Nickel Aluminide Powder
Table of Contents
Overview of nickel aluminide powder
Nickel aluminide powder is an intermetallic compound composed of nickel (Ni) and aluminum (Al) atoms in an approximate ratio of 1:1. It is characterized by high strength and hardness, excellent corrosion and oxidation resistance at high temperatures, low density, and good wear resistance.
Nickel aluminide powders are produced by gas or water atomization of pre-alloyed ingots containing 35-65% nickel and balanced aluminum. The powders have spherical morphology with smooth surface and controlled particle size distribution.
Key properties and applications of nickel aluminide powder:
Composition:
- Nickel: 35-65%
- Aluminum: Balance
Properties:
- High strength and hardness at room and elevated temperatures
- Low density (5.3 – 6.2 g/cc)
- Good corrosion resistance
- Excellent oxidation resistance up to ~1000°C
- Good thermal conductivity and thermal shock resistance
- Low coefficient of thermal expansion
Applications:
- Powder metallurgy – sintered components
- Thermal spray coatings
- Additive manufacturing
Product forms: Gas atomized spherical powder
Particle sizes: 10 – 150 microns
Standards: ASTM B951, UNS N07041, other custom specifications
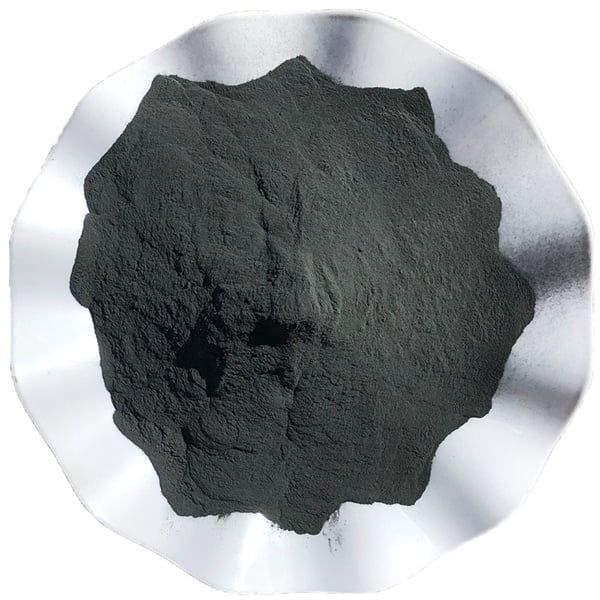
Types of nickel aluminide powder
Nickel aluminide intermetallic compounds exist in several phases with different nickel-aluminum ratios and crystal structures. Common types include:
Type | Composition | Crystal Structure | Key Properties |
---|---|---|---|
NiAl (Stoichiometric) | Nickel 50%, Aluminum 50% | B2 – Cubic | Highest strength and ductility, good oxidation resistance up to 1000°C |
Ni3Al (Nickel-rich) | Nickel 75%, Aluminum 25% | L12 – Cubic | High hardness and brittleness, lower oxidation resistance |
NiAl3 (Aluminum-rich) | Nickel 25%, Aluminum 75% | DO22 – Orthorhombic | Lowest strength and hardness, poor oxidation resistance |
Gas atomized pre-alloyed nickel aluminide powders typically have near-equal Ni:Al ratio to form the NiAl B2 phase in the finished component. Deviations from 1:1 composition produce mixed NiAl + Ni3Al or NiAl + NiAl3 microstructures after sintering/consolidation.
Production Process
Nickel aluminide powders are manufactured by inert gas atomization of induction-melted Ni-Al ingots containing 35-65 wt% Ni. The process involves:
- Melting – Ni and Al are induction melted under inert/vacuum atmosphere
- Atomization – High pressure inert gas (N2, Ar) disintegrates the molten stream into fine droplets
- Solidification – Droplets rapidly solidify into spherical powder particles
- Collection – Atomized powder collected in chamber and classified by particle size
Key process parameters:
- Composition control of master alloy critical
- Induction melting under inert atmosphere to minimize oxygen/nitrogen pickup
- Atomization gas pressure and flowrate affects particle size distribution
- Rapid solidification rate produces fine grained microstructure
Properties of nickel aluminide powder
Nickel aluminide powders and consolidated components exhibit a range of unique properties making them suitable for high performance applications:
Property | NiAl Powder | Sintered NiAl |
---|---|---|
Density (g/cc) | 5.3 – 6.2 | 5.8 – 6.5 |
Melting Point (°C) | 1638 | 1638 |
Strength (MPa) | 200 – 350 | 500 – 1100 |
Hardness (HV) | 300 – 500 | 500 – 800 |
Young’s Modulus (GPa) | 180 – 220 | 160 – 200 |
Compression Strength (MPa) | 500 – 1500 | 1000 – 2500 |
Coefficient of Thermal Expansion (10<sup>-6</sup>/K) | 11 – 13 | 11 – 14 |
Thermal Conductivity (W/m-K) | 20 – 35 | 15 – 30 |
Electrical Resistivity (μΩ-cm) | 125 – 160 | 60 – 100 |
Oxidation Resistance | Excellent up to 1000°C | Excellent up to 1000°C |
Corrosion Resistance | Very Good | Very Good |
The outstanding strength-to-density ratio and high temperature capabilities make these materials attractive alternatives to conventional nickel and cobalt superalloys for aircraft, automotive, space, and energy applications.
Applications of nickel aluminide powder
The unique capabilities of nickel aluminide powders lead to a diverse range of applications across industries:
Powder Metallurgy
- Structural components for aerospace and automotives
- Turbine blades, disks, shafts, cases
- Extreme environment sensors
Thermal Spray Coatings
- Protective coatings for turbine blades and vanes
- Combustion chamber liners
- High temperature oxidation/corrosion resistance
Additive Manufacturing
- Complex geometries not feasible by casting
- Reduced lead times and costs vs machining
- Components for aerospace engines and airframes
Other Applications
- Joining aids, brazements
- Electronic packaging
- Catalysts
Some advantages over competing materials:
Vs Superalloys | Vs Titanium Alloys | Vs Stainless Steels |
---|---|---|
Higher strength-to-weight ratio | Better high temperature strength and creep resistance | Superior oxidation and corrosion resistance at high temperatures |
Excellent oxidation resistance | Lower density | Higher strength and hardness |
Lower component costs | Higher service temperature limits | Higher working temperatures |
Nickel aluminide outperforms these conventional alloys in the harshest environments across critical engineering applications.
Specifications of nickel aluminide powder
Gas atomized nickel aluminide powders are available in various standard and custom specifications tailored to end-use requirements:
Compositions
Alloy | Ni | Al | Other Elements |
---|---|---|---|
NiAl | 50% | 50% | – |
Ni-40Al | 60% | 40% | – |
Ni-45Al | 55% | 45% | – |
Ni-35Al-20Cr | 35% | 35% | 20% Cr |
Particle Size Distributions
Size Range | Typical Uses |
---|---|
<20 μm | additive manufacturing, thermal spray |
20-63 μm | metal injection molding, spraying |
63-150 μm | general powder metallurgy |
Size Specification Standards
- ASTM B214: Standard classification system and size analysis
- DIN 51902: Air jet sieved analysis
- ISO 13318-1: Laser diffraction particle size analysis
Chemical Requirements
- ASTM B951: Base specification for NiAl intermetallic powders
- Other application-specific chemical requirements
Condition Specifications
- ASC PS7: Gas atomized, spherical powders
- Other customized conditions like inert gas atomized, high purity etc.
Suppliers and Pricing of nickel aluminide powder
Some leading global suppliers of nickel aluminide powders include:
Manufacturer | Brand Names | Production Capacity |
---|---|---|
Sandvik | Osprey®, Nypcor® | Medium |
Carpenter Technology | CarTech® | Small |
Hoganas | Hoganas NiAl | Medium |
Praxair | – | Small |
Atlantic Equipment Engineers | Ferro-Term, Pulvimet | Small |
Pricing
- Cost per kg varies from $50 – $300 based on alloy, powder size, quality
- Small lots under 50 kg much more expensive (~2-5x) than bulk volumes
- Reduced pricing for long term supply contracts
- Economy pricing for lower purity developmental grades
Custom Manufacturing
- Several contract manufacturers provide custom atomization services
- MOQ around 500-1000 kg
- Lead times typically 12-16 weeks
Buying Guide
Key considerations when selecting a nickel aluminide powder supplier:
Technical Factors
- Alloy composition suited for application
- Particle shape and size distribution
- Chemical purity and microstructure
- Lot-to-lot consistency
- Quality certifications
Commercial Factors
- Pricing for powder specifications
- Minimum order quantity
- Lead time for orders
- Long term supply agreements
- Change control process
Supplier Capabilities
- Industry experience and reputation
- Technical expertise and customer service
- Production capacity and scalability
- Customization services
- Inventory management and buffer stock
Buyers must evaluate both product quality and business factors when sourcing nickel aluminide powders for critical programs.
nickel aluminide powder Pros vs Cons
Advantages
- High strength-to-weight ratio
- Excellent high temperature properties
- Good environmental resistance
- Near-net-shape manufacturability
- Favorable cost structure
Disadvantages
- Inferior room temperature ductility/toughness
- Susceptibility to environmental embrittlement
- Complex thermo-mechanical processing
- Control of stoichiometry challenging
- Limited suppliers and high MOQs
For extreme temperature applications, nickel aluminide’s capabilities offset the increased processing complexity and expense.
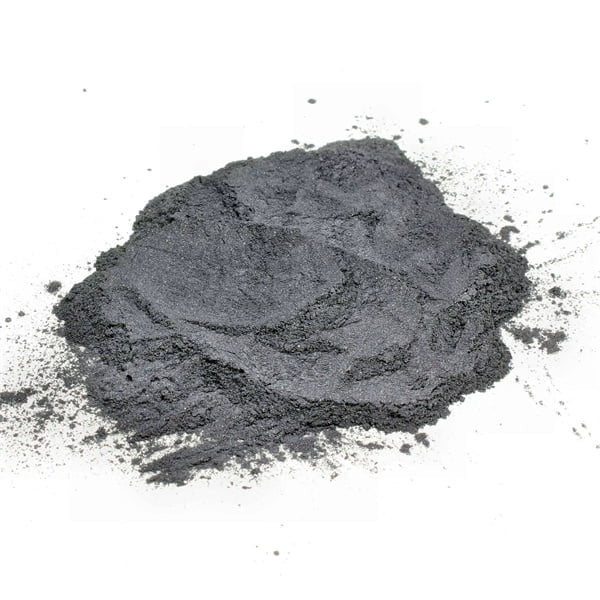
FAQs
Q: What is the chemical formula of nickel aluminide?
A: The stochiometric intermetallic compound has a chemical formula of NiAl. Other nickel-rich and aluminum-rich phases exist with formulas such as Ni3Al and NiAl3.
Q: Is nickel aluminide ferromagnetic?
A: No, unlike pure nickel metal, nickel aluminide has negligible ferromagnetism in its equilibrium microstructure. However, certain non-equilibrium phases formed during processing may exhibit temporary ferromagnetism.
Q: What is the melting point of nickel aluminide?
A: 1638°C is the melting temperature of the equilibrium NiAl phase. The melting point reduces for nickel-rich and aluminum-rich deviations from this composition.
Q: What are common uses of nickel aluminide?
A: Main uses are in structural powder metallurgy parts, additive manufacturing components, thermal spray coatings, catalysts, and electronic packaging. Applications leverage excellent mechanical properties and environmental resistance at high temperatures up to 1000°C.
Q: What industries use nickel aluminide alloys?
A: Aerospace is the largest consumer for aircraft and rocket engine components. Other major industries are power generation, automotive/racing, chemical processing, and oil and gas.
Q: How is nickel aluminide powder made?
A: Gas atomization is the conventional process where the molten NiAl alloy stream is disintegrated by high pressure inert gas jets into fine spherical powder particles that rapidly solidify. Water atomization is also used on a smaller scale.
Q: Why is nickel aluminide not used more widely?
A: Challenges around developing complex thermo-mechanical processing to achieve adequate ductility/toughness and controlling precise stoichiometry have limited more widespread structural adoption. Costs are also higher than competing alloys.
Q: What is the difference between nickel and nickel aluminide?
A: Pure nickel is a metal while nickel aluminide is an intermetallic compound. Nickel is tougher but weaker at high temperatures. Nickel aluminide has excellent elevated temperature strength, hardness and environmental resistance.
Conclusion
With its attractive high temperature capability-to-weight ratio, nickel aluminide enables lighter, higher performing components across demanding applications in aerospace, automotive, energy, and industrial sectors.
Though more costly and challenging to fabricate than traditional alloys, continued research and development is expanding nickel aluminide’s operational envelope – allowing engineers to push limits in next generation engines, airframes, powerplants and processes.
Share On
MET3DP Technology Co., LTD is a leading provider of additive manufacturing solutions headquartered in Qingdao, China. Our company specializes in 3D printing equipment and high-performance metal powders for industrial applications.
Inquiry to get best price and customized Solution for your business!
Related Articles
About Met3DP
Recent Update
Our Product
CONTACT US
Any questions? Send us message now! We’ll serve your request with a whole team after receiving your message.
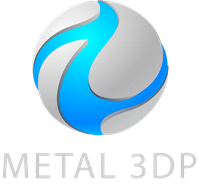
Metal Powders for 3D Printing and Additive Manufacturing