3D Printed Pump Impellers
Table of Contents
Introduction: The Rising Tide of 3D Printed Impellers in Marine Applications
The marine industry, encompassing everything from massive cargo ships and agile naval vessels to essential offshore platforms and intricate underwater systems, demands components that can withstand some of the most challenging operational environments on Earth. Exposure to corrosive saltwater, extreme pressures, and continuous operation necessitates materials and manufacturing processes that ensure unwavering reliability and longevity. In this context, the traditional methods of producing critical parts like pump impellers – often involving casting, forging, and machining – are increasingly being complemented, and in some cases, superseded by the transformative power of metal 3D printing, also known as metal additive manufacturing.
Metal 3D printing is not merely a novel technology; it represents a paradigm shift in how complex metal components are conceived, designed, and manufactured. By building parts layer by layer from metallic powders, this advanced technique offers unprecedented design freedom, the ability to tailor material properties, and the potential for significant improvements in performance and efficiency. For marine pump impellers, this translates to the possibility of creating intricate geometries optimized for fluid dynamics, utilizing high-performance alloys specifically chosen for their resistance to the harsh marine environment, and achieving faster production cycles with reduced material waste.
The adoption of 3D printed impellers is gaining momentum across the marine sector. Engineers and procurement managers are recognizing the strategic advantages this technology offers, from rapid prototyping and on-demand spare parts production to the creation of custom-designed impellers that can enhance the performance of existing pump systems. As the industry continues to navigate the complexities of efficiency, sustainability, and operational reliability, metal 3D printing stands out as a powerful tool for innovation, offering a pathway to next-generation marine components that are both robust and highly optimized for their demanding applications. At Metal3DP, we are at the forefront of this revolution, providing cutting-edge metal 3D printing solutions that empower the marine industry to embrace the future of manufacturing. Our commitment to industry-leading print volume, accuracy, and reliability ensures that mission-critical marine parts can be produced with the highest standards of quality and performance.
What are 3D Printed Marine Pump Impellers Used For?
Marine pump impellers are the heart of any fluid transfer system in maritime applications, responsible for propelling liquids – primarily seawater, but also fuel, lubricants, and coolants – through various systems essential for the operation and maintenance of vessels and offshore structures. The versatility of these components means they are deployed across a wide spectrum of critical functions within the marine industry:
- Cooling Systems: Impellers drive the circulation of seawater to cool engines, generators, and other heat-generating machinery, preventing overheating and ensuring operational efficiency. This is particularly crucial for large vessels and offshore platforms that require continuous and reliable cooling.
- Ballast Systems: These impellers are integral to managing the stability and trim of ships by pumping seawater into and out of ballast tanks. Efficient ballast systems are vital for safe navigation and cargo operations.
- Bilge Pumping: Impellers facilitate the removal of accumulated water from the lower compartments (bilges) of a vessel, preventing damage and maintaining the integrity of the hull. Reliable bilge pumps are essential for safety at sea.
- Firefighting Systems: In the event of a fire onboard a vessel or offshore structure, powerful pumps with robust impellers are critical for delivering large volumes of water to extinguish the blaze. The reliability of these impellers can be a matter of life and death.
- Fuel Transfer: Impellers are used in pumps that transfer fuel between tanks and to engines, ensuring a consistent supply for propulsion and power generation.
- Desalination Plants: Onboard some vessels and offshore platforms, impellers play a role in pumping seawater through desalination systems to produce fresh water for crew and operations.
- Hydraulic Systems: Certain marine hydraulic systems rely on pumps with impellers to generate the fluid power needed for various mechanical operations.
- Wastewater Management: Impellers are used in pumps that handle the transfer and treatment of wastewater generated onboard vessels, adhering to environmental regulations.
Given the diverse and critical nature of these applications, the performance and durability of marine pump impellers are paramount. Metal 3D printing offers a unique opportunity to tailor the design and material of these impellers to the specific demands of each application, potentially leading to enhanced efficiency, reduced wear, and longer service life. Metal3DP’s advanced metal powders and printing technologies are ideally suited for producing impellers that meet the stringent requirements of these demanding marine environments.
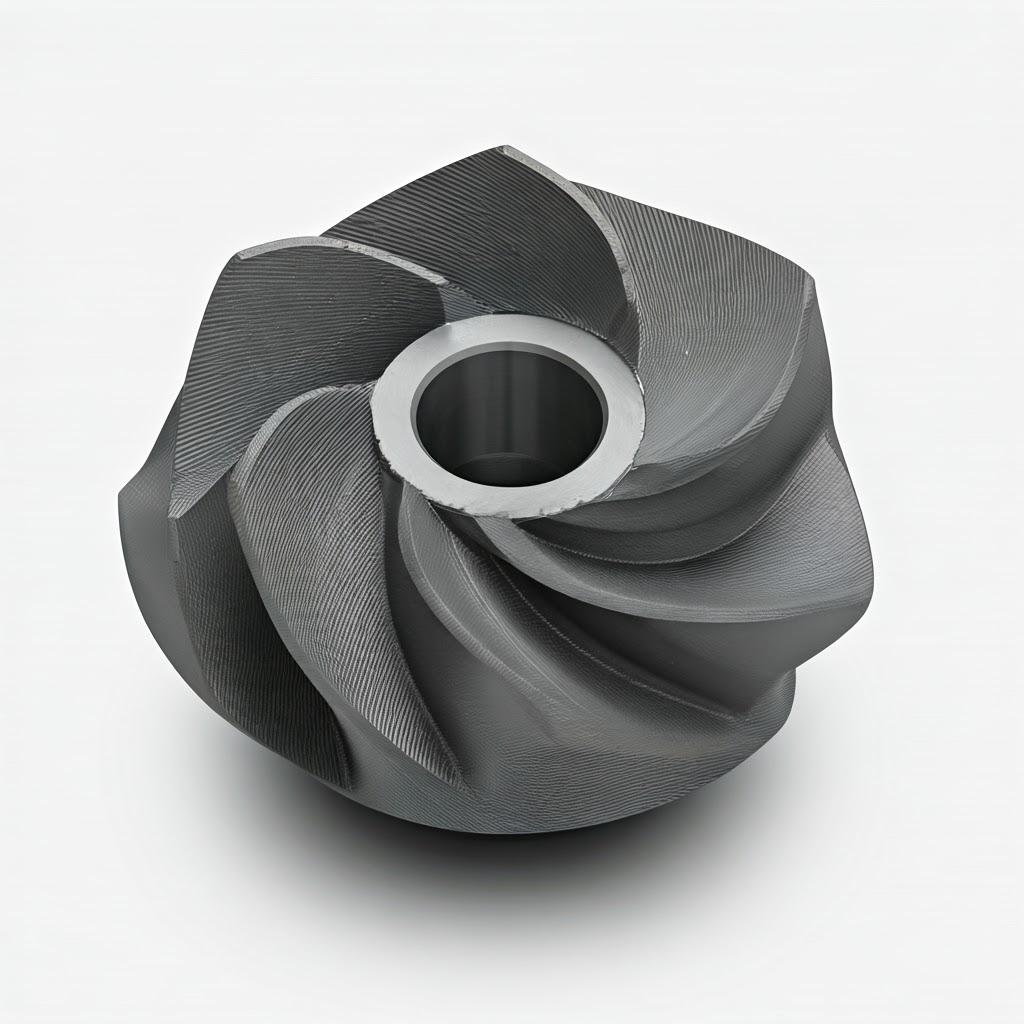
Why Choose Metal 3D Printing for Marine Pump Impellers?
While traditional manufacturing methods have long served the marine industry, metal 3D printing presents several compelling advantages for the production of marine pump impellers:
- Enhanced Design Freedom and Optimization: Additive manufacturing allows for the creation of complex impeller geometries that are difficult or impossible to achieve with casting or machining. This includes optimized blade profiles, internal cooling channels, and lightweighting features that can improve hydraulic efficiency and reduce energy consumption. Engineers can iterate on designs rapidly, using computational fluid dynamics (CFD) analysis to fine-tune impeller performance before committing to full-scale production.
- Material Efficiency and Reduced Waste: Traditional subtractive manufacturing processes often involve removing significant amounts of material, leading to substantial waste. Metal 3D printing, being an additive process, builds the part layer by layer, using only the necessary material. This not only reduces material costs but also contributes to more sustainable manufacturing practices.
- On-Demand and Customized Production: Metal 3D printing facilitates the production of impellers on demand, eliminating the need for large inventories of spare parts. This is particularly beneficial for older or specialized vessels where replacement parts may be difficult to source. Furthermore, impellers can be customized to specific pump designs or operational requirements without the need for expensive tooling changes.
- Rapid Prototyping and Iteration: The ability to quickly produce prototypes allows for faster design validation and iteration. Engineers can test different impeller designs and materials in real-world conditions, making necessary adjustments before final production. This accelerates the development cycle and leads to more optimized and reliable components.
- Integration of Features and Reduced Assembly: Metal 3D printing can enable the integration of multiple components into a single part, reducing the need for assembly and the associated costs and potential points of failure. For example, features like balancing weights or specific mounting interfaces can be directly incorporated into the impeller design.
- Tailored Material Properties: By carefully selecting and processing metal powders, the material properties of 3D printed impellers can be optimized for specific marine applications. This includes enhancing corrosion resistance, increasing strength-to-weight ratio, and improving wear resistance in harsh operating conditions. Metal3DP’s expertise in advanced metal powders ensures that customers can select the ideal material for their marine impeller applications.
- Supply Chain Flexibility: Metal 3D printing can decentralize the manufacturing process, allowing for the production of impellers closer to the point of need. This can reduce lead times, transportation costs, and reliance on complex global supply chains, enhancing operational agility.
Considering these advantages, it’s clear why metal 3D printing is becoming an increasingly attractive option for the marine industry seeking high-performance, durable, and efficiently produced pump impellers.
Recommended Materials: CuNi30Mn1Fe and 316L for Superior Marine Performance
The selection of the appropriate material is paramount for the performance and longevity of marine pump impellers, given the corrosive nature of seawater and the demanding operational conditions. Metal3DP offers a range of high-quality metal powders specifically suited for marine applications, with CuNi30Mn1Fe and 316L stainless steel being particularly noteworthy for their excellent properties:
1. CuNi30Mn1Fe (Copper-Nickel Alloy):
This copper-nickel alloy, with approximately 30% nickel and additions of manganese and iron, is renowned for its exceptional resistance to seawater corrosion and biofouling. These properties make it an ideal choice for marine impellers that require long-term reliability in direct contact with seawater.
- Superior Corrosion Resistance: Copper-nickel alloys naturally resist the corrosive effects of saltwater, including pitting and crevice corrosion, which are common challenges for materials in marine environments. The addition of nickel enhances this resistance, ensuring the impeller maintains its structural integrity and performance over extended periods.
- Excellent Biofouling Resistance: The copper content in CuNi30Mn1Fe inhibits the growth and attachment of marine organisms such as algae, barnacles, and mussels. Biofouling can significantly reduce the efficiency of pump impellers by increasing surface roughness and flow resistance. Using this alloy helps maintain optimal hydraulic performance and reduces the need for frequent cleaning and maintenance.
- Good Mechanical Properties: Despite its excellent corrosion and biofouling resistance, CuNi30Mn1Fe also exhibits good strength and ductility, allowing impellers to withstand the mechanical stresses encountered during pump operation.
- Thermal Conductivity: Copper-nickel alloys have relatively high thermal conductivity, which can be beneficial in applications where heat dissipation is a concern.
2. 316L Stainless Steel:
316L is an austenitic stainless steel alloyed with molybdenum and a low carbon content. It offers enhanced corrosion resistance compared to standard 304 stainless steel, making it a widely used material in marine and offshore applications.
- Enhanced Corrosion Resistance: The addition of molybdenum in 316L significantly improves its resistance to pitting and crevice corrosion, particularly in chloride-rich environments like seawater. The low carbon content minimizes carbide precipitation during welding or high-temperature processing, further enhancing its corrosion resistance.
- Good Strength and Ductility: 316L stainless steel possesses excellent mechanical properties, including high tensile strength and good ductility, ensuring the impeller can withstand operational stresses and potential impacts.
- Weldability and Fabricability: 316L is readily weldable and can be easily fabricated using metal 3D printing techniques, allowing for complex impeller designs to be realized.
- Wide Availability and Cost-Effectiveness: Compared to some specialized marine alloys, 316L is widely available and generally more cost-effective, making it a practical choice for many marine pump impeller applications where a balance of performance and cost is required.
The choice between CuNi30Mn1Fe and 316L will depend on the specific requirements of the application, including the level of corrosion and biofouling resistance needed, the mechanical loads involved, and budgetary considerations. Metal3DP’s advanced powder making system ensures that both these high-quality metal powders are produced with high sphericity and good flowability, essential for achieving dense, high-performance 3D printed impellers. Our team of experts can provide guidance on selecting the optimal material for your specific marine pump impeller needs.
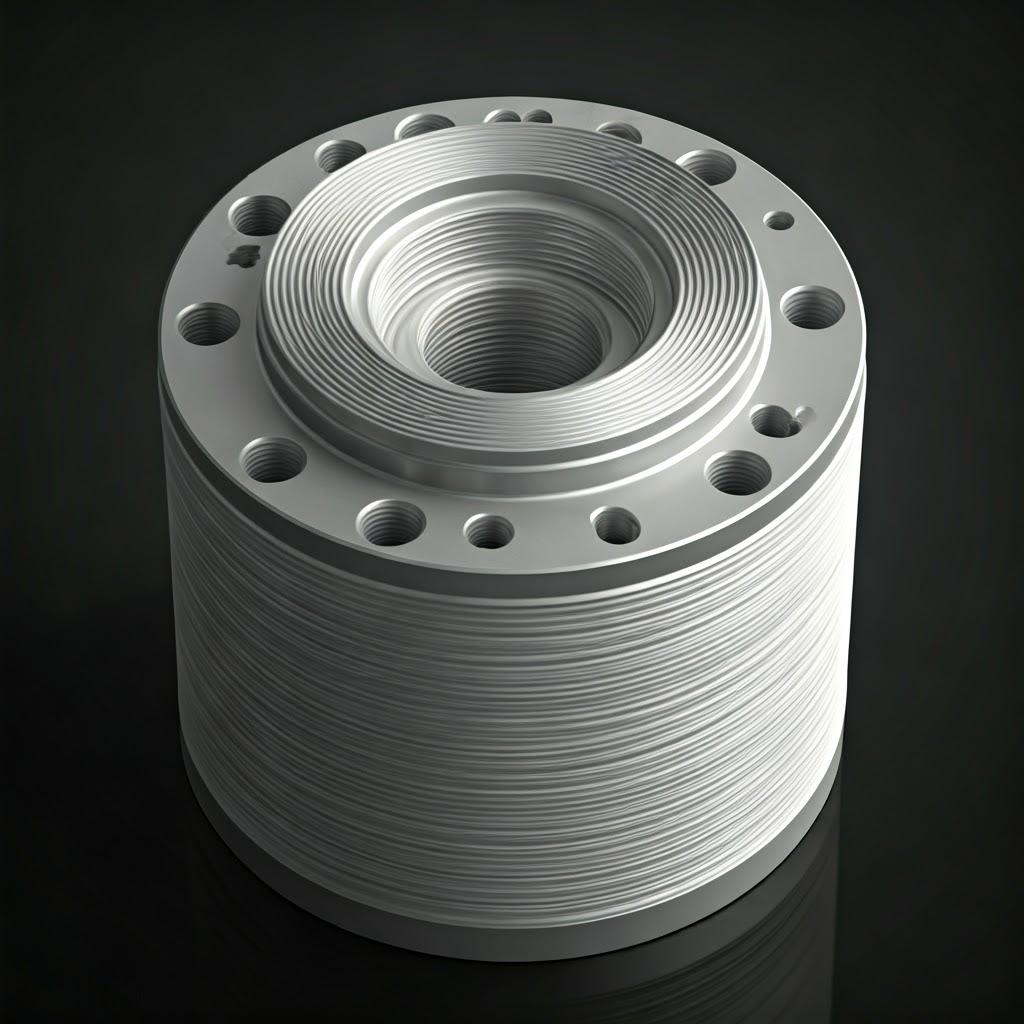
Design Optimization for Additive Manufacturing of Marine Impellers
Designing marine pump impellers for metal 3D printing requires a shift in mindset compared to traditional manufacturing. The layer-by-layer build process unlocks design freedoms that can lead to significant improvements in performance, weight reduction, and functionality. Here are key design considerations for optimizing impellers for additive manufacturing:
- Hydrodynamic Efficiency: Leverage the ability to create complex blade geometries, such as double curvature and varying blade angles, to optimize fluid flow and minimize energy losses. Computational Fluid Dynamics (CFD) analysis should be an integral part of the design process to simulate and refine the impeller’s hydraulic performance. Consider incorporating features like splitter blades or inducer sections to further enhance efficiency, particularly under varying flow conditions.
- Weight Optimization: Metal 3D printing allows for the creation of internal lattice structures and hollow features that can significantly reduce the weight of the impeller without compromising its structural integrity. This is particularly beneficial in applications where rotational inertia and overall system weight are critical factors. Careful stress analysis using Finite Element Analysis (FEA) should guide the design of these lightweighting features to ensure they can withstand operational loads.
- Material Distribution and Stress Management: Optimize the distribution of material within the impeller to align with the expected stress patterns. Additive manufacturing allows for the strategic placement of material only where it is needed, enhancing strength in critical areas while reducing mass in lower-stress regions. Consider the orientation of the part during the printing process, as this can influence the mechanical properties in different directions.
- Integration of Features: Explore the possibility of integrating features directly into the impeller design that would typically require secondary operations or additional components in traditional manufacturing. This could include balancing features, specific mounting interfaces, or even sensors for monitoring performance. Reducing the number of parts and assembly steps can lead to cost savings and improved reliability.
- Surface Finish Considerations: The as-printed surface finish of a metal 3D printed part can impact its hydraulic performance and resistance to biofouling. Design considerations should include minimizing sharp angles and overhangs that might result in rougher surfaces. Post-processing techniques, as discussed in a later section, can be planned for at the design stage to achieve the desired surface finish.
- Support Structure Optimization: Support structures are often necessary in metal 3D printing to prevent collapse and ensure dimensional accuracy during the build process. Designing the part with self-supporting angles and minimizing the need for extensive support structures can reduce material waste and post-processing time. Consider the ease of support removal when orienting the part for printing.
- Thermal Management: In some high-performance pump applications, managing heat generated by fluid friction or the pump motor can be important. Additive manufacturing allows for the incorporation of internal cooling channels within the impeller design to dissipate heat more effectively.
- Cavitation Resistance: Cavitation, the formation and collapse of vapor bubbles in the fluid, can severely damage impeller blades. Design features aimed at minimizing pressure drops and ensuring smooth flow can help mitigate cavitation. Consider blade thickness profiles and leading-edge designs that are less susceptible to cavitation.
By carefully considering these design aspects, engineers can fully leverage the capabilities of metal 3D printing to create marine pump impellers that offer superior performance, durability, and efficiency compared to those produced using traditional methods. Metal3DP’s comprehensive understanding of both metal additive manufacturing processes and material science ensures that our customers can achieve these optimized designs effectively.
Achieving Precision: Tolerance, Surface Finish, and Dimensional Accuracy of 3D Printed Impellers
In the realm of marine pump impellers, where performance and reliability are paramount, the tolerance, surface finish, and dimensional accuracy of the manufactured components are critical. Metal 3D printing has evolved significantly in its ability to achieve tight specifications, making it a viable option for producing impellers that meet the demanding requirements of marine applications.
- Tolerance Capabilities: Modern metal 3D printing technologies, such as Selective Laser Melting (SLM) and Electron Beam Melting (EBM), can achieve impressive dimensional tolerances. Typically, tolerances in the range of pm0.1 to pm0.05 mm can be achieved for critical features. However, the achievable tolerance can be influenced by factors such as part geometry, size, material, and the specific printing process and machine used. For marine impellers, critical dimensions such as blade profiles, hub diameter, and mounting features can be produced with sufficient accuracy to ensure proper fit and function within the pump assembly.
- Surface Finish: The as-printed surface finish in metal 3D printing is generally rougher compared to machined surfaces, typically ranging from R_a 5-20 µm depending on the process and powder particle size. For hydraulic components like impellers, a smoother surface finish is often desirable to minimize friction losses and improve efficiency. Post-processing techniques such as polishing, abrasive flow machining, or chemical etching can be employed to achieve smoother surface finishes down to R_a 1-0.2 µm or even finer, depending on the application requirements. The choice of powder material and the printing parameters also play a role in the initial surface roughness.
- Dimensional Accuracy: Dimensional accuracy refers to the degree to which the printed part matches the intended design dimensions. Metal 3D printing has made significant strides in this area, with high-precision machines and optimized process parameters capable of producing parts with excellent conformity to the CAD model. Factors affecting dimensional accuracy include thermal shrinkage during solidification, support structure deformation, and the inherent resolution of the printing process. Careful process control, optimized build orientation, and appropriate support structure design are crucial for achieving high dimensional accuracy in 3D printed marine impellers.
- Factors Influencing Precision: Several factors influence the achievable tolerance, surface finish, and dimensional accuracy in metal 3D printing:
- Printing Technology: SLM generally offers finer feature resolution and potentially better surface finish compared to EBM, although EBM can be advantageous for larger parts and certain materials.
- Powder Characteristics: The size, shape, and distribution of the metal powder particles significantly impact the surface finish and the level of detail that can be achieved. Metal3DP’s advanced powder making system ensures high sphericity and flowability, contributing to improved precision.
- Process Parameters: Laser power, scan speed, layer thickness, and build orientation are critical process parameters that must be carefully optimized to achieve the desired precision.
- Post-Processing: As mentioned earlier, various post-processing techniques can significantly improve the surface finish and dimensional accuracy of 3D printed parts.
- Machine Calibration and Maintenance: Regular calibration and maintenance of the 3D printing equipment are essential for ensuring consistent and accurate results.
By understanding these factors and leveraging the capabilities of advanced metal 3D printing technologies and appropriate post-processing methods, it is possible to produce marine pump impellers with the precision required for demanding applications.
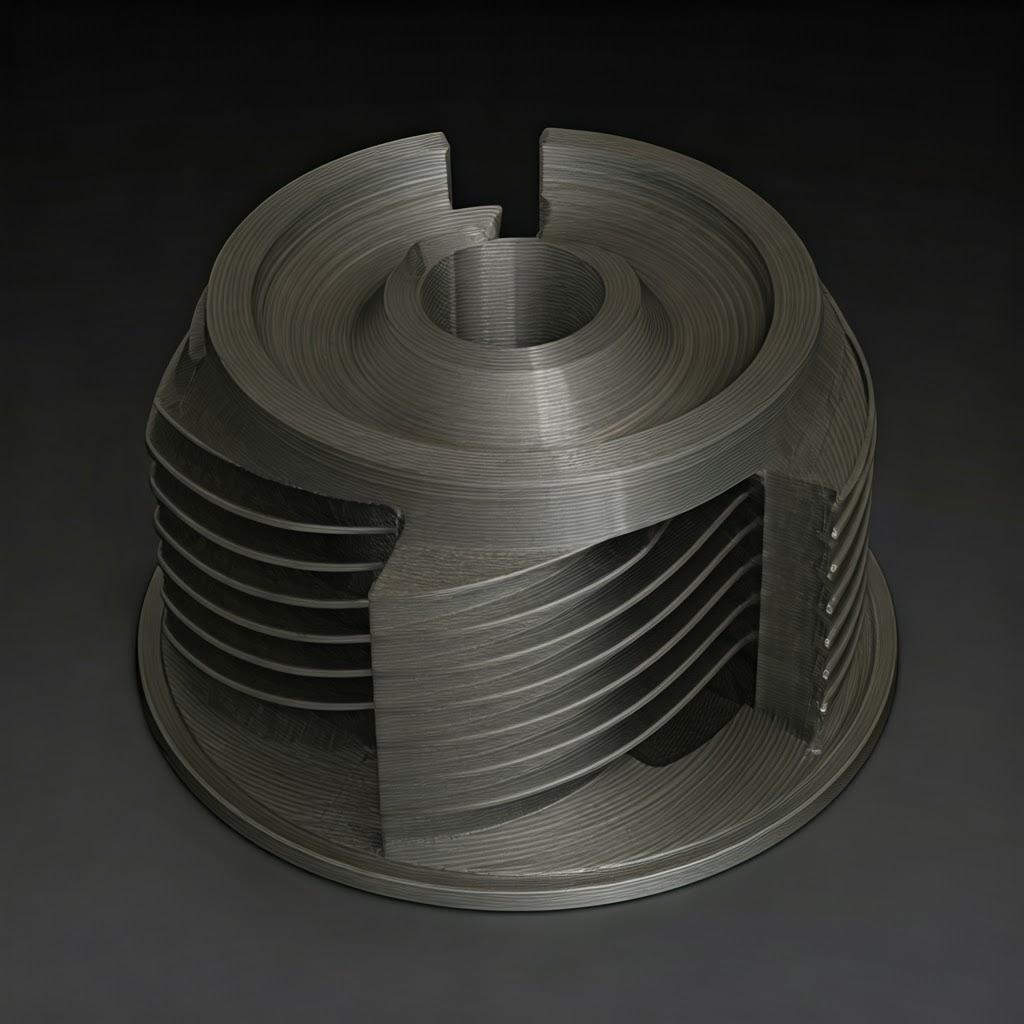
Post-Processing Techniques for Marine-Grade Impellers
While metal 3D printing offers significant advantages in terms of design freedom and material efficiency, post-processing steps are often necessary to achieve the final desired properties and performance for marine-grade impellers. These techniques can enhance surface finish, improve mechanical properties, and ensure the longevity of the components in harsh marine environments:
- Heat Treatment: Stress relief annealing is a common post-processing step for metal 3D printed parts to reduce internal stresses that may have built up during the rapid solidification process. For certain alloys, other heat treatments like hardening and tempering can be applied to achieve the desired strength and hardness characteristics required for demanding impeller applications. The specific heat treatment cycle will depend on the material and the intended service conditions.
- Surface Finishing: As discussed earlier, the as-printed surface roughness may not be optimal for hydraulic performance or resistance to biofouling. Several surface finishing techniques can be employed:
- Polishing: Mechanical polishing using abrasive media can significantly reduce surface roughness, leading to improved fluid flow and reduced friction.
- Abrasive Flow Machining (AFM): This process involves forcing an abrasive-laden fluid through the internal passages and over the external surfaces of the impeller, effectively smoothing complex geometries.
- Chemical Etching: Controlled chemical removal of surface layers can also improve surface finish, particularly for intricate features.
- Media Blasting: Techniques like shot peening can not only improve surface finish but also enhance fatigue resistance by introducing compressive stresses on the surface.
- Machining: In cases where very tight tolerances are required for critical features such as the impeller bore or mounting surfaces, precision CNC machining can be used as a secondary operation to achieve the final dimensions and surface finish.
- Balancing: For rotating components like pump impellers, dynamic balancing is crucial to minimize vibrations and ensure smooth operation, extending the lifespan of the pump and reducing noise. This process involves identifying and correcting any imbalance by adding or removing small amounts of material.
- Coating: To further enhance corrosion and biofouling resistance in aggressive marine environments, various coatings can be applied to 3D printed impellers:
- Electropolishing: This electrochemical process can create a smooth, passive layer on stainless steel alloys, improving their corrosion resistance.
- Ceramic Coatings: These coatings offer excellent hardness, wear resistance, and corrosion protection.
- Polymer Coatings: Specialized marine-grade polymer coatings can provide effective protection against saltwater corrosion and biofouling.
- Sacrificial Coatings: For certain applications, sacrificial coatings that corrode preferentially can protect the underlying impeller material.
- Non-Destructive Testing (NDT): Techniques like dye penetrant inspection or ultrasonic testing can be used to ensure the structural integrity of the 3D printed impellers and detect any internal flaws or surface defects that may have occurred during the printing process.
The selection of appropriate post-processing techniques will depend on the specific material, the intended application, and the performance requirements of the marine pump impeller. A well-defined post-processing strategy is essential to realize the full potential of metal 3D printing for producing high-quality, durable components for the marine industry.
Common Challenges and How to Avoid Them in 3D Printing Marine Impellers
While metal 3D printing offers numerous advantages for producing marine pump impellers, several challenges need to be addressed to ensure successful and reliable outcomes:
- Corrosion Resistance: The marine environment is highly corrosive, and not all metals are suitable for prolonged exposure to saltwater. Challenge: Ensuring the 3D printed impeller material possesses adequate corrosion resistance to prevent premature failure. Solution: Select marine-grade alloys like CuNi30Mn1Fe or 316L, as recommended by Metal3DP, which are known for their excellent resistance to saltwater corrosion. Consider post-processing treatments like electropolishing or protective coatings for added defense.
- Cavitation: The rapid formation and collapse of vapor bubbles in low-pressure areas within the pump can cause significant damage to the impeller surface. Challenge: Designing impellers that minimize cavitation and selecting materials that can withstand its effects. Solution: Optimize the impeller design using CFD analysis to reduce pressure drops and ensure smooth flow. Consider materials with higher hardness and fatigue strength. Surface hardening post-processing techniques can also improve cavitation resistance.
- Biofouling: The accumulation of marine organisms on the impeller surface can reduce efficiency and increase wear. Challenge: Preventing or minimizing biofouling. Solution: Utilizing materials like CuNi30Mn1Fe, which naturally resists biofouling, is a primary strategy. Smooth surface finishes achieved through post-processing can also make it harder for organisms to attach. Anti-fouling coatings can provide an additional layer of protection.
- Dimensional Accuracy and Warping: Achieving precise dimensions and preventing warping during the 3D printing process can be challenging, especially with complex geometries and large parts. Challenge: Ensuring the impeller meets the required tolerances and maintains its intended shape. Solution: Optimize the build orientation, use appropriate support structures, and carefully control the printing parameters. Stress relief heat treatment after printing can help mitigate warping. Precision machining of critical features as a post-processing step can ensure tight tolerances.
- Porosity and Internal Defects: Metal 3D printed parts can sometimes exhibit internal porosity or other defects that can compromise their mechanical strength and fatigue life. Challenge: Producing dense, defect-free impellers. Solution: Employ high-quality metal powders with good flowability, such as those produced by Metal3DP’s, and optimize the printing parameters to promote full melting and solidification. Hot Isostatic Pressing (HIP) can be used as a post-processing step to reduce porosity and improve density. Non-destructive testing can help identify any internal flaws.
- Surface Roughness: The as-printed surface can be too rough for optimal hydraulic performance. Challenge: Achieving a smooth surface finish. Solution: Employ appropriate post-processing techniques like polishing, abrasive flow machining, or chemical etching to reduce surface roughness and improve efficiency.
- Support Structure Removal: Removing support structures from complex impeller geometries can be challenging and may leave surface marks. Challenge: Efficient and damage-free removal of support structures. Solution: Design the impeller with self-supporting angles where possible and optimize the support structure design for easy removal. Techniques like dissolvable supports can be used in some cases. Careful manual removal or specialized tools can minimize surface damage.
- Cost and Lead Time: While 3D printing can offer cost and lead time advantages in certain scenarios, these factors need careful consideration, especially for large-scale production. Challenge: Ensuring cost-effectiveness and meeting production timelines. Solution: Optimize the design for efficient printing, choose appropriate materials and printing processes based on cost and performance requirements, and select a reliable 3D printing service provider like Metal3DP with efficient production capabilities.
By understanding these potential challenges and implementing appropriate design strategies, material selection, printing parameters, and post-processing techniques, the marine industry can successfully leverage metal 3D printing to produce high-performance and durable pump impellers.
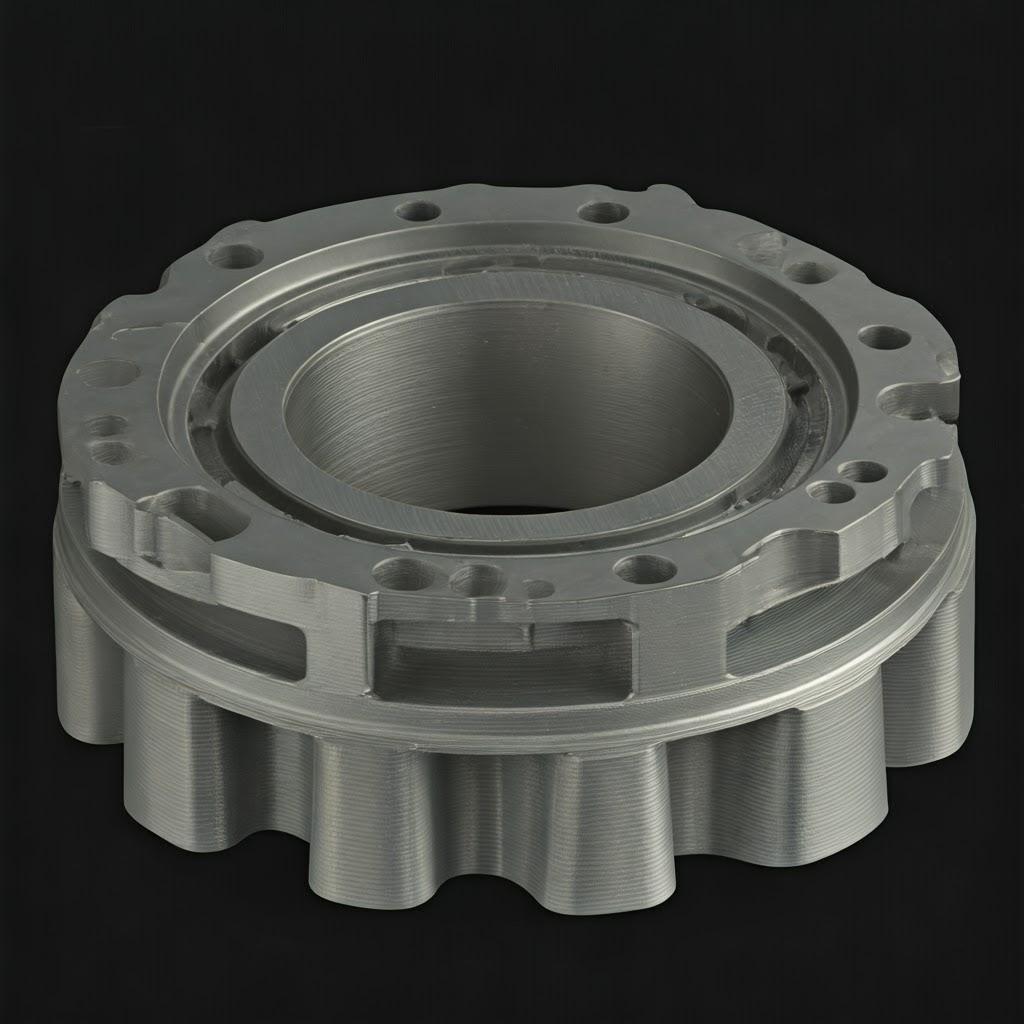
How to Choose the Right Metal 3D Printing Service Provider for Marine Components
Selecting the right metal 3D printing service provider is crucial for obtaining high-quality marine pump impellers that meet stringent performance and durability requirements. Here are key factors to consider when evaluating potential suppliers:
- Expertise in Metal Additive Manufacturing: Look for a provider with a proven track record and deep expertise in metal 3D printing technologies, particularly those relevant to the materials and geometries required for marine impellers (e.g., SLM, DMLS, EBM). Inquire about their experience with the specific metal powders you need, such as CuNi30Mn1Fe and 316L, and their ability to optimize printing parameters for these materials. Metal3DP boasts decades of collective expertise in metal additive manufacturing, specializing in both equipment and high-performance metal powders.
- Material Capabilities and Certifications: Ensure the service provider offers the specific marine-grade metal alloys you require and possesses the necessary material certifications and quality control processes. They should be able to provide material data sheets and demonstrate traceability of their powders.
- Design and Engineering Support: A strong service provider will offer design and engineering support to optimize your impeller design for additive manufacturing. This includes guidance on design for additive manufacturing (DfAM) principles, material selection, and performance optimization using tools like CFD and FEA. Metal3DP provides comprehensive solutions, including application development services, to help you leverage the full potential of metal 3D printing.
- Post-Processing Capabilities: As discussed earlier, post-processing is often essential for marine impellers. Evaluate the provider’s in-house or partnered capabilities for heat treatment, surface finishing (polishing, coating), machining, and balancing. Ensure they have experience in post-processing marine-grade alloys.
- Quality Assurance and Inspection: A reliable provider will have robust quality assurance processes in place, including dimensional inspection, material testing, and non-destructive testing (NDT) methods. They should be able to provide inspection reports and certifications to ensure the impellers meet your specifications.
- Production Capacity and Lead Times: Consider the service provider’s production capacity and typical lead times, especially if you have ongoing or large-volume requirements. Discuss their ability to scale production to meet your future needs.
- Industry Experience and References: Look for a provider with experience serving the marine or related industries (e.g., aerospace, oil & gas) where similar demands for high-performance, corrosion-resistant components exist. Request references or case studies to assess their track record and customer satisfaction.
- Communication and Customer Support: Effective communication and responsive customer support are crucial for a successful partnership. Evaluate the provider’s responsiveness, technical expertise, and willingness to collaborate throughout the project lifecycle.
- Cost Competitiveness: While quality and expertise should be primary considerations, cost-effectiveness is also important. Obtain detailed quotes and understand the pricing structure, including any costs for design optimization, post-processing, and quality assurance.
- Location and Logistics: Depending on your location and logistical requirements, the geographic location of the service provider and their shipping capabilities may also be a factor. Metal3DP is headquartered in Qingdao, China, and serves customers globally.
By carefully evaluating potential metal 3D printing service providers based on these criteria, you can select a partner that can reliably produce high-quality marine pump impellers tailored to your specific needs.
Cost Factors and Lead Time Advantages of 3D Printed Marine Impellers
Understanding the cost factors and lead time implications of using metal 3D printing for marine pump impellers is essential for making informed decisions. While the initial perception might be that 3D printing is always more expensive, a closer look reveals nuanced advantages, particularly in certain scenarios:
- Cost Factors:
- Material Costs: The cost of metal powders can be a significant factor. Specialized marine-grade alloys like CuNi30Mn1Fe can be more expensive than standard materials like 316L. However, the buy-to-fly ratio in additive manufacturing is often much higher than in subtractive methods, meaning less material is wasted, potentially offsetting some of the initial powder cost. Metal3DP focuses on producing high-quality metal powders optimized for efficiency.
- Printing Time: The build time depends on the complexity, size, and volume of the impeller, as well as the chosen printing technology. Longer print times translate to higher machine usage costs. Optimizing the design for efficient printing and part nesting (printing multiple parts simultaneously) can help reduce this cost.
- Post-Processing Costs: The extent of post-processing required (e.g., heat treatment, surface finishing, machining) will add to the overall cost. Minimizing the need for extensive post-processing through design optimization can be beneficial.
- Design and Engineering Costs: Initial design optimization for additive manufacturing may involve engineering time and potentially CFD or FEA analysis, which can incur costs. However, a well-optimized design can lead to long-term savings through improved performance and reduced material usage.
- Tooling Costs: Unlike traditional methods like casting or forging, metal 3D printing typically does not require expensive molds or tooling, which can result in significant cost savings for low to medium production volumes and for customized designs.
- Labor Costs: While the 3D printing process is largely automated, skilled labor is required for machine setup, operation, post-processing, and quality control.
- Lead Time Advantages:
- Rapid Prototyping: Metal 3D printing significantly reduces the lead time for producing prototypes compared to traditional methods that require tooling. This allows for faster design iteration and validation.
- On-Demand Manufacturing: The ability to produce impellers on demand eliminates the need for long lead times associated with ordering and shipping traditionally manufactured parts, especially for obsolete or specialized components. This can be crucial for minimizing downtime in marine operations.
- Reduced Supply Chain Complexity: 3D printing can potentially simplify supply chains by enabling localized production, reducing reliance on multiple suppliers and long transportation times.
- Faster Production for Low to Medium Volumes: For small to medium production runs, metal 3D printing can often offer faster lead times compared to traditional manufacturing processes that involve tooling setup.
- Customization without Delay: Customizing impeller designs for specific applications can be done quickly with 3D printing without the delays associated with modifying or creating new tooling.
In summary, the cost-effectiveness and lead time advantages of using metal 3D printing for marine pump impellers are highly dependent on factors such as production volume, part complexity, material choice, and the extent of post-processing required. For low to medium volumes, highly complex geometries, and customized parts, metal 3D printing often presents a compelling economic case and significant lead time reductions. As the technology continues to advance and material costs evolve, the benefits of 3D printing for marine applications are likely to become even more pronounced.
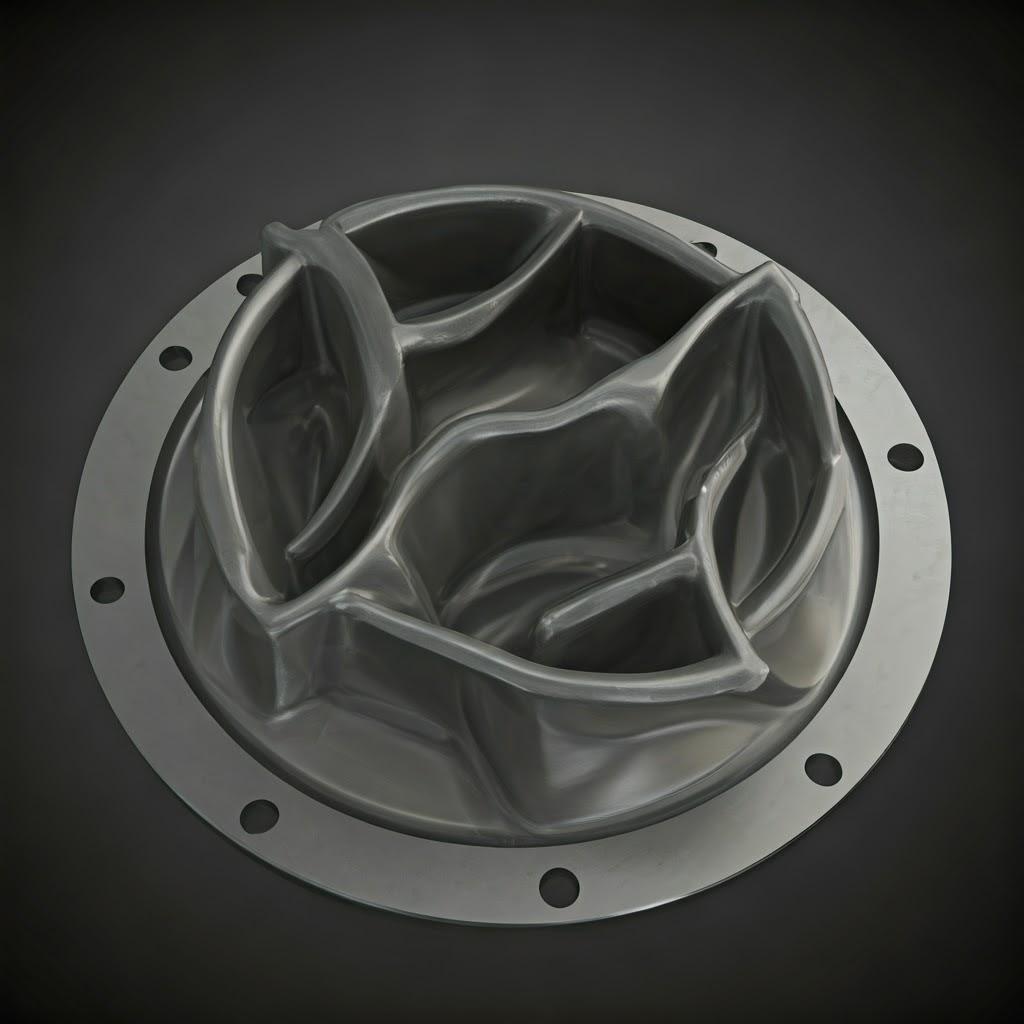
Frequently Asked Questions (FAQ) About 3D Printed Marine Pump Impellers
Here are some frequently asked questions regarding the use of metal 3D printing for marine pump impellers:
- Q: Are 3D printed metal impellers strong enough for demanding marine applications? A: Yes, when the appropriate marine-grade alloys are used and the printing process is optimized, 3D printed metal impellers can achieve mechanical properties comparable to or even exceeding those of traditionally manufactured parts. Materials like CuNi30Mn1Fe and 316L offer excellent strength and durability for demanding marine environments. Proper post-processing, such as heat treatment and HIP, can further enhance their mechanical properties.
- Q: How does the corrosion resistance of 3D printed impellers compare to cast or machined impellers? A: The corrosion resistance of a 3D printed impeller largely depends on the material used. When marine-grade alloys like CuNi30Mn1Fe and 316L are employed, the 3D printed impellers can exhibit comparable or even superior corrosion resistance due to the homogeneity of the material and the potential for optimized microstructures achieved through controlled printing processes. Post-processing treatments like electropolishing can further enhance corrosion resistance.
- Q: Can metal 3D printing produce impellers with the required dimensional accuracy for marine pumps? A: Yes, modern metal 3D printing technologies can achieve tight tolerances and high dimensional accuracy suitable for marine pump impellers. Careful process control, optimized build orientation, and post-processing techniques like precision machining for critical features ensure that the impellers meet the required specifications for fit and performance.
- Q: What is the typical lead time for 3D printed marine impellers? A: Lead times can vary depending on the complexity and size of the impeller, the chosen material and printing process, and the service provider’s capacity. However, for prototypes and low to medium volume production, metal 3D printing generally offers significantly shorter lead times compared to traditional manufacturing methods that require tooling. On-demand production of spare parts can also drastically reduce downtime.
- Q: Are 3D printed metal impellers cost-effective for marine applications? A: The cost-effectiveness depends on factors such as production volume, part complexity, and material choice. For low to medium volumes, highly customized designs, and parts with intricate geometries, metal 3D printing can be very cost-competitive due to the elimination of tooling costs and reduced material waste. The long-term benefits of improved performance and durability should also be considered.
- Q: Can 3D printed impellers be used in existing marine pump systems? A: Yes, 3D printed impellers can be designed to match the specifications of existing pump systems. This is particularly advantageous for replacing obsolete or hard-to-find parts. Reverse engineering and 3D scanning can be used to create digital models of existing impellers for 3D printing.
Conclusion: Navigating the Future of Marine Pump Technology with Metal 3D Printing
Metal 3D printing is no longer a futuristic concept in the marine industry; it is a tangible and increasingly vital technology for the design and manufacture of critical components like pump impellers. The ability to create complex geometries, utilize high-performance marine-grade alloys such as CuNi30Mn1Fe and 316L, and achieve rapid production cycles offers significant advantages over traditional manufacturing methods.
From enhancing hydrodynamic efficiency and reducing weight to enabling on-demand spare parts production and customized designs, metal 3D printing empowers engineers and procurement managers in the marine sector to overcome traditional limitations and drive innovation. By addressing challenges such as corrosion, cavitation, and dimensional accuracy through careful material selection, optimized design, and appropriate post-processing techniques, 3D printed marine pump impellers are proving to be a reliable and effective solution for a wide range of applications.
As the marine industry continues to prioritize efficiency, sustainability, and operational reliability, the role of metal 3D printing will only become more prominent. Companies like Metal3DP are at the forefront of this evolution, providing cutting-edge metal 3D printing equipment, advanced metal powders, and comprehensive application development services to help the marine industry navigate the future of manufacturing. Embracing metal 3D printing is not just about adopting a new technology; it’s about unlocking new possibilities for performance, durability, and cost-effectiveness in marine pump technology and beyond. Contact Metal3DP today to explore how our capabilities can power your organization’s additive manufacturing goals in the marine sector.
Share On
MET3DP Technology Co., LTD is a leading provider of additive manufacturing solutions headquartered in Qingdao, China. Our company specializes in 3D printing equipment and high-performance metal powders for industrial applications.
Inquiry to get best price and customized Solution for your business!
Related Articles
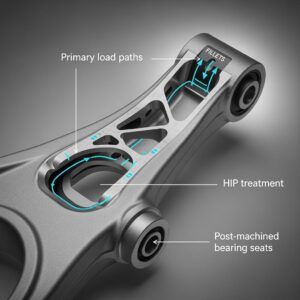
Metal 3D Printing for U.S. Automotive Lightweight Structural Brackets and Suspension Components
Read More »About Met3DP
Recent Update
Our Product
CONTACT US
Any questions? Send us message now! We’ll serve your request with a whole team after receiving your message.