Metal Powder Suppliers
Table of Contents
Metal powders are widely used across additive manufacturing, metal injection molding and other powder metallurgy applications. This article provides an overview of various metal powders, production methods, properties, specifications, applications, pricing, metal powder supplier as well as advantages and limitations of powder-based technologies.
Overview of metal powders
Metal powders processed into end-use components offer benefits like:
- Customized alloys/compositions unattainable via ingot metallurgy
- Intricate, lightweight geometries through additive manufacturing
- Net shape fabrication reducing wastage versus subtractive methods
- Isotropic properties from rapid solidification versus casting
Common metal powders range from stainless steels, tool steels, superalloys to titanium, aluminum, copper and exotic alloys. Production via inert gas atomization, water atomization and plasma rotating electrode process allow tailoring particle size distribution, morphology and microstructure for different applications.
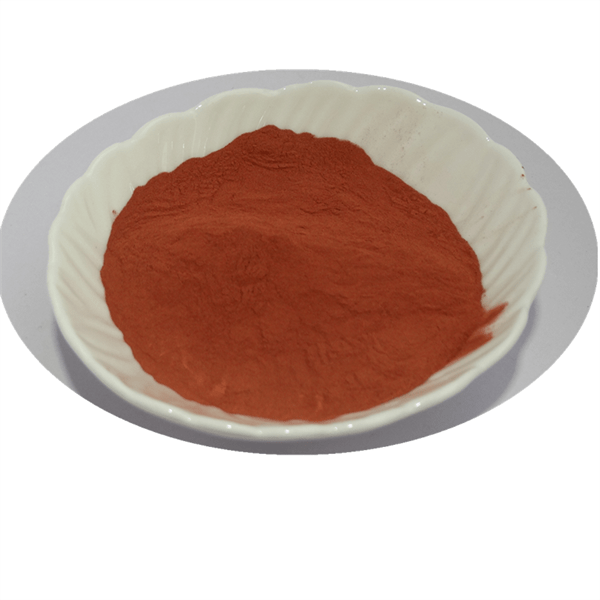
Metal Powder Types
Stainless Steels
Austenitic and martensitic stainless steel powders like 316L, 420, and 17-4PH offer good corrosion resistance and high hardness after heat treatment:
Grade | Properties | Applications |
---|---|---|
316L | Excellent corrosion resistance, great weldability/formability | Pumps, valves, marine hardware |
420 | High hardness, wear resistance | Cutting tools, bearings |
17-4PH | High strength, moderate corrosion resistance, good toughness after aging | Aerospace and industrial components |
Tool Steels
Air-hardening tool steels like H13 and D2 provide very high hardness levels after heat treatment:
Grade | Hardness Range | Uses |
---|---|---|
H13 | 50-55 HRC | Injection molds, dies, tooling |
P20 | 30-40 HRC | Plastic injection molds |
D2 | 60-62 HRC | Cutting tools, forming dies |
Superalloys
Nickel, iron and cobalt-based alloys offer exceptional high temperature strength for extreme environments:
Grade | Max Service Temp | Uses |
---|---|---|
Inconel 718 | 700°C | Aerospace components and systems |
Inconel 625 | 980°C | Aerospace turbines, petrochemical equipment |
Haynes 282 | 870°C | Jet engine parts, land-based turbines |
Cobalt Chrome | 500°C | Medical/dental implants |
Aluminum & Titanium
Light metals like aluminum and titanium alloys enable lightweight structrual parts combined with good corrosion resistance (Ti) and high strength-to-weight ratio:
Grade | Uses |
---|---|
AlSi10Mg | Aerospace and automotive components, prototypes |
Ti-6Al-4V | Aerospace structural parts, biomedical implants |
Copper & Tungsten
Copper offers high thermal and electrical conductivity while tungsten grades provide extreme hardness and density up to 18 g/cc:
Material | Applications |
---|---|
Copper | Heat sinks, electrodes, welding tips |
Tungsten heavy alloys | Radiation shielding, vibration damping |
Exotic Alloys
Advanced grades include precious metals, refractory metals and rare earth permanent magnets:
Grade | Composition | Uses |
---|---|---|
Elgiloy | Co-Cr-Ni + trace elements | Medical devices, fasteners |
Nitinol | Nickel-titanium | Actuators, cryogenic apps |
Neodymium magnets | Nd-Fe-B | Motors, generators, sensors |
These enable specialized electrical, magnetic, thermomechanical and biocompatible properties for niche applications.
Production Methods
Gas atomization is the primary technique for fabricating defined particle size distributions optimized for additive manufacturing, metal injection molding etc. Water atomization serves cost-driven applications like powder injection molding bushings and filters.
Gas Atomization
High pressure inert gas (usually argon or nitrogen) sheers off fine molten metal droplets from the melt stream which rapidly solidify into spherical powders ideal for layer-by-layer fusion. Desired chemistry and microstructure are built into the alloy before atomization. This facilitates high powder purity and consistent composition tailored to part functionality.
Water Atomization
In this process, molten metal stream is disintegrated by high velocity water jets into fine particles which cool rapidly to form irregular shapes. It is a cheaper process useful for high volume applications where loose powder characteristics are acceptable.
Rotating Electrode Process
In this method, an electric arc melts a rotating bar feeding into a plasma torch. The evaporated metal condenses in an inert gas atmosphere and the spinning molten particles form spherical powder. It offers extremely fine control over particle size distribution for niche applications.
Properties and Specifications
Key powder characteristics like particle shape, size distribution, flow rate and apparent density govern performance in downstream processes like additive manufacturing:
Parameter | Typical Range | Significance |
---|---|---|
Particle shape | Spherical preferred | Influences packing density, flowability, spreadability during printing |
Size distribution | 15-45 μm typical | Impacts min feature resolution, surface finish, density |
Flow rate | 25-40 s/50g | Indicates powder fluidization, spreadability, reduced agglomeration |
Apparent density | Up to 65% of theoretical | Needed for high densification during sintering or melting |
Residual carbon | < 0.01% | Determines oxygen/nitrogen pickup affecting mechanicals |
Material test reports from reputed metal powder suppliers showcase detailed characterization data to choose the right grade for intended application and process.
Application Areas
Additive Manufacturing
- Aerospace components – blades, impellers, engine sections
- Medical implants – orthopedic/dental, surgical tools
- Automotive – valves, pistons, manifold
- Industrial tooling – cutting tools, dies, molds
Metal Injection Molding
- Small precision parts – gears, nozzles, fasteners
- Orthopedic screws, knee/hip implants
- Automotive mechanisms – locks, pulleys
Thermal Spray Coatings
- Wear resistant layers – pump shafts, rollers
- Corrosion protection – valves, pipes, vessels
Powder Press and Sinter
- Self-lubricating bearings
- Permanent magnets
- Structural parts via cold/hot isostatic pressing
Tailored powder characteristics enable diverse applications leveraging net shape or near-net shape fabrication.
metal powder supplier
Leading European, Asian and North American suppliers cater to metal powder demand across industries and geographies.
Company | Materials | Capacity | Markets |
---|---|---|---|
Sandvik | Stainless, tool steels, superalloys | 210,000 MT | Europe, Asia |
GKN | Stainless steels, superalloys, Ti alloys | 170,000 MT | Europe, North America |
Praxair | Ti, Ni, Co alloys | 110,000 MT | North/South America |
Hoganas | Tool steels, stainless, low alloy steels | 100,000 MT | Europe, Asia |
Rio Tinto Metal Powders | Aluminum, Ti, intermetallic grades | 75,000 MT | Global |
These companies offer wide capability in atomization processes matched by rigorous in-house quality control on powder characteristics and cleanliness backed by certified test reports on chemistry, particle size distribution, microstructure and batch consistency.
Application experts help customize existing alloys or engineer new grades tailored to customer mechanical property, geometry and functionality needs from prototyping to commercial scale metal powder orders.
Metal Powder Pricing
Material | Price Range |
---|---|
Stainless steel 316L | $5-20/kg |
Maraging steel | $30-60/kg |
Tool steel H13 | $12-30/kg |
Inconel 718 | $50-150/kg |
Titanium Ti-6Al-4V | $100-500/kg |
Prices depend significantly on order volume, quality grade (commercial, aircraft, medical etc.), regional demand dynamics and extent of certification. Large OEM approved customers get much lower pricing of even $30-40/kg for common aerospace superalloys.
Pros and Cons of Powder Metallurgy
Advantages
- Custom alloys/compositions outside conventional ingot metallurgy range
- Complex geometries from additive manufacturing with reduced assembly
- Near net shape fabrication with lower raw material wastage
- Enhanced mechanical properties from rapid solidification
Limitations
- Generally slower production rates than casting or forging
- Additional steps like CIP/HIP needed in AM to improve density
- Reuse of powder can result in changed characteristics
- Requires handling systems to recover/recycle unused powder
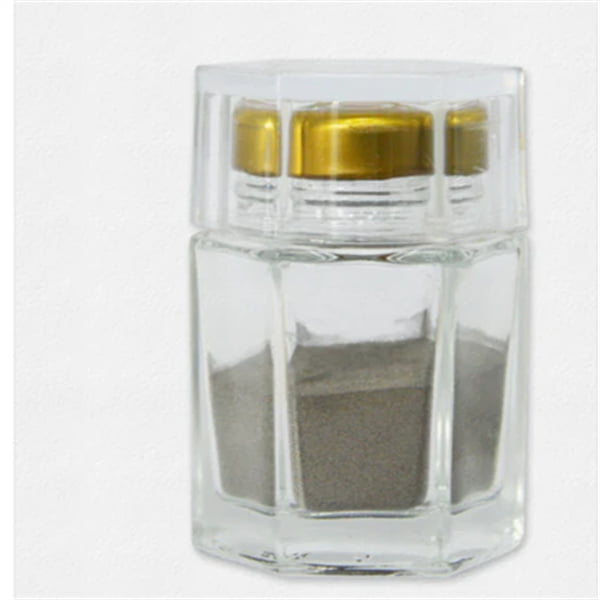
Summary
In summary, key metal powder types span stainless, tool and superalloys plus aluminum/titanium used across additive manufacturing, metal injection molding and thermal spray coatings. Gas, water and plasma atomization enable tailored powder size distribution, shape and microstructure. Leading global suppliers certified quality matched to application requirements in terms of chemistry, particle characteristics and cleanliness. For prototyping or volume production, matching the proper metal powder type to functionality, process and part performance needs drives overall fabrication success.
FAQs
How are metal powders made?
Most commercial powders rely on inert gas atomization or water atomization processes to generate fine spherical particles with tightly controlled size distribution.
What are the main types of metal powders?
Common classifications include stainless steels, tool steels, superalloys, aluminum/titanium alloys, tungsten heavy alloys and precious metals including exotics like Elgiloy, Nitinol etc.
What factors affect metal powder pricing?
Prices depend significantly on volume, extent of certification, regional demand dynamics, raw material costs and alloy composition – exotic superalloys can cost 5-10X stainless steel grades per kilogram.
What are typical sizes for metal powders?
A standard distribution for additive manufacturing lies between 15-45 microns. Water atomized grades can range from 45-150 μm used mainly for pressing and sintering.
What governs choice of metal powders?
Key considerations are part functionality (operating temperature, stresses etc.), fabrication method (casting, MIM, AM), cost targets, extent of post processing and availability in desired product form.
How are metal powders characterized and specified?
Typical parameters provided in material test reports cover powder composition, particle size distribution, morphology (spherical/irregular), flow characteristics, apparent density and residual impurity levels. These govern fitness for service.
Are there standards for metal powders?
ASTM, ASME, MPIF, ISO and equivalent national/regional standards help define specifications for common grades in terms of chemistry, manufacture, sampling procedures, testing methodology, supply condition and quality assurance.
What precautions are necessary when handling metal powders?
Key risks involve flammability and explosion hazards. Inert gas glove boxes, enclosed conveyor/transport systems, grounding, antistatic coatings help safe powder handling alongwith personal protective gear use during extraction and transfer.
Share On
MET3DP Technology Co., LTD is a leading provider of additive manufacturing solutions headquartered in Qingdao, China. Our company specializes in 3D printing equipment and high-performance metal powders for industrial applications.
Inquiry to get best price and customized Solution for your business!
Related Articles
About Met3DP
Recent Update
Our Product
CONTACT US
Any questions? Send us message now! We’ll serve your request with a whole team after receiving your message.
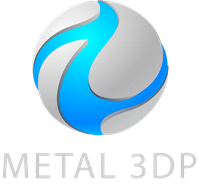
Metal Powders for 3D Printing and Additive Manufacturing