The Application of MIM Technology in Automotive Parts
Table of Contents
Imagine a manufacturing process that seamlessly combines the near-net shape complexity of plastic injection molding with the exceptional strength and durability of metal. This isn’t science fiction; it’s the reality of Metal Injection Molding (MIM), a technology rapidly transforming the automotive industry. Buckle up, gearheads, because we’re about to delve into the fascinating world of MIM and explore its profound impact on crafting the cars of tomorrow.
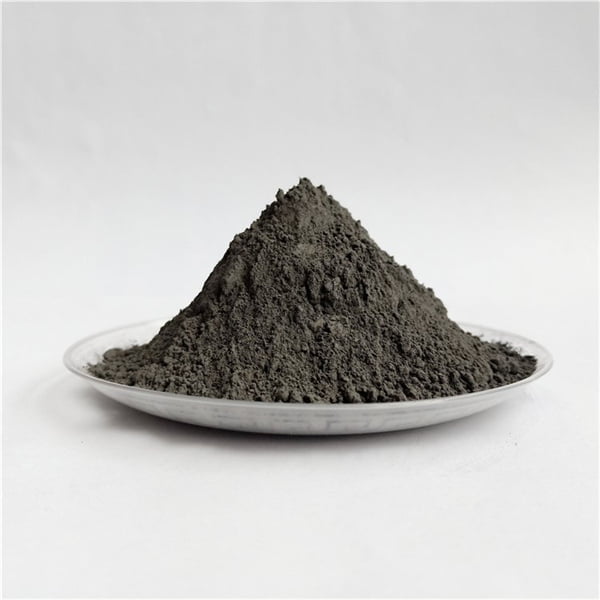
Unveiling the Magic Behind MIM
At its core, MIM revolves around a captivating blend of metal powders and polymer binders. Here’s a breakdown of the key players in this intricate dance:
- Metal Powders: These finely-grained metallic particles, typically ranging from 1 to 150 microns in size, form the foundation of the MIM process. The specific type of metal powder used significantly influences the final part’s properties. Let’s explore a diverse selection of these metallic marvels:
Common Metal Powders for MIM Applications
Metal Powder | Description | Properties | Applications in Automotive Parts |
---|---|---|---|
Low-Alloy Steel | The workhorse of MIM, offering a balance of affordability, strength, and machinability. | High strength, good wear resistance, readily available. | Gears, sprockets, fasteners, engine components. |
Stainless Steel | Renowned for its corrosion resistance, making it ideal for harsh automotive environments. | Excellent corrosion resistance, good strength, biocompatible grades available. | Fuel system components, exhaust parts, sensor housings. |
Nickel-based Alloys | Champions in high-temperature applications, offering exceptional strength and oxidation resistance. | Exceptional strength at elevated temperatures, good corrosion resistance, high cost. | Turbocharger components, valve train parts, exhaust manifolds. |
Aluminum Alloys | Lightweight champions, prized for their strength-to-weight ratio and excellent thermal conductivity. | Lightweight, good strength, good thermal conductivity, more complex debinding process. | Engine components, transmission parts, brake calipers. |
Copper Alloys | Highly conductive superstars, perfect for applications requiring efficient heat transfer. | Excellent electrical and thermal conductivity, good machinability, prone to oxidation. | Electrical connectors, heat sinks, bushings. |
Titanium Alloys | The epitome of strength and lightweight design, but comes at a premium. | Exceptional strength-to-weight ratio, excellent corrosion resistance, biocompatible grades available, high cost. | High-performance engine components, suspension parts. |
Tool Steels | Tough guys for demanding applications, offering superior wear resistance. | Exceptional wear resistance, good hardness, requires post-processing for optimal performance. | Cutting tools, gears, cams, valve components. |
Magnetic Alloys | The masters of magnetism, crucial for components requiring precise magnetic properties. | Tailored magnetic properties, good machinability, requires post-processing for optimal performance. | Sensor components, solenoid cores, rotor shafts. |
Refractory Alloys | Heat shields against the inferno, ideal for withstanding extreme temperatures. | Exceptional high-temperature strength, good oxidation resistance, requires specialized processing. | Engine heat shields, exhaust components, turbocharger parts. |
Precious Metal Alloys | A touch of luxury, used for specialized applications requiring high electrical conductivity or corrosion resistance. | Exceptional electrical conductivity, superior corrosion resistance, very high cost. | Electrical contacts, connectors, sensor housings (limited use due to cost). |
- Polymer Binders: These act as the temporary glue, holding the metal powder particles together during the molding process. After shaping, the binder is removed through a debinding process, leaving behind a near-net shape metal component.
The MIM Manufacturing Marvel
The MIM process can be likened to a meticulously choreographed ballet, with each step contributing to the final masterpiece. Here’s a glimpse into the captivating journey of an automotive part crafted through MIM:
- Mixing and Molding: The metal powder and polymer binder are precisely blended to create a feedstock with optimal flow characteristics. This mixture is then injected into a mold cavity under high pressure, mimicking the familiar process of plastic injection molding.
- Debinding: The magic unfolds! Through a carefully controlled thermal or chemical process, the binder is meticulously removed from the molded part. This leaves behind a fragile, porous metal structure.
- Sintering: Now comes the heat! The debinded part is subjected to high temperatures, typically close to the melting point of the metal powder. This process strengthens the part by causing the metal particles to bond together, creating a near-net shape component with exceptional properties.
- Secondary Operations (Optional): Depending on the specific application requirements, the MIM part may undergo additional processes like machining, heat treatment, or surface finishing to achieve the desired final dimensions, performance characteristics, and aesthetics.
The Symphony of Advantages: Why MIM Reigns Supreme
MIM’s captivating blend of capabilities has earned it a coveted place in the automotive industry’s arsenal. Here’s a harmonious chorus of advantages that make MIM a true game-changer:
- Complex Geometries: Unlike traditional machining, MIM excels at producing intricate shapes with tight tolerances, minimizing the need for multiple components and simplifying assembly processes. Imagine a single MIM gear replacing a complex assembly of machined parts, leading to a lighter, more efficient design.
- Near-Net Shapes: MIM parts emerge close to their final form, requiring minimal secondary machining. This translates to significant cost savings, reduced material waste, and faster production cycles compared to traditional subtractive manufacturing techniques.
- Mass Production Prowess: MIM thrives in high-volume manufacturing environments. Once the mold is established, MIM can churn out parts with exceptional consistency and repeatability, ensuring a steady flow of high-quality components for automotive assembly lines.
- Material Versatility: As we explored earlier, the diverse selection of metal powders available for MIM allows for the creation of parts with a wide range of properties, from the robust strength of steel to the lightweight allure of aluminum. This flexibility empowers engineers to tailor the material to the specific needs of each automotive application.
- Design Freedom: MIM unlocks a world of design possibilities. Forget the limitations of traditional manufacturing; complex internal features, intricate channels, and even weight-saving lattices can all be incorporated into MIM parts, pushing the boundaries of automotive design and functionality.
- Environmental Friendliness: Compared to traditional machining processes that generate significant scrap metal, MIM boasts a more environmentally friendly footprint. With near-net shapes and minimal material waste, MIM contributes to a more sustainable automotive manufacturing ecosystem.
The Counterpoint: Unveiling the Limitations of MIM
While MIM sings a powerful anthem of advantages, it’s essential to acknowledge its limitations to ensure informed decision-making. Here’s a peek at the other side of the coin:
- Molding Costs: The upfront investment in designing and creating MIM molds can be significant. This might be a hurdle for low-volume production runs or prototypes.
- Part Size Constraints: There are limitations to the size and complexity of parts that can be effectively produced using MIM. Very large or extremely intricate parts might be better suited for alternative manufacturing methods.
- Surface Finish: MIM parts may exhibit a slightly rougher surface finish compared to machined components. Post-processing techniques like polishing or plating might be necessary to achieve a desired aesthetic or functional surface finish.
- Material Limitations: While offering a vast array of options, MIM might not be suitable for all desired material properties. For instance, some very high-strength alloys or those requiring specific grain structures might be challenging to achieve through MIM.
A Symphony of Applications
The captivating melody of MIM’s advantages resonates across a wide range of automotive applications. Here are some prominent examples where MIM is rewriting the script for automotive part production:
Engine Components: From intricate valve lifters and lightweight pistons to robust camshafts and durable connecting rods, MIM is revolutionizing the heart of the automobile. Its ability to produce near-net shapes with exceptional strength and wear resistance makes it ideal for these demanding applications.
Transmission Parts: MIM gears, synchronizer rings, and other transmission components are increasingly being crafted using MIM technology. The process delivers the precise tolerances, high strength, and wear resistance required for smooth and efficient power transfer.
Fuel System Components: MIM’s corrosion resistance and ability to handle high pressures make it a perfect fit for fuel injectors, fuel rails, and other components within the automotive fuel system.
Steering and Suspension Systems: MIM is finding its way into steering knuckles, suspension components, and other parts that require a balance of strength, lightweight design, and intricate geometries.
Body and Chassis Components: From lightweight brackets and clips to robust structural components, MIM is gradually making its mark on the body and chassis of automobiles.
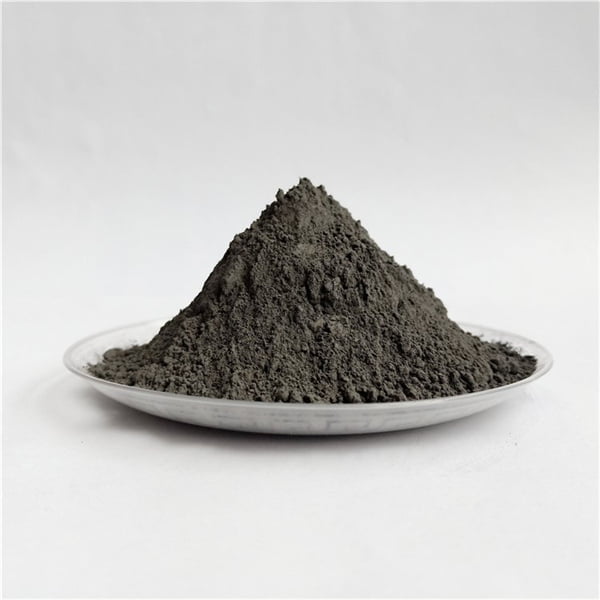
FAQ
Let’s address some frequently asked questions to ensure a complete understanding of MIM’s role in the automotive industry:
Question | Answer |
---|---|
What are the cost implications of MIM compared to traditional manufacturing? | While upfront mold costs can be significant, MIM often leads to lower overall costs for high-volume production runs due to near-net shapes, minimal material waste, and faster production cycles. |
Is MIM suitable for prototyping automotive parts? | MIM can be a viable option for prototyping complex automotive parts, especially when multiple iterations are needed. However, the upfront mold cost needs to be weighed against the required number of prototypes. Additive manufacturing techniques like 3D printing might be a quicker and more cost-effective option for single prototypes. |
How does MIM compare to other metal shaping techniques like casting or forging? | MIM offers several advantages over casting and forging. It excels at producing near-net shapes with tight tolerances, minimizing the need for extensive post-processing. Additionally, MIM allows for the creation of intricate geometries that might be challenging or impossible to achieve through casting or forging. However, casting and forging might be better suited for very large or high-volume production runs of simpler shapes, due to their lower upfront tooling costs. |
What are some future trends for MIM technology in the automotive industry? | As MIM technology continues to evolve, we can expect to see the development of new metal powders with even more specialized properties. Additionally, advancements in debinding and sintering processes will likely lead to the creation of MIM parts with improved surface finishes and even greater dimensional accuracy. The integration of MIM with other additive manufacturing techniques might also unlock new possibilities for complex part production. |
conclusion
MIM’s captivating blend of capabilities positions it as a powerful force in the automotive industry’s ongoing quest for innovation. From crafting intricate engine components to shaping lightweight body parts, MIM is redefining the way automotive parts are designed and manufactured. As the technology continues to mature and expand its reach, we can expect MIM to play an even more prominent role in the symphony of automotive excellence, driving the creation of lighter, stronger, and more efficient vehicles for the road ahead.
Share On
MET3DP Technology Co., LTD is a leading provider of additive manufacturing solutions headquartered in Qingdao, China. Our company specializes in 3D printing equipment and high-performance metal powders for industrial applications.
Inquiry to get best price and customized Solution for your business!
Related Articles
About Met3DP
Recent Update
Our Product
CONTACT US
Any questions? Send us message now! We’ll serve your request with a whole team after receiving your message.
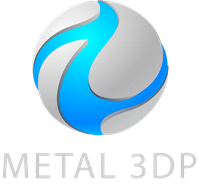
Metal Powders for 3D Printing and Additive Manufacturing