Nickel Alloy Powder
Table of Contents
Nickel alloy powder refers to powder metallurgy forms of various nickel-based alloys. These powders can be processed into finished components using powder consolidation techniques like hot isostatic pressing and metal injection molding. Nickel alloy powders feature high strength, corrosion resistance, high temperature performance, and other specialized properties.
Types of Nickel Alloy Powders
Nickel alloys are complex materials with precise compositions tailored to achieve certain characteristics. The most common nickel alloy powder types include:
Alloy | Nickel Content | Other Alloys | Key Properties |
---|---|---|---|
Nickel-based Superalloys | Over 50% | Chromium, cobalt, molybdenum, tungsten, aluminum, titanium | High strength at high temperatures, corrosion resistance, oxidation resistance |
Stainless Steels | 8-32% | Iron, chromium, molybdenum | Corrosion resistance, high temperature strength |
Low Expansion Alloys | 36-50% | Iron, chromium, cobalt | Extremely low thermal expansion |
Magnetic Alloys | Up to 79% | Iron, molybdenum | High permeability and saturation magnetization |
Resistance Alloys | 10-30% | Chromium, aluminum, copper | High electrical resistivity |
Nickel alloy powders span a wide range compositional varieties depending on the target material properties needed. Tailoring the microstructure is critical.
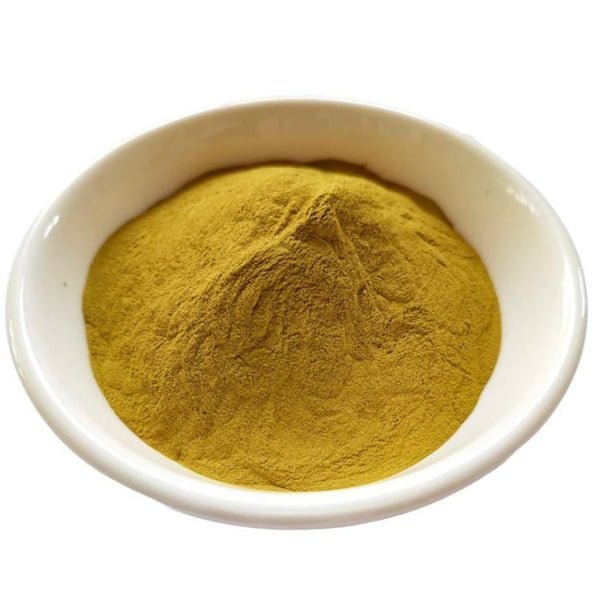
Production Methods for Nickel Alloy Powders
Several techniques can produce nickel alloy powder for industrial consumption:
- Atomization – Melted alloys streamed into high pressure gas flow and rapidly solidified into powder
- Electrolysis – Aqueous electrolytic process to directly obtain powders from plate
- Carbonyl Process – Exposure to carbon monoxide gas at low temperatures/pressures
Atomization is the most common method, allowing higher volumes and cheaper production costs. The table below outlines some pros and cons of each nickel alloy powder production route:
Method | Advantages | Disadvantages |
---|---|---|
Atomization | Higher output rates, lower costs | Less control over powder morphology |
Electrolysis | Good chemical homogeneity | Slow production rate |
Carbonyl | Ultra high purity | Limited alloys, lower density |
Controlling particle size distribution, morphology, oxide content, and microcleanliness are also key quality considerations during manufacturing.
Nickel Alloy Powder Composition
As outlined before, nickel alloys contain nickel plus various other elements to achieve desired attributes. Here are some typical compositions:
Nickel Superalloys
Element | Weight % |
---|---|
Nickel | 50-80% |
Chromium | 10-25% |
Aluminum | 0-6% |
Titanium | 0-5% |
Cobalt | 0-15% |
Molybdenum | 0-12% |
Tungsten | 0-12% |
Iron | 0-10% |
Stainless Steel Powders
Element | Weight % |
---|---|
Nickel | 8-32% |
Chromium | 11-27% |
Molybdenum | 0-6% |
Manganese | 0-2% |
Silicon | 0-1% |
Nitrogen | 0-0.25% |
Iron | Balance |
Low Expansion Alloys
Element | Weight % |
---|---|
Nickel | 34-38% |
Iron | 39-41% |
Chromium | 19-23% |
Cobalt | 12-15% |
The weight percentages can vary quite significantly even within the same alloy family to create versions with specifically targeted attributes.
Characteristics of Nickel Alloy Powders
Key characteristics of nickel alloy powders include:
- Particle Size: Typically 10 – 45 microns
- Morphology: Spherical, satellite, irregular shapes
- Apparent Density: Up to 65% of bulk alloy density
- Flowability: Effects mold filling behavior
- Oxide Content: Affects consolidation and properties
- Microcleanliness: Presence of voids, cracks or inclusions
Controlling these powder characteristics through optimized manufacturing is essential for consistency in downstream powder processing methods.
Applications of Nickel Alloy Powders
Nickel alloy powders are used across industries where high performance materials with specialized properties are needed:
Nickel Superalloys
- Turbine blades
- Rocket engine combustion chambers
- Nuclear reactors
- Chemical processing equipment
Stainless Steel Powders
- Pumps and valves
- Marine components
- Food processing equipment
- Surgical instruments
- Mixing equipment
Low Expansion Alloys
- Precision instruments
- Optical mirrors and mounts
- Electronics packaging
- Aerospace composites
Magnetic Alloys
- Magnet cores
- Magnetic sensors
- Actuators
- Electric motors
Resistance Alloys
- Heating elements
- Resistors
- Thermocouples
- Battery components
Nickel alloy powders enable small, complex components with superior properties compared to wrought forms.
Consolidation Methods for Nickel Alloy Powders
Common techniques to consolidate nickel alloy powders into solid parts include:
- Metal Injection Molding (MIM): Binder mixed with powder, molded, then debinded and sintered
- Hot Isostatic Pressing (HIP): Applying high heat and isostatic pressure to compact powder
- Additive Manufacturing: 3D printing techniques like binder jetting and directed energy deposition
MIM yields high volumes of small, complex geometries at low costs. HIP offers near full density and net shape outcomes. Additive techniques provide the most design freedom.
Each consolidation process has its own set of recommended powder characteristics for optimal results:
Process | Ideal Particle Size | Morphology | Apparent Density |
---|---|---|---|
Metal Injection Molding | 10-20 microns | Spherical | Over 50% |
Hot Isostatic Pressing | 15-45 microns | Irregular | Over 40% |
Additive Manufacturing | 15-45 microns | Spherical | Over 40% |
Specifications for Nickel Alloy Powders
Industrial grade nickel alloy powders must meet composition limits and quality metrics as per various international specifications:
Standard | Description |
---|---|
ASTM B168 | Unalloyed Nickel Powder grades |
AMS 2249 | Nickel Alloy Powder grades |
ISO 4490 | Gas Atomized powders |
ASTM B214 | Classification system |
ISO 22068 | Specifications for MIM powders |
These standards help define chemical makeup limits, acceptable levels of impurities/inclusions, particle size distribution expectations, apparent density ranges, and other critical parameters that significantly influence performance.
Suppliers of Nickel Alloy Powders
Leading global suppliers of various nickel alloy powders include:
Company | Key Products | Production Capacity | Pricing |
---|---|---|---|
VDM Metals | Nickel superalloys, low expansion alloys | 10,000 tons per year | $50+ per kg |
Sandvik Osprey | Stainless steels, maraging steels | 15,000 tons per year | $12-$40 per kg |
Hoganas | Stainless steels, magnetic alloys | 25,000 tons per year | $5-$25 per kg |
AMETEK | Resistance heating alloys | 7,000 tons per year | $30-$100 per kg |
CNPC Powder | Nickel superalloys | 5,000 tons per year | $150+ per kg |
Prices vary based on alloy complexity, powder characteristics, production method used, customization needs, as well as market demand/capacity.
Advantages of Nickel Alloy Powders
Key benefits of using nickel alloy powders instead of wrought products:
- Produce small, complex component geometries
- Near net shape with minimal wastage
- Fine microstructures from rapid solidification
- Components with superior properties
- Allows economic use of expensive materials
- Simplifies processing of hard-to-work alloys
- Components can be mass produced
- Range of consolidation methods
Powder metallurgy techniques make otherwise unmanufacturable designs feasible.
Limitations of Nickel Alloy Powders
Some drawbacks associated with nickel alloy powders:
- Powder production methods can be energy/resource intensive
- Consolidated properties dependent on multiple powder characteristics
- Lower ductility and fracture toughness vs wrought forms
- Limited sizes/volumes compared to cast/wrought methods
- Post-processing may be needed to achieve final part specifications
- Porosity in finished components if improper consolidation
- Needs specialized equipment and expert handling
However, the unique properties and geometrical flexibility provided by nickel alloy powders make them an indispensable advanced material across many technology sectors.
Nickel Alloy Powder Research
Ongoing research aims to expand capabilities and new applications using nickel alloy powders:
- Alloy development – New compositions for enhanced high temperature strength, wear resistance, etc.
- Novel consolidation methods – Microwave sintering, plasma densification, etc. for faster processing
- Nanocrystalline powders – For extremely fine microstructures and advanced properties
- Functionally graded materials – Graded composition/structures within components
- Metal matrix composites – Reinforcing nickel alloys with carbides/ceramics
- Topology optimization – Generating organic, bionic shapes with AM techniques
There are extensive opportunities to stretch limits and pioneer nickel alloy powder technologies through cross-disciplinary R&D. Government entities like the EU and USA have introduced special funding schemes to accelerate development of powder metallurgy innovation centers.
Nickel Alloy Powder Component Design
Several design considerations apply when using nickel alloy powders to manufacture end-use components:
General Design Guidelines
- Optimize wall thickness and avoid dramatic changes
- Include fillets in sharp corners
- Minimize tall, isolated features
- Check minimum draft angles for selected process
- Follow consolidation method’s recommended geometries
- Account for post-processing steps in dimensions
MIM-Specific Advice
- Keep overall length below 50mm
- Use consistent wall thicknesses
- Include filling heads and hot runner gates
- Watch out for steel tool wear with abrasive powders
AM-Specific Pointers
- No geometric constraints! Go wild.
- Utilize lattice structures and organic shapes
- Remember support structure requirements
Component design must account for quirks of powder consolidation techniques as well as intended functionality.
Safety Measures for Nickel Alloy Powders
Handling nickel alloy powders demands certain precautions:
- Use appropriate PPE – gloves, respirators, goggles as needed
- Ensure adequate ventilation and dust collection
- Prevent powder exposure during consolidation
- Follow flammability ratings – some powders are pyrophoric
- Contain spills immediately using appropriate cleanup methods
- Dispose according to local environmental regulations
Any production or research activities with nickel alloy powder should include comprehensive risk assessments and incorporate all necessary systems to mitigate health, explosion, and environmental hazards appropriately. Personnel need sufficient training for safe handling procedures.
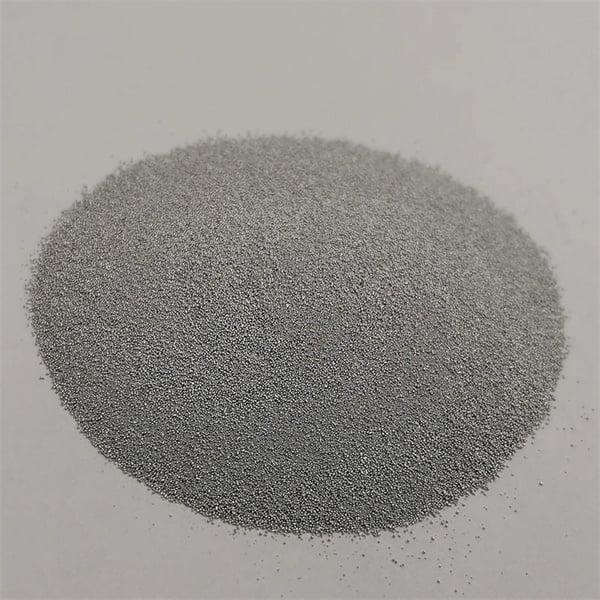
FAQ
Q: What particle size nickel alloy powder is best for additive manufacturing?
A: 15-45 micron spherical powders work well across most AM methods to balance spreadability, flowability and high density consolidation. Finer 10-25 micron powder can resolve finer features if the specific AM process allows it.
Q: Why choose metal injection molding for manufacturing with nickel alloy powders?
A: MIM allows high volume production of complex components with good dimensional accuracy and surface finishes. It maintains the alloy’s inherent properties well. The process is cost effective for small intricate nickel alloy parts.
Q: How are nickel alloy powders made spherical?
A: Inert gas atomization uses rapid solidification principles through smooth liquid breakup mechanisms mediated by gas flow turbulences to create largely spherical powder particle shapes with good flow characteristics.
Q: What are common applications for low expansion nickel alloys?
A: Precision instruments, optical mirrors, electronics packaging, aerospace structures, radiation shields, thermal isolation links, composites with low CTE requirements utilize controlled expansion nickel alloys.
Q: Why is flowability an important nickel alloy powder characteristic?
A: Powders must spread and flow smoothly into mold cavities completely and rapidly to avoid defects. Testing methods like Hall flow rate help quantify this behavior which impacts consolidation and properties.
Share On
MET3DP Technology Co., LTD is a leading provider of additive manufacturing solutions headquartered in Qingdao, China. Our company specializes in 3D printing equipment and high-performance metal powders for industrial applications.
Inquiry to get best price and customized Solution for your business!
Related Articles
About Met3DP
Recent Update
Our Product
CONTACT US
Any questions? Send us message now! We’ll serve your request with a whole team after receiving your message.
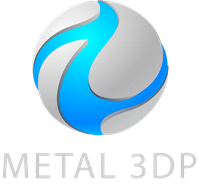
Metal Powders for 3D Printing and Additive Manufacturing