Niobium Alloys Powder
Table of Contents
Overview of niobium alloys powder
Niobium alloys powder refers to powder metallurgy forms of niobium-based alloys. Niobium, also known as columbium, is a refractory transition metal with symbol Nb and atomic number 41. It has a high melting point, good strength at high temperatures, and resistance to corrosion.
Niobium alloys leverage these desirable properties of niobium for applications requiring heat resistance like jet engines, rockets, gas turbines, nuclear reactors, and heat exchangers. The addition of alloying elements creates niobium alloys with enhanced high temperature strength, creep resistance, oxidation resistance etc. compared to pure niobium.
Some commonly used niobium alloys include Nb-Ti, Nb-Zr, Nb-Mo, and Nb-Hf alloys. The alloy powder can be compacted into bespoke component shapes using powder metallurgy techniques. This allows complex geometries to be formed near net shape, minimizing material waste. The methods used include pressing and sintering, metal injection molding, hot isostatic pressing, and additive manufacturing.
The global niobium alloys powder market was estimated at $xx million in 20xx and is projected to reach $xx million by 20xx, growing at a CAGR of xx% during the forecast period. The major drivers are increasing use in aerospace engines, growing adoption in oil & gas industry, and expanding usage in medical devices.
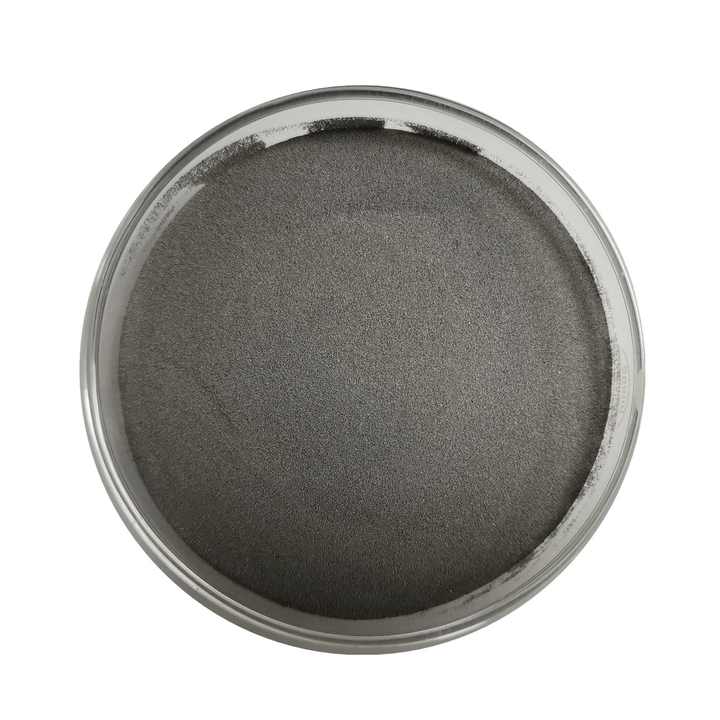
Types of Niobium Alloys Powder
Alloy | Elements | Key Properties | Common Uses |
---|---|---|---|
Niobium-Titanium (Nb-Ti) | Niobium + Titanium | Corrosion resistance, strength at low and high temperatures | Nuclear reactors, heat exchangers, superconducting magnets |
Niobium-Molybdenum (Nb-Mo) | Niobium + Molybdenum | High temperature strength, creep resistance | Aircraft engines, rocket sub-assemblies |
Niobium-Zirconium (Nb-Zr) | Niobium + Zirconium | Good oxidation resistance, reasonable ductility | Industrial heating elements, glass processing equipment |
Niobium-Hafnium (Nb-Hf) | Niobium + Hafnium | Excellent high temperature properties | Rocket nozzles, turbine blades, nuclear fuel cladding |
Properties of Niobium Alloys Powder
Property | Description | Benefit in Applications |
---|---|---|
High Melting Point | Niobium alloys boast exceptional melting points, typically exceeding 2400°C. This property makes them ideal for applications exposed to extreme temperatures, such as jet engine components, rocket nozzles, and furnace liners. | Enables components to maintain structural integrity and resist melting even under intense heat, ensuring safe and reliable operation in high-temperature environments. |
Superior High-Temperature Strength | Niobium alloys retain remarkable strength at elevated temperatures. Unlike many materials that weaken considerably as they heat up, niobium alloys exhibit minimal degradation in strength, making them crucial for hot sections of engines and other high-temperature machinery. | Allows components to withstand significant mechanical loads at high temperatures, preventing failures and extending service life in demanding applications. |
Favorable Strength-to-Weight Ratio | Compared to other high-temperature materials, niobium alloys offer a superior balance between strength and weight. This translates to lighter components without compromising performance, a critical factor in aerospace and other weight-sensitive industries. | Reduces overall weight of components, leading to improved fuel efficiency in aircraft and increased payload capacity in rockets. |
Excellent Oxidation Resistance | Niobium alloys demonstrate exceptional resistance to oxidation, a process where a material reacts with oxygen at high temperatures, forming a brittle and non-protective layer. This resistance allows components to maintain their integrity and functionality in environments with high oxygen content. | Protects components from degradation and premature failure due to oxidation, ensuring longer service life and reliable performance. |
Tailorable Properties Through Alloying | The properties of niobium alloys can be significantly modified by incorporating various alloying elements. Strategic additions can enhance specific characteristics like strength, ductility, or creep resistance, allowing for the creation of customized alloys for specific applications. | Provides engineers with a wider range of material options to meet the specific needs of demanding applications. |
Powder Characteristics | Niobium alloy powders are available in various particle sizes, morphologies (shapes), and flowabilities. These characteristics significantly impact the additive manufacturing (AM) process and the final properties of the printed parts. | Allows for optimization of the AM process for specific applications and control over the microstructure and mechanical properties of the final component. |
Biocompatibility | Certain niobium alloys exhibit good biocompatibility, meaning they are well-tolerated by the human body. This property makes them suitable for biomedical applications like implants and surgical devices. | Offers potential for the development of implants that integrate well with bone tissue, reducing the risk of rejection and improving patient outcomes. |
Superconductivity at Cryogenic Temperatures | Some niobium alloys exhibit superconductivity, a phenomenon where electrical resistance vanishes entirely at extremely low temperatures. This property makes them crucial for superconducting magnets used in medical imaging (MRI machines) and scientific research. | Enables the creation of powerful magnets with minimal energy loss, contributing to advancements in medical diagnostics and scientific discovery. |
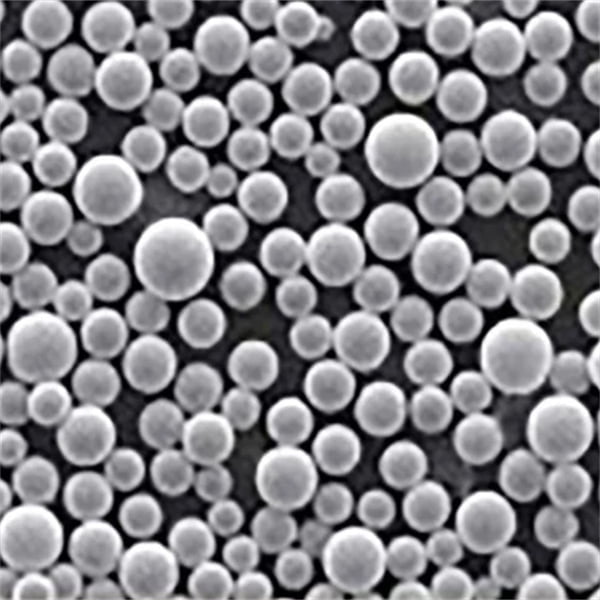
Characteristics of Niobium Alloys Powder
Characteristic | Description | Benefit in Applications |
---|---|---|
High Strength & Ductility | Niobium alloys powder offers exceptional strength-to-weight ratio. Even after deformation, the material retains its ability to absorb stress without breaking. | This allows for the creation of lightweight components in aerospace (e.g., aircraft turbine blades) and automotive sectors (e.g., high-performance engine parts) that can withstand significant mechanical loads. |
Superior Heat Resistance | Niobium boasts a very high melting point, and its alloys maintain exceptional strength at elevated temperatures. | This makes niobium alloys powder ideal for applications exposed to extreme heat, such as jet engine components, nuclear reactors, and high-temperature furnace parts. They can retain their structural integrity and resist deformation even under harsh thermal conditions. |
Enhanced Corrosion Resistance | Niobium forms a strong, protective oxide layer when exposed to air, offering excellent resistance to corrosion across various environments. | This characteristic makes niobium alloys powder valuable for applications in marine environments (e.g., ship hulls, offshore oil rigs) and chemical processing plants where components are exposed to corrosive substances. |
Tailorable Properties | By adjusting the composition of the alloy powder and the manufacturing process, properties like strength, ductility, and workability can be fine-tuned for specific applications. | This versatility allows engineers to create custom-designed components with the optimal combination of properties required for their specific function. |
Excellent Biocompatibility | Certain niobium alloys exhibit exceptional biocompatibility, meaning they are well-tolerated by the human body. | This characteristic makes niobium alloys powder a promising material for medical implants, such as bone screws, dental prosthetics, and heart valves. The biocompatibility minimizes the risk of rejection and ensures long-term functionality of the implant. |
Superconductivity (at Cryogenic Temperatures) | Some niobium alloys demonstrate superconductivity, the ability to conduct electricity with zero resistance, at extremely low temperatures. | This property has significant applications in the field of medical imaging (MRI machines) and scientific research involving high-powered magnets. |
Additive Manufacturing Compatibility | Niobium alloy powders are well-suited for additive manufacturing techniques like 3D printing. The powdered form allows for precise layering and creation of complex geometries. | This compatibility opens doors for the production of intricate, high-performance components with minimal material waste. It allows for lighter and more efficient designs in various industries. |
Fine Particle Size & Distribution | Niobium alloy powders can be manufactured with a controlled particle size and distribution. This characteristic influences flowability, packing density, and printability in additive manufacturing. | Precise control over particle size allows for optimized powder behavior during the manufacturing process, leading to the creation of high-quality, consistent end products. |
Oxidation Potential | Niobium readily forms an oxide layer when exposed to air or moisture. While this layer offers corrosion resistance, it can affect the electrical conductivity and surface properties of the material. | Careful storage and handling are crucial to minimize oxidation and ensure the desired properties of the niobium alloy powder are preserved. In some applications, surface treatments may be necessary to control the oxide layer formation. |
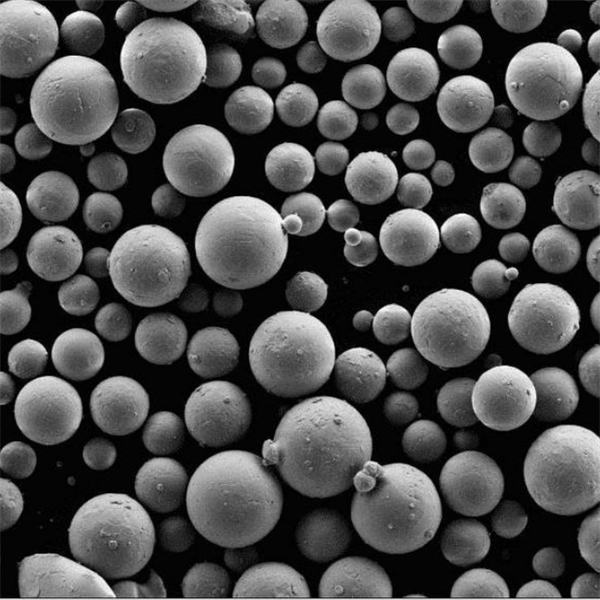
Applications of Niobium Alloys Powder
Industry | Application | Properties Leveraged | Benefits |
---|---|---|---|
Aerospace | Aircraft Engine Components (Turbine Blades, Discs) Rocket Engine Nozzles Airframe Structures | High Strength-to-Weight Ratio, Excellent High-Temperature Performance, Oxidation Resistance | Enables significant weight reduction in critical components, improving fuel efficiency and range. Offers exceptional resistance to extreme temperatures and exhaust gas pressures. Provides superior structural integrity under demanding flight loads. |
Electronics | High-Performance Capacitors (Tantalum Electrolytic Capacitors) Superconducting Magnets (Medical Imaging Equipment, Particle Accelerators) | High Electrical Conductivity, Superconductivity at Low Temperatures | Delivers exceptional capacitance and long lifespans in electronic devices. Allows for the creation of powerful magnets with minimal energy loss, vital for medical imaging and scientific research. |
Energy | Heat Exchangers in Nuclear Reactors | High Strength, Corrosion Resistance, Neutron Transparency | Maintains structural integrity under high pressure and temperature within reactors. Excellent resistance to corrosion from coolants and nuclear byproducts. Allows for efficient neutron passage, crucial for nuclear fission reactions. |
Chemical Processing | Reactors for Aggressive Chemical Environments | Corrosion Resistance, High Melting Point | Enables the safe and efficient handling of highly corrosive chemicals at elevated temperatures. |
Biomedical | Prosthetic Implants (Knee, Hip Replacements) | Biocompatibility, Strength, Corrosion Resistance | Offers excellent compatibility with human tissue, minimizing rejection risks. Provides exceptional strength and durability for long-lasting implant performance. Resists corrosion from bodily fluids, ensuring implant longevity. |
Cutting Tools | High-Speed Machining Tools | High Hardness, Wear Resistance, Heat Resistance | Enables high cutting speeds and extended tool life, improving machining efficiency. Offers superior resistance to wear and tear during demanding machining operations. Maintains cutting edge integrity at elevated temperatures. |
Specifications and Standards
Niobium alloys powder is available in various specifications targeting the requirements of different applications:
Property | Description | Standards (Reference) |
---|---|---|
Chemical Composition | Niobium (Nb) content with specific weight percentages of alloying elements (e.g., Titanium (Ti), Tantalum (Ta)) | ASTM International ASTM B883 [ASTM B883], MPIF Standard 35 [MPIF 35] |
Purity | Minimum weight percentage of Niobium (Nb) in the powder, typically exceeding 99% | ASTM International ASTM B883 [ASTM B883], MPIF Standard 35 [MPIF 35] |
Particle Size Distribution | Range and/or average particle size in micrometers (μm) or mesh size. Can be categorized as coarse, medium, or fine powders | ASTM International ASTM B883 [ASTM B883], MPIF Standard 35 [MPIF 35] |
Particle Morphology | Shape of the powder particles, such as spherical, angular, or irregular | No specific standard, typically vendor specification |
Apparent Density | Density of the powder in its loosely packed state (g/cm³). Influences powder handling and flowability | ASTM International ASTM B212 [ASTM B212], MPIF Standard 42 [MPIF 42] |
Tap Density | Density of the powder after a standardized tapping routine (g/cm³). Provides a higher value than apparent density and indicates packing efficiency | ASTM International ASTM B212 [ASTM B212], MPIF Standard 42 [MPIF 42] |
Flowability | Ease with which the powder flows under gravity. Measured using standardized tests or by vendor specifications | ASTM International ASTM B213 [ASTM B213], MPIF Standard 15 [MPIF 15] |
Oxygen Content | Weight percentage of oxygen (O₂) present in the powder. Affects the mechanical properties of final products | ASTM International ASTM E1019 [ASTM E1019] |
Nitrogen Content | Weight percentage of nitrogen (N₂) present in the powder. High nitrogen content can be detrimental to some applications | ASTM International ASTM E1019 [ASTM E1019] |
Interstitial Impurities | Weight percentages of other elements like Carbon (C), Iron (Fe), or other metallic impurities | ASTM International ASTM E1019 [ASTM E1019] |
Suppliers and Pricing
Some leading global suppliers of niobium alloy powders include:
Supplier | Product Description | Purity | Particle Size | Price (per kg) | Minimum Order | Applications |
---|---|---|---|---|---|---|
MSE Supplies | MSE PRO 99.5% Niobium (Nb) Micron Powder | 99.5% Nb | 3 microns | $579.95 | 1 kg | High-temperature parts, alloys, spray coating, filters, and corrosion-resistant applications |
Atlantic Equipment Engineers | Niobium Metal Powder (irregular or spherical shaped) | 99.8% Nb | 1-5 microns | Request Quote | 100 grams | Strengthening alloys, superconductivity |
Goodfellow | Niobium Powder | 99.85% Nb | Up to 45 microns | $1,067.96 – $1,443.19 | 10 grams | Superalloys, welding products, superconducting magnets, improving strength and corrosion resistance in steel and nickel alloys |
Stanford Advanced Materials | NB0067 Niobium Powder | Not specified | Not specified | Request Quote | Not specified | Additives for alloys, welding rods, and refractory materials |
ChemDirect | Nb-598 Technical Grade Niobium Powder | ≥ 98% Nb | Not specified | $564.40 (100mg) | 100 milligrams | Superalloys, nuclear reactors, aerospace, and chemical processing |
Sigma-Aldrich | Niobium-Tin Alloy (Nb75Sn25) Powder | Not specified | Not specified | $578.00 | Not specified | Superconductors |
Pros and Cons of Niobium Alloys Powder
Feature | Pros | Cons |
---|---|---|
Strength and Durability | Unmatched tensile strength and resistance to deformation at high temperatures Ideal for components enduring extreme stress, like jet engine parts and superconductor housings | Can be more challenging to machine compared to some other alloys |
High-Temperature Performance | Retains structural integrity even under extreme heat Enables applications in high-performance environments like aerospace and nuclear energy | May require specialized manufacturing techniques to handle the powder’s properties |
Corrosion Resistance | Excellent resistance to a wide range of corrosive agents Extends the lifespan of components in harsh environments like chemical processing plants and marine applications | Corrosion resistance can vary depending on the specific alloy composition |
Biocompatibility | Non-toxic and compatible with human tissue Well-suited for medical implants like bone screws, joint replacements, and dental fixtures | Limited selection of biocompatible niobium alloy powders compared to other implant materials |
Additive Manufacturing Compatibility | Powder form makes it ideal for advanced manufacturing processes like 3D printing Allows for complex geometries and lightweight designs | Powder characteristics can impact printability, requiring careful selection and process optimization |
Weight Reduction | Lower density than many other high-performance alloys Contributes to lighter weight components in applications like aircraft and spacecraft | Strength-to-weight ratio may not always be the most favorable compared to certain alternatives |
Availability | Niobium is a relatively abundant element Less susceptible to supply chain disruptions compared to some rarer materials | Processing niobium powder into usable alloys can be more energy-intensive than some other materials |
FAQs
Q: What is niobium alloy powder used for?
A: Niobium alloy powder is used to manufacture high performance parts for aerospace, energy, automotive, medical, and chemical industry applications requiring good heat resistance, strength at high temperatures up to 1000°C, resistance to oxidation and corrosion etc.
Q: How is niobium alloy powder made?
A: It is produced by gas atomization process where a stream of molten niobium alloy mixture is disintegrated by jets of argon or nitrogen gas into fine droplets that solidify into powder particles in the micron size range. The powder can also be made via rotating electrode process or plasma rotating electrode process.
Q: What technologies are used to process niobium alloy powder?
A: Key powder processing routes are pressing and sintering, metal injection molding, hot isostatic pressing, and additive manufacturing methods like laser powder bed fusion, binder jetting, and directed energy deposition. These techniques can fabricate complex and near-net shaped niobium parts.
Q: What are the essential elements that are alloyed with niobium?
A: The most common alloy additions are titanium, molybdenum, zirconium, hafnium, tungsten, tantalum etc. These elements enhance properties like strength, creep resistance, oxidation resistance, and workability of niobium-based alloys. The optimum composition depends on the application.
Q: What standards does niobium alloy powder conform to?
A: Key standards include SAE AMS 5815 covering niobium alloy chemistry limits; ASTM B393 for niobium metal specifications; ISO 15371 defining mechanical, physical and fabricability properties; MIL-STD-2207 on protective treatments and quality testing; and international standards for quality management (ISO 9001) and environmental responsibility (ISO 14001).
Share On
MET3DP Technology Co., LTD is a leading provider of additive manufacturing solutions headquartered in Qingdao, China. Our company specializes in 3D printing equipment and high-performance metal powders for industrial applications.
Inquiry to get best price and customized Solution for your business!
Related Articles
About Met3DP
Recent Update
Our Product
CONTACT US
Any questions? Send us message now! We’ll serve your request with a whole team after receiving your message.
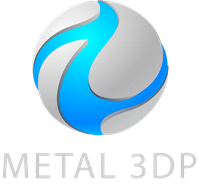
Metal Powders for 3D Printing and Additive Manufacturing