts.
9. Cobalt-Chromium Powders:
Cobalt-chromium powders like CoCrMo (cobalt-chromium-molybdenum) excel in wear resistance. This makes them ideal for components like valve tappets and cam followers, which experience constant friction.
10. Bronze Powders:
Bronze powders like CuSn (copper-tin) offer a unique combination of good wear resistance, self-lubricating properties, and excellent corrosion resistance. They’re often used in bushings and bearings where smooth operation and longevity are paramount.
metal powder for engine: A Match Made in Engine Heaven
Now that we’ve met the key players, let’s explore how metal powders are revolutionizing various engine components:
- Engine Blocks: Metal powder technology allows for the creation of complex engine block designs with intricate cooling channels. This translates into more efficient cooling and improved engine performance.
- Connecting Rods: Metal powder connecting rods can be lighter and stronger than traditional forged steel rods. This reduces weight and improves engine responsiveness.
- Camshafts and Crankshafts: Metal powder offers the ability to create complex internal features in camshafts and crankshafts, leading to optimized oil flow and reduced weight. Additionally, some metal powders boast improved fatigue strength compared to traditional cast iron components.
- Piston Rings and Valve Seats: Metal powders like molybdenum and cobalt-chromium excel in these applications due to their exceptional wear resistance at high temperatures. This translates into reduced friction, improved engine efficiency, and longer engine life.
- Bearings and Bushings: Bronze powders shine in these wear-prone components due to their self-lubricating properties and excellent resistance to wear and tear. This translates into smoother operation and reduced maintenance needs.
Advantages of metal powder for engine
Metal powders aren’t just a fancy new trick; they offer a compelling set of advantages that are transforming the engine game:
- Design Flexibility: Unlike traditional casting or forging techniques, metal powder allows for the creation of complex shapes with intricate details. This opens doors for innovative engine designs that were previously impossible.
- Lightweighting: Several metal powders, like aluminum and titanium, offer significant weight reduction compared to traditional materials. This translates into improved fuel efficiency and better overall vehicle performance.
- Material Efficiency: The PM process minimizes material waste compared to traditional methods. This not only reduces costs but also aligns with a more sustainable manufacturing approach.
- Dimensional Accuracy: Metal powder components can be produced with near-net shapes, requiring minimal post-processing. This leads to higher production efficiency and reduces overall costs.
- Improved Performance: The ability to tailor material properties through specific powder selection allows for components with optimized characteristics for strength, wear resistance, and thermal management, leading to improved engine performance.
Disadvantages of metal powder for engine
While metal powders offer a treasure trove of benefits, it’s important to acknowledge some potential drawbacks:
- Cost: The PM process can be more expensive compared to traditional casting or forging, especially for high-volume production. However, the cost advantage may narrow as PM technology continues to mature.
- Material Limitations: Not all metals are readily available in powder form, and some may exhibit different properties compared to their bulk counterparts. Ongoing research and development are addressing these limitations.
- Part Size Restrictions: Current PM technology has limitations on the size of parts that can be manufactured. However, advancements are being made to overcome this hurdle.
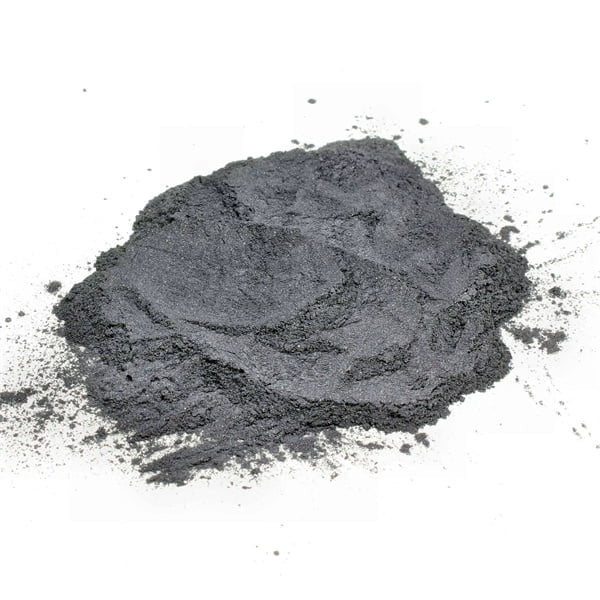
Metal Powders vs. Traditional Techniques: A Head-to-Head Showdown
How do metal powders stack up against the established players in engine component manufacturing? Here’s a breakdown:
- Metal Powders vs. Casting: Metal powders offer greater design flexibility and dimensional accuracy compared to casting. However, casting generally has a lower cost advantage for high-volume production.
- Metal Powders vs. Forging: Metal powders can achieve similar strength characteristics as forged components but with potentially less material waste. However, forging may be more cost-effective for specific applications.
The Future of Metal Powders: Gearing Up for Innovation
The future of metal powders in the engine arena is bright. Here’s a glimpse of what’s on the horizon:
- Advanced Powders: Research is ongoing to develop new metal powders with even better properties, including improved strength-to-weight ratios and higher temperature resistance.
- Hybrid Techniques: The integration of metal powders with other manufacturing methods like 3D printing holds immense potential for creating even more complex and high-performance engine components.
- Sustainability Focus: As the focus on sustainable manufacturing intensifies, the PM process’s material efficiency will become an even more significant advantage.
FAQs
Q: Are metal powder engines more powerful?
A: Not necessarily. While metal powders can contribute to improved engine performance through weight reduction and optimized component design, overall engine power depends on various factors like engine displacement and design.
Q: Are metal powder engines more expensive?
A: Currently, metal powder engines may have a slightly higher cost compared to traditional engines. However, this gap is expected to narrow as PM technology becomes more established.
Q: Are metal powder engines more reliable?
A: Metal powders offer the potential for improved wear resistance and dimensional accuracy, which can contribute to increased engine reliability. However, the overall reliability depends on various factors like material selection, component design, and manufacturing processes.
Q: Can metal powders be used in all engine components?
A: Not yet. While there’s ongoing development, current limitations exist in terms of material availability, part size restrictions, and cost considerations.
Share On
MET3DP Technology Co., LTD is a leading provider of additive manufacturing solutions headquartered in Qingdao, China. Our company specializes in 3D printing equipment and high-performance metal powders for industrial applications.
Inquiry to get best price and customized Solution for your business!
Related Articles
About Met3DP
Recent Update
Our Product
CONTACT US
Any questions? Send us message now! We’ll serve your request with a whole team after receiving your message.
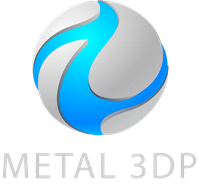
Metal Powders for 3D Printing and Additive Manufacturing