metal powder for semiconductor
Table of Contents
Metal powders play a critical role in the intricate dance of semiconductor fabrication. They act as the building blocks for various thin films and coatings, meticulously deposited onto the semiconductor substrate to create the electrical pathways that power our devices.
Here, we delve into the fascinating world of metal powder for semiconductor, exploring their types, properties, applications, and the intricate details that make them indispensable.
Different Metal Powders
The world of metal powders for semiconductors is a diverse one. Each type offers unique properties that cater to specific needs in the fabrication process. Let’s meet some of the key players:
1. Aluminum (Al) Powder:
- Description: A highly versatile and conductive metal powder, aluminum finds extensive use in metallization layers and bonding wires.
- Properties: Excellent electrical conductivity, good adhesion to other materials, formability.
- Applications: Metallization layers for integrated circuits (ICs), bonding wires for chip packaging.
2. Tungsten (W) Powder:
- Description: Renowned for its exceptional thermal stability and high melting point, tungsten powder is a champion for high-performance applications.
- Properties: Extremely high melting point, outstanding thermal stability, good electrical conductivity.
- Applications: Diffusion barriers, gate electrodes, vias, plugs in advanced ICs.
3. Tantalum (Ta) Powder:
- Description: A valuable asset for capacitors, tantalum powder offers high permittivity and excellent corrosion resistance.
- Properties: High permittivity, exceptional corrosion resistance, good thermal stability.
- Applications: Tantalum capacitors for power management and filtering in electronic devices.
4. Titanium (Ti) Powder:
- Description: Offering a robust combination of strength, corrosion resistance, and biocompatibility, titanium powder finds applications beyond just semiconductors.
- Properties: High strength-to-weight ratio, excellent corrosion resistance, biocompatible.
- Applications: Diffusion barriers, metal gates, electrodes in advanced ICs, biocompatible medical implants (although a different form than used in semiconductors).
5. Copper (Cu) Powder:
- Description: A highly conductive and cost-effective choice, copper powder is widely used for electrical interconnects.
- Properties: Excellent electrical conductivity, good thermal conductivity, cost-effective.
- Applications: Electrical interconnects, bonding wires, heat sinks in ICs.
6. Nickel (Ni) Powder:
- Description: Valued for its good electrical conductivity and magnetic properties, nickel powder caters to diverse applications.
- Properties: Good electrical conductivity, magnetic properties (depending on alloy composition), good thermal stability.
- Applications: Ohmic contacts, metal gates, magnetic random-access memory (MRAM) devices.
7. Cobalt (Co) Powder:
- Description: Often used in alloys, cobalt powder brings its magnetic properties and high melting point to the table.
- Properties: High melting point, magnetic properties (depending on alloy composition), good thermal stability.
- Applications: Magnetic tunnel junctions (MTJs) in MRAM devices, diffusion barriers.
8. Molybdenum (Mo) Powder:
- Description: Offering exceptional high-temperature performance, molybdenum powder is a go-to choice for heat dissipation applications.
- Properties: Very high melting point, excellent thermal stability, good electrical conductivity.
- Applications: Heat sinks, metallization layers for high-power devices.
9. Silver (Ag) Powder:
- Description: The undisputed champion of electrical conductivity, silver powder is used for applications demanding the highest performance.
- Properties: Unmatched electrical conductivity, good thermal conductivity, good solderability.
- Applications: Die attach for high-power devices, conductive pads for flip-chip packaging.
10. Gold (Au) Powder:
- Description: Beyond its luxurious reputation, gold powder offers exceptional corrosion resistance and electrical conductivity.
- Properties: Excellent electrical conductivity, superior corrosion resistance, good solderability.
- Applications: Bonding wires for high-reliability applications, electrical contacts in specialty devices.
This list just scratches the surface of the metal powder universe for semiconductors. Material scientists are constantly innovating and developing new alloys and composite powders to meet the ever-evolving demands of the industry.
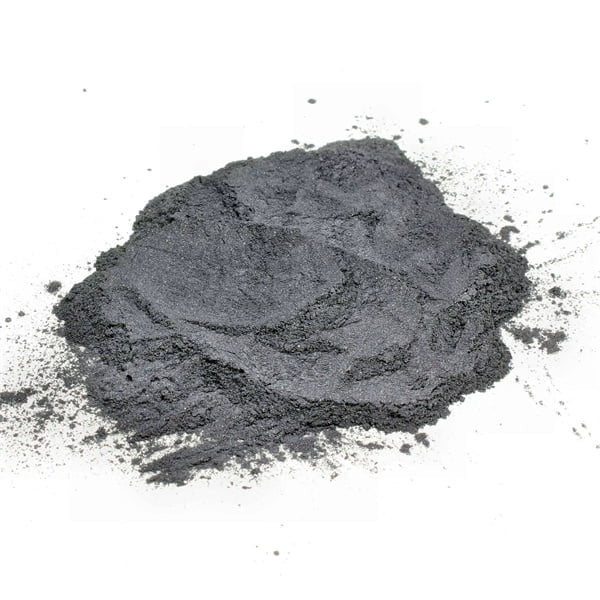
Characteristics of metal powder for semiconductor
Just like superheroes have unique powers, each metal powder boasts a distinct set of properties that make it perfect for specific roles in the semiconductor arena. Let’s delve deeper into these characteristics:
Physical Properties:
- Particle size and distribution: This plays a crucial role in film thickness, uniformity, and electrical performance. Ideally, the particles should be uniform in size and spherical in shape to ensure smooth and densely packed films.
- Surface area: A high surface area can enhance the reactivity and adhesion of the powder during deposition processes.
- Density: The density of the metal powder affects the final density of the deposited film, which in turn impacts electrical conductivity and other properties.
Chemical Properties:
- Purity: Impurities in the metal powder can significantly affect the electrical properties of the final film. High purity (often exceeding 99.5%) is essential for optimal performance.
- Oxidation: Some metals readily react with oxygen to form oxides. Strict control over oxygen content is crucial to avoid the formation of insulating oxides that can impede electrical performance.
Deposition Characteristics:
- Melting point: The melting point of the powder determines the compatibility with various deposition techniques. For instance, techniques like sputtering might require lower melting point powders compared to processes like sintering.
- Flowability: The ability of the powder to flow freely is essential for uniform deposition during processes like screen printing.
- Sintering behavior: Sintering is a process where the powder particles are bonded together to form a solid film. The sintering behavior of the powder, including the required temperature and time, needs to be carefully considered for optimal film formation.
Material scientists carefully tailor the properties of metal powders through various techniques like inert gas atomization, chemical vapor deposition, and reduction processes. These techniques allow for precise control over particle size, purity, and surface characteristics, ensuring the metal powders meet the demanding specifications of the semiconductor industry.
Applications of Metal Powder for Semiconductor
Metal powders are the invisible workhorses behind the scenes, playing a critical role in various stages of semiconductor fabrication. Here’s a glimpse into their diverse applications:
- Metallization Layers: Metal powders are deposited to create thin films that form the conductive pathways within an integrated circuit. Aluminum (Al) and copper (Cu) are commonly used for their excellent conductivity.
- Bonding Wires: These tiny wires connect the chip to the external package. Gold (Au) and aluminum (Al) are popular choices due to their good conductivity and solderability.
- Diffusion Barriers: Metal powders like titanium (Ti) and tantalum (Ta) are used to create thin layers that prevent unwanted diffusion of atoms between different parts of the device.
- Gates and Electrodes: These control the flow of current in a transistor. Tungsten (W) and nickel (Ni) powders are often used due to their good electrical properties.
- Capacitors: Tantalum (Ta) powder is a key ingredient in tantalum capacitors, which are used for power management and filtering in electronic devices.
- Heat dissipation: Molybdenum (Mo) powder with its exceptional thermal properties finds application in heat sinks that dissipate heat generated by high-power devices.
The specific choice of metal powder depends on the desired properties for the final film. For instance, when creating metallization layers, factors like conductivity, adhesion, and cost come into play. Aluminum might be a cost-effective option, while silver offers superior conductivity for high-performance applications.
Specifications, Sizes, and Grades
Metal Powder Specifications, Sizes, and Grades
Metal Powder | Typical Particle Size (µm) | Purity (%) | Grades |
---|---|---|---|
Aluminum (Al) | 0.5 – 10 | >99.5 | High purity (electrical grade), ultra-high purity |
Tungsten (W) | 0.5 – 15 | >99.9 | High purity (electronic grade), doping grades |
Tantalum (Ta) | 1 – 20 | >99.5 | Electrolytic grade, capacitor grade |
Titanium (Ti) | 1 – 50 | >99.2 | Commercially pure (CP) grade, various alloy grades |
Copper (Cu) | 1 – 50 | >99.5 | Electrolytic tough pitch (ETP) grade, oxygen-free electronic (OFE) grade |
Nickel (Ni) | 1 – 10 | >99.5 | Reduced carbonyl grade, electrolytic grade |
Molybdenum (Mo) | 2 – 20 | >99.5 | High purity (electronic grade), carbide grades |
Silver (Ag) | 1 – 10 | >99.9 | High purity (electronic grade) |
Gold (Au) | 1 – 10 | >99.99 | High purity (electronic grade) |
Key Considerations:
- Particle size: Affects film thickness, uniformity, and electrical performance. Smaller particles generally create denser and more conductive films.
- Purity: High purity minimizes impurities that can degrade electrical properties.
- Grades: Different grades cater to specific applications. For example, electrolytic copper might be suitable for some applications, while oxygen-free electronic copper is preferred for high-performance devices.
Pros and Cons of Metal Powders for Semiconductors
Just like any material, metal powders for semiconductors come with their own set of advantages and limitations. Let’s weigh the pros and cons:
Advantages:
- High Purity: Metal powders can be achieved with exceptionally high purity levels, leading to superior electrical performance of the final films.
- Tailored Properties: Material scientists can precisely control the properties of metal powders through various processes, ensuring they meet the specific needs of the application.
- Versatility: The wide variety of metal powders available offers a material solution for diverse applications within a semiconductor device.
- Cost-Effectiveness: Some metal powders, like aluminum, offer a cost-effective option for specific applications.
Disadvantages:
- Oxidation: Certain metal powders are prone to oxidation, requiring careful handling and storage to avoid the formation of insulating oxides.
- Agglomeration: Over time, metal powders can clump together, affecting their flowability and deposition characteristics. Special handling techniques might be required to prevent this.
- Environmental Concerns: The production of some metal powders can involve hazardous chemicals or energy-intensive processes, requiring proper environmental controls.
Making the Right Choice:
Selecting the right metal powder for a particular application requires careful consideration of the desired properties, cost, and potential limitations. Material scientists and engineers work together to find the optimal balance between these factors to ensure successful semiconductor fabrication.
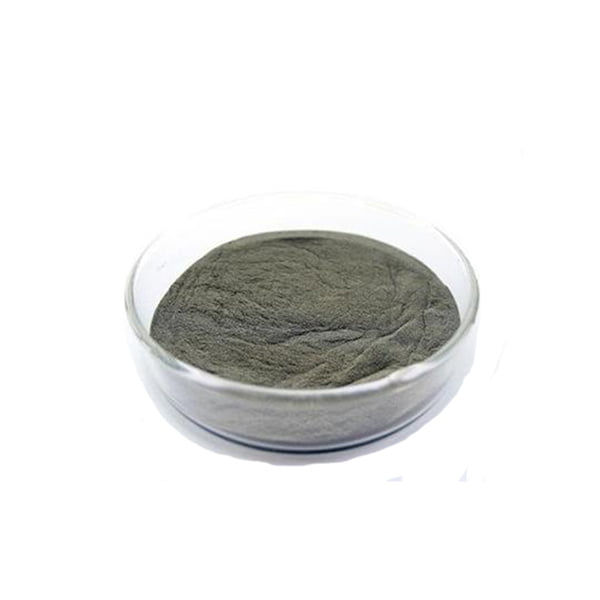
Supplier of metal powder for semiconductor
Metal Powder Suppliers:
Here’s a glimpse into some of the leading suppliers of metal powders for the semiconductor industry:
- American Elements: Offers a wide range of high-purity metal powders, including aluminum, tungsten, and tantalum.
- Umicore: A global leader in specialty materials, including high-purity metal powders for electronics applications.
- Sandvik Hyperion: Provides metal powders for various industries, including the semiconductor sector.
- Höganäs AB: A Swedish manufacturer known for its high-quality metal powders for additive manufacturing and other applications.
- JX Nippon Mining & Metals Corporation: A Japanese multinational that produces various metal powders, including those for electronics.
Pricing Punchline:
The pricing of metal powders can vary depending on the specific metal, purity level, particle size, and quantity. Generally, high-purity and finer particle size powders command a premium price.
For the latest pricing information, it’s recommended to consult directly with metal powder suppliers.
FAQ
Q: What are the different methods used to deposit metal powders in semiconductor fabrication?
A: Several techniques are used, including:
- Sputtering: A physical vapor deposition (PVD) technique where metal atoms are ejected from a target and deposited onto the substrate.
- Evaporation: A PVD technique where metal atoms are vaporized from a source and deposited onto the substrate.
- Electroplating: An electrochemical process where metal ions are deposited onto a conductive substrate from an electrolytic solution.
- Screen printing: A technique where a metal powder paste is forced through a stencil to create a patterned film on the substrate.
Q: How are metal powders stored to prevent degradation?
A: Metal powders are often stored in inert gas environments like argon or nitrogen to minimize oxidation. Moisture control is also crucial to prevent the formation of oxides or hydroxides.
Q: Are there any emerging trends in metal powders for semiconductors?
A: Yes, there’s ongoing research in developing:
- Nanoparticles: Metal nanoparticles offer unique properties for next-generation devices.
- Composite powders: Combining different metal powders or incorporating dopant elements can create powders with tailored properties for specific applications.
Share On
MET3DP Technology Co., LTD is a leading provider of additive manufacturing solutions headquartered in Qingdao, China. Our company specializes in 3D printing equipment and high-performance metal powders for industrial applications.
Inquiry to get best price and customized Solution for your business!
Related Articles
About Met3DP
Recent Update
Our Product
CONTACT US
Any questions? Send us message now! We’ll serve your request with a whole team after receiving your message.
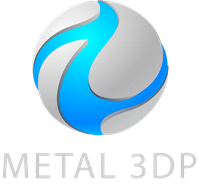
Metal Powders for 3D Printing and Additive Manufacturing