Powder Making Process
Table of Contents
Overview
Powder making processes are essential in various industries, from pharmaceuticals to metallurgy. The process involves converting raw materials into fine particles, which can be used in numerous applications, including manufacturing, 3D printing, and surface coatings. This guide will explore different methods, specific metal powder models, their properties, applications, and more.
Types of Powder Making Processes
Atomization
Atomization is one of the most common methods, where molten metal is dispersed into fine droplets that solidify into powder.
Mechanical Alloying
This process involves repeated welding, fracturing, and re-welding of a mixture of powder particles to create a new alloy.
Electrolysis
Electrolysis is used to produce high-purity powders. The metal is deposited onto a cathode and subsequently scraped off to form powder.
Chemical Reduction
This involves reducing metal oxides with a reducing agent to produce metal powders.
Solid-State Reduction
Here, metal oxides are reduced in solid form, usually involving a high-temperature process.
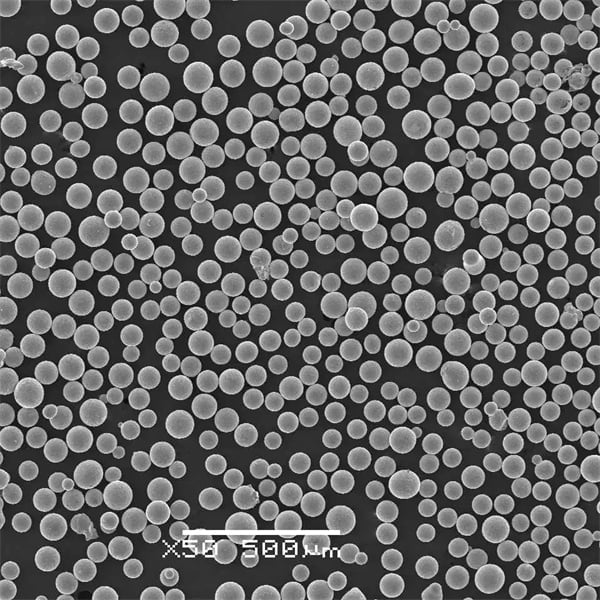
Key Metal Powder Models and Their Descriptions
Metal Powder Model | Composition | Properties | Applications |
---|---|---|---|
Aluminum 6061 | Al, Mg, Si | Lightweight, corrosion-resistant | Automotive parts, aerospace components |
Stainless Steel 316L | Fe, Cr, Ni, Mo | High corrosion resistance, high strength | Medical implants, marine applications |
Titanium Ti-6Al-4V | Ti, Al, V | High strength-to-weight ratio, biocompatible | Aerospace, medical implants |
Nickel 625 | Ni, Cr, Mo, Nb | High corrosion resistance, heat resistance | Chemical processing, marine environments |
Copper C11000 | Cu | Excellent electrical conductivity, thermal conductivity | Electrical components, heat exchangers |
Inconel 718 | Ni, Cr, Fe, Nb, Mo | High strength, corrosion resistance | Gas turbines, aerospace components |
Bronze CuSn10 | Cu, Sn | Good wear resistance, machinability | Bearings, bushings, sculptures |
Cobalt Chrome | Co, Cr, Mo | High wear resistance, biocompatibility | Dental implants, orthopedic implants |
Tool Steel M2 | Fe, C, W, Mo, Cr, V | High hardness, wear resistance | Cutting tools, dies, molds |
Iron Fe-P | Fe, P | High magnetic permeability, ductility | Magnetic cores, soft magnetic components |
Powder Characteristics and Properties
Property | Description |
---|---|
Particle Size | Influences the powder’s flowability and packing density |
Particle Shape | Affects the surface area and reactivity of the powder |
Purity | Determines the quality and performance of the final product |
Density | Impacts the strength and weight of the material |
Flowability | Essential for processes like additive manufacturing |
Applications of Powder Making Process
Industry | Application |
---|---|
Aerospace | Production of lightweight components with high strength |
Automotive | Manufacturing engine parts, gears, and other critical components |
Medical | Creation of biocompatible implants and surgical instruments |
Electronics | Production of conductive components and circuits |
Energy | Development of batteries and fuel cells |
Manufacturing | Use in 3D printing and additive manufacturing |
Specifications, Sizes, Grades, and Standards
Metal Powder Model | Sizes Available | Grades | Standards |
---|---|---|---|
Aluminum 6061 | 15-45 µm, 45-105 µm | A, B | ASTM B209 |
Stainless Steel 316L | 15-45 µm, 45-150 µm | A, B | ASTM F138 |
Titanium Ti-6Al-4V | 15-45 µm, 45-100 µm | A, B | ASTM F1472 |
Nickel 625 | 15-45 µm, 45-105 µm | A, B | ASTM B446 |
Copper C11000 | 15-45 µm, 45-105 µm | A, B | ASTM B170 |
Inconel 718 | 15-45 µm, 45-105 µm | A, B | ASTM B637 |
Bronze CuSn10 | 15-45 µm, 45-105 µm | A, B | ASTM B505 |
Cobalt Chrome | 15-45 µm, 45-105 µm | A, B | ASTM F75 |
Tool Steel M2 | 15-45 µm, 45-105 µm | A, B | ASTM A600 |
Iron Fe-P | 15-45 µm, 45-105 µm | A, B | ASTM A848 |
Suppliers and Pricing Details
Supplier | Metal Powder Model | Price Range (per kg) |
---|---|---|
Höganäs | Aluminum 6061 | $30 – $50 |
Carpenter Technology | Stainless Steel 316L | $50 – $70 |
Arcam AB | Titanium Ti-6Al-4V | $250 – $350 |
Sandvik | Nickel 625 | $100 – $150 |
Praxair | Copper C11000 | $15 – $25 |
AMETEK | Inconel 718 | $150 – $200 |
Oerlikon | Bronze CuSn10 | $20 – $40 |
EOS GmbH | Cobalt Chrome | $200 – $300 |
Kennametal | Tool Steel M2 | $60 – $80 |
Rio Tinto | Iron Fe-P | $10 – $20 |
Advantages and Disadvantages of Powder Making Processes
Process | Advantages | Disadvantages |
---|---|---|
Atomization | Uniform particle size, high production rate | High energy consumption, expensive |
Mechanical Alloying | Ability to create complex alloys, fine microstructures | Time-consuming, equipment wear |
Electrolysis | High purity powders | High operational costs, limited to certain metals |
Chemical Reduction | Cost-effective, simple process | Potential contamination, limited scalability |
Solid-State Reduction | High purity, suitable for refractory metals | Requires high temperatures, slow process |
Detailed Insights into Powder Making Processes
Atomization: Splitting Molten Metal
Atomization, especially gas atomization, involves spraying molten metal through a nozzle to create fine droplets. These droplets rapidly solidify into powder. It’s like using a high-pressure garden hose to create mist from water. This method ensures uniformity in particle size and is ideal for metals like aluminum and steel.
Mechanical Alloying: Blending to Perfection
Mechanical alloying is akin to mixing ingredients in a food processor, where the repeated action creates a uniform mixture. It involves high-energy ball milling to repeatedly fracture and weld particles, creating fine, homogeneous powders. This is particularly useful for creating superalloys.
Electrolysis: Pure and Simple
Electrolysis, much like how a battery works, uses an electric current to reduce metal ions in a solution. The metal is deposited on the cathode and then scraped off as powder. This method is prized for producing ultra-pure powders, essential in high-tech applications.
Chemical Reduction: Back to Basics
Chemical reduction is straightforward; it involves a chemical reaction where a reducing agent (like hydrogen) converts metal oxides into metal powder. Think of it as a more controlled version of a chemistry experiment, yielding powders like tungsten and molybdenum.
Solid-State Reduction: Heating Things Up
Solid-state reduction is a high-temperature process where metal oxides are reduced directly in their solid form. This method is particularly effective for refractory metals, those with high melting points, such as tantalum and niobium.
Applications in Various Industries
Aerospace: Flying High with Powder Technology
The aerospace industry benefits from powder metallurgy by producing lightweight, high-strength components. For instance, titanium alloys like Ti-6Al-4V are extensively used for parts that endure extreme stress and temperature variations, such as turbine blades and structural components.
Automotive: Driving Efficiency and Performance
In the automotive sector, metal powders are essential for making engine parts, gears, and other critical components. The use of powders like aluminum and iron ensures that parts are both lightweight and durable, enhancing fuel efficiency and performance.
Medical: Healing with Precision
Medical applications require biocompatible and high-strength materials. Stainless steel 316L and cobalt-chrome alloys are popular choices for making implants and surgical instruments. These powders enable the production of intricate shapes and structures that match the human body’s requirements.
Electronics: Conducting Innovation
Copper and other conductive powders are vital in the electronics industry. They are used to create
conductive pathways in printed circuit boards (PCBs) and other electronic components, ensuring efficient electrical conductivity and thermal management.
Energy: Powering the Future
In the energy sector, metal powders play a crucial role in developing advanced batteries and fuel cells. Nickel and cobalt powders are used in the production of electrodes, enhancing the efficiency and longevity of energy storage devices.
Manufacturing: Shaping Tomorrow
Additive manufacturing, or 3D printing, relies heavily on metal powders to build complex and customized parts layer by layer. Powders like stainless steel and titanium are commonly used, allowing for rapid prototyping and production of high-performance parts.
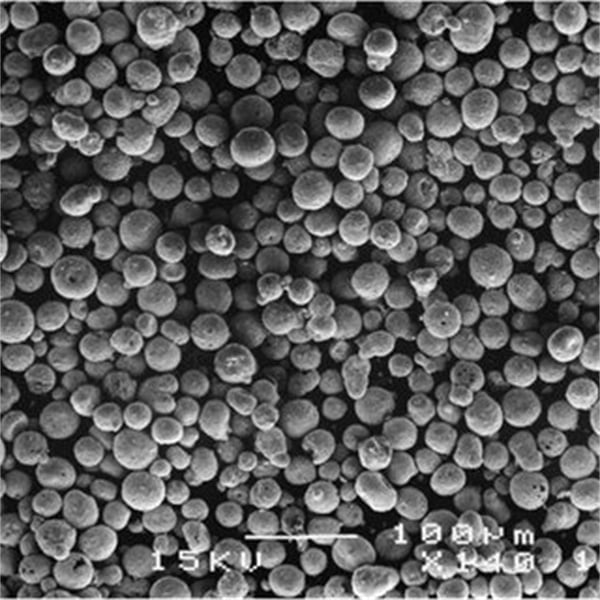
Comparing Pros and Cons: Powder Making Processes
Atomization vs. Mechanical Alloying
Atomization offers high production rates and uniform particle sizes, making it ideal for large-scale operations. However, it’s energy-intensive and costly. Mechanical alloying, on the other hand, excels in creating complex alloys but is time-consuming and causes significant equipment wear.
Electrolysis vs. Chemical Reduction
Electrolysis produces ultra-pure powders, perfect for high-tech applications, but comes with high operational costs. Chemical reduction is simpler and more cost-effective but might result in contamination and has scalability issues.
Solid-State Reduction: A Niche Player
Solid-state reduction is excellent for producing high-purity refractory metal powders but requires high temperatures and is generally slower compared to other methods.
FAQ
Question | Answer |
---|---|
What is the most common method for producing metal powders? | Atomization is the most common method due to its ability to produce uniform particles at high production rates. |
Why are metal powders important in additive manufacturing? | They allow for precise control over part geometry and material properties, enabling the production of complex and high-performance components. |
How does particle size affect powder properties? | Smaller particles generally have higher surface area, improving reactivity and sintering properties but can affect flowability and packing density. |
What are the environmental impacts of powder making processes? | Processes like chemical reduction and electrolysis can have significant environmental impacts due to chemical waste and high energy consumption. |
Which metal powders are best for medical implants? | Titanium Ti-6Al-4V and cobalt-chrome alloys are widely used due to their biocompatibility and strength. |
Share On
MET3DP Technology Co., LTD is a leading provider of additive manufacturing solutions headquartered in Qingdao, China. Our company specializes in 3D printing equipment and high-performance metal powders for industrial applications.
Inquiry to get best price and customized Solution for your business!
Related Articles
About Met3DP
Recent Update
Our Product
CONTACT US
Any questions? Send us message now! We’ll serve your request with a whole team after receiving your message.
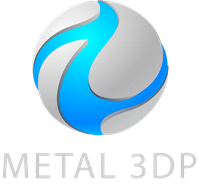
Metal Powders for 3D Printing and Additive Manufacturing