3D Printed Plates for Thermal Interface Modules: Revolutionizing Thermal Management
Table of Contents
Introduction – The Critical Role of Thermal Interface Plates in Modern Electronics
As electronic devices become increasingly powerful and compact, effective thermal management has become paramount. Overheating can lead to performance degradation, reduced lifespan, and even catastrophic failure of critical components. Thermal interface plates play a vital role in dissipating heat away from these sensitive electronics, ensuring optimal operating temperatures and long-term reliability. These plates act as a crucial bridge between heat-generating components and heat sinks or other cooling solutions, facilitating efficient thermal transfer. In industries spanning aerospace, automotive, medical devices, and industrial machinery, the demand for high-performance thermal interface solutions is constantly growing. Metal 3D printing, offered by innovative companies like Metal3DP, presents a groundbreaking approach to manufacturing these critical components, offering unprecedented design flexibility and material customization.
What are 3D Printed Thermal Interface Plates Used For? – Diverse Applications Across Industries
3D printed thermal interface plates serve a wide array of applications across various high-tech industries. Their primary function is to enhance thermal conductivity between two surfaces, effectively drawing heat away from sensitive electronic components such as microprocessors, power transistors, LEDs, and integrated circuits. Here’s a closer look at their key use cases:
- Aerospace: In aerospace applications, where weight and performance are critical, 3D printed thermal interface plates are used in avionics systems, power electronics for satellites, and cooling solutions for sensitive sensors. The ability to create complex geometries allows for optimized heat dissipation in tightly constrained spaces.
- Automotive: Electric vehicles (EVs) and advanced driver-assistance systems (ADAS) rely heavily on efficient thermal management. 3D printed plates are employed in battery cooling systems, power inverter cooling, and thermal management for high-performance computing units within vehicles.
- Medical Devices: Medical imaging equipment (MRI, CT scanners), laser surgery devices, and high-performance diagnostic tools generate significant heat. Custom-designed 3D printed thermal interface plates ensure the reliable operation and accuracy of these critical devices.
- Industrial Manufacturing: Industrial automation systems, power supplies, and high-performance machinery benefit from effective thermal management. 3D printed plates are used to cool motor drives, control units, and other heat-sensitive components, improving their longevity and performance.
- Electronics Cooling: Beyond these specific industries, 3D printed thermal interface plates find widespread use in cooling high-performance computing (HPC) clusters, telecommunications equipment, and consumer electronics where efficient heat dissipation is crucial for maintaining performance and reliability.
The versatility of metal 3D printing allows for the creation of thermal interface plates tailored to the specific thermal management challenges of each application.
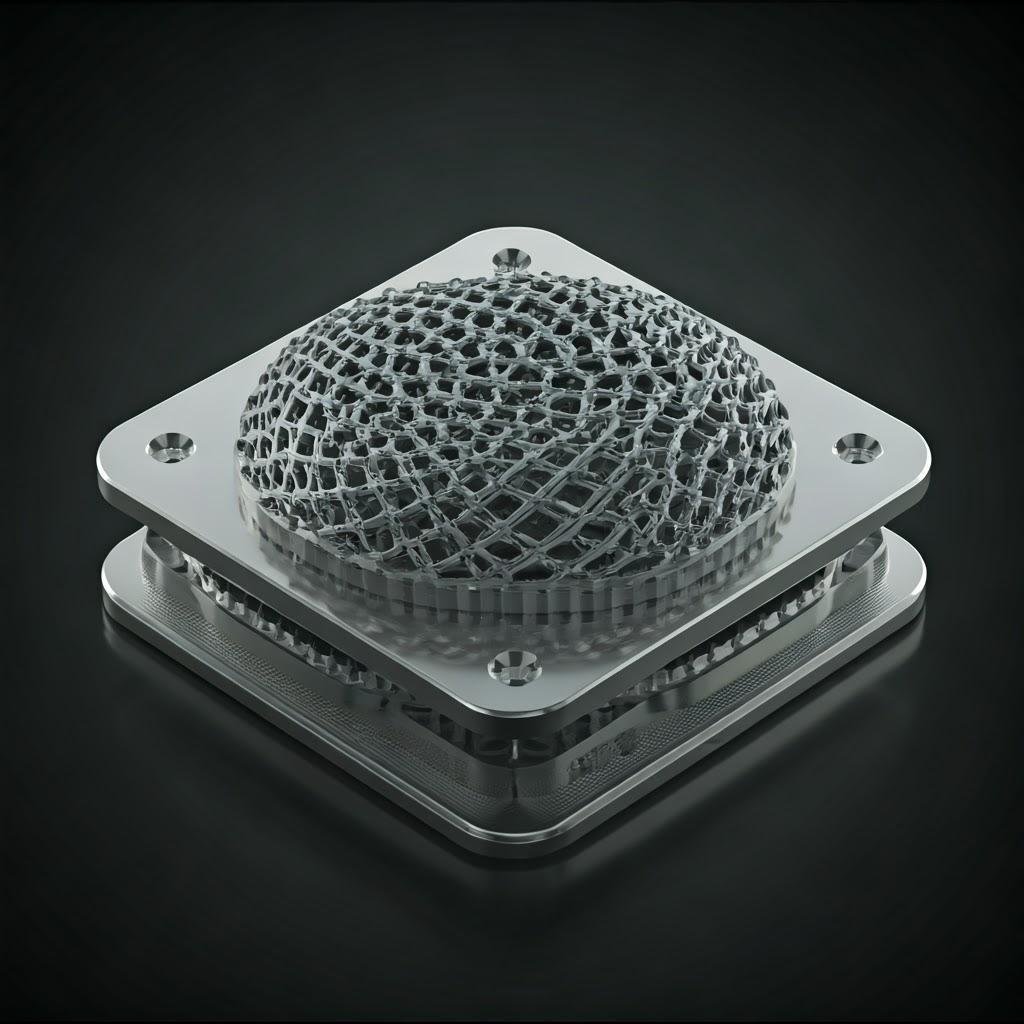
Why Use Metal 3D Printing for Thermal Interface Plates? – Advantages Over Traditional Manufacturing
Opting for metal 3D printing for the production of thermal interface plates offers numerous advantages over traditional manufacturing methods such as machining or die casting. These benefits are particularly compelling for industries demanding high performance, complex geometries, and material customization:
- Design Freedom and Complexity: Additive manufacturing allows for the creation of intricate internal structures, such as conformal cooling channels and complex fin designs, that are impossible or cost-prohibitive to achieve with traditional methods. This design freedom enables optimized heat transfer and more efficient cooling. Metal3DP’s advanced printing technology excels at producing these complex geometries with high accuracy.
- Material Optimization: Metal 3D printing enables the use of advanced materials like CuCrZr and AlSi10Mg, which offer excellent thermal conductivity and mechanical properties. Furthermore, the ability to tailor the material composition to specific thermal requirements provides a significant advantage. Metal3DP manufactures a wide range of high-quality metal powders optimized for demanding thermal applications.
- Lightweighting: In aerospace and automotive applications, reducing weight is crucial. 3D printing allows for the creation of lightweight yet robust thermal interface plates with optimized material distribution, contributing to overall system efficiency.
- Rapid Prototyping and Customization: Metal 3D printing significantly reduces lead times for prototyping and allows for rapid design iterations. This agility is invaluable for developing and testing new thermal management solutions. Moreover, customized designs for specific applications can be produced efficiently without the need for expensive tooling.
- Reduced Material Waste: Additive manufacturing processes are generally more material-efficient than subtractive methods like machining, as material is only deposited where needed. This reduces waste and lowers material costs, particularly when working with expensive specialty alloys.
- On-Demand Manufacturing and Lower Volume Production: Metal 3D printing is economically viable for both low-volume production and the creation of customized parts on demand, eliminating the need for large production runs and warehousing. This is particularly beneficial for specialized applications or when dealing with fluctuating demand.
By leveraging the capabilities of metal 3D printing, businesses can achieve superior thermal management solutions with enhanced performance, reduced weight, and greater design flexibility.
Recommended Materials and Why They Matter – CuCrZr and AlSi10Mg for Optimal Thermal Performance
The choice of material is critical for the performance of thermal interface plates. Metal 3D printing offers the flexibility to utilize advanced alloys specifically chosen for their thermal and mechanical properties. For thermal interface applications, CuCrZr (Copper-Chromium-Zirconium) and AlSi10Mg (Aluminum-Silicon-Magnesium) are excellent choices, each offering unique advantages:
CuCrZr (Copper-Chromium-Zirconium):
- High Thermal Conductivity: Copper is renowned for its exceptional thermal conductivity, making CuCrZr an ideal material for efficient heat transfer. The addition of Chromium and Zirconium enhances its strength and hardness at elevated temperatures without significantly compromising its thermal performance.
- Excellent Electrical Conductivity: While primarily used for thermal management, the good electrical conductivity of CuCrZr can be beneficial in certain applications where grounding or electrical connections are integrated into the thermal interface plate.
- Good Corrosion Resistance: CuCrZr exhibits better corrosion resistance compared to pure copper, ensuring long-term reliability in various operating environments.
- High Strength and Hardness: The alloying elements Chromium and Zirconium significantly improve the mechanical properties of copper, allowing for the creation of robust and durable thermal interface plates that can withstand mechanical stresses.
AlSi10Mg (Aluminum-Silicon-Magnesium):
- Good Thermal Conductivity: While not as high as copper alloys, AlSi10Mg offers a respectable level of thermal conductivity, making it suitable for many thermal management applications.
- Lightweight: Aluminum alloys are significantly lighter than copper alloys, which is a critical advantage in weight-sensitive applications such as aerospace and automotive.
- Excellent Strength-to-Weight Ratio: AlSi10Mg offers a good balance of strength and weight, making it a structurally sound material for thermal interface plates.
- Good Processability: AlSi10Mg is well-suited for metal 3D printing processes like Selective Laser Melting (SLM), allowing for the creation of complex geometries with good surface finish.
- Cost-Effective: Compared to some copper alloys, AlSi10Mg can be a more cost-effective material choice for certain applications where the highest thermal conductivity is not strictly required.
Metal3DP offers a comprehensive portfolio of high-quality metal powders, including CuCrZr and AlSi10Mg, specifically optimized for additive manufacturing. Their advanced powder making system ensures high sphericity and flowability, crucial for producing dense, high-performance 3D printed parts.
| Property | CuCrZr | AlSi10Mg |
| :---------------------- | :----------------------------------------- | :----------------------------------------- |
| Thermal Conductivity | High (around 350-380 W/m·K) | Moderate (around 120-160 W/m·K) |
| Density | High (around 8.9 g/cm³) | Low (around 2.7 g/cm³) |
| Strength | High | Good |
| Hardness | High | Moderate |
| Corrosion Resistance | Good | Good |
| Electrical Conductivity | Good | Moderate |
| Lightweighting | Low Potential | High Potential |
| Cost | Generally Higher | Generally Lower |
| Applications | High-performance cooling, electrical contact | Lightweight cooling, structural integration |
The selection between CuCrZr and AlSi10Mg depends on the specific requirements of the application, including the level of thermal conductivity needed, weight constraints, and cost considerations. Consulting with experts at Metal3DP can help determine the optimal material choice for your 3D printed thermal interface plates.
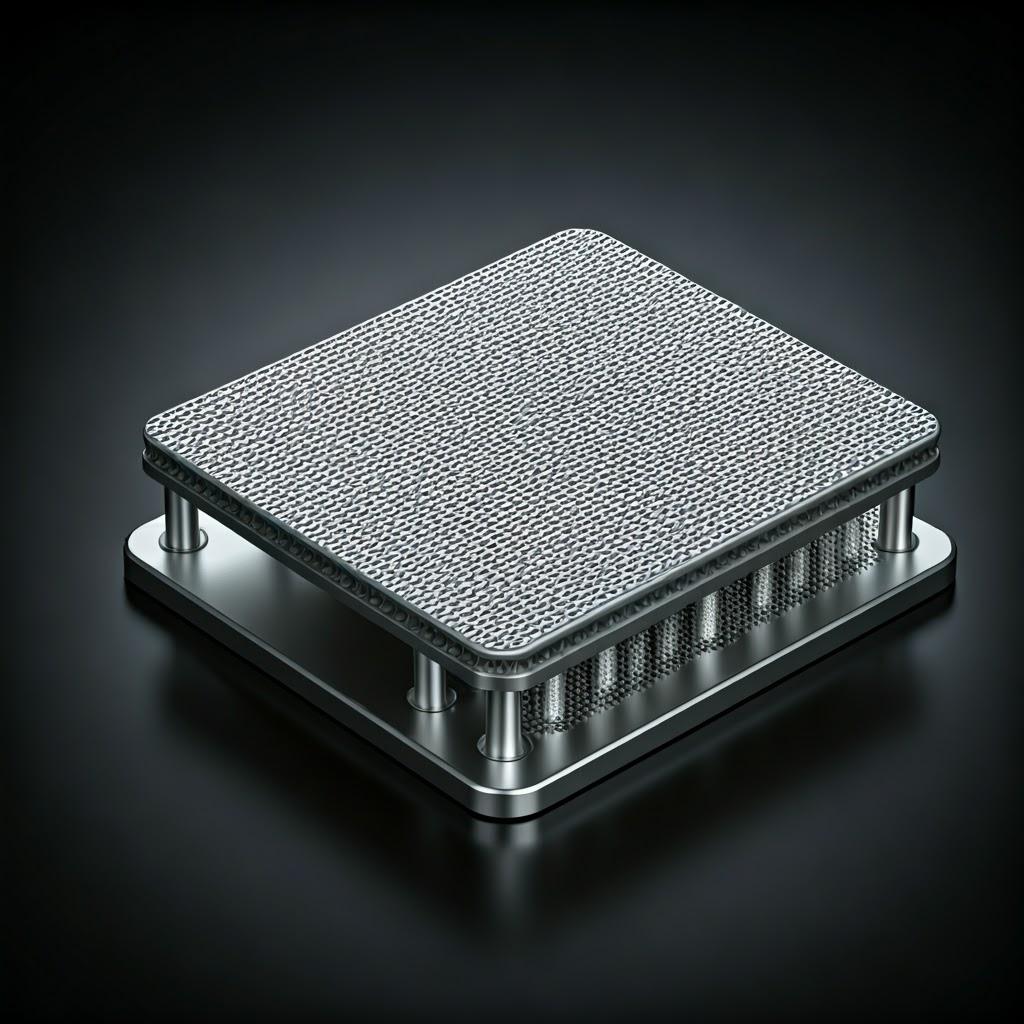
Design Considerations for Additive Manufacturing of Thermal Interface Plates – Optimizing for Performance and Printability
Designing thermal interface plates for metal 3D printing requires a different mindset compared to traditional manufacturing. To fully leverage the capabilities of additive manufacturing and achieve optimal thermal performance, several design considerations are crucial:
- Conformal Cooling Channels: One of the most significant advantages of 3D printing is the ability to integrate conformal cooling channels directly within the thermal interface plate. These channels can follow the exact contours of the heat-generating component, ensuring efficient and uniform heat extraction. Designing these channels with optimized flow paths and cross-sections is essential for maximizing cooling efficiency. Metal3DP’s expertise in application development can assist in designing these complex internal features.
- Fin Design and Optimization: Fins are commonly used to increase the surface area for heat dissipation. 3D printing allows for the creation of intricate fin geometries, such as micro-fins, pin fins, or lattice structures, that offer enhanced heat transfer compared to conventional fin designs. Computational fluid dynamics (CFD) analysis can be used to optimize fin shape, size, and spacing for specific airflow conditions.
- Surface Texture for Enhanced Contact: The surface finish of the thermal interface plate directly impacts the thermal contact resistance between the plate and the heat source or heat sink. 3D printing offers control over surface texture, allowing for the creation of micro-scale features that can improve contact area and reduce thermal resistance.
- Topology Optimization for Lightweighting: For weight-sensitive applications, topology optimization techniques can be employed to design thermal interface plates with minimal material usage while maintaining structural integrity and thermal performance. This involves using algorithms to determine the optimal material distribution based on thermal and mechanical loads.
- Integration of Mounting Features: 3D printing allows for the direct integration of mounting features, such as screw holes, standoffs, or alignment pins, into the design of the thermal interface plate. This can simplify assembly and reduce the need for additional hardware.
- Wall Thickness and Structural Integrity: While maximizing surface area for heat transfer is important, ensuring sufficient wall thickness and structural integrity is also crucial. The design must withstand the expected mechanical loads and thermal stresses during operation. Simulation tools can help determine the optimal wall thickness and ribbing structures for reinforcement.
- Support Structure Optimization: During the metal 3D printing process, support structures are often required to prevent warping and ensure the correct geometry of overhanging features. Designing parts with self-supporting angles and minimizing the need for extensive support structures can reduce material waste and post-processing time. Metal3DP’s advanced printing technology is designed to minimize the need for supports in many applications.
By carefully considering these design aspects, engineers can leverage the unique capabilities of metal 3D printing to create high-performance thermal interface plates tailored to their specific application requirements.
Tolerance, Surface Finish, and Dimensional Accuracy in 3D Printed Thermal Interface Plates – Achieving Precision for Optimal Contact
Achieving the required tolerance, surface finish, and dimensional accuracy is critical for ensuring optimal thermal contact and performance of 3D printed interface plates. Metal 3D printing technologies have advanced significantly, offering impressive levels of precision:
- Dimensional Accuracy: Selective Laser Melting (SLM) and Electron Beam Melting (EBM), the primary metal 3D printing technologies used by Metal3DP, can achieve dimensional accuracies typically ranging from ±0.1 mm to ±0.05 mm, depending on the part geometry, size, and printing parameters. This level of accuracy is often sufficient for thermal interface applications where precise fitting with heat sources and sinks is required.
- Tolerance Control: While achieving tight tolerances directly during the printing process can be challenging for complex geometries, careful design and optimized printing parameters can minimize deviations from the nominal dimensions. For applications requiring very tight tolerances, post-processing steps like precision machining or grinding can be employed to achieve the desired accuracy.
- Surface Finish: The as-printed surface finish in metal 3D printing is typically rougher than that achieved by machining. The surface roughness (Ra) can range from 5 to 20 µm depending on the material, layer thickness, and printing orientation. For thermal interface plates, a smooth surface finish is generally preferred to maximize contact area and minimize thermal interface resistance. Post-processing techniques such as polishing, sanding, or chemical etching can be used to improve the surface finish to the required level.
- Factors Affecting Accuracy and Finish: Several factors influence the dimensional accuracy and surface finish of 3D printed parts, including:
- Printer Calibration and Maintenance: Properly calibrated and maintained 3D printers are essential for achieving consistent and accurate results.
- Material Properties: Different metal powders exhibit varying levels of shrinkage and warpage during the printing process, which can affect dimensional accuracy. Metal3DP’s high-quality metal powders are engineered to minimize these effects.
- Printing Parameters: Layer thickness, laser power, scan speed, and build orientation are critical parameters that influence both accuracy and surface finish. Optimized parameter sets are crucial for achieving the desired results.
- Part Geometry: Complex geometries with overhangs or intricate features can be more challenging to print accurately and may require support structures that can impact surface finish.
- Importance of Metrology and Quality Control: Rigorous metrology and quality control procedures are essential to verify the dimensional accuracy and surface finish of 3D printed thermal interface plates. Techniques such as coordinate measuring machines (CMM), optical scanners, and surface profilometers are used to ensure that parts meet the required specifications. Metal3DP adheres to strict quality control standards to guarantee the precision of its 3D printed components.
By understanding the capabilities and limitations of metal 3D printing in terms of tolerance, surface finish, and dimensional accuracy, engineers can design thermal interface plates that meet the performance requirements of their applications. When ultra-precise dimensions or exceptionally smooth surfaces are needed, appropriate post-processing techniques can be incorporated into the manufacturing workflow.
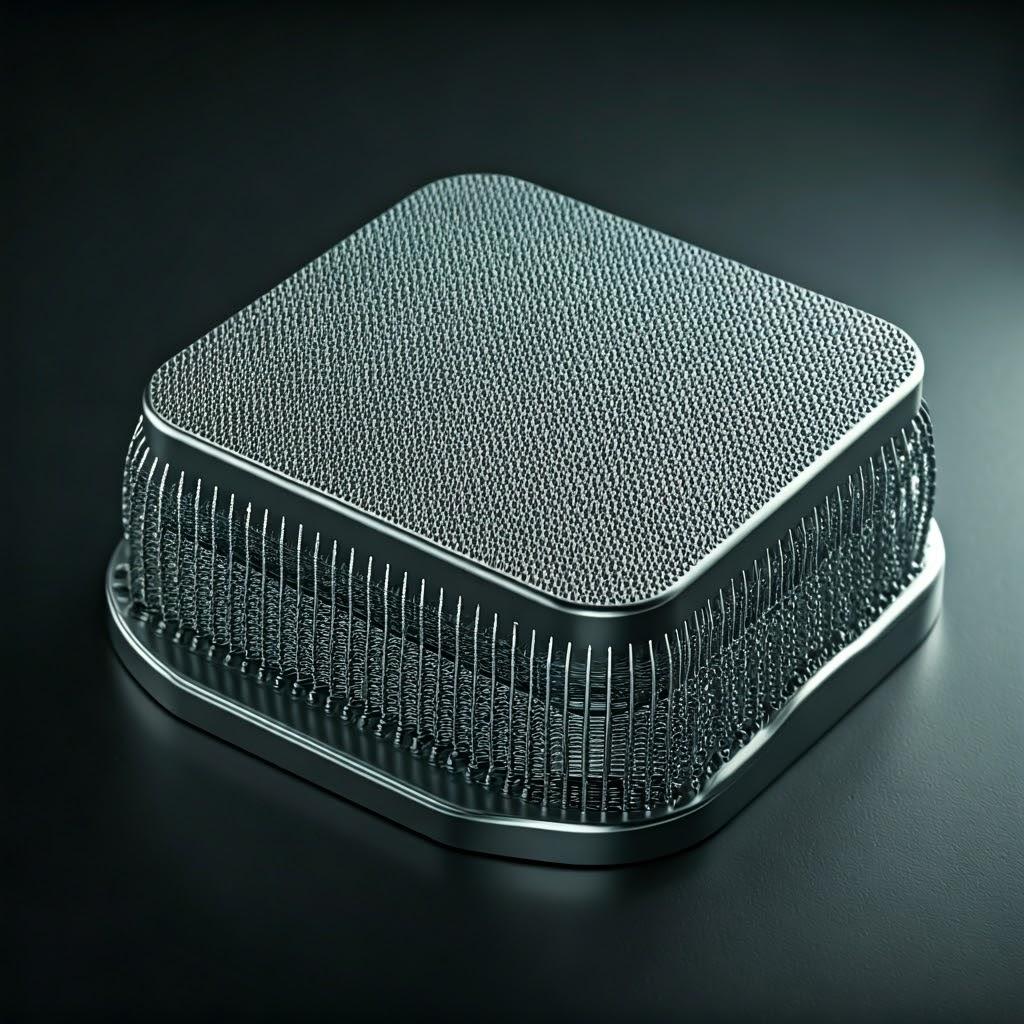
Post-Processing Requirements for 3D Printed Thermal Interface Plates – Enhancing Functionality and Finish
While metal 3D printing offers significant advantages in creating complex geometries, post-processing steps are often necessary to achieve the final desired properties, surface finish, and dimensional accuracy of thermal interface plates. Common post-processing requirements include:
- Support Removal: In many metal 3D printing processes, support structures are used to stabilize overhanging features and prevent warping during the build. These supports need to be carefully removed after printing. The method of support removal can vary depending on the material and the geometry of the part, and may involve manual breaking, cutting, or machining. Designing parts with minimal support requirements, as facilitated by Metal3DP’s technology, can reduce post-processing effort.
- Stress Relief Heat Treatment: Metal 3D printed parts can sometimes contain residual stresses due to the rapid heating and cooling cycles during the printing process. Stress relief heat treatment is often performed to reduce these internal stresses, improving the dimensional stability and mechanical properties of the thermal interface plates. The specific heat treatment cycle depends on the material being used.
- Hot Isostatic Pressing (HIP): For critical applications requiring maximum density and mechanical performance, Hot Isostatic Pressing (HIP) may be employed. This process involves subjecting the printed part to high pressure and temperature in an inert gas environment, which eliminates internal porosity and enhances the material’s strength and fatigue resistance. Metal3DP can facilitate access to HIP services for demanding applications.
- CNC Machining: In cases where very tight tolerances or specific surface finishes are required on certain features, CNC machining can be used as a secondary process. This is particularly relevant for achieving precise mating surfaces for optimal thermal contact.
- Surface Finishing: As mentioned earlier, the as-printed surface finish may not be suitable for all thermal interface applications. Various surface finishing techniques can be employed to reduce surface roughness and improve contact area. These include:
- Polishing: Mechanical polishing using abrasive materials can create a smooth, reflective surface.
- Sanding: Using progressively finer grit sandpaper can improve surface finish.
- Media Blasting: Blasting with fine media can create a uniform matte finish and remove minor surface imperfections.
- Chemical Etching: Controlled chemical reactions can be used to smooth the surface.
- Coating: In some applications, coatings may be applied to the thermal interface plates to enhance their corrosion resistance, electrical insulation properties, or surface wettability for thermal interface materials. Examples include anodizing for aluminum alloys or specialized thermal interface coatings.
The specific post-processing steps required will depend on the application requirements, the material used, and the capabilities of the 3D printing process. It’s crucial to consider these requirements during the design phase to optimize the overall manufacturing workflow and ensure the final thermal interface plates meet the desired performance specifications. Metal3DP offers comprehensive solutions and can advise on the necessary post-processing steps for your specific needs.
Common Challenges and How to Avoid Them in 3D Printing Thermal Interface Plates – Ensuring Successful Manufacturing
While metal 3D printing offers numerous advantages, certain challenges can arise during the manufacturing of thermal interface plates. Understanding these potential issues and implementing appropriate strategies can help avoid them and ensure successful production:
- Warping and Distortion: Thermal gradients during the printing process can lead to warping and distortion of the part, particularly for large or complex geometries.
- How to Avoid: Optimize part orientation on the build platform, use appropriate support structures to anchor the part, and carefully control printing parameters such as laser power and scan speed. Metal3DP’s expertise in process optimization minimizes these issues.
- Porosity: Internal voids or porosity within the printed part can reduce its thermal conductivity and mechanical strength.
- How to Avoid: Utilize high-quality metal powders with good flowability, optimize laser or electron beam parameters to ensure complete melting and solidification, and consider post-processing techniques like Hot Isostatic Pressing (HIP) for critical applications. Metal3DP’s advanced powder making system ensures high powder quality.
- Support Structure Removal Difficulties: Removing support structures from intricate geometries can be challenging and may leave surface imperfections.
- How to Avoid: Design parts with self-supporting angles whenever possible, optimize support structure design for easy removal, and utilize dissolvable support materials if compatible with the chosen metal.
- Surface Roughness: Achieving a smooth surface finish directly from the printing process can be difficult, which can impact thermal contact resistance.
- How to Avoid: Optimize printing parameters such as layer thickness and laser focus, and incorporate appropriate post-processing techniques like polishing or machining to achieve the desired surface finish.
- Dimensional Inaccuracies: Deviations from the intended dimensions can occur due to material shrinkage, thermal expansion, or printer calibration issues.
- How to Avoid: Properly calibrate and maintain the 3D printer, optimize printing parameters for the chosen material, and account for material shrinkage in the design phase. Employ post-processing metrology to verify dimensions and perform corrective machining if necessary.
- Material Selection Issues: Choosing the wrong metal powder for the application can lead to suboptimal thermal or mechanical performance.
- How to Avoid: Carefully consider the thermal conductivity, coefficient of thermal expansion, strength, and other relevant properties of the material for the specific application requirements. Consult with material experts at Metal3DP to select the most suitable powder, such as CuCrZr or AlSi10Mg, for your thermal interface plates.
- Cost Considerations: Metal 3D printing can be more expensive than traditional manufacturing methods for high-volume production.
- How to Avoid: Optimize part design for efficient printing and minimal material usage, consider the total cost of manufacturing including post-processing, and evaluate the benefits of 3D printing, such as design freedom and rapid prototyping, in relation to the overall value.
By proactively addressing these potential challenges through careful design, optimized printing parameters, appropriate material selection (including Metal3DP’s high-quality offerings), and suitable post-processing techniques, manufacturers can successfully leverage metal 3D printing to produce high-performance thermal interface plates.
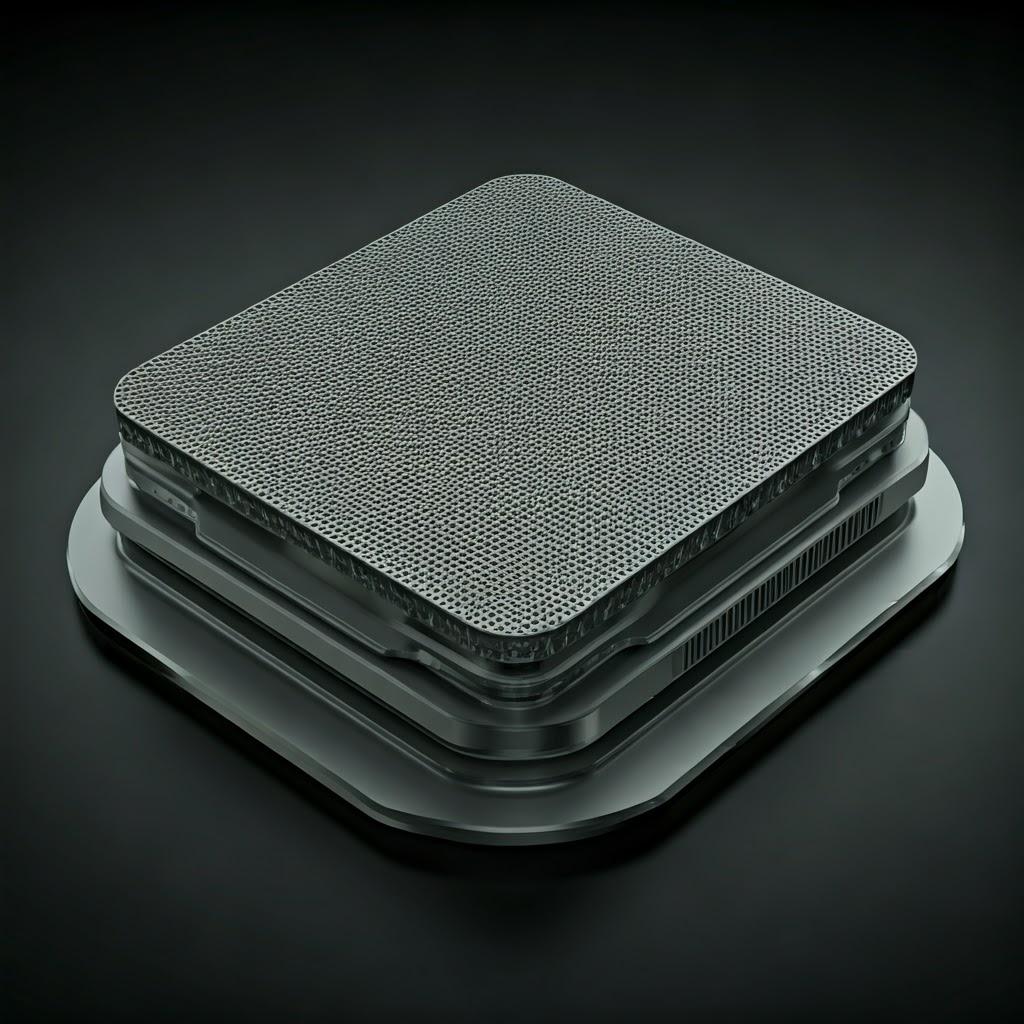
How to Choose the Right Metal 3D Printing Service Provider for Thermal Interface Plates – Key Considerations for B2B Buyers
Selecting the right metal 3D printing service provider is crucial for ensuring the successful manufacturing of high-quality thermal interface plates that meet your specific performance and application requirements. For B2B buyers, several key factors should be considered when evaluating potential suppliers:
- Material Capabilities: Ensure the service provider has experience working with the recommended materials for thermal interface plates, such as CuCrZr and AlSi10Mg. Verify their expertise in processing these materials to achieve optimal thermal and mechanical properties. Metal3DP specializes in a wide range of high-performance metal powders, including those ideal for thermal management applications.
- Printing Technology and Equipment: Understand the types of metal 3D printing technologies the provider utilizes (e.g., SLM, EBM). Different technologies offer varying levels of accuracy, surface finish, and build volume. Ensure their equipment is well-maintained and capable of producing parts with the required specifications. Metal3DP boasts industry-leading print volume, accuracy, and reliability in its printing systems. You can learn more about their printing methods here: https://met3dp.com/printing-methods/
- Design and Engineering Support: A strong service provider should offer design and engineering support to optimize your thermal interface plate design for additive manufacturing. This includes guidance on material selection, design for additive manufacturing (DfAM) principles, thermal simulation, and structural analysis. Metal3DP provides comprehensive solutions spanning SEBM printers, advanced metal powders, and application development services. 1 1. About Us – Metal3DP – 3D Printing Metal Powder Hub met3dp.sg
- Post-Processing Services: Inquire about the in-house or partnered post-processing capabilities, such as support removal, heat treatment, surface finishing (polishing, machining), and coating. Ensure they can provide the necessary post-processing to meet your final part requirements.
- Quality Assurance and Certifications: Verify the service provider’s quality management system and any relevant industry certifications (e.g., ISO 9001, AS9100 for aerospace). Robust quality control procedures are essential to ensure the consistency and reliability of the 3D printed thermal interface plates.
- Experience and Expertise: Look for a provider with a proven track record in manufacturing similar components for your industry. Their experience and expertise can significantly impact the success of your project. Metal3DP has decades of collective expertise in metal additive manufacturing and partners with organizations across various sectors. You can explore their product offerings here: https://met3dp.com/product/
- Lead Times and Production Capacity: Discuss lead times for prototyping and production, as well as their capacity to handle your anticipated volumes. Ensure their timelines align with your project schedule.
- Cost Structure and Transparency: Understand the pricing model and all associated costs, including design, printing, materials, and post-processing. A transparent pricing structure is essential for budgeting and cost analysis.
- Communication and Customer Support: Effective communication and responsive customer support are crucial for a smooth and successful collaboration. Evaluate the provider’s responsiveness and willingness to address your questions and concerns. You can learn more about Metal3DP as a company on their “About Us” page: https://met3dp.com/about-us/
By carefully evaluating these factors, B2B buyers can select a metal 3D printing service provider that can deliver high-quality thermal interface plates tailored to their specific needs, ensuring optimal thermal management solutions for their applications.
Cost Factors and Lead Time for 3D Printed Thermal Interface Plates – Understanding the Economics of Additive Manufacturing
Understanding the cost factors and lead times associated with metal 3D printing is essential for budget planning and project management when considering this manufacturing method for thermal interface plates. Several elements influence the overall cost and turnaround time:
Cost Factors:
- Material Costs: The cost of the metal powder (e.g., CuCrZr, AlSi10Mg) is a significant factor. Specialty alloys and smaller production volumes of powders can lead to higher per-unit material costs. Metal3DP’s ability to manufacture its own high-quality metal powders can offer potential cost advantages.
- Printing Time: The build time depends on the part’s geometry, size, complexity, and the chosen layer thickness. Longer print times translate to higher machine operating costs. Optimizing part orientation and design for faster printing can help mitigate this.
- Machine Usage and Depreciation: Service providers factor in the cost of operating and maintaining their 3D printing equipment, as well as the depreciation of these machines.
- Post-Processing Costs: The extent of post-processing required (support removal, heat treatment, surface finishing, machining) significantly impacts the final cost. Complex post-processing can add substantial expense.
- Design and Engineering Costs: If design optimization or engineering support is required from the service provider, these services will be factored into the overall cost.
- Quantity and Volume: While 3D printing excels at low- to medium-volume production and customization, higher volumes may become less cost-competitive compared to traditional manufacturing methods. However, for complex geometries, 3D printing can remain cost-effective even at higher volumes.
- Quality Assurance and Inspection Costs: Rigorous quality control procedures and inspections add to the overall cost but are essential for ensuring part quality.
Lead Time:
- Design and Pre-processing: The initial design phase, including optimization for 3D printing and build file preparation, can take varying amounts of time depending on the complexity of the part and the need for simulations.
- Printing Time: As mentioned earlier, the actual printing duration is a key component of the lead time.
- Post-Processing Time: The time required for support removal, heat treatment, surface finishing, and other post-processing steps can vary significantly based on the complexity and the required finish.
- Quality Inspection: Thorough quality checks and dimensional verification add to the overall lead time.
- Shipping and Logistics: The time for packaging and shipping the final parts also needs to be considered.
Metal3DP is committed to providing transparent cost structures and efficient lead times for its metal 3D printing services. By understanding these factors, customers can make informed decisions and effectively plan their projects involving 3D printed thermal interface plates. Contact Metal3DP directly to discuss your specific requirements and obtain a detailed cost and lead time estimate.
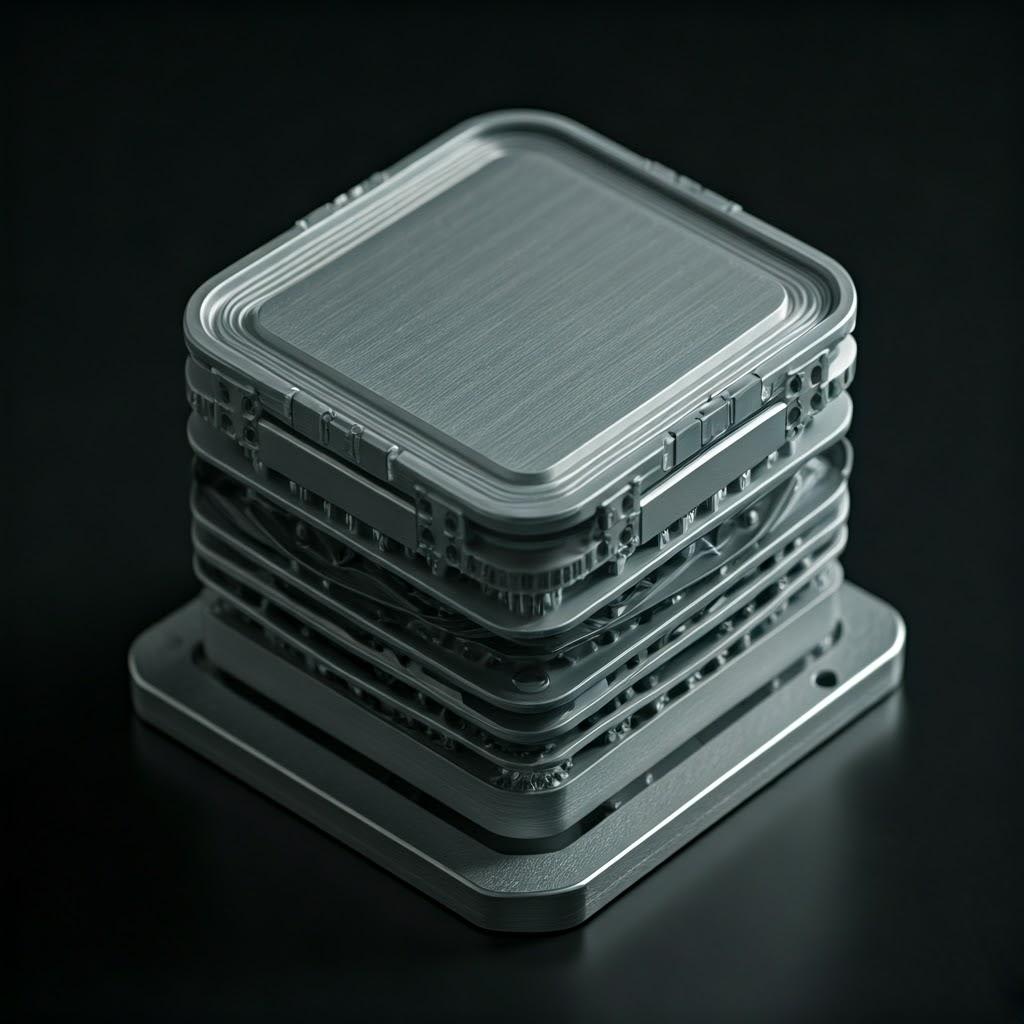
Frequently Asked Questions (FAQ)
- What is the typical thermal conductivity achievable with 3D printed CuCrZr thermal interface plates?
- 3D printed CuCrZr can achieve thermal conductivity in the range of 350-380 W/m·K, which is comparable to wrought CuCrZr. The exact value can depend on the density achieved during the printing process and any subsequent heat treatments. Metal3DP’s optimized printing parameters aim to maximize the density and thermal conductivity of the final parts.
- Can metal 3D printing produce thermal interface plates with integrated cooling channels?
- Yes, absolutely. One of the key advantages of metal 3D printing is the ability to create complex internal geometries, including conformal cooling channels that follow the contours of the heat-generating component for efficient heat dissipation. Metal3DP specializes in producing parts with such intricate internal features.
- What are the typical tolerances achievable for 3D printed AlSi10Mg thermal interface plates?
- With optimized printing parameters, tolerances of ±0.1 mm to ±0.05 mm are achievable for AlSi10Mg parts printed using technologies like SLM offered by Metal3DP. For applications requiring tighter tolerances, post-processing machining can be employed.
Conclusion – Embracing the Future of Thermal Management with Metal 3D Printing
Metal 3D printing offers a transformative approach to the design and manufacturing of thermal interface plates. Its ability to create complex geometries, utilize high-performance materials like CuCrZr and AlSi10Mg, and enable rapid customization provides significant advantages over traditional manufacturing methods. For industries demanding efficient thermal management solutions, such as aerospace, automotive, medical, and industrial manufacturing, the benefits of metal 3D printing are compelling.
By partnering with a reliable and experienced metal 3D printing service provider like Metal3DP, businesses can unlock new possibilities for optimizing thermal performance, reducing weight, and accelerating product development. Metal3DP’s expertise in advanced metal powders, cutting-edge printing technology, and comprehensive application support makes them a trusted partner in realizing the full potential of additive manufacturing for thermal management solutions. Explore how Metal3DP’s capabilities can power your organization’s additive manufacturing goals by visiting their website: https://met3dp.com/.
Share On
MET3DP Technology Co., LTD is a leading provider of additive manufacturing solutions headquartered in Qingdao, China. Our company specializes in 3D printing equipment and high-performance metal powders for industrial applications.
Inquiry to get best price and customized Solution for your business!
Related Articles
About Met3DP
Recent Update
Our Product
CONTACT US
Any questions? Send us message now! We’ll serve your request with a whole team after receiving your message.
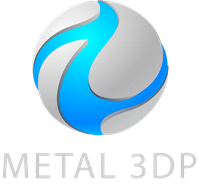
Metal Powders for 3D Printing and Additive Manufacturing