Metal Powder Printers
Table of Contents
Metal powder printer, also known as metal 3D printers or metal additive manufacturing systems, are advanced machines that create three-dimensional objects by fusing together layers of metal powder. These printers have revolutionized the manufacturing industry, enabling the production of complex geometries, customized parts, and intricate designs that would be difficult or impossible to create using traditional manufacturing methods.
Overview of Metal Powder Printers
Metal powder printers work by spreading thin layers of metal powder onto a build platform and selectively melting or fusing the powder particles together using a high-energy source, such as a laser or an electron beam. This process is repeated layer by layer until the desired object is formed. The unfused powder acts as a support material, allowing for the creation of intricate geometries and overhanging structures.
Printer Type | Powder Fusion Method | Materials |
---|---|---|
Laser Powder Bed Fusion (LPBF) | High-power laser beam | Stainless steels, tool steels, aluminum alloys, titanium alloys, nickel alloys, cobalt-chromium alloys |
Electron Beam Melting (EBM) | Electron beam | Titanium alloys, cobalt-chromium alloys, nickel alloys |
Binder Jetting | Liquid binder | Stainless steels, tool steels, aluminum alloys, inconel, tungsten carbides |
These printers offer several advantages over traditional manufacturing methods, including the ability to create complex geometries, reduce material waste, and enable mass customization. However, they also have limitations, such as higher costs, slower production rates, and potential porosity or surface roughness issues.
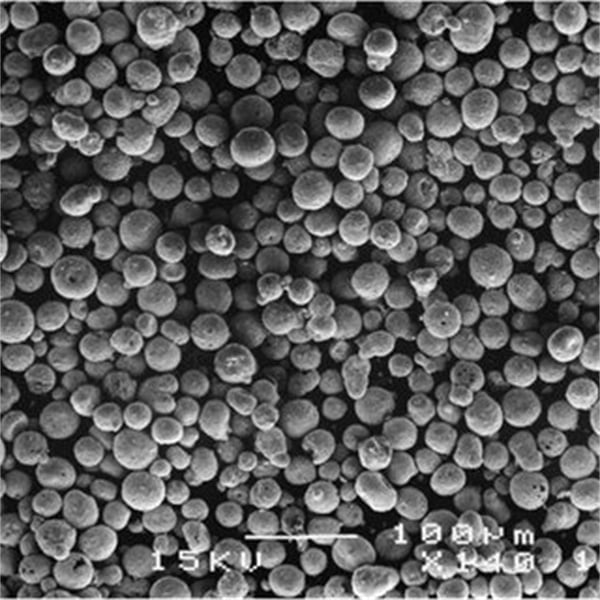
Metal Powder Printer Composition and Properties
Metal powder printers consist of several key components that work together to create the final product:
Component | Description |
---|---|
Build Chamber | An enclosed area where the printing process takes place, often with controlled atmospheric conditions. |
Powder Delivery System | Mechanisms for spreading and distributing the metal powder evenly across the build platform. |
Energy Source | High-energy sources like lasers or electron beams used to selectively melt or fuse the metal powder. |
Control System | Computer software and hardware for controlling the printing process, managing parameters, and generating the desired geometry. |
Post-Processing Equipment | Additional equipment for heat treatment, surface finishing, or removing support structures. |
The properties of the printed parts depend on various factors, including the metal powder material, printing parameters, and post-processing techniques.
Industrial Applications of Metal Powder Printers
Metal powder printers have found widespread applications across various industries due to their ability to create complex and customized parts. Some of the key applications include:
Industry | Applications |
---|---|
Aerospace | Lightweight structural components, engine parts, heat exchangers |
Automotive | Functional prototypes, production parts, tooling inserts |
Medical | Implants, prosthetics, surgical instruments |
Energy | Turbine blades, fuel nozzles, heat exchangers |
Tooling | Injection molds, dies, fixtures |
Specifications and Standards for Metal Powder Printers
Metal powder printers and their components are subject to various industry standards and specifications to ensure consistent performance, quality, and safety. These standards cover aspects such as materials, processes, testing, and certification.
Standard/Specification | Description |
---|---|
ASTM F3055 | Standard specification for additive manufacturing nickel alloy (UNS N07718) with powder bed fusion |
ISO/ASTM 52900 | Standard terminology for additive manufacturing – general principles and terminology |
ISO/ASTM 52901 | Standard guide for additive manufacturing – general principles and requirements |
ISO/ASTM 52911 | Standard practice for finishing metal powder bed fusion components |
Suppliers and Pricing for Metal Powder Printers
Metal powder printers are manufactured by several leading companies, each offering a range of models with varying capabilities and price points. The cost of these printers can vary significantly depending on the technology, build volume, materials, and additional features.
Supplier | Printer Model | Approximate Price Range |
---|---|---|
EOS | M 290, M 300-4 | $500,000 – $1,500,000 |
SLM Solutions | SLM 280, SLM 500 | $500,000 – $1,000,000 |
Concept Laser | M2 Cusing, X LINE | $500,000 – $1,500,000 |
3D Systems | DMP Flex 350 Dual | $500,000 – $1,000,000 |
Renishaw | RenAM 500Q | $500,000 – $800,000 |
It’s important to note that the pricing can vary based on factors such as optional features, support and maintenance contracts, and regional markets.
Pros and Cons of Metal Powder Printers
Like any technology, metal powder printers have both advantages and limitations. Understanding these factors can help organizations make informed decisions about whether to adopt this technology and how to best utilize it.
Pros | Cons |
---|---|
Create complex geometries and intricate designs | High initial investment and operating costs |
Enable mass customization and rapid prototyping | Slower production rates compared to traditional manufacturing |
Reduce material waste and lead times | Potential for porosity, surface roughness, or residual stresses |
Produce lightweight and high-strength parts | Limited range of compatible materials |
Excellent for small-batch or on-demand production | Post-processing requirements (heat treatment, surface finishing) |
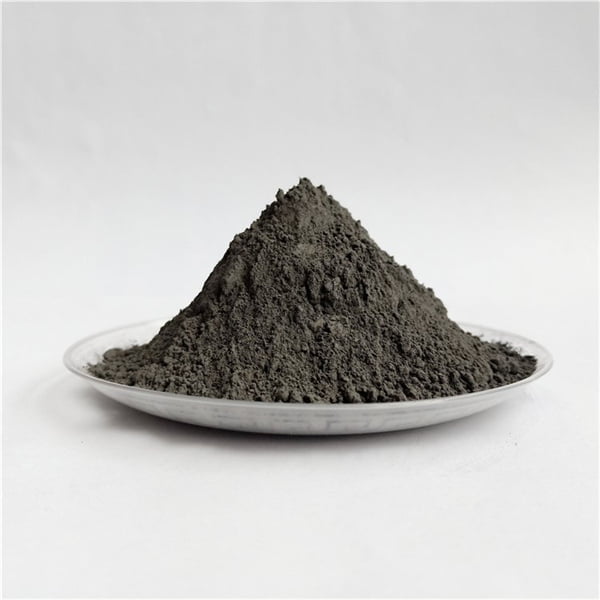
FAQs
Question | Answer |
---|---|
What metals can be used in metal powder printers? | Common materials include stainless steels, tool steels, aluminum alloys, titanium alloys, nickel alloys, and cobalt-chromium alloys. |
How does the surface finish of 3D printed metal parts compare to traditional manufacturing? | Metal 3D printed parts often have a rougher surface finish compared to machined or cast parts, but post-processing techniques like bead blasting, polishing, or machining can improve the surface quality. |
Can metal powder printers produce fully dense parts? | Yes, properly optimized printing parameters and post-processing techniques can produce fully dense parts with mechanical properties comparable to traditionally manufactured parts. |
How does the cost of metal 3D printing compare to traditional manufacturing? | For small production runs or complex geometries, metal 3D printing can be more cost-effective due to reduced material waste and tooling costs. However, for larger production volumes, traditional manufacturing methods may be more economical. |
What are the typical build volumes of metal powder printers? | Build volumes can range from a few cubic inches for desktop-sized printers to several cubic feet for large industrial machines. |
How are metal powder printers different from traditional manufacturing methods? | Metal 3D printing is an additive manufacturing process that builds parts layer by layer, allowing for greater design freedom and complexity compared to subtractive (e.g., machining) or formative (e.g., casting) manufacturing methods. |
Share On
MET3DP Technology Co., LTD is a leading provider of additive manufacturing solutions headquartered in Qingdao, China. Our company specializes in 3D printing equipment and high-performance metal powders for industrial applications.
Inquiry to get best price and customized Solution for your business!
Related Articles
About Met3DP
Recent Update
Our Product
CONTACT US
Any questions? Send us message now! We’ll serve your request with a whole team after receiving your message.
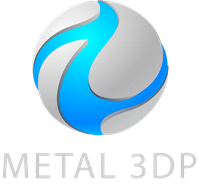
Metal Powders for 3D Printing and Additive Manufacturing