Wysokotemperaturowy proszek żelaza
Spis treści
Przegląd
Wysokotemperaturowe proszki żelaza to specjalistyczne proszki metaliczne wykonane ze stopów na bazie żelaza, zaprojektowane do pracy w podwyższonych temperaturach przekraczających 850°C bez gwałtownej utraty wytrzymałości. Konwencjonalne proszki żelaza i stali utleniają się i niszczą szybciej po przekroczeniu tego progu.
Poprzez staranne dostosowanie składu chemicznego proszku i obróbki, zwiększa się wytrzymałość w wysokich temperaturach i odporność na warunki środowiskowe. Kluczowe obszary zastosowań wymagające takich ekstremalnych termicznych materiałów konstrukcyjnych obejmują przemysł motoryzacyjny, lotniczy, energetyczny i przetwórstwa chemicznego.
Rodzaje Wysokotemperaturowe proszki żelaza
Typ | Metoda produkcji | Kluczowe cechy charakterystyczne | Zastosowania (ze względu na działanie w wysokich temperaturach) |
---|---|---|---|
Proszek żelaza karbonylowego | Rozkład oparów pentakarbonylu żelaza w wysokich temperaturach | - Wysoka czystość (>99% Fe) - Sferyczna morfologia cząstek - Gładka powierzchnia - Ścisła kontrola rozmiaru - Miękkie właściwości magnetyczne | - Wysokowydajne komponenty magnetyczne (np. cewki indukcyjne do zastosowań o wysokiej częstotliwości) - Miękkie rdzenie magnetyczne do transformatorów i silników - Absorbery mikrofalowe - Zastosowania katalityczne ze względu na dużą powierzchnię |
Elektrolityczny proszek żelaza | Elektroliza roztworów chlorku żelaza | - Bardzo wysoka czystość (często przekraczająca 99,5% Fe) - Gęste, kuliste cząstki - Doskonała płynność - Wysoka ściśliwość | - Miękkie rdzenie magnetyczne do zastosowań o wysokiej częstotliwości, takich jak transformatory i cewki indukcyjne - Elementy elektroniczne wymagające wysokiej czystości (np. ekranowanie elektromagnetyczne) - Produkcja addytywna złożonych części metalowych o kształcie zbliżonym do siatki - Zastosowania wykorzystujące dobrą przewodność elektryczną w podwyższonych temperaturach |
Proszek żelaza atomizowany wodą | Stopione żelazo jest rozbijane na drobne cząstki za pomocą strumieni wody pod wysokim ciśnieniem | - Wysoka wydajność produkcji - Najniższy koszt wśród wysokotemperaturowych proszków żelaza - Stosunkowo wysoka zawartość tlenu - Nieregularne kształty cząstek - Szeroki rozkład wielkości cząstek | - Zastosowania, w których najważniejszy jest koszt (np. niektóre procesy formowania wtryskowego metali) - Części wymagające dobrej obrabialności po spiekaniu - Lutowanie w wysokiej temperaturze ze względu na obecność tlenu - Zastosowania korzystające z nieregularnego upakowania cząstek (np. niektóre media filtracyjne) |
Proszek żelaza wyżarzany próżniowo | Dalsze przetwarzanie innych proszków żelaza (często atomizowanych wodą) poprzez wyżarzanie w atmosferze wodoru. | - Poprawia właściwości proszku bazowego (np. zmniejsza zawartość tlenu, poprawia kształt cząstek) - Dostosowane właściwości w oparciu o proszek wyjściowy | - Aplikacje wymagające równowagi między kosztami a wydajnością w wysokich temperaturach (np. niektóre miękkie elementy magnetyczne) - Procesy wytwarzania przyrostowego, w których wymagane są określone właściwości proszku - Aplikacje lutownicze wymagające dobrej wydajności w podwyższonych temperaturach |
Metody produkcji proszków wysokotemperaturowych
Metoda | Opis | Zalety | Wady | Typowe produkowane materiały |
---|---|---|---|---|
Atomizacja gazu | Stopiony metal jest rozbijany na drobne kropelki za pomocą strumienia gazu obojętnego o dużej prędkości | - Proszki o wysokiej czystości - Sferyczna morfologia cząstek - Wąski rozkład wielkości - Dobra płynność - Nadaje się do szerokiej gamy materiałów | - Wysokie zużycie energii - Stosunkowo wysoka cena w porównaniu z innymi metodami - Potencjalne tworzenie się tlenków w niektórych materiałach | - Stopy wysokotemperaturowe (np. nadstopy niklu, glinki tytanu) - Metale ogniotrwałe (np. wolfram, molibden) - Stale narzędziowe |
Atomizacja wody | Stopiony metal jest rozbijany na kropelki za pomocą strumieni wody pod wysokim ciśnieniem | - Wysoka wydajność produkcji - Niski koszt - Możliwość zastosowania do szerokiej gamy materiałów | - Nieregularne kształty cząstek - Szeroki rozkład wielkości cząstek - Wyższa zawartość tlenu w porównaniu z atomizacją gazową | - Stale niskostopowe i żeliwa - Stale nierdzewne (do niektórych zastosowań) - Proszki do formowania wtryskowego metali (MIM) |
Atomizacja plazmowa | Stopiony metal jest wtryskiwany do wysokotemperaturowego strumienia plazmy o dużej prędkości, co prowadzi do szybkiego krzepnięcia | - Bardzo drobne proszki (<10 mikrometrów) - Sferyczne cząstki - Wąski rozkład wielkości - Możliwość wytwarzania faz metastabilnych | - Bardzo wysokie zużycie energii - Ograniczona zdolność produkcyjna - Złożony i kosztowny proces | - Amorficzne proszki metali - wysokowydajne stopy do zastosowań lotniczych i turbinowych |
Rozkład karbonylu | Rozkład termiczny karbonyli metali (związków metali zawierających tlenek węgla) w wysokich temperaturach | - Proszki o wysokiej czystości - Sferyczna morfologia cząstek - Ścisła kontrola nad rozmiarem i morfologią cząstek | - Ograniczone do kilku metali, które tworzą stabilne karbonyle (np. żelazo, nikiel) - Złożony i stosunkowo powolny proces | - Proszki żelaza o wysokiej czystości do zastosowań magnetycznych - Materiały katalityczne |
Elektroliza | Osadzanie metalu ze stopionej soli lub roztworu wodnego za pomocą prądu elektrycznego | - Proszki o bardzo wysokiej czystości - Gęste, kuliste cząstki - Doskonała płynność | - Ograniczona szybkość produkcji - Wysoki koszt - Możliwość zastosowania do ograniczonego zakresu materiałów | - Elektrolityczny proszek żelaza do wysokowydajnych komponentów magnetycznych - Proszki miedzi do zastosowań elektrycznych |
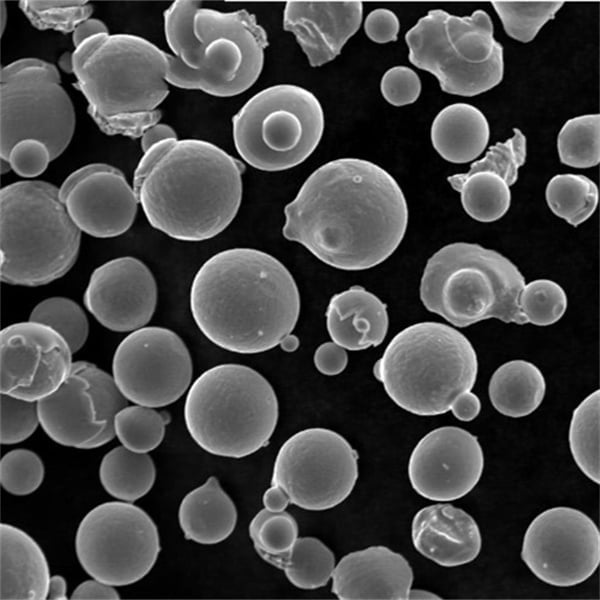
Rodzaje i skład stopów
Istnieją cztery podstawowe kategorie specjalnych proszków stopów żelaza przeznaczonych do długotrwałego stosowania w temperaturach przekraczających 850°C:
Proszki z austenitycznej stali nierdzewnej
Stopy takie jak stale nierdzewne 316L, 304L i 301L zawierają nikiel, który utrzymuje austenityczną strukturę krystaliczną FCC do 1100°C oraz chrom, który zapewnia odporność na utlenianie dzięki ochronnym warstwom powierzchniowym chromu (Cr2O3) w wysokich temperaturach.
Element stopowy | Rola | Waga % Zakres |
---|---|---|
Nikiel (Ni) | Stabilizator austenitu | 8 – 12% |
Chrom (Cr) | Odporność na utlenianie | 16 – 18% |
Mangan (Mn) | Wytrzymałość i ziarnistość | Do 2% |
Azot (N) | Wzmocnienie | 0.1 – 0.25% |
Korzyści: Doskonała wytrzymałość na gorąco, łatwość zagęszczania i spiekania, niższy koszt niż w przypadku superstopów.
Ograniczenia: Skłonność do pełzania powyżej 1000°C, nie nadaje się do zastosowań dynamicznych.
Stopy żelaza o wysokiej zawartości niklu
Stopy niklowo-żelazowe zawierające od 25 do 60 wt% niklu oferują optymalne połączenie wytrzymałości w wysokich temperaturach, ciągliwości i odporności na korozję. Dodatki niklu znacznie spowalniają szybkość dyfuzji i zmniejszają szkodliwe zmiany mikrostrukturalne do 1150°C.
Inne kluczowe pierwiastki stopowe to:
Element stopowy | Rola | Waga % Zakres |
---|---|---|
Nikiel (Ni) | Wzmocnienie roztworu stałego | 25 – 60% |
Chrom (Cr) | Odporność na utlenianie | 10 – 25% |
Kobalt (Co) | Poprawia właściwości mechaniczne w wysokich temperaturach | 10 – 25% |
Molibden (Mo) | Odporność na pełzanie | 2 – 6% |
Korzyści: Niezrównana wydajność mechaniczna w temperaturze 1100°C+, wolniejsza kinetyka degradacji. Stabilna termicznie mikrostruktura.
Ograniczenia: Bardzo wysokie ceny stopów, trudności z kontrolą porowatości, wymagające zagęszczania HIP.
Wzmocnione dyspersją tlenkową stopy żelaza
W stopach wzmocnionych dyspersją tlenkową, bardzo drobne (50-100 nm) obojętne cząstki tlenku itru są osadzone w matrycy materiału. Te tlenki w skali nano utrudniają ruch dyslokacji, utrzymując w ten sposób wytrzymałość powyżej 1000°C.
Element stopowy | Rola | Waga % Zakres |
---|---|---|
Tlenek itru (Y2O3) | Cząsteczki nanotlenku zapewniające stabilność termiczną | 0.25% – 1% |
Chrom (Cr) | Odporność środowiskowa | Do 20% |
Aluminium (Al) | Zwiększa dyspersję tlenków | Do 4% |
Korzyści: Wyjątkowa stabilność mikrostrukturalna i wytrzymałość na pełzanie w warunkach roboczych 1100°C+.
Ograniczenia: Bardzo wysoki koszt, trudności w przetwarzaniu - tradycyjnie wytwarzane poprzez mechaniczne stopowanie i konsolidację.
Stopy glinku żelaza (FeAl)
Stopy glinku żelaza o zawartości aluminium 10- 40% oferują doskonałą odporność na utlenianie i siarczkowanie do 900°C dzięki tworzeniu trwałej wierzchniej warstwy ochronnej z tlenku glinu (Al2O3). Chrom wspomaga ochronę powierzchni.
Element stopowy | Rola | Waga % Zakres |
---|---|---|
Aluminium (Al) | Odporność na utlenianie | 10 – 40% |
Chrom (Cr) | Zwiększa odporność na warunki środowiskowe | 5 – 10% |
Węgiel, Zr (C, Zr) | Wzmacniacze z węglików spiekanych | Do 0,5% |
Korzyści: Duża stabilność środowiskowa, niższa gęstość niż stali, łatwość produkcji w porównaniu do superstopów.
Ograniczenia: Utrata wytrzymałości powyżej 750°C, słaba odporność na pełzanie, przyłożone naprężenia zwiększają zjawiska szkodników.
Metody produkcji
Specjalne techniki są wykorzystywane do produkcji wysokotemperaturowych proszków stopów żelaza o odpowiednich właściwościach:
Atomizacja gazu
- Kontrolowane szybkie chłodzenie strumienia stopionego metalu umożliwia zatrzymanie pierwiastków stopowych w roztworze zamiast tworzenia osadów.
Sferoidyzacja plazmy
- Nieregularne proszki z procesów atomizacji wodnej są ponownie topione za pomocą palnika plazmowego i ponownie zestalane w kuliste proszki idealne do metod AM.
Wielokrotne cykle Sinter-Crush
- Proszki są wielokrotnie zagęszczane w wysokich temperaturach, kruszone i przesiewane w celu udoskonalenia rozkładu proszku, idealnego do przetwarzania MIM.
Stopowanie mechaniczne
- Mielenie kulowe proszków metali elementarnych tworzy nano-rozproszone rozkłady cząstek i klastrów w stopach ODS
Rafinacja karbonylu
- Produkuje proszki metali o bardzo wysokiej czystości, gdy tańsze metody produkcji powodują zanieczyszczenie.
Porównanie metod produkcji
Metoda | Poziomy czystości | Zawartość tlenu | Opcje morfologii | Wydajność (tony/rok) |
---|---|---|---|---|
Atomizacja gazu | Umiarkowany | <1000 ppm | Głównie kulisty | Wysoka >20 000 |
Atomizacja wody | Niski | 2000-4000 ppm | Nieregularny | Bardzo wysoka >50 000 |
Sferoidyzacja plazmy | Średni | 500-2000 ppm | Kulisty | Niski <5,000 |
Stopowanie mechaniczne | Wysoki | <1500 ppm | Zmienne kształty cząstek | Niskie setki |
Proces karbonylowy | Bardzo wysoka | <200 ppm | Kulisty/guzkowy | Wysoka >25 000 |
Metody charakteryzacji
Kilka metod analitycznych jest niezbędnych do kwalifikacji wysokotemperaturowych stopów proszkowych:
Skład chemiczny
- Techniki spektrograficzne i chemii mokrej identyfikują składniki pierwiastkowe i ich ilości - niezbędne do weryfikacji projektu stopu.
- Zawartość węgla, siarki, tlenu i azotu wskazuje na zanieczyszczenie spowodowane procesem, które ma wpływ na wydajność materiału.
Rozmiar i morfologia cząstek
- Analizatory wielkości cząstek wykorzystujące dyfrakcję laserową określają pełną granulometrię w zakresie od 10 nm do 3 mm.
- Obrazowanie SEM wizualizuje kształt, cechy powierzchni, cząstki satelitarne, porowatość przydatne do oceny przydatności procesu budowy i analizy defektów.
Krystalografia
- XRD pokazuje obecne fazy, stany wytrącania, analizę ilościową właściwości krystalicznych
- Ocenia wpływ ekspozycji termicznej na frakcje fazowe poprzez ewolucję mikrostrukturalną
Testowanie właściwości proszku
- Przepływometria Halla, gęstość pozorna i ściśliwość określają ilościowo zachowanie proszku, ułatwiając obsługę i konsolidację.
Zastosowania i wykorzystanie proszków wysokotemperaturowych
Obszar zastosowań | Rodzaj proszku (przykłady) | Wykorzystane kluczowe właściwości | Korzyści |
---|---|---|---|
Wytwarzanie przyrostowe metali (AM) | Nadstopy niklu atomizowane gazem, stale nierdzewne atomizowane wodą | - Sferyczna morfologia zapewniająca dobrą płynność - Wąski rozkład wielkości zapewniający równomierne osadzanie - Wydajność w wysokich temperaturach do budowy funkcjonalnych części | - Umożliwia tworzenie złożonych komponentów o kształcie zbliżonym do siatki - Dostosowane właściwości materiału do konkretnych zastosowań - Zmniejszona ilość odpadów w porównaniu do tradycyjnej produkcji subtraktywnej |
Wysokowydajne komponenty magnetyczne | Proszek żelaza karbonylowego, proszek żelaza elektrolitycznego | - Wysoka czystość zapewniająca niskie straty energii - Sferyczna morfologia zapewniająca dobrą gęstość rdzenia - Miękkie właściwości magnetyczne zapewniające efektywny transfer energii | - Zwiększona wydajność transformatorów, cewek indukcyjnych i silników - Obniżone temperatury pracy i poziomy hałasu - Miniaturyzacja urządzeń dzięki lepszym parametrom magnetycznym |
Lutowanie w wysokiej temperaturze | Proszek żelaza atomizowany wodą, stopy niklu atomizowane gazem | - Kontrolowana temperatura topnienia do lutowania różnych materiałów - Obecność tlenków (w niektórych proszkach) dla lepszego zwilżania i łączenia - Wytrzymałość na wysokie temperatury dla solidnych połączeń | - Łączenie różnych metali i stopów - Tworzenie mocnych, szczelnych uszczelnień w trudnych warunkach - Zastosowania w przemyśle lotniczym, motoryzacyjnym i energetycznym |
Powłoki natryskiwane cieplnie | Stopy aluminium atomizowane wodą, nadstopy niklu atomizowane gazem | - Szeroki zakres temperatur topnienia do różnych zastosowań powlekania - Nieregularne kształty cząstek do mechanicznego blokowania - Odporność na wysokie temperatury do ochrony podłoży | - Zwiększona odporność na zużycie i korozję - Izolacja termiczna - Odbudowa zużytych komponentów - Zastosowania w silnikach, turbinach i wymiennikach ciepła |
Formowanie wtryskowe metali (MIM) | Stale atomizowane wodą, wstępnie stopione proszki | - Drobny rozmiar cząstek dla skomplikowanych geometrii części - Dobra płynność dla równomiernego wypełnienia formy - Kontrolowane właściwości proszku dla dokładności wymiarowej | - Ekonomiczna produkcja złożonych części metalowych o kształcie zbliżonym do siatki - Możliwość uzyskania wysokiej wytrzymałości i gęstości - Zastosowania w przemyśle motoryzacyjnym, medycznym i elektronicznym |
Zastosowania katalityczne | Sproszkowane żelazo karbonylowe, metale przejściowe atomizowane gazem | - Wysoka powierzchnia dla wydajnych reakcji katalitycznych - Kontrolowana struktura porów dla selektywnej katalizy - Dostosowana morfologia cząstek dla lepszej aktywności katalizatora | - Kontrola emisji w samochodowych układach wydechowych - Reakcje przetwarzania chemicznego - Produkcja czystych paliw i energii odnawialnej |
Specyfikacje i klasy
Wysokotemperaturowe stopy proszkowe muszą spełniać minimalne wymagania dotyczące składu chemicznego, czystości, charakterystyki cząstek i właściwości:
Cecha | Opis | Kluczowe kwestie |
---|---|---|
Skład materiału | Proszki wysokotemperaturowe są dostępne w różnych materiałach, z których każdy ma różne właściwości odpowiednie do określonych zastosowań. Typowe materiały obejmują: Stopy na bazie niklu: Oferując wyjątkową odporność na utlenianie i wytrzymałość w wysokich temperaturach, idealnie nadaje się do komponentów silników odrzutowych, wymienników ciepła i części turbin gazowych. Stopy na bazie kobaltu: Znane ze swojej odporności na zużycie i stabilności cieplnej, często stosowane w narzędziach skrawających, łopatkach turbin i implantach biomedycznych. Stale nierdzewne: Zapewnia równowagę między odpornością na korozję i wysoką temperaturą, nadaje się do kolektorów wydechowych, kotłów i urządzeń do przetwarzania żywności. Stale narzędziowe: Zapewniają wyjątkową twardość i odporność na zużycie w podwyższonych temperaturach, idealne do form, matryc i stempli. Ceramika ogniotrwała: Oferuje doskonałe właściwości izolacji cieplnej, powszechnie stosowane w wykładzinach pieców, tyglach i dyszach rakietowych. | Wybór materiału zależy od zamierzonego przypadku użycia. Należy wziąć pod uwagę takie czynniki jak szczytowa temperatura pracy, pożądane właściwości mechaniczne (wytrzymałość, odporność na zużycie), odporność na utlenianie i kompatybilność z otaczającym środowiskiem. |
Rozmiar i rozkład cząstek | Rozmiar i rozkład cząstek proszku znacząco wpływają na proces aplikacji i właściwości produktu końcowego. Drobniejsze proszki (10-45 mikronów): Poprawia wykończenie powierzchni i tworzy cienkie, gładkie powłoki. Doskonale nadaje się do elektrostatycznego osadzania natryskowego i zastosowań ze złożem fluidalnym. Grubsze proszki (45-150 mikronów): Oferują lepszą płynność i mogą tworzyć grubsze powłoki. Większe zastosowanie w technikach prasowania i spiekania. | Rozmiar cząstek ma kluczowe znaczenie dla uzyskania pożądanej grubości powłoki i estetyki. Zrównoważona dystrybucja zapewnia wydajną aplikację i minimalizuje ilość odpadów. |
Płynność | Łatwość, z jaką proszek przepływa, ma zasadnicze znaczenie dla spójnej aplikacji i wydajnego użytkowania. Proszki o dobrej sypkości umożliwiają płynne podawanie do pistoletów natryskowych i zasobników, minimalizując tworzenie się grudek i zatorów. | Nieodpowiednia płynność może prowadzić do niespójności aplikacji, nierównych powłok i opóźnień w produkcji. Producenci często stosują dodatki lub dostosowują rozkład wielkości cząstek, aby zoptymalizować przepływ. |
Gęstość pozorna | Odnosi się to do wagi proszku na jednostkę objętości, wpływając na czynniki takie jak wymagania dotyczące przechowywania, pojemność zbiornika i grubość powłoki. * Proszki o wysokiej gęstości pozornej: Oferują korzyści w zakresie wydajnego przechowywania i potencjalnie wymagają mniej materiału do uzyskania określonej grubości powłoki. * Proszki o niskiej gęstości pozornej: Może wymagać większych przestrzeni magazynowych, ale może być łatwiejszy w obsłudze i tworzyć grubsze powłoki przy pojedynczej aplikacji. | Gęstość pozorna wpływa na obsługę materiału, potrzeby w zakresie przechowywania i wydajność powlekania. Wybór odpowiedniej gęstości zależy od wymagań aplikacji i dostępnego sprzętu. |
Temperatura topnienia i rozszerzalność cieplna | Temperatura topnienia określa maksymalną temperaturę użytkową proszku, podczas gdy rozszerzalność cieplna dyktuje zmiany wymiarów po podgrzaniu. * Proszki o wysokiej temperaturze topnienia: Są odporne na ekstremalne temperatury, dzięki czemu nadają się do wymagających zastosowań, takich jak komponenty silników rakietowych. * Proszki o niskiej rozszerzalności cieplnej: Minimalizacja zmian wymiarów podczas cykli nagrzewania, co ma kluczowe znaczenie dla zachowania precyzyjnych tolerancji w środowiskach o wysokiej temperaturze. | Zrozumienie tych właściwości ma kluczowe znaczenie dla zapewnienia, że proszek może wytrzymać zamierzoną temperaturę roboczą bez uszczerbku dla funkcjonalności lub stabilności wymiarowej. |
Odporność na korozję | Zdolność materiału proszkowego do odporności na degradację spowodowaną czynnikami środowiskowymi, takimi jak utlenianie lub atak chemiczny, ma kluczowe znaczenie dla długoterminowej wydajności. Proszki o wysokiej odporności na korozję: Zachowują integralność w trudnych warunkach, idealne do zastosowań narażonych na działanie chemikaliów, wysokiej wilgotności lub mgły solnej. Proszki o niższej odporności na korozję: Może wymagać dodatkowej obróbki powierzchni lub powłok ochronnych w celu wydłużenia żywotności. | Wybór odporności na korozję zależy od przewidywanych warunków ekspozycji. Wybór proszku o wysokiej odporności na korozję może wydłużyć żywotność produktu końcowego. |
Analiza kosztów proszków wysokotemperaturowych
Czynnik | Opis | Wpływ na koszty |
---|---|---|
Rodzaj materiału | Jak wspomniano wcześniej, proszki wysokotemperaturowe są dostępne w różnych materiałach, z których każdy ma różne ceny. Stopy na bazie niklu: Generalnie najdroższe ze względu na ich wyjątkową wydajność w wysokich temperaturach i złożone procesy produkcyjne. Stopy na bazie kobaltu: Często mieszczą się w podobnym przedziale cenowym jak stopy na bazie niklu, ale mogą się różnić w zależności od konkretnej zawartości kobaltu i pożądanych właściwości. Stale nierdzewne: Zazwyczaj są bardziej przystępne cenowo niż stopy na bazie niklu lub kobaltu, oferując równowagę między kosztami a wydajnością. Stale narzędziowe: Koszty mogą się różnić w zależności od konkretnych pierwiastków stopowych i pożądanych właściwości. Generalnie tańsze niż opcje na bazie niklu lub kobaltu. Ceramika ogniotrwała: Wykazując doskonałą odporność na ciepło, niektóre materiały ogniotrwałe mogą być stosunkowo niedrogie, szczególnie w przypadku popularnych materiałów, takich jak tlenek glinu. Jednak bardziej wyspecjalizowana ceramika o wysokiej czystości może być znacznie droższa. | Wybór materiałów znacząco wpływa na całkowity koszt projektu. Należy dokładnie ocenić wymagania dotyczące wydajności w stosunku do ograniczeń budżetowych. |
Czystość proszku | Poziom czystości proszku wysokotemperaturowego ma bezpośredni wpływ na jego właściwości i cenę. Proszki o wysokiej czystości: Oferują doskonałe właściwości użytkowe, takie jak zwiększona wytrzymałość, lepsza odporność na utlenianie i lepsze zachowanie podczas spiekania. Są one jednak drogie ze względu na skomplikowane procesy oczyszczania. Proszki o niższej czystości: Może być wystarczający do niektórych zastosowań, w których maksymalizacja wydajności nie jest krytyczna. Proszki te są zazwyczaj bardziej opłacalne. | Należy rozważyć kompromis między osiągnięciem pożądanej wydajności a efektywnością kosztową. W niektórych przypadkach niewielka redukcja czystości może być akceptowalna, jeśli przekłada się na znaczne oszczędności kosztów. |
Rozmiar i rozkład cząstek | Rozmiar i rozkład cząstek proszku może wpływać zarówno na koszt materiału, jak i koszty przetwarzania. Drobniejsze proszki: Zazwyczaj wymagają bardziej złożonych i energochłonnych procesów produkcyjnych, co prowadzi do wyższych kosztów jednostkowych. Proszki gruboziarniste: Chociaż potencjalnie tańsze w produkcji, mogą wymagać dodatkowych etapów przetwarzania (np. mielenia) w celu uzyskania pożądanego rozkładu wielkości cząstek dla określonych zastosowań, potencjalnie kompensując część początkowej przewagi kosztowej. | Optymalizacja wielkości cząstek dla wybranego zastosowania może pomóc w osiągnięciu równowagi między kosztami materiału i przetwarzania. |
Minimalna ilość zamówienia (MOQ) | Wielu dostawców ustala minimalne ilości zamówienia (MOQ) dla proszków wysokotemperaturowych. Duże MOQ: Może to prowadzić do znacznych kosztów początkowych, szczególnie w przypadku rzadziej używanych lub specjalistycznych proszków. Mniejsze MOQ: Może być dostępny po wyższej cenie ze względu na zwiększoną obsługę i administrację związaną z mniejszymi partiami. | Należy wziąć pod uwagę wymagania projektu i potencjalne straty. Jeśli duże MOQ nie zostanie w pełni wykorzystane, należy zbadać alternatywnych dostawców oferujących mniejsze ilości lub współpracować z innymi użytkownikami w celu podzielenia się większym zamówieniem. |
Reputacja i lokalizacja dostawcy | Reputacja dostawcy proszku ma znaczący wpływ na koszty i ogólne powodzenie projektu. Renomowani dostawcy: Wdrożenie rygorystycznych środków kontroli jakości, zapewniających spójne właściwości materiału i minimalizujących ryzyko otrzymania bezużytecznych proszków. Ta niezawodność może być bardzo kosztowna. Mniej uznani dostawcy: Mogą oferować niższe ceny, ale mogą nie mieć rygorystycznych procedur kontroli jakości, co może prowadzić do wyższego wskaźnika odrzuceń lub niespójnej wydajności. | Starannie oceniaj kwalifikacje dostawców i przedkładaj stałą jakość nad potencjalnie niższe koszty początkowe. |
Czas realizacji dostawy | Czas potrzebny na dostarczenie proszku może wpłynąć na harmonogram projektu i potencjalnie wpłynąć na koszty. Krótszy czas realizacji: Może wymagać opcji przyspieszonej wysyłki, która może być droższa. Dłuższy czas realizacji: Mogą być bardziej opłacalne, ale wymagają starannego planowania i zarządzania zapasami, aby uniknąć opóźnień w produkcji. | Oceń kompromis między kosztami a harmonogramem projektu. Jeśli czas realizacji ma krytyczne znaczenie, zbadaj opcje przyspieszonej wysyłki lub zapasów buforowych, aby złagodzić potencjalne opóźnienia. |
Plusy i minusy wysokotemperaturowych stopów żelaza
Cecha | Przewaga | Wada |
---|---|---|
Efektywność kosztowa | W porównaniu z innymi materiałami wysokotemperaturowymi, takimi jak nadstopy na bazie niklu lub kobaltu, stopy na bazie żelaza oferują znaczną przewagę kosztową. Żelazo jest łatwo dostępnym pierwiastkiem, dzięki czemu stopy te są generalnie tańsze w produkcji. | Chociaż opłacalne, wysokotemperaturowe stopy żelaza nie zawsze osiągają ten sam poziom wydajności, co niektóre opcje na bazie niklu lub kobaltu pod względem szczytowej temperatury pracy lub określonych właściwości mechanicznych. |
Odporność na utlenianie | Niektóre stopy żelaza mogą wykazywać dobrą odporność na utlenianie w umiarkowanych temperaturach (do około 700°C). Pierwiastki stopowe, takie jak chrom i aluminium, pomagają tworzyć ochronną warstwę tlenku, która utrudnia dalsze utlenianie. | Odporność stopów żelaza na utlenianie zazwyczaj nie dorównuje superstopom na bazie niklu lub kobaltu, które mogą zachować integralność w znacznie wyższych temperaturach. Stopy żelaza mogą wymagać dodatkowej obróbki powierzchni lub powłok w celu wydłużenia żywotności w środowiskach silnie utleniających. |
Wytrzymałość i odporność na pełzanie | Niektóre stopy żelaza, choć nie dorównują najlepszym, mogą zapewnić odpowiednią wytrzymałość i odporność na pełzanie w podwyższonych temperaturach. Określone pierwiastki stopowe, takie jak molibden i wanad, mogą poprawić te właściwości, czyniąc je odpowiednimi do różnych zastosowań przemysłowych. | Wytrzymałość wysokotemperaturowa i odporność na pełzanie stopów żelaza są zazwyczaj gorsze niż w przypadku superstopów na bazie niklu lub kobaltu. W przypadku zastosowań wymagających wyjątkowej wydajności w ekstremalnych temperaturach, konieczne może być zastosowanie innych materiałów. |
Spawalność i obrabialność | Stopy na bazie żelaza generalnie oferują dobrą spawalność i obrabialność w porównaniu z niektórymi innymi materiałami wysokotemperaturowymi. Przekłada się to na łatwiejszą produkcję i niższe ogólne koszty przetwarzania. | Chociaż stopy żelaza nadają się do spawania i obróbki skrawaniem, mogą wymagać określonych technik spawania lub procedur obróbki skrawaniem, aby uniknąć pogorszenia ich właściwości w złączu spawanym lub wprowadzenia naprężeń podczas obróbki skrawaniem. |
Możliwość recyklingu | Żelazo jest jednym z najczęściej poddawanych recyklingowi metali na świecie. Wysokotemperaturowe stopy żelaza mogą być potencjalnie poddawane recyklingowi po zakończeniu okresu eksploatacji, minimalizując wpływ na środowisko i oferując pewien stopień zrównoważonego rozwoju materiału. | Proces recyklingu złożonych stopów żelaza może być bardziej skomplikowany w porównaniu do czystego żelaza, a czynniki takie jak pierwiastki stopowe i zanieczyszczenia powierzchni mogą wpływać na zdolność do recyklingu. |
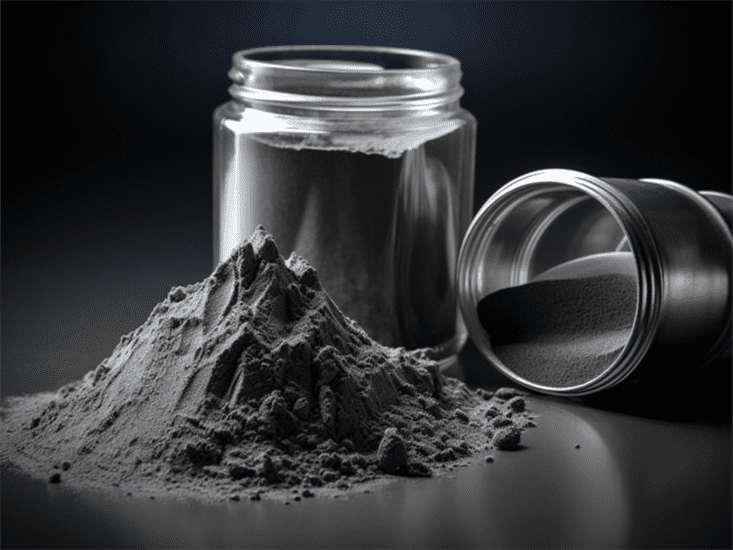
Najczęściej zadawane pytania
P: Jaki jest typowy rozkład wielkości cząstek stosowany dla wysokotemperaturowych proszków ze stali nierdzewnej w metalowym AM?
W przypadku procesów syntezy w złożu proszku, takich jak selektywne topienie laserowe (SLM) i topienie wiązką elektronów (EBM), powszechny zakres to frakcje o wielkości 15 μm - 45 μm. Drobniejsze rozkłady mogą poprawić rozdzielczość, ale pogarszają rozprzestrzenianie się proszku podczas osadzania warstw i zmniejszają charakterystykę przepływu.
P: Jakie szybkości chłodzenia przy atomizacji gazowej pozwalają zachować optymalny skład proszku stopowego?
O: Aby uzyskać najlepsze połączenie retencji chemicznej i odpowiedniej morfologii proszku, w przypadku wysokotemperaturowych proszków stali nierdzewnej i nadstopów powszechnie stosuje się szybkości krzepnięcia w zakresie 1000-3000°C na sekundę.
P: Dlaczego wysoki poziom cząstek tlenku jest szkodliwy dla wysokotemperaturowych stopów żelaza?
O: Podczas pracy obecne tlenki mogą ulec zgrubieniu i migracji, tworząc mniej ochronne i mniej stabilne populacje tlenków, co skutkuje przyspieszonym atakiem ze strony środowisk utleniających, zasiarczających, nawęglających lub chlorujących - skracając żywotność komponentów. Staranne określenie i kontrola poziomów tlenu w oparciu o maksymalne temperatury ekspozycji i warunki pracy są niezbędne przy opracowywaniu stopów.
P: Jakich metod można użyć w celu zwiększenia gęstości proszku do >95% teoretycznej?
O: Prasowanie izostatyczne na gorąco jest powszechnie stosowane na wysokotemperaturowych elementach ze stali nierdzewnej lub nadstopów po wstępnej produkcji AM lub MIM w celu wyeliminowania porów resztkowych, tworząc wydajność materiału zbliżoną do stopów kutych w tych samych wzmocnionych stanach obróbki cieplnej. Gęstość zbliżona do teoretycznej zapewnia wytrzymałość mechaniczną.
P: Dlaczego kontrola zawartości azotu poniżej 1000 ppm ma krytyczne znaczenie w przypadku wysokowytrzymałych stopów miedzi o wysokiej przewodności?
O: Odbiór azotu powoduje powstawanie bardzo twardych, kruchych faz azotkowych, które drastycznie obniżają przewodność cieplną i elektryczną, zmniejszając funkcjonalność w zastosowaniach związanych z zarządzaniem ciepłem, jednocześnie zmniejszając formowalność i plastyczność podczas produkcji.
Udostępnij
MET3DP Technology Co., LTD jest wiodącym dostawcą rozwiązań w zakresie produkcji addytywnej z siedzibą w Qingdao w Chinach. Nasza firma specjalizuje się w sprzęcie do druku 3D i wysokowydajnych proszkach metali do zastosowań przemysłowych.
Zapytaj o najlepszą cenę i spersonalizowane rozwiązanie dla Twojej firmy!
Powiązane artykuły
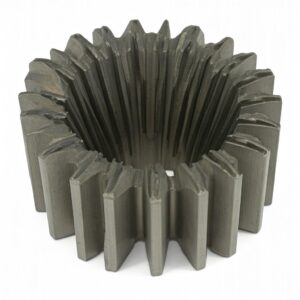
Wysokowydajne segmenty łopatek dysz: Rewolucja w wydajności turbin dzięki drukowi 3D w metalu
Czytaj więcej "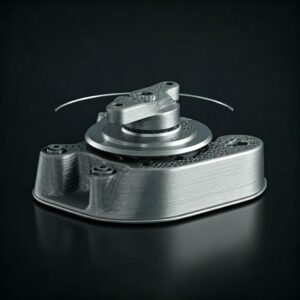
Drukowane w 3D mocowania dla samochodowych czujników radarowych: Precyzja i wydajność
Czytaj więcej "Informacje o Met3DP
Ostatnia aktualizacja
Nasz produkt
KONTAKT
Masz pytania? Wyślij nam wiadomość teraz! Po otrzymaniu wiadomości obsłużymy Twoją prośbę całym zespołem.
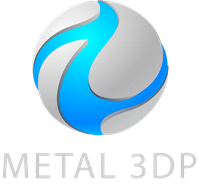
Proszki metali do druku 3D i produkcji addytywnej