The Application of MIM Technology in Medical Devices
Table of Contents
Imagine a world where intricate medical devices, boasting complex geometries and exceptional strength, can be mass-produced with unparalleled precision. This isn’t science fiction; it’s the reality ushered in by Metal Injection Molding (MIM) technology.
MIM is revolutionizing the medical device industry, offering a unique blend of design flexibility, high-performance materials, and cost-effectiveness. This article delves deep into the wonders of MIM, exploring its applications, material options, and the profound impact it has on various medical instruments.
MIM Technology: A Marriage of Metal and Plastic
At its core, MIM bridges the gap between traditional metalworking and plastic injection molding. Here’s a breakdown of the process:
- Powder Preparation: Metal powders, meticulously chosen for their properties, are mixed with a binder to create a feedstock with a consistency similar to wet sand.
- Molding: The feedstock is injected into a precisely designed mold cavity under high pressure, mimicking the process used for plastic injection molding.
- Debinding: The binder is carefully removed through a thermal or chemical process, leaving behind a fragile metal part.
- Sintering: The remaining metal structure undergoes high-temperature sintering, causing the metal particles to fuse together, resulting in a robust and near-net-shape final product.
This innovative technique unlocks a treasure trove of benefits for medical device manufacturers:
- Design Freedom: MIM allows for the creation of intricate geometries with internal channels, undercuts, and thin walls, features that are often challenging or impossible to achieve with traditional methods like machining or casting.
- Material Versatility: A wide range of metal powders can be used, each offering unique properties tailored for specific applications.
- Mass Production: MIM facilitates the cost-effective production of complex parts in high volumes, making it ideal for high-demand medical devices.
- Exceptional Precision: MIM delivers near-net-shape components with tight tolerances, minimizing the need for post-processing, and ensuring consistent quality.
- Biocompatibility: Certain metal powders used in MIM are biocompatible, making them suitable for implantable medical devices.
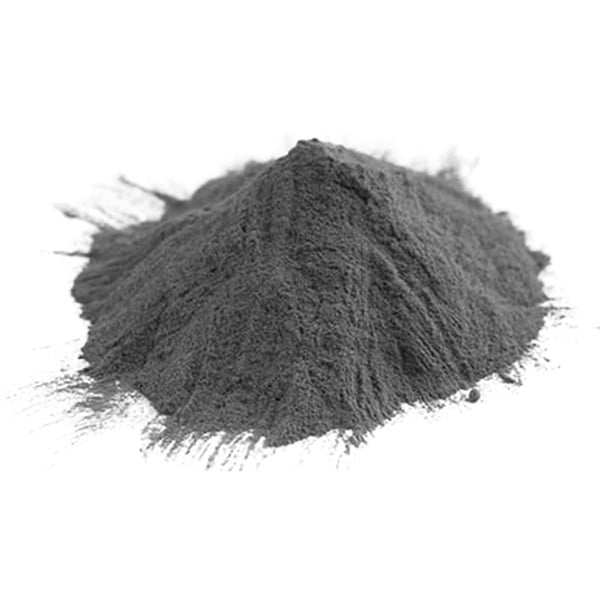
10+ Metal Powders for MIM
The success of MIM hinges on the careful selection of metal powders. Each powder boasts unique characteristics, making it ideal for specific applications. Here’s a glimpse into the diverse metal powder arsenal available for MIM:
1. 316L Stainless Steel: A versatile workhorse, 316L stainless steel offers excellent corrosion resistance, biocompatibility, and good mechanical strength. It’s widely used for bone screws, dental implants, and surgical instruments.
2. 17-4 PH Stainless Steel: This high-strength precipitation-hardening stainless steel delivers exceptional strength and wear resistance, making it a prime candidate for orthopedic implants, joint components, and spinal instrumentation.
3. Cobalt-Chromium (CoCr): Renowned for its biocompatibility and high wear resistance, CoCr is a popular choice for hip and knee replacements, dental implants, and guidewires.
4. Titanium (Ti): Lightweight yet remarkably strong, titanium is a biocompatible metal prized for its excellent osseointegration (bone bonding) properties. It’s extensively used for dental implants, maxillofacial implants, and fracture repair devices.
5. MP35N: This precipitation-hardening nickel-based superalloy boasts exceptional strength, high-temperature performance, and corrosion resistance. It finds application in demanding surgical instruments and minimally invasive surgical (MIS) tools.
6. Inconel 625: Another high-performance nickel-based superalloy, Inconel 625 offers superior strength, creep resistance, and resistance to harsh environments. It’s used for specialized surgical instruments and components exposed to high temperatures.
7. Tantalum (Ta): This biocompatible and corrosion-resistant metal is particularly valuable for its excellent radiolucency, allowing for clear X-ray imaging. It’s used in dental implants, cranial implants, and other applications where X-ray visibility is crucial.
8. Molybdenum (Mo): Molybdenum’s high melting point and excellent thermal conductivity make it a valuable addition to certain MIM powders, enhancing heat dissipation in instruments used for electrosurgery and laser applications.
9. Tungsten (W): Tungsten’s exceptional density and high melting point make it ideal for applications requiring radiation shielding or ballast weights in medical devices.
10. Kovar: This iron-nickel-cobalt alloy boasts a thermal expansion coefficient that closely matches glass, making it perfect for creating glass-to-metal seals in medical devices with integrated glass components.
MIM Technology in Action: Transforming Medical Devices
MIM’s versatility extends across a broad spectrum of medical devices, each benefiting from its unique advantages. Let’s delve into some key applications:
MIM for Implantable Devices:
- Cardiac Stents, Vascular Stents, and Other Implantable Stents: MIM allows for the creation of intricate stent designs with thin walls and precise strut geometries, crucial for optimal blood flow and minimal vessel obstruction. Biocompatible materials like 316L stainless steel and CoCr ensure long-term performance within the body.
- Artificial Joints, Orthopedic Screws, Dental Implants, and Other Implants: MIM facilitates the production of complex orthopedic implants with near-net shapes, eliminating the need for extensive post-processing. Materials like 17-4 PH stainless steel and titanium offer exceptional strength, wear resistance, and osseointegration for long-lasting functionality.
MIM for Surgical Instruments:
- Surgical Knives, Forceps, Scissors, and Other Surgical Instruments: MIM enables the creation of sharp, intricate surgical instruments with exceptional precision and durability. High-performance materials like MP35N and Inconel 625 ensure these instruments can withstand demanding surgical procedures.
MIM for Other Medical Devices:
- Drug Delivery Devices: MIM’s ability to produce intricate components with internal channels makes it ideal for complex drug delivery devices like microneedles and drug-eluting stents.
- Microscopic Components: MIM excels at creating miniature medical devices with tight tolerances, such as components used in minimally invasive surgical tools and diagnostic equipment.
- Biocompatible Housings: MIM allows for the production of biocompatible housings for implantable devices like pacemakers and defibrillators, offering a combination of strength, biocompatibility, and design freedom.
Advantages of MIM for Medical Devices:
- Improved Functionality: MIM enables the creation of complex geometries that enhance device performance and functionality compared to traditional manufacturing methods.
- Enhanced Biocompatibility: The selection of biocompatible metal powders allows for the creation of implantable devices that minimize the risk of rejection by the body.
- Cost-Effectiveness: For high-volume production of complex medical devices, MIM offers a cost-effective alternative to traditional methods like machining or casting.
- Reduced Material Waste: MIM minimizes material waste compared to subtractive manufacturing techniques like machining, making it a more sustainable option.
Considerations for Using MIM in Medical Devices:
- Part Complexity: MIM is best suited for parts with intricate geometries and internal features that are challenging to produce with other methods.
- Material Selection: Choosing the appropriate metal powder is crucial to ensure the final device possesses the desired properties for its intended application.
- Surface Finish: While MIM delivers near-net-shape parts, some post-processing may be required to achieve the desired surface finish for specific applications.
MIM vs. Traditional Manufacturing Methods
MIM isn’t without competition. Traditional manufacturing methods like machining, casting, and forging have long dominated the medical device landscape. Here’s a breakdown of how MIM stacks up against these established techniques:
MIM vs. Machining:
- Complexity: MIM excels at producing complex geometries, while machining can be time-consuming and expensive for intricate parts.
- Material Waste: MIM generates minimal material waste compared to machining, which removes excess material to create the desired shape.
- Cost: For high-volume production of complex parts, MIM can be more cost-effective than machining.
MIM vs. Casting:
- Precision: MIM offers greater dimensional accuracy and tighter tolerances compared to casting, which can be prone to variations.
- Surface Finish: MIM parts typically require less post-processing to achieve a desired surface finish compared to castings.
- Material Options: MIM offers a wider variety of metal powder choices compared to the limitations of casting alloys.
MIM vs. Forging:
- Strength: Forging excels at producing high-strength components, but MIM can achieve sufficient strength for many medical device applications.
- Complexity: MIM allows for the creation of intricate geometries, while forging is limited to simpler shapes.
- Cost: For high-volume production of complex parts, MIM can be a more cost-competitive option than forging.
The Future of MIM in Medical Devices
The future of MIM in medical devices is brimming with promise. Here are some exciting trends to watch:
- Hybrid Designs: Imagine a device where the base structure is efficiently manufactured using MIM, and intr intricate details or internal lattices are created using AM. This could lead to lighter yet stronger implants or instruments with improved functionality.
- Multi-Material Parts: MIM excels with metals, while AM allows for a wider range of materials. Combining these techniques could create devices with sections made from different materials, each chosen for its ideal properties in that specific location.
- Faster Prototyping and Development: The combined workflow of MIM for core structures and AM for intricate features could streamline the prototyping process for medical devices, accelerating development and time to market.
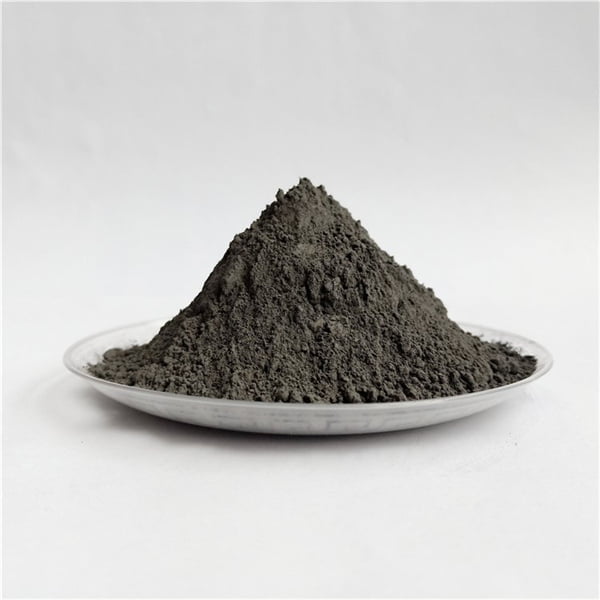
FAQ
Here are some commonly asked questions regarding MIM technology and its applications in medical devices:
Q: What are the limitations of MIM for medical devices?
While MIM offers numerous advantages, it’s essential to consider its limitations:
- Part Size: There are limitations on the size of parts that can be effectively produced using MIM. Very large or bulky components may not be suitable for MIM due to potential challenges with powder flow and sintering uniformity.
- Surface Finish: While MIM delivers near-net-shape parts, achieving a highly polished or ultra-smooth surface finish may require additional post-processing steps.
- Design for Manufacturability (DFM): Designing parts specifically for MIM is crucial to optimize the process and minimize potential issues. Sharp internal corners or extremely thin walls can be challenging to produce with MIM.
- Material Availability: While a wide range of metal powders are available for MIM, some specialized or exotic materials may not be readily obtainable or cost-effective for this process.
Q: How does the cost of MIM compare to other manufacturing methods?
The cost of using MIM depends on several factors, including:
- Part complexity: Complex parts with intricate features will generally cost more to produce with MIM compared to simpler designs.
- Material selection: The chosen metal powder can significantly impact the cost, with some exotic or high-performance powders being more expensive.
- Production volume: MIM is most cost-effective for high-volume production runs. For low-volume applications, other methods like machining might be more suitable.
Overall, MIM can be a very cost-competitive option for high-volume production of complex medical devices compared to traditional methods like machining or casting.
Q: What are the regulatory considerations for using MIM in medical devices?
Medical devices are subject to strict regulatory requirements depending on their classification and intended use. MIM manufacturers and device designers must ensure the MIM process adheres to relevant regulations, which may involve:
- Material characterization: The properties and biocompatibility of the chosen metal powder must be thoroughly characterized and documented.
- Process validation: The MIM process itself needs to be validated to ensure consistent production of high-quality parts that meet the required specifications.
- Quality control: Rigorous quality control procedures must be implemented throughout the MIM process to guarantee the safety and efficacy of the final medical device.
Q: Is MIM a sustainable manufacturing process?
MIM offers several advantages from a sustainability perspective:
- Reduced Material Waste: MIM utilizes a near-net-shape manufacturing approach, minimizing material waste compared to subtractive techniques like machining.
- Material Recycling: Metal powders used in MIM can often be recycled and reused, further reducing environmental impact.
- Energy Efficiency: Compared to some traditional methods like casting, MIM can be more energy-efficient, particularly for high-volume production.
However, the environmental footprint of MIM also depends on factors like the chosen metal powder and the energy source used during the process.
Share On
MET3DP Technology Co., LTD is a leading provider of additive manufacturing solutions headquartered in Qingdao, China. Our company specializes in 3D printing equipment and high-performance metal powders for industrial applications.
Inquiry to get best price and customized Solution for your business!
Related Articles
About Met3DP
Recent Update
Our Product
CONTACT US
Any questions? Send us message now! We’ll serve your request with a whole team after receiving your message.
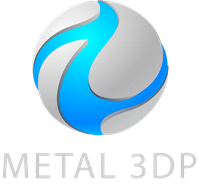
Metal Powders for 3D Printing and Additive Manufacturing