The process steps of MIM Technology
Table of Contents
Have you ever held a tiny gear or a complex watch component and marveled at its intricate details? Chances are, that intricate piece of metal might have been born through a fascinating process called Metal Injection Molding (MIM). MIM isn’t just about creating miniature marvels; it’s a powerful technique for crafting complex, near-net-shaped metal parts with exceptional precision and repeatability.
But how exactly does MIM transform fine metal powder into intricate metal components? Buckle up, because we’re about to embark on a journey into the captivating world of MIM technology, dissecting its four main steps and exploring the world of metal powders that fuel this process.
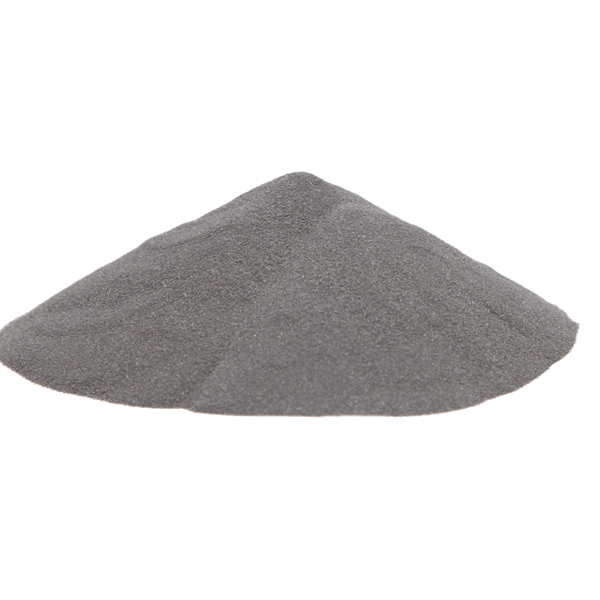
The Four Main Steps of MIM Technology
MIM, like a well-rehearsed play, unfolds in four distinct acts:
- Compounding: Imagine a skilled baker meticulously blending flour, sugar, and other ingredients to create a perfect dough. Similarly, compounding in MIM involves mixing metal powder with a special binder system. These binders, typically consisting of thermoplastics and waxes, act like the glue that holds the metal particles together during the molding process.
Metal Powder Mania:
The heart of MIM lies in the diverse range of metal powders used. Here’s a glimpse into some of the most popular metal powders and their unique properties:
Metal Powder | Composition | Properties | Applications |
---|---|---|---|
316L Stainless Steel | Fe (Iron), Cr (Chromium), Ni (Nickel), Mo (Molybdenum) | Excellent corrosion resistance, good strength and ductility | Medical devices, aerospace components, automotive parts |
17-4 PH Stainless Steel | Fe (Iron), Cr (Chromium), Ni (Nickel), Cu (Copper) | High strength, good ductility, age-hardenable | Gears, fasteners, valves, pump components |
Carbon Steel | Fe (Iron) with controlled amount of Carbon (C) | High strength, low cost, good machinability | Bearings, gears, levers, structural components |
Nickel | Ni (Nickel) | Excellent corrosion resistance, high thermal and electrical conductivity | Electronic components, heat exchangers, chemical processing equipment |
Copper | Cu (Copper) | High electrical and thermal conductivity, good ductility | Electrical connectors, heat sinks, brazing materials |
Titanium | Ti (Titanium) | High strength-to-weight ratio, excellent corrosion resistance | Aerospace components, medical implants, sporting goods |
Inconel 625 | Ni (Nickel), Cr (Chromium), Mo (Molybdenum) | Exceptional high-temperature strength and oxidation resistance | Gas turbine components, rocket engine parts, heat exchangers |
Kovar | Fe (Iron), Ni (Nickel), Co (Cobalt) | Excellent thermal expansion match to glass and ceramics | Electronic packages, optoelectronic devices, vacuum seals |
Tungsten | W (Tungsten) | Very high melting point, excellent wear resistance | Cutting tools, electrodes, heat shields |
Molybdenum | Mo (Molybdenum) | High melting point, good thermal conductivity | Furnace components, electrical contacts, heating elements |
The selection of the right metal powder depends on the desired properties of the final part, such as strength, corrosion resistance, and thermal conductivity.
- Molding: Now, picture the baker pouring the prepared dough into a mold to create the desired shape. In MIM, the compounded feedstock (metal powder and binder mix) is injected into a precisely designed steel mold under high pressure. This injection molding process replicates the intricate details of the mold cavity onto the green part, which is the technical term for the newly formed component before subsequent processing.
- Debinding: Imagine the baker carefully removing the cake from the mold, leaving behind a beautiful creation. Debinding in MIM is a controlled process where the binder is gradually removed from the green part. This can be achieved through thermal or solvent-based techniques. The binder removal is crucial as it allows the metal particles to come closer together, paving the way for the final stage.
- Sintering: The final act of the MIM play is like baking the cake. Sintering involves heating the debindered part in a controlled atmosphere to a temperature close to, but below, the melting point of the metal powder. This high temperature promotes grain growth and bonding between the metal particles, resulting in a near-net-shaped, high-density metal component with excellent mechanical properties.
The Advantages of MIM Technology
MIM offers a compelling set of advantages that make it a highly sought-after manufacturing technique:
- Complex Geometries: Unlike traditional machining, MIM excels at producing intricate shapes with tight tolerances.
- Near-Net-Shape Manufacturing: MIM minimizes the need for extensive post-processing steps compared to traditional machining. The parts emerge from the sintering process close to their final dimensions, reducing material waste and production time.
- High Precision and Repeatability: MIM offers exceptional control over dimensional accuracy and part-to-part consistency. This is particularly beneficial for applications requiring identical components in large quantities.
- Material Versatility: As we explored earlier, MIM boasts compatibility with a wide range of metal powders, enabling the creation of parts with diverse properties to suit specific needs.
- Cost-Effectiveness: For complex, high-volume production runs, MIM can be a cost-effective alternative to traditional machining. The reduced material waste and minimal post-processing contribute to its economic viability.
- Design Freedom: MIM opens doors to innovative designs that might be challenging or impossible to achieve through conventional techniques. This design freedom empowers engineers to push the boundaries of product functionality.
Disadvantages of MIM Technology
While MIM is a powerful technology, it’s not without limitations:
- High Initial Investment: Setting up an MIM production line requires significant upfront costs for equipment and tooling. This can be a barrier for smaller companies or those with limited production volumes.
- Part Size Limitations: The size of MIM parts is generally restricted due to limitations in the injection molding process and potential challenges during debinding and sintering.
- Surface Finish: MIM parts may not achieve the same level of surface finish as those produced through machining or other techniques. However, post-processing techniques like polishing or tumbling can improve the surface aesthetics.
- Design Considerations: The design of MIM parts needs to take into account factors like material properties, draft angles, and potential debinding challenges. Consulting with experienced MIM engineers during the design phase is crucial.
Applications of MIM Technology
MIM finds application in a diverse range of industries due to its ability to produce complex, high-precision metal parts. Here are some prominent examples:
- Medical Devices: MIM is extensively used in the production of intricate medical components like stents, implants, and surgical instruments. The biocompatibility of certain metal powders and the high precision of MIM make it ideal for these critical applications.
- Aerospace & Defense: The aerospace and defense industries leverage MIM for components requiring high strength-to-weight ratios, excellent heat resistance, and tight tolerances. Examples include jet engine components, missile parts, and firearm components.
- Automotive: MIM is increasingly used in the automotive industry for the production of complex gears, transmission parts, and fuel system components. The near-net-shape capability and material versatility of MIM contribute to its growing adoption in this sector.
- Electronics: MIM plays a role in the creation of miniature electronic components with intricate features, such as connectors, housings, and heat sinks. The high conductivity and dimensional accuracy achievable with MIM make it suitable for these applications.
- Consumer Goods: From watch components to sporting goods, MIM is finding its way into a variety of consumer products. The ability to produce complex shapes with good aesthetics makes it an attractive option for certain consumer goods applications.
Considerations for Choosing MIM
MIM is a powerful technology, but it’s not a one-size-fits-all solution. Here are some key factors to consider when deciding if MIM is the right choice for your application:
- Part Complexity: If your design involves intricate shapes, thin walls, or internal features, MIM might be a perfect fit.
- Production Volume: MIM excels in high-volume production runs where its cost-effectiveness shines.
- Material Requirements: Consider the desired properties like strength, corrosion resistance, and thermal conductivity when selecting a metal powder compatible with MIM.
- Part Size: Ensure your part design falls within the size limitations of MIM technology.
- Budget: The upfront investment costs associated with MIM setup need to be factored into your decision.
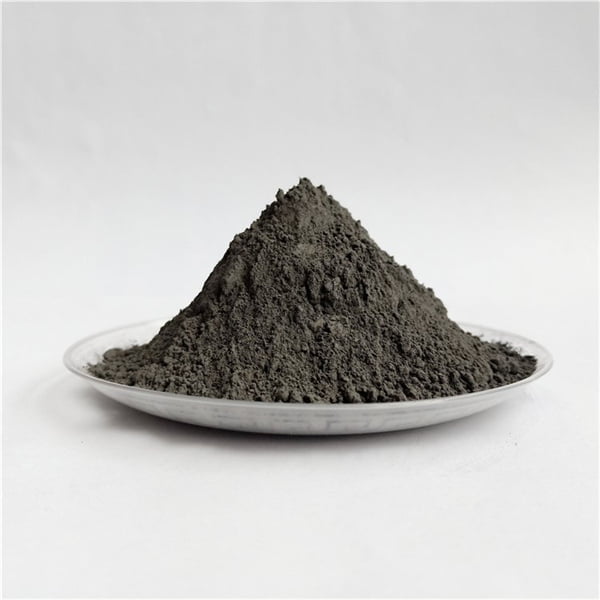
FAQ
Q: What is the difference between MIM and traditional machining?
A: Traditional machining involves removing material from a solid block to create the desired shape. MIM, on the other hand, builds the part layer by layer using metal powder and a binder system. MIM offers advantages for complex geometries, near-net-shape manufacturing, and high-volume production.
Q: What are the different types of metal powders used in MIM?
A: A wide range of metal powders are compatible with MIM, including stainless steels, carbon steels, nickel, copper, titanium, and various alloys. The choice of metal powder depends on the desired properties of the final part.
Q: What are the surface finish limitations of MIM parts?
A: MIM parts may have a slightly rougher surface finish compared to machined components. However, post-processing techniques like polishing, tumbling, or vibrofinishing can significantly improve the surface aesthetics.
Q: Can MIM be used for multi-material parts?
A: MIM is typically limited to single-material parts. However, techniques like metal insert molding can be employed to create hybrid components with metal and plastic elements.
Q: What are the environmental considerations of MIM?
A: The debinding process in MIM can involve solvents that require proper handling and disposal to minimize environmental impact. Manufacturers are increasingly adopting environmentally friendly debinding techniques to address this concern.
Q: What is the future of MIM technology?
A: MIM technology is constantly evolving. Advancements in metal powder development, debinding techniques, and sintering processes are pushing the boundaries of MIM capabilities. We can expect to see the creation of even more complex and high-performance parts using MIM in the future.
Conclusion
MIM technology offers a unique combination of design freedom, high precision, and cost-effectiveness for the production of complex, near-net-shaped metal components. With its growing versatility and continuous advancements, MIM is poised to play an even more significant role in various industries in the years to come. Whether you’re a designer, engineer, or simply curious about innovative manufacturing techniques, understanding MIM’s potential can open doors to exciting possibilities in the world of metal parts creation.
Share On
MET3DP Technology Co., LTD is a leading provider of additive manufacturing solutions headquartered in Qingdao, China. Our company specializes in 3D printing equipment and high-performance metal powders for industrial applications.
Inquiry to get best price and customized Solution for your business!
Related Articles
About Met3DP
Recent Update
Our Product
CONTACT US
Any questions? Send us message now! We’ll serve your request with a whole team after receiving your message.
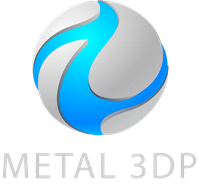
Metal Powders for 3D Printing and Additive Manufacturing