Overview of Metal Atomization Technology
Table of Contents
Metal atomization is a specialized technology used to produce fine metal powders with precise particle sizes and characteristics. This advanced process has revolutionized metal manufacturing across various industries that rely on high-quality metal powders as raw material.
This comprehensive guide will provide a deep dive into all aspects of metal atomization technology. We will cover how it works, its applications, types of atomization systems, product characteristics, cost analysis, suppliers, standards and more. Whether you are looking to adopt this technology or just want to learn more about it, this guide has all the details required.
Overview of Metal Atomization Technology
Metal atomization is a method of turning metal into powder by breaking up molten metal into tiny droplets that solidify into powder particles. It involves the following main steps:
Melting: The raw metal material is melted using an induction furnace or an electric arc furnace. Common metals atomized include aluminum, copper, iron, nickel, titanium, cobalt, etc.
Atomization: The molten metal stream is broken into fine droplets by exposing it to high velocity jets of water, air or inert gas. Different atomizing mediums and forces are used to control particle size and shape.
Solidification: The droplets rapidly solidify into powder particles as they cool down. The rate of cooling affects the microstructure. Faster cooling yields finer grains.
Collection: The atomized powder particles are collected for sieving, screening, annealing, coating and other secondary processes before use.
The finished metal powder has a precisely controlled particle size distribution usually ranging from 10 to 250 microns. The powder morphology, composition and microstructure is customized to meet application requirements.
Some of the major advantages of metal atomization technology include:
- Extremely fine and consistent powder particle size control
- Ability to atomize reactive and high-melting point alloys
- Powders with customized alloy chemistry and microstructures
- Cost-effective production of metal powders in large quantities
- High purity of powder and lower contamination
Metal atomization enables manufacturing of high-performance parts from advanced metal powders otherwise difficult produce using conventional casting, forging or mechanical alloying.
Let’s look at the different types of atomization systems, powder characteristics, applications and other aspects of this technology.
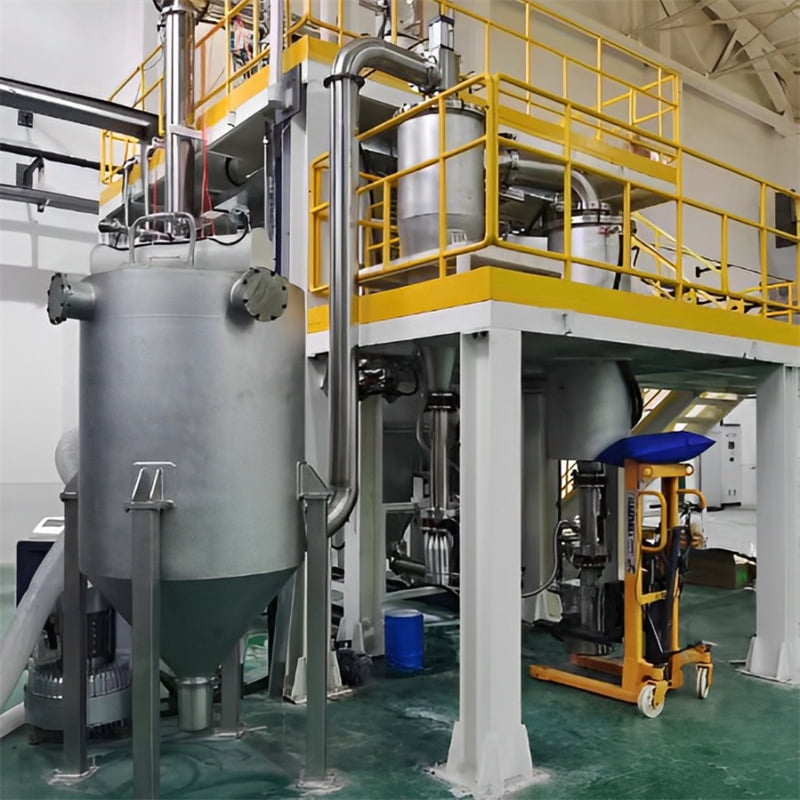
Types of Metal Atomization Systems
There are several techniques used for atomization of metals into powders. The atomization method and system is selected based on the material, desired powder characteristics, production rate and cost considerations.
Atomization Type | Mechanism | Particle Size | Common Metals |
---|---|---|---|
Water Atomization | High pressure water jet breaks up molten metal stream | 50 – 250 μm | Ferrous alloys like stainless steel, tool steel, low alloy steel |
Gas Atomization | Inert gas jets used for atomization | 10 – 150 μm | Nickel, cobalt, titanium alloys; reactive & high melting point metals |
Rotating Electrode Process | Centrifugal forces disintegrate molten metal on spinning cup/disk | 5 – 150 μm | Copper, aluminum, magnesium, tin, lead |
Plasma Atomization | Plasma arc melts and atomizes metals into ultrafine powders | 5 – 50 μm | Specialty alloys, reactive metals like titanium, zirconium etc. |
Water Atomization
In water atomization, the molten metal stream coming out of the furnace is disintegrated by jets of high-velocity water coming from multiple nozzles surrounding it. The water jets break up the metal into fine droplets. The water also quenches and rapidly cools the droplets into solid powder.
This is the most widely used atomization technique given its lower equipment cost. It can produce powders of 50-250 micron size from relatively low melting point alloys like steel, zinc, tin etc. But water atomization may not work well for reactive metals like titanium which can react with water and oxygen.
Gas Atomization
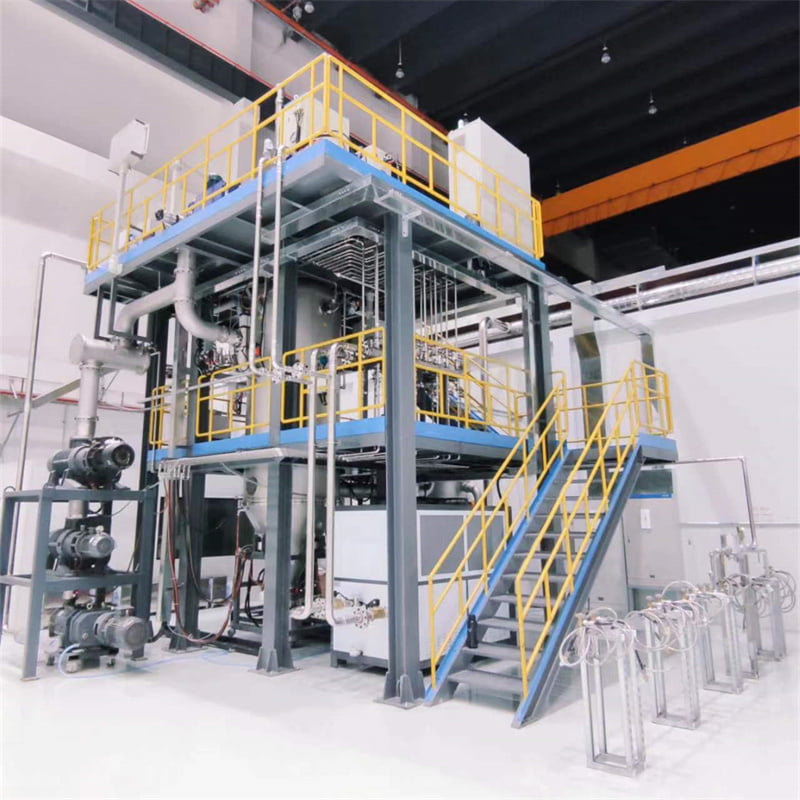
Gas atomization uses jets of inert gas like nitrogen, argon or helium to turn the liquid metal into a spray of droplets under controlled conditions. Since no water or oxygen contacts the metal, oxidation is minimized allowing production of reactive metal powders.
The gas jets also provide finer control over particle size down to 10-150 microns. Gas atomized powders have a spherical morphology preferred in metal injection molding. But the equipment is more sophisticated and operating costs are higher than water atomization.
Rotating Electrode Process
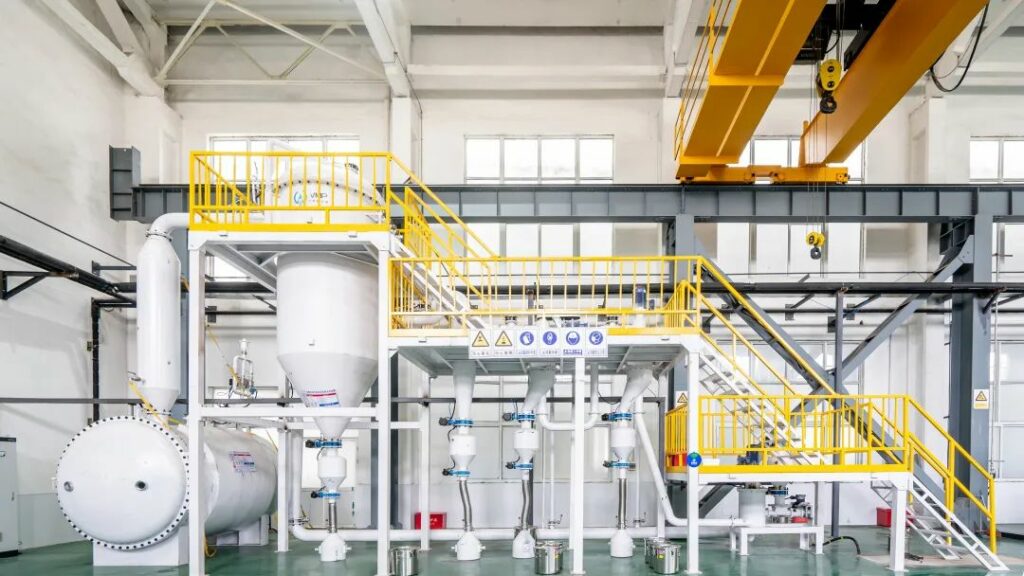
In this method, the molten metal stream pours on to the periphery of a spinning electrode disk or cup. Centrifugal forces throw off fine droplets from the metal which then solidify into powder.
Rotating electrode atomization is ideal for lower melting point non-ferrous metals like aluminum, magnesium, zinc, tin, copper etc. It generates metal powders in the 25-150 micron size range.
Plasma Atomization
Plasma atomization uses extremely high temperatures of plasma arc (10,000-15,000°C) to melt and atomize reactive and refractory metals. The high heat of plasma rapidly melts and disperses metals with melting points over 2500°C into fine powders.
Plasma systems can produce highly spherical powders down to 5-50 micron size. But it requires very specialized equipment and is an expensive process suitable only for niche applications.
Characteristics of Atomized Metal Powders
The various characteristics of atomized metal powders like particle size, shape, chemistry, microstructure, density etc. determines their suitability for the intended application. By controlling the atomization process parameters, powders can be customized to precise specifications.
Particle Size and Shape
- Particle size distribution is a critical characteristic that influences compaction, sintering, performance.
- Water and gas atomization produce fine powders from 10 to 250 microns size. Plasma can go down to 5 microns.
- Particle shape is dependent on the atomization technique. Gas and plasma produce highly spherical particles preferred in metal injection molding feedstock.
Parameter | Role and Effect |
---|---|
Particle Size | Affects flow, packing density, shrinkage, sintering, microstructure, strength, surface finish |
Particle Shape | Spherical shape improves fluidity and compacting; irregular shapes improve mechanical interlocking |
Chemical Composition
- Chemical analysis of metal powders is done to ensure composition is within specified limits for the alloy.
- Loss of volatile elements like Zn, Mg during atomization must be accounted for through starting charge adjustments.
- Minor variations in composition can drastically alter mechanical properties through solid solution strengthening, precipitation etc.
Alloy Composition Control | Importance |
---|---|
Carbon, oxygen, nitrogen levels | Affect microstructure and mechanical properties |
Alloying elements | Maintain specified chemistry for desired characteristics |
Impurity levels | Impacts defects and quality |
Phases and Microstructure
- Rapid solidification during atomization leads to fine microstructures with refined grains, extended solid solubility, metastable phases etc.
- Heat treatment and annealing can be used to modify phases and microstructure as per application needs.
Parameter | Role |
---|---|
Phases Present | Affects strength, hardness, ductility, toughness, electrical properties etc. |
Grain Size | Finer grains improve tensile strength and hardness through Hall-Petch effect |
Porosity/Density | Higher density increases strength; porosity lowers fatigue resistance |
Surface Chemistry
- The surface chemistry of powders influences their flow, packing density, sintering and compaction behavior during component manufacturing.
- Annealing and dry coating provides controlled surface oxide layers to optimize powder properties.
Aspect | Purpose |
---|---|
Surface Oxides | Improves flow; excessive oxide can degrade compaction and sintering |
Lubricant Coatings | Aid in powder flow and compaction; impacts density |
Passivation Layers | Reduce reactivity and sensitivity of reactive powders |
By optimizing these powder characteristics, atomization can produce high-quality powders tailored to meet the needs of advanced manufacturing techniques.
Applications of Metal Atomization Technology
Atomized metal powders find widespread use in manufacturing across aviation, automotive, medical, electronic, defense and other industries. Some of the main applications are:
Powder Metallurgy
- Press and sinter components
- Metal injection molding (MIM) feedstock
- Additive manufacturing powders for 3D printing
Casting and Welding
- Powder atomization for gravity and precision casting
- Powders for brazing, welding consumables
Coatings and Thermal Spray
- Thermal spray powders for wear/corrosion resistant coatings
- Powder coatings for decorative and protective finishes
Powder Compaction
- P/M compacted products like gears, bearings and bushings
- High density parts through cold/hot isostatic pressing
Magnets and Electronics
- Sintered rare earth permanent magnets
- Soft magnetic components like inductors, sensors
- Conductive metal powders for pastes, EMI shielding
Chemical and Structural Packaging
- Porous metal filters from sintered powder structures
- Metal foam materials with high surface area
Atomized powders enable manufacturing of high-performance components with properties superior to traditional fabrication routes. By using pre-alloyed powders, parts can be made from very hard metals like tool steel, cobalt chromium and nickel alloys.
Critical applications in aerospace, medical and automotive rely extensively on precision components produced from atomized powders owing to their exemplary mechanical characteristics and reliability.
Let’s go through some specific examples demonstrating the capabilities of metal powder atomization technology.
Case Example 1: Titanium Alloy Orthopedic Implants
- Biocompatible titanium alloy TI-6AL-4V powder produced using inert gas atomization prevents oxidation.
- Precise particle size distribution ensures excellent flow and packing density for metal injection molding.
- Controlled alloy chemistry results in fully biocompatible implant with high strength.
- Fine microstructure from rapid solidification improves fatigue performance.
- Complex shaped implants can be manufactured cost-effectively.
Case Example 2: Nickel Superalloy Turbine Parts
- Inert gas atomized pre-alloyed nickel superalloy powders for additive manufacturing.
- Ability to atomize high temperature resistant superalloys not possible with casting.
- Fine grain structure with uniform distribution of strengthening particles.
- Components exhibit excellent high temperature mechanical properties.
- Intricate cooling channels and designs possible through 3D printing.
Case Example 3: Soft Magnetic Ferrite Parts
- Water atomized iron powder with controlled low oxygen content.
- Optimized powder shape and size distribution for compaction.
- Pressed and sintered into highly magnetically permeable components like inductors.
- Excellent magnetic properties achieved through precise chemistry control.
- Cost advantage over ferrite magnets machined from bulk alloys.
These examples illustrate the critical role played by metal atomization technology in enabling high-performance advanced manufacturing across several industries.
Cost Analysis of Metal Atomization
Here is a look at some of the cost factors involved in the metal atomization process:
- Capital equipment: Specialized melting furnaces, atomization vessels, powder collection systems represent major fixed cost. Additional equipment needed for secondary processing like sieving, coating, heat treatment.
- Operating costs: Consumables like water, gas, electricity are recurrent costs. Maintenance and manpower add to operating expenses.
- Raw materials: Metallurgical grade metal inputs for melting and alloy preparation is a variable cost dependent on material type and quality.
- Yield: Powder recovery yield from atomization process impacts usable output. Yield losses to be minimized through process optimization.
- Production capacity: Installed capacity based on furnace size, atomization nozzles etc. determines maximum hourly powder output and impacts per unit cost.
- Quality control: Testing and characterization to ensure powder meets specifications also adds to production costs.
- Economies of scale: Larger production volumes improve cost efficiency due to better utilization of fixed capital investments.
The atomization technique chosen also affects the economics:
Atomization Method | Equipment Cost | Consumable Cost | Output Rate |
---|---|---|---|
Water Atomization | Lower | Lower | Medium |
Gas Atomization | High | High | Slow |
Plasma Atomization | Very High | Very High | Low |
For most cost-sensitive applications, water atomization provides the best value. But for more advanced alloys and powders, gas and plasma techniques may be necessary despite higher costs.
The typical cost range for atomized metal powders based on volume and powder quality:
Parameter | Cost Range |
---|---|
Nickel alloy powder (Gas atomized) | $50 – $120 per kg |
Titanium alloy powder (Plasma atomized) | $270 – $450 per kg |
Stainless steel powder (Water atomized) | $5 – $30 per kg |
Iron base powder (Water atomized) | $2 – $7 per kg |
Despite the costs involved, atomization creates enormous value by enabling high-end component manufacturing in aerospace, medical, automotive and other advanced technology sectors.
Standards and Specifications
To ensure quality and consistency of atomized metal powders, various standards have been published by standards organizations:
ASTM International
- ASTM B215: Standard for Gas Atomization of Aluminum Powder
- ASTM B964: Standard for Gas Atomization of Titanium Alloy Powders
- ASTM B819: Standard for Nominal Apparent Density of Metallic Powders and Compacts
- ASTM B833: Standard Specification for Titanium Alloy Powders for Coatings and Turbocharger Compressor Wheels
ISO Standards
- ISO 4490: Metallic powders – Determination of oxygen content by reduction methods
- ISO 5832-4: Implants for surgery — Metallic materials — Part 4: Cobalt-chromium-molybdenum casting alloy
Other Standards
- SAE AMS 7002: Heat Treatment of Titanium Alloy Powders
- MPIF Standard 35: Materials Standards for Metal Injection Molded Parts
- AMS 7016: Metallic Powders Used for Powder Metallurgy (P/M) Processing
These standards help define material chemistry, particle characteristics, sampling methods, testing procedures, quality acceptance levels and other parameters associated with metal powders produced by atomization process.
Adherence to the applicable standards is critical in industries like aerospace and medical where material and performance specifications are tightly controlled. The standards also provide a common technical language between powder producers and industrial users.
Choosing a Metal Powder Atomization Supplier
Selecting the right supplier is key to obtaining high quality metal powders tailored to your specific component production needs. Here are some factors to evaluate:
Technical Capability
- Experience and expertise with the particular alloy and atomization process
- Right equipment and facilities suitable for the material and capacity
- Stringent quality assurance and testing capability
- Skilled technical support for customization and optimization
Performance Record
- Proven track record of supplying to major OEMs or powder metallurgy manufacturers
- Samples evaluated to validate claimed powder characteristics
- Evidence of customer satisfaction and loyal long-term clientele
Customization Ability
- Flexibility to tailor powder characteristics like particle size, shape, chemistry etc.
- Openness to co-development projects to produce engineered powders
- Variety of atomization techniques and secondary processing available
Business Reliability
- Established company with solid financials and stable supply capacity
- Responsiveness to needs including timely deliveries and after-sales support
- Competitive and transparent pricing structure
- Strong relationships with raw material vendors
Evaluating suppliers on both technical and commercial criteria better ensures you receive powders that consistently meet your manufacturing and quality requirements at a reasonable price.
Advantages and Limitations of Metal Powder Atomization
Advantages
- Consistent particle size distribution down to 10 microns
- Cost-effective production of customized alloys
- High purity powders with minimal contamination
- Fine microstructure from rapid solidification
- Products with superior mechanical properties
- Environmentally cleaner process compared to casting
- Simplifies manufacturing of complex, high-performance components
- Expands range of producible alloys beyond conventional melting
Limitations
- High capital investment required for equipment
- Limited production capacity per atomization unit
- Additional downstream processing needed to achieve final powder properties
- Shape and morphology limitations in water atomization
- Reactive materials require controlled inert atomization
- Stability and handling requirements of fine powders
- Cost factors currently restrict applications
Despite some limitations, metal atomization is an indispensable technology enabling production of tailored powders that offer substantial improvements in material performance and component fabrication capability.
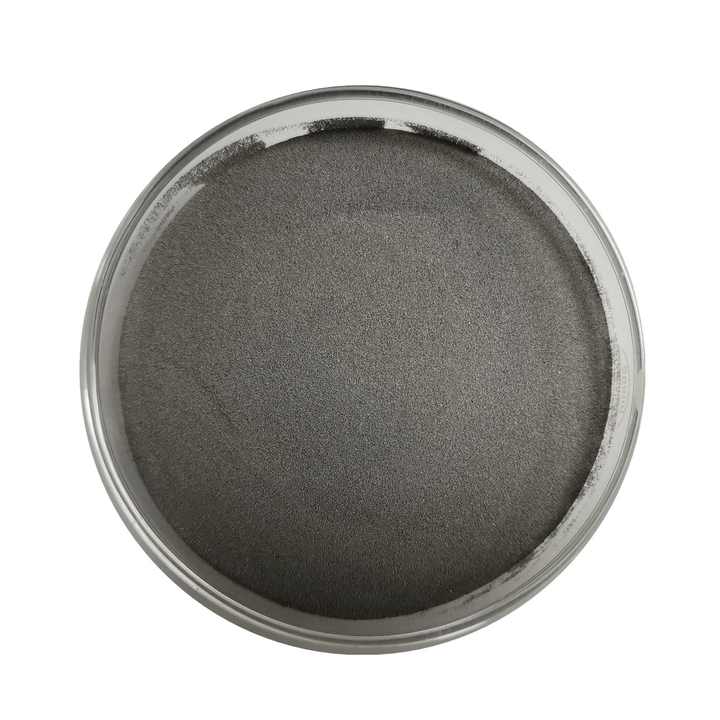
FAQs
What is the typical particle size range achieved in gas atomization?
Gas atomization can produce very fine and precise metal powders usually in the range of 10 to 150 microns. Adjusting the gas pressure and nozzle design allows size control from 10-45 micron for ultrafine powder requirements.
How does water atomization work?
In water atomization, the molten metal stream is disintegrated by high-velocity water jets into tiny droplets which rapidly solidify into powder particles. The water jets break up the metal and also provide rapid cooling.
What metals can be atomized into powder?
Almost all commercial metals and alloys including stainless steel, tool steel, titanium alloys, nickel superalloys, aluminum alloys, copper and copper alloys can be atomized into powders. Even highly reactive metals like titanium, zirconium, niobium can be atomized using inert gas or plasma techniques.
What is the typical yield from atomization process?
The powder recovery yield is typically 80-95% for water and gas atomization. Some metal is lost as oversized particles that do not meet size specifications. Finer control of atomization parameters can increase yields. Plasma atomization gives lower yields of 50-75% due to very high temperatures.
Share On
MET3DP Technology Co., LTD is a leading provider of additive manufacturing solutions headquartered in Qingdao, China. Our company specializes in 3D printing equipment and high-performance metal powders for industrial applications.
Inquiry to get best price and customized Solution for your business!
Related Articles
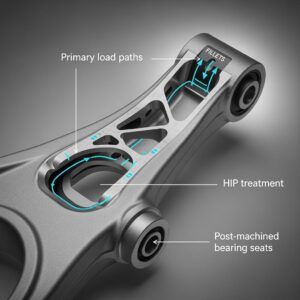
Metal 3D Printing for U.S. Automotive Lightweight Structural Brackets and Suspension Components
Read More »About Met3DP
Recent Update
Our Product
CONTACT US
Any questions? Send us message now! We’ll serve your request with a whole team after receiving your message.