Minor Gas-Trapped Pores Powders
Table of Contents
Metal powders play a crucial role in various industrial applications, from additive manufacturing to powder metallurgy. However, one key characteristic that often affects their performance is the presence of minor gas-trapped pores. These microscopic voids can influence the properties and usability of metal powders. In this comprehensive guide, we’ll delve deep into the world of minor gas-trapped pores in metal powders, exploring their impact, specific metal powder models, applications, and much more.
Overview Of Minor Gas-Trapped Pores In Metal Powders
Metal powders are composed of tiny particles that often contain gas-trapped pores. These pores can be formed during the manufacturing process, particularly when gases are not completely expelled. Understanding these pores’ characteristics and effects is essential for optimizing the performance of metal powders in various applications.
Key Details Of Minor Gas-Trapped Pores In Metal Powders
Aspect | Details |
---|---|
Formation | Gas-trapped pores form during the solidification of metal powders when gases are not fully expelled. |
Impact on Properties | These pores can affect density, mechanical strength, thermal conductivity, and overall performance of the metal powders. |
Detection Methods | Methods like X-ray tomography, scanning electron microscopy (SEM), and laser diffraction are used to detect and analyze these pores. |
Mitigation Techniques | Techniques such as optimizing gas flow during manufacturing, post-processing treatments, and alloying can help reduce the occurrence of these pores. |
Importance in Applications | Understanding and controlling gas-trapped pores is vital for applications requiring high precision and performance, such as aerospace, automotive, and medical industries. |
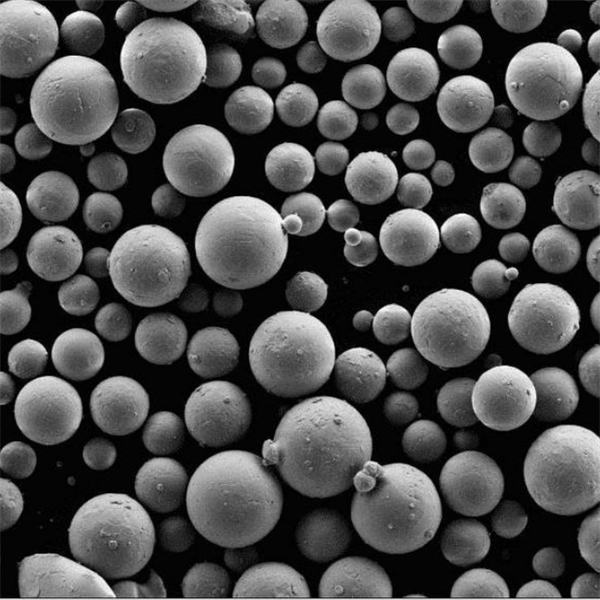
Types Of Metal Powders With Minor Gas-Trapped Pores
When dealing with metal powders, it’s essential to consider specific models that exhibit minor gas-trapped pores. Here are some notable examples:
Metal Powder Model | Description |
---|---|
316L Stainless Steel | Known for its corrosion resistance and excellent mechanical properties, but may exhibit minor gas-trapped pores affecting its density. |
Ti-6Al-4V Titanium Alloy | Widely used in aerospace and medical implants, prone to gas-trapped pores impacting fatigue strength. |
Inconel 718 | A nickel-based superalloy with high strength and corrosion resistance, gas-trapped pores can affect its creep and fatigue properties. |
AlSi10Mg Aluminum Alloy | Common in additive manufacturing, exhibits minor gas-trapped pores which can influence its thermal conductivity and mechanical strength. |
Cobalt-Chrome Alloys | Used in medical implants and dental applications, gas-trapped pores can impact their biocompatibility and mechanical performance. |
Copper Powders | Essential for electrical applications, minor gas-trapped pores can affect their conductivity and thermal properties. |
Tungsten Powders | Known for its high density and melting point, gas-trapped pores can influence its thermal and electrical conductivity. |
Iron Powders | Commonly used in powder metallurgy, gas-trapped pores can affect its magnetic properties and density. |
Nickel Powders | Utilized in batteries and coatings, minor gas-trapped pores can impact its chemical and thermal stability. |
Magnesium Alloys | Lightweight with good mechanical properties, gas-trapped pores can influence its corrosion resistance and strength. |
Composition And Properties Of Metal Powders
The composition and properties of metal powders are critical in determining their performance, especially when minor gas-trapped pores are present.
Metal Powder | Composition | Properties Affected by Gas-Trapped Pores |
---|---|---|
316L Stainless Steel | Iron, Chromium, Nickel, Molybdenum | Density, corrosion resistance, mechanical strength |
Ti-6Al-4V | Titanium, Aluminum, Vanadium | Fatigue strength, tensile strength, corrosion resistance |
Inconel 718 | Nickel, Chromium, Iron | Creep resistance, fatigue strength, high-temperature stability |
AlSi10Mg | Aluminum, Silicon, Magnesium | Thermal conductivity, mechanical strength, ductility |
Cobalt-Chrome | Cobalt, Chromium | Biocompatibility, mechanical strength, wear resistance |
Copper | Copper | Electrical conductivity, thermal conductivity, mechanical strength |
Tungsten | Tungsten | Density, thermal conductivity, electrical conductivity |
Iron | Iron | Magnetic properties, density, mechanical strength |
Nickel | Nickel | Chemical stability, thermal stability, mechanical strength |
Magnesium Alloys | Magnesium, Aluminum, Zinc | Corrosion resistance, mechanical strength, density |
Applications Of Metal Powders With Minor Gas-Trapped Pores
Metal powders with minor gas-trapped pores find use in various industries, each requiring specific properties and performance characteristics.
Application | Metal Powder Models | Impact of Gas-Trapped Pores |
---|---|---|
Additive Manufacturing | 316L Stainless Steel, AlSi10Mg, Ti-6Al-4V | Affects layer adhesion, density, mechanical properties |
Aerospace Components | Ti-6Al-4V, Inconel 718 | Influences fatigue strength, high-temperature performance, and reliability |
Medical Implants | Cobalt-Chrome, Ti-6Al-4V | Impacts biocompatibility, mechanical integrity, and longevity |
Electrical Conductors | Copper, Aluminum | Affects electrical conductivity, thermal management, and mechanical strength |
Automotive Parts | Aluminum Alloys, Magnesium Alloys | Influences weight reduction, mechanical strength, and corrosion resistance |
Tooling and Molds | Tungsten, Inconel 718 | Affects wear resistance, thermal conductivity, and mechanical stability |
Batteries and Energy Storage | Nickel, Cobalt-Chrome | Impacts chemical stability, energy density, and thermal management |
Powder Metallurgy | Iron, Copper | Affects density, mechanical strength, and magnetic properties |
Coatings and Surface Treatments | Nickel, Aluminum, Copper | Influences adhesion, wear resistance, and surface finish |
Biomedical Devices | Titanium Alloys, Cobalt-Chrome | Affects biocompatibility, mechanical performance, and corrosion resistance |
Specifications, Sizes, Grades, And Standards Of Metal Powders
Specifications for metal powders vary based on their intended applications and the presence of gas-trapped pores.
Metal Powder | Specifications | Sizes | Grades | Standards |
---|---|---|---|---|
316L Stainless Steel | ASTM A276, ISO 5832-1 | 15-45 microns | 316L, 1.4404 | ASTM F138, ISO 5832-1 |
Ti-6Al-4V | ASTM B348, ISO 5832-3 | 20-50 microns | Grade 5 | ASTM F136, ISO 5832-3 |
Inconel 718 | ASTM B637, AMS 5662 | 15-53 microns | AMS 5662, AMS 5663 | AMS 5662, ASTM B637 |
AlSi10Mg | ISO 3522 | 20-63 microns | AlSi10Mg | ISO 3522 |
Cobalt-Chrome | ASTM F1537, ISO 5832-4 | 10-45 microns | CoCrMo | ASTM F75, ISO 5832-4 |
Copper | ASTM B170, ASTM B216 | 15-63 microns | Cu-ETP, Cu-DHP | ASTM B170, ASTM B216 |
Tungsten | ASTM B777, ISO 5457 | 5-50 microns | W1, W2 | ASTM B777, ISO 5457 |
Iron | ASTM B783, ISO 10085 | 10-100 microns | Fe-1, Fe-2 | ASTM B783, ISO 10085 |
Nickel | ASTM B160, ISO 6280 | 10-45 microns | Ni-201, Ni-200 | ASTM B160, ISO 6280 |
Magnesium Alloys | ASTM B93, ASTM B403 | 20-100 microns | AZ31B, AZ91D | ASTM B93, ASTM B403 |
Advantages And Disadvantages Of Minor Gas-Trapped Pores In Metal Powders
Understanding the pros and cons of gas-trapped pores helps in making informed decisions about material selection and application.
Aspect | Advantages | Disadvantages |
---|---|---|
Mechanical Properties | Can create lightweight structures with high strength-to-weight ratios. | Reduced density, potential decrease in mechanical strength. |
Thermal Properties | Minor gas-trapped pores can act as insulators, improving thermal performance in some applications. | Decreased thermal conductivity can be detrimental in high-heat applications. |
Manufacturing | Pores can be tailored to achieve desired properties through controlled manufacturing processes. | Difficult to control and predict, leading to variability in properties. |
Cost | Potential cost savings in certain manufacturing processes by reducing material usage. | Increased costs due to additional processing or quality control measures to manage pore content. |
Applications | Beneficial in applications requiring lightweight and thermally insulating materials. | Limiting in high-strength, high-conductivity, or high-precision applications where pore presence is detrimental. |
Mitigation Techniques For Minor Gas-Trapped Pores
Several techniques are employed to mitigate the effects of minor gas-trapped pores in metal powders, ensuring better performance and reliability.
1. Optimizing Gas Flow During Manufacturing
Ensuring proper gas flow during the powder production process helps minimize the occurrence of gas-trapped pores. Techniques like vacuum melting and inert gas atomization are commonly used.
2. Post-Processing Treatments
Processes such as hot isostatic pressing (HIP) can significantly reduce or eliminate gas-trapped pores by applying high pressure and temperature, resulting in a denser and more homogeneous material.
3. Alloying And Additive Elements
Introducing specific alloying elements can help in controlling the formation and distribution of gas-trapped pores. For instance, adding rare earth elements to certain alloys can improve gas solubility and reduce pore formation.
4. Advanced Manufacturing Techniques
Techniques such as laser sintering and electron beam melting allow for better control over the microstructure of metal powders, reducing the likelihood of gas-trapped pores.
Comparative Analysis Of Metal Powders
Comparing different metal powders on various parameters provides insights into their suitability for specific applications.
Parameter | 316L Stainless Steel | Ti-6Al-4V | Inconel 718 | AlSi10Mg | Cobalt-Chrome | Copper | Tungsten | Iron | Nickel | Magnesium Alloys |
---|---|---|---|---|---|---|---|---|---|---|
Density | Moderate | Low | High | Low | High | Moderate | Very High | High | Moderate | Very Low |
Mechanical Strength | High | Very High | Very High | Moderate | Very High | Moderate | High | High | Moderate | Moderate |
Thermal Conductivity | Moderate | Low | Low | High | Moderate | Very High | High | Moderate | Moderate | Moderate |
Corrosion Resistance | Very High | High | Very High | Moderate | High | Low | Very High | Moderate | High | Moderate |
Cost | Moderate | High | Very High | Low | High | Moderate | Very High | Low | High | Low |
Application Suitability | Additive manufacturing, medical | Aerospace, medical | Aerospace, high-temp | Additive manufacturing | Medical, dental | Electrical, thermal | Tooling, high-temp | Powder metallurgy | Batteries, coatings | Automotive, aerospace |
In-Depth Examples And Case Studies
Case Study 1: Ti-6Al-4V In Aerospace
Ti-6Al-4V, commonly used in aerospace applications, often faces challenges due to minor gas-trapped pores. A detailed study showed that optimizing the electron beam melting process significantly reduced the occurrence of these pores, resulting in improved fatigue strength and reliability of the components.
Case Study 2: 316L Stainless Steel In Medical Implants
316L stainless steel is widely used in medical implants due to its excellent corrosion resistance and biocompatibility. However, the presence of gas-trapped pores can affect its mechanical properties. Using hot isostatic pressing (HIP) to treat the powder resulted in a denser material with enhanced mechanical properties, making it more suitable for load-bearing implants.
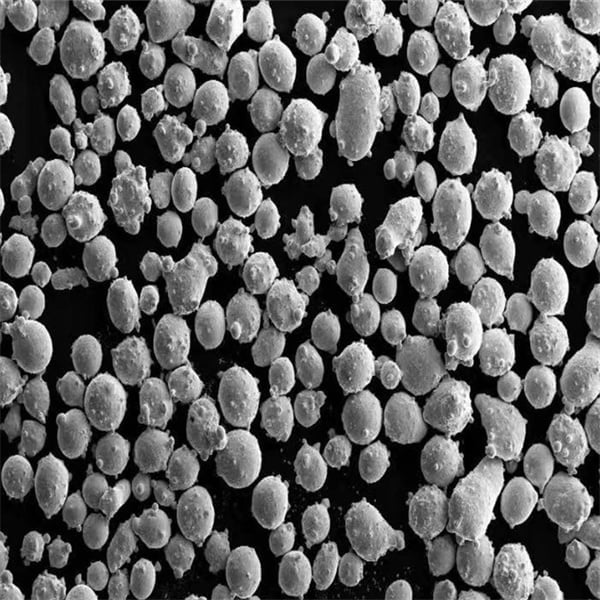
FAQ
Question | Answer |
---|---|
What are minor gas-trapped pores in metal powders? | Minor gas-trapped pores are tiny voids within metal powder particles formed during the manufacturing process when gases are not fully expelled. |
How do gas-trapped pores affect metal powder performance? | They can influence properties like density, mechanical strength, and thermal conductivity, impacting the overall performance of the metal powders. |
Can gas-trapped pores be completely eliminated? | While it is challenging to eliminate them entirely, techniques like hot isostatic pressing (HIP) and optimized manufacturing processes can significantly reduce their presence. |
Which industries are most affected by gas-trapped pores in metal powders? | Aerospace, medical, automotive, and additive manufacturing industries are particularly sensitive to the effects of gas-trapped pores. |
Are there any benefits to having gas-trapped pores in metal powders? | In some cases, they can provide insulation and lightweight properties, beneficial for specific applications. However, these advantages are often context-dependent. |
What methods are used to detect gas-trapped pores in metal powders? | Techniques like X-ray tomography, scanning electron microscopy (SEM), and laser diffraction are commonly used for detecting and analyzing these pores. |
How do suppliers ensure the quality of metal powders with minimal gas-trapped pores? | Suppliers use advanced manufacturing techniques, rigorous quality control measures, and post-processing treatments to minimize the presence of these pores. |
Conclusion
Understanding and managing minor gas-trapped pores in metal powders is crucial for optimizing their performance across various applications. By exploring different metal powder models, their properties, applications, and mitigation techniques, industries can make informed decisions to enhance the reliability and efficiency of their products. Whether it’s in aerospace, medical, or additive manufacturing, controlling these microscopic voids can lead to significant improvements in material performance and application success.
Share On
MET3DP Technology Co., LTD is a leading provider of additive manufacturing solutions headquartered in Qingdao, China. Our company specializes in 3D printing equipment and high-performance metal powders for industrial applications.
Inquiry to get best price and customized Solution for your business!
Related Articles
About Met3DP
Recent Update
Our Product
CONTACT US
Any questions? Send us message now! We’ll serve your request with a whole team after receiving your message.
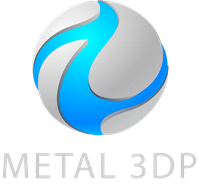
Metal Powders for 3D Printing and Additive Manufacturing