The Power of Metal 3D Printing for Custom Pump Volute Manufacturing
Table of Contents
In today’s rapidly evolving industrial landscape, the demand for high-performance, customized components is constantly increasing. Metal 3D printing, also known as metal additive manufacturing, stands at the forefront of this revolution, offering unprecedented design freedom and manufacturing flexibility. For critical components like pump volutes, this technology unlocks new possibilities for optimizing performance, reducing lead times, and achieving complex geometries that were previously unattainable with traditional manufacturing methods. At https://met3dp.com/, we are dedicated to providing cutting-edge metal 3D printing solutions that empower engineers and procurement managers across diverse industries to realize these benefits. Our expertise in advanced printing technologies and high-quality metal powders ensures that your custom pump volutes meet the most stringent performance requirements.
What are Custom Pump Volutes Used For? Exploring Key Applications and Industries
Pump volutes are essential components in centrifugal pumps, playing a crucial role in converting the kinetic energy of the rotating impeller into pressure energy of the fluid. Their intricate spiral design is critical for efficient fluid flow and optimal pump performance. Custom-designed volutes are particularly valuable in applications where standard, off-the-shelf solutions cannot meet specific performance demands or spatial constraints.
Here are some key applications and industries that benefit significantly from custom metal 3D printed pump volutes:
- Aerospace: In aerospace applications, pumps are used in various systems, including fuel delivery, hydraulic systems, and cooling. Custom volutes made with lightweight yet high-strength materials like IN625 can optimize pump efficiency and reduce overall weight, crucial factors in aircraft performance.
- Automotive: The automotive industry utilizes pumps for cooling systems, oil circulation, and fuel delivery. Metal 3D printing allows for the creation of complex volute geometries that improve fluid dynamics and engine efficiency, particularly in high-performance vehicles and electric vehicles where thermal management is critical.
- Medical: In the medical field, pumps are integral to drug delivery systems, dialysis machines, and surgical equipment. Custom volutes made from biocompatible materials like stainless steel or titanium alloys can be designed for precise flow control and device miniaturization.
- Industrial Manufacturing: Across various industrial sectors, pumps are used for fluid transfer in chemical processing, water treatment, and manufacturing processes. Custom volutes made from corrosion-resistant materials like CuNi30Mn1Fe or IN625 can withstand harsh operating environments and optimize process efficiency.
- Oil & Gas: The demanding conditions in the oil and gas industry require robust and reliable pumping solutions. Metal 3D printing enables the production of custom volutes with enhanced wear resistance and corrosion protection, crucial for long-term performance in challenging environments.
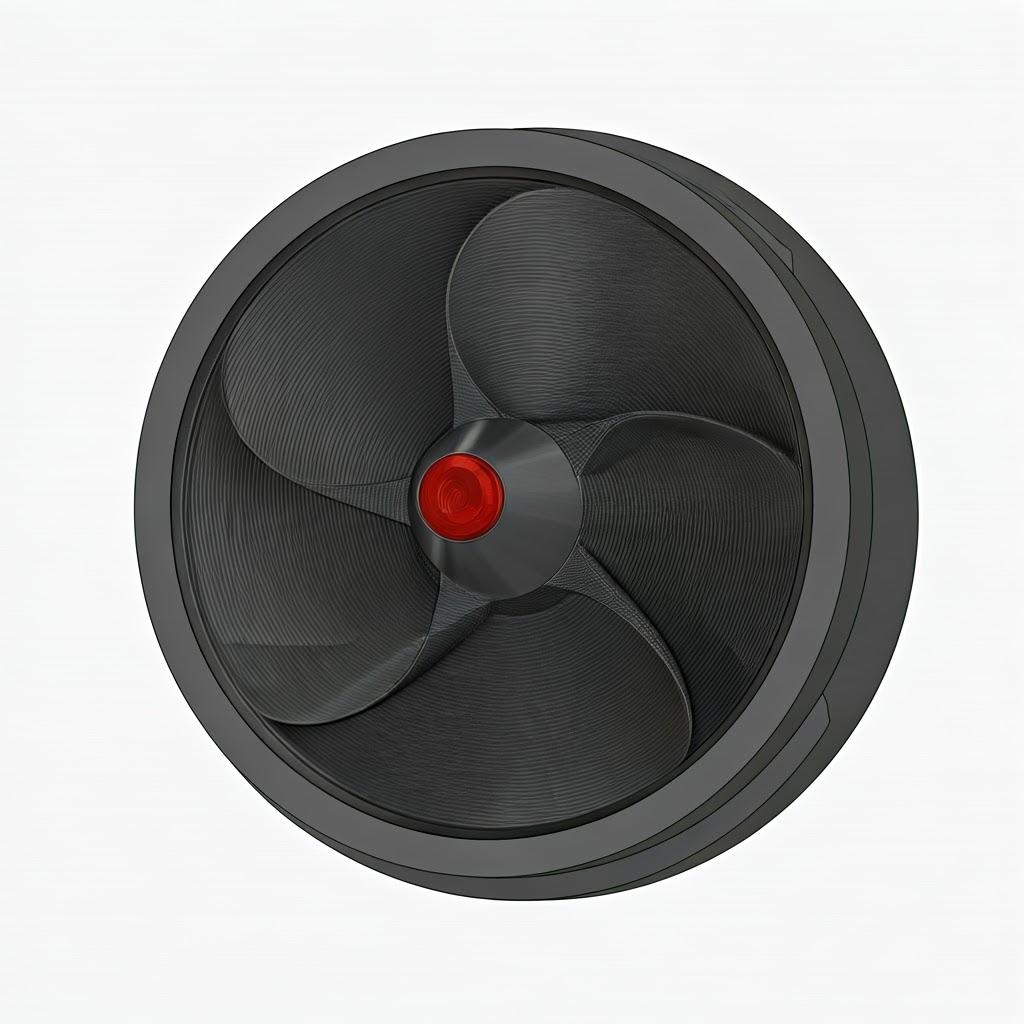
Why Choose Metal 3D Printing for Your Pump Volute Needs? Advantages Over Traditional Methods
Opting for metal 3D printing for the production of custom pump volutes offers a multitude of advantages compared to traditional manufacturing techniques such as casting, machining, or forging. These benefits translate to improved performance, reduced costs, and faster time-to-market:
- Design Freedom and Complexity: Additive manufacturing allows for the creation of intricate internal geometries and complex flow paths within the volute that are simply not possible with traditional methods. This design freedom enables engineers to optimize fluid dynamics for maximum efficiency and minimize energy losses.
- Material Efficiency: Metal 3D printing utilizes a layer-by-layer construction process, adding material only where needed. This significantly reduces material waste compared to subtractive methods like machining, leading to lower material costs, especially for expensive alloys.
- Rapid Prototyping and Iteration: The speed and flexibility of 3D printing enable rapid prototyping of different volute designs. Engineers can quickly iterate on designs, test performance, and make necessary adjustments without the long lead times associated with traditional tooling.
- Customization and On-Demand Manufacturing: Metal 3D printing is ideal for producing low to medium volumes of custom volutes tailored to specific application requirements. This eliminates the need for expensive tooling and large production runs, making it cost-effective for specialized pumps or replacement parts.
- Lightweighting: By optimizing the design and utilizing advanced materials like titanium alloys or high-performance nickel alloys available at https://met3dp.com/product/, metal 3D printing can produce lighter pump volutes without compromising structural integrity. This is particularly beneficial in weight-sensitive applications like aerospace and automotive.
- Integration of Features: Additive manufacturing allows for the integration of multiple components or features directly into the volute design, reducing the need for assembly and potential weak points. This can lead to improved reliability and performance.
Selecting the Right Materials: Understanding IN625 and CuNi30Mn1Fe for Optimal Performance
The choice of metal powder is critical for achieving the desired performance characteristics of a 3D printed pump volute. At Metal3DP, we offer a range of high-quality metal powders, including IN625 and CuNi30Mn1Fe, specifically optimized for additive manufacturing.
IN625 (Nickel-Chromium-Molybdenum Alloy)
IN625 is a high-performance nickel-based superalloy known for its exceptional strength, corrosion resistance, and high-temperature 1 performance. Its key properties make it an excellent choice for demanding pump volute applications:
- High Strength and Toughness: IN625 exhibits excellent tensile strength and toughness over a wide temperature range, making it suitable for high-pressure pumping applications.
- Exceptional Corrosion Resistance: This alloy demonstrates superior resistance to various corrosive environments, including seawater, acids, and alkaline solutions, making it ideal for applications in marine, chemical processing, and oil & gas industries.
- High-Temperature Performance: IN625 retains its mechanical properties at elevated temperatures, making it suitable for pumps handling hot fluids or operating in high-temperature environments.
- Excellent Weldability and Fabricability: While traditionally challenging to machine, IN625 is well-suited for the additive manufacturing process, allowing for the creation of complex geometries with good structural integrity.
CuNi30Mn1Fe (Copper-Nickel Alloy)
CuNi30Mn1Fe is a copper-nickel alloy with excellent corrosion resistance, particularly in seawater and other marine environments. Its key properties make it a suitable alternative for specific pump volute applications:
- Excellent Corrosion and Biofouling Resistance: This alloy exhibits high resistance to corrosion and the adhesion of marine organisms, making it ideal for pumps used in seawater desalination, marine cooling systems, and offshore applications.
- Good Thermal Conductivity: Copper-nickel alloys have good thermal conductivity, which can be beneficial in applications where heat dissipation is a concern.
- Moderate Strength and Ductility: While not as strong as IN625 at high temperatures, CuNi30Mn1Fe offers a good balance of strength and ductility for many pumping applications.
- Cost-Effectiveness: In some cases, CuNi30Mn1Fe can be a more cost-effective alternative to nickel-based superalloys while still providing adequate corrosion resistance.
The selection between IN625 and CuNi30Mn1Fe will depend on the specific performance requirements, operating environment, and cost considerations of your pump volute application. Our team at Metal3DP can provide expert guidance on material selection to ensure optimal results.
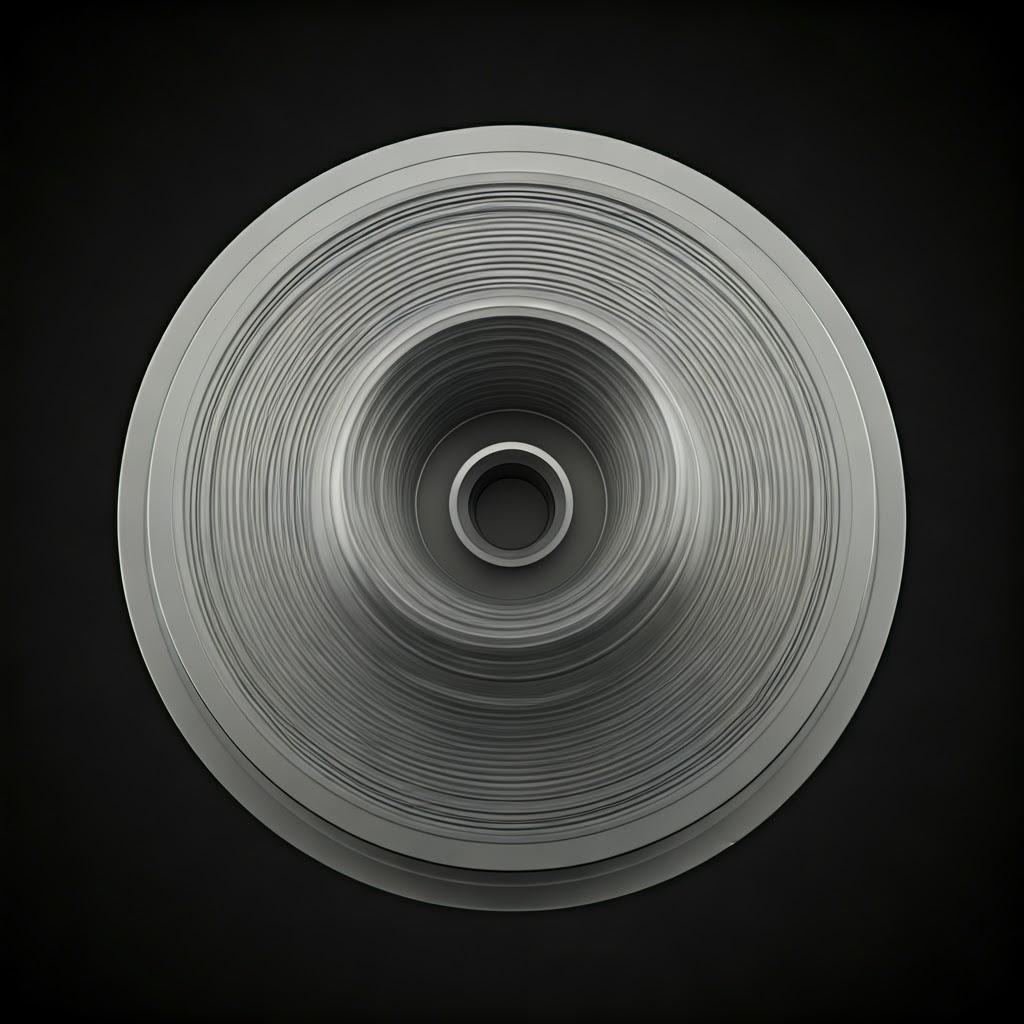
Design Optimization for 3D Printed Pump Volutes: Key Considerations for Efficiency and Flow
The unique capabilities of metal 3D printing open up exciting possibilities for optimizing the design of pump volutes. Unlike traditional manufacturing constraints, additive manufacturing allows for intricate internal features and complex geometries that can significantly enhance fluid flow and overall pump efficiency. Here are some key design considerations for 3D printed pump volutes:
- Internal Flow Channels: Metal 3D printing enables the creation of smooth, optimized internal flow channels with minimal sharp bends or restrictions. This reduces turbulence, minimizes energy losses due to friction, and improves the hydraulic efficiency of the pump. Consider incorporating features like airfoil-shaped vanes or gradually changing cross-sections to enhance flow linearity.
- Volute Tongue Design: The design of the volute tongue, the point where the fluid exits the impeller and enters the volute, is critical for minimizing pressure pulsations and noise. 3D printing allows for the creation of complex tongue geometries with varying radii and clearances to optimize the transition of fluid flow.
- Surface Finish of Internal Passages: The surface finish of the internal flow passages directly impacts frictional losses. While as-printed surfaces can be rougher than machined surfaces, careful process optimization and post-processing techniques (discussed later) can significantly improve surface smoothness, leading to enhanced efficiency.
- Wall Thickness and Structural Integrity: Optimizing the wall thickness of the volute is crucial for balancing weight and structural integrity. Finite element analysis (FEA) can be used in conjunction with the design freedom of 3D printing to create lightweight yet robust volutes that can withstand the operating pressures. Consider incorporating internal stiffening ribs or lattice structures in areas of high stress.
- Integration of Features: Metal 3D printing allows for the integration of features such as mounting points, sensor housings, or even cooling channels directly into the volute design. This reduces the need for secondary operations and simplifies assembly.
- Topology Optimization: Advanced design software and topology optimization algorithms can be used to generate highly efficient volute designs based on specific performance requirements and constraints. 3D printing is then used to realize these complex, organic shapes that would be impossible to manufacture conventionally. For insights into the possibilities, explore the capabilities discussed on our website at https://met3dp.com/printing-methods/.
Achieving Precision: Tolerance, Surface Finish, and Dimensional Accuracy in 3D Printed Volutes
In critical applications like pump systems, the tolerance, surface finish, and dimensional accuracy of the volute are paramount for ensuring optimal performance and longevity. Metal 3D printing technologies have made significant strides in achieving tight tolerances and good surface finishes. Here’s what you can expect:
- Dimensional Accuracy: Selective Laser Melting (SLM) and Electron Beam Melting (EBM), the primary metal 3D printing processes used at Metal3DP, can achieve dimensional accuracies typically ranging from ±0.1 to ±0.5 mm, depending on the part size and geometry. Critical dimensions can be further refined through post-processing.
- Tolerance: Achievable tolerances are closely linked to the printing process and part geometry. Generally, tolerances of ±0.2 mm are feasible for many features. For tighter tolerances, consider designing critical interfaces with slight undersize for subsequent machining.
- Surface Finish: The as-printed surface finish in metal 3D printing is typically rougher than that achieved by machining, with Ra (average roughness) values ranging from 5 to 20 μm depending on the material and printing parameters. This can be improved through various post-processing methods, such as:
- Media Blasting: Uses abrasive media to remove partially sintered powder and reduce surface roughness.
- Polishing: Mechanical or chemical polishing can achieve smoother surface finishes down to Ra values of less than 1 μm.
- CNC Machining: For critical surfaces requiring very tight tolerances and smooth finishes, precision CNC machining can be performed as a secondary operation.
- Factors Influencing Accuracy: Several factors can influence the dimensional accuracy and surface finish of 3D printed metal volutes, including:
- Printer Calibration and Maintenance: Regular calibration and maintenance of the 3D printer are crucial for consistent results.
- Material Properties: Different metal powders exhibit varying shrinkage rates and thermal behavior during the printing process, which can affect accuracy.
- Build Orientation: The orientation of the part during printing can impact surface finish and the need for support structures.
- Slicing Parameters: Parameters such as layer thickness, laser power, and scan speed significantly influence the final part quality.
At Metal3DP, we leverage our expertise in process optimization and post-processing techniques to ensure that your 3D printed pump volutes meet the required levels of precision and surface finish for your specific application. You can learn more about our capabilities on our services page at https://met3dp.com/metal-3d-printing/.
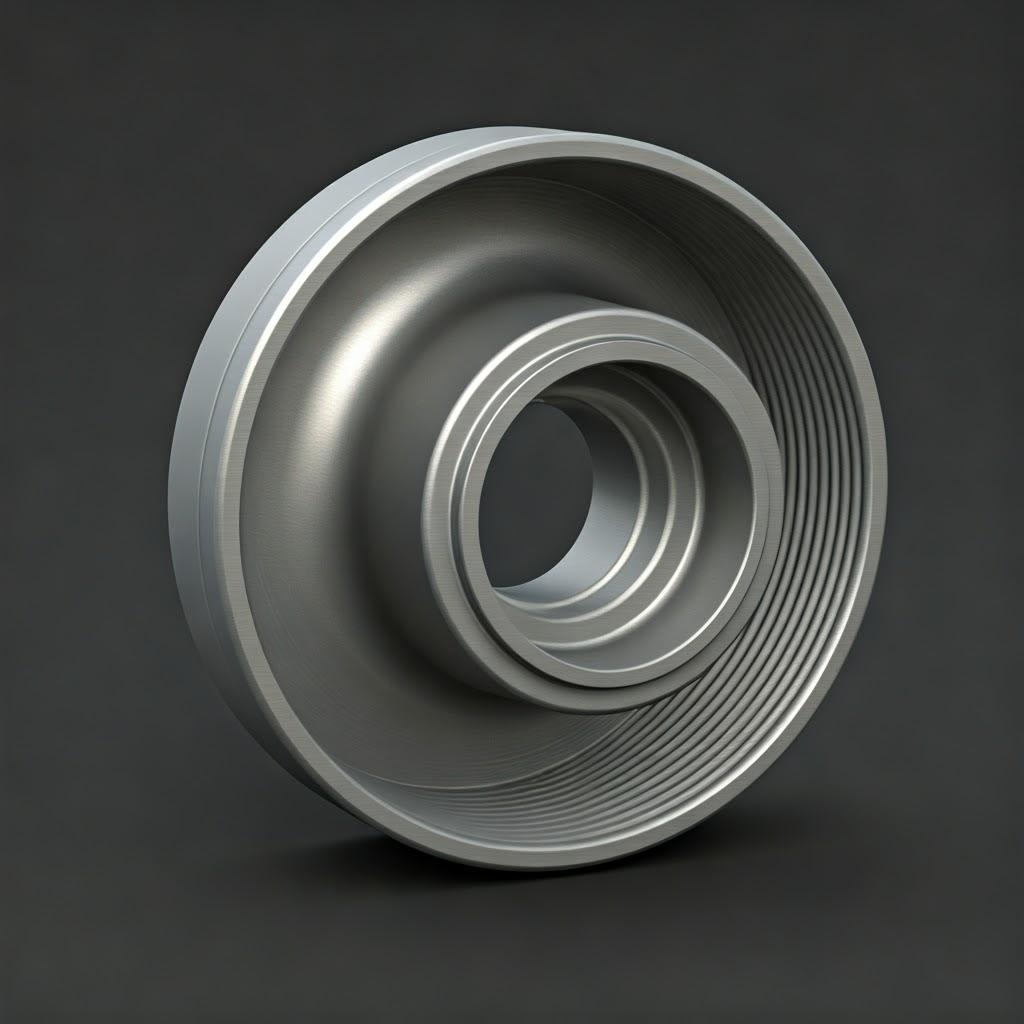
Streamlining Production: Post-Processing Techniques for Metal 3D Printed Volutes
While metal 3D printing offers significant advantages in creating complex geometries, post-processing steps are often necessary to achieve the final desired properties, surface finish, and dimensional accuracy of pump volutes. Here are some common post-processing techniques:
- Powder Removal: After the printing process, excess unsintered powder needs to be carefully removed from the part’s surfaces and internal channels. This is typically done using compressed air, brushes, or vacuum systems. For intricate internal geometries, specialized powder removal techniques may be required.
- Support Structure Removal: Support structures are often necessary to prevent warping and ensure the stability of overhanging features during printing. These supports need to be removed after the build is complete. The removal method depends on the support material and geometry and can involve manual breaking, cutting, or machining.
- Heat Treatment: Heat treatment is a crucial step for relieving internal stresses, optimizing the microstructure, and enhancing the mechanical properties of the 3D printed metal. Common heat treatment processes for materials like IN625 include stress relieving, annealing, and solution annealing followed by aging. The specific heat treatment cycle is tailored to the alloy and the desired properties.
- Surface Finishing: As discussed earlier, various surface finishing techniques can be employed to improve the surface roughness of the volute. These include media blasting, polishing (mechanical, chemical, or electrochemical), and vibratory finishing. The choice of method depends on the required surface finish and the part geometry.
- CNC Machining: For critical interfaces or features requiring very tight tolerances, precision CNC machining can be performed as a secondary operation. This ensures accurate mating surfaces and dimensional conformity.
- Coating and Surface Treatments: Depending on the application environment, coatings or surface treatments may be applied to enhance corrosion resistance, wear resistance, or other specific properties. Examples include electroplating, PVD coating, or ceramic coating.
- Inspection and Quality Control: Thorough inspection using techniques such as coordinate measuring machines (CMM), non-destructive testing (NDT) like ultrasonic testing or dye penetrant inspection, and material analysis is essential to ensure the quality and integrity of the 3D printed pump volutes.
At Metal3DP, we offer comprehensive post-processing services to ensure that your 3D printed pump volutes meet the highest standards of quality and performance. Our experienced team can advise on the most appropriate post-processing steps for your specific material and application.
Overcoming Challenges in Metal 3D Printing: Ensuring Quality and Reliability in Volute Manufacturing
While metal 3D printing offers numerous advantages, there are also potential challenges that need to be addressed to ensure the production of high-quality and reliable pump volutes. Understanding these challenges and implementing appropriate mitigation strategies is crucial.
- Warping and Distortion: Thermal stresses during the printing process can lead to warping or distortion of the part, particularly for complex geometries or large parts. Optimizing the build orientation, using appropriate support structures, and controlling the printing parameters can minimize these issues.
- Residual Stresses: The rapid heating and cooling cycles in metal 3D printing can induce residual stresses within the part. These stresses can affect the mechanical properties and dimensional stability. Post-printing heat treatment is essential for relieving residual stresses.
- Porosity: The formation of pores or voids within the printed part can compromise its mechanical strength and fatigue resistance. Optimizing printing parameters such as laser power, scan speed, and powder bed density is crucial for minimizing porosity. Our advanced powder making system, as highlighted on our https://met3dp.com/about-us/ page, ensures the high quality and flowability of our metal powders, which helps in reducing porosity.
- Support Structure Removal Damage: Improper removal of support structures can leave surface defects or damage delicate features of the volute. Careful design of support structures and the use of appropriate removal techniques are necessary.
- Surface Roughness: As mentioned earlier, the as-printed surface roughness can be higher than desired for some applications. Implementing appropriate post-processing techniques is essential to achieve the required surface finish.
- Material Property Consistency: Ensuring consistent material properties throughout the printed part is crucial for reliable performance. Careful control of the printing process and the quality of the metal powder are essential. Metal3DP’s rigorous quality control measures ensure the consistency of our high-quality metal powders.
- Scalability and Cost-Effectiveness: While metal 3D printing is ideal for customization and low to medium volumes, scaling up production for very high volumes can present challenges in terms of cost and production rate. Careful consideration of the overall production strategy is necessary.
By understanding these potential challenges and implementing best practices in design, material selection, printing process optimization, and post-processing, manufacturers can effectively leverage metal 3D printing to produce high-quality and reliable custom pump volutes.
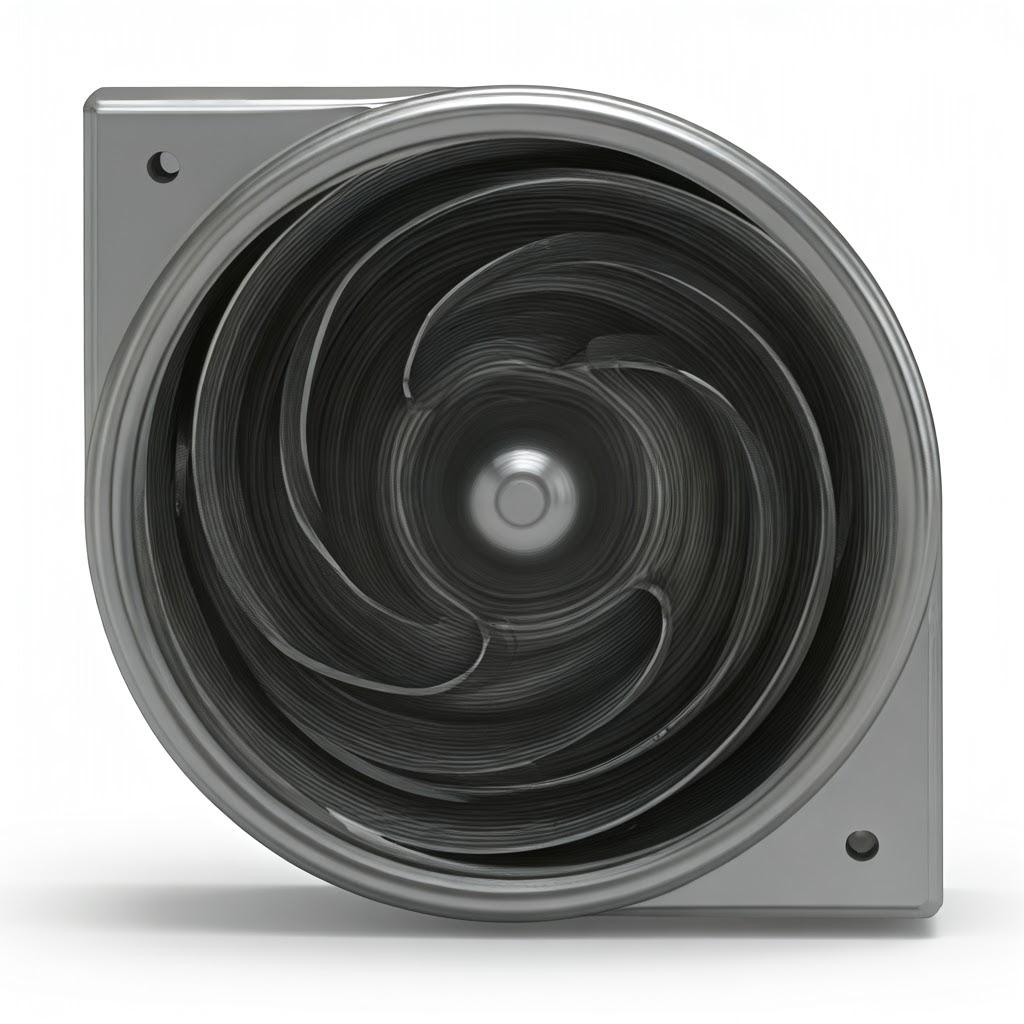
Partnering for Success: How to Select a Trusted Metal 3D Printing Service Provider
Choosing the right metal 3D printing service provider is crucial for the successful production of your custom pump volutes. A reliable partner will possess the expertise, equipment, and quality control processes necessary to deliver high-performance parts that meet your specific requirements. Here are key factors to consider when evaluating potential suppliers:
- Material Capabilities: Ensure the service provider offers the specific metal powders you require, such as IN625 and CuNi30Mn1Fe, and has experience processing these materials for demanding applications. Inquire about their material characterization and testing procedures. Metal3DP boasts a wide range of high-quality metal powders, as detailed on our website.
- Printing Technology and Equipment: Understand the types of metal 3D printing technologies they utilize (e.g., SLM, EBM) and the capabilities of their equipment in terms of build volume, accuracy, and resolution. Industry-leading print volume, accuracy, and reliability are hallmarks of Metal3DP’s printers.
- Design and Engineering Support: A strong service provider should offer design consultation and engineering support to help optimize your volute design for additive manufacturing, ensuring manufacturability and performance. Our team at Metal3DP provides comprehensive solutions spanning design optimization and application development.
- Post-Processing Services: Inquire about the in-house post-processing capabilities, including powder removal, support removal, heat treatment, surface finishing, and machining. A provider offering a comprehensive suite of services can streamline the production process.
- Quality Assurance and Certifications: Verify that the service provider has robust quality management systems in place, including material traceability, process controls, and inspection procedures. Relevant certifications (e.g., ISO 9001, AS9100 for aerospace) are indicators of their commitment to quality.
- Industry Experience and Expertise: Look for a provider with a proven track record in serving your industry (e.g., aerospace, automotive, medical). Their experience with similar applications can be invaluable. With decades of collective expertise in metal additive manufacturing, Metal3DP partners with organizations across various sectors.
- Communication and Customer Support: Effective communication and responsive customer support are essential for a smooth and successful project. Assess their responsiveness and willingness to collaborate.
- Lead Times and Production Capacity: Understand their typical lead times for similar projects and their production capacity to ensure they can meet your delivery requirements.
- Cost Structure and Transparency: Obtain a clear and detailed quotation that outlines all costs involved, including printing, materials, post-processing, and any additional services.
By carefully evaluating these factors, you can select a metal 3D printing service provider like Metal3DP that aligns with your needs and ensures the successful production of your custom pump volutes.
Understanding the Investment: Cost Factors and Lead Times for 3D Printed Pump Volutes
The cost and lead time for producing custom pump volutes using metal 3D printing are influenced by several factors. Understanding these elements will help you plan your project effectively:
Cost Factors:
- Material Costs: The type and quantity of metal powder used are significant cost drivers. High-performance alloys like IN625 are generally more expensive than standard alloys. Material waste in additive manufacturing is typically lower than in subtractive methods, which can offset some of the material cost.
- Build Time: The duration of the printing process directly impacts the cost. Longer build times, influenced by part size, complexity, and layer thickness, will increase the machine time and associated energy consumption costs.
- Post-Processing Costs: The extent and complexity of required post-processing steps (e.g., heat treatment, machining, surface finishing) will add to the overall cost.
- Design and Engineering Costs: If you require design optimization or engineering support from the service provider, these services will be factored into the cost.
- Setup and Tooling Costs: Unlike traditional manufacturing, metal 3D printing generally has minimal tooling costs, which can be a significant advantage for low to medium volume production. However, complex build setups or specialized fixtures may incur some setup costs.
- Quantity and Volume: While 3D printing is cost-effective for low to medium volumes, the unit cost may decrease with larger production runs due to economies of scale in material procurement and process optimization.
Lead Times:
- Design and Engineering Phase: The time required for design optimization and preparation for 3D printing will depend on the complexity of the volute and the need for simulations or analysis.
- Printing Time: The actual printing time is determined by the part’s volume, complexity, and the chosen printing parameters.
- Post-Processing Time: The duration of post-processing steps such as heat treatment, surface finishing, and inspection will add to the overall lead time.
- Shipping and Logistics: The time required for shipping the finished parts to your location needs to be considered.
Metal3DP is committed to providing transparent and competitive pricing along with efficient lead times. Contact us to discuss your specific requirements and receive a detailed quotation.
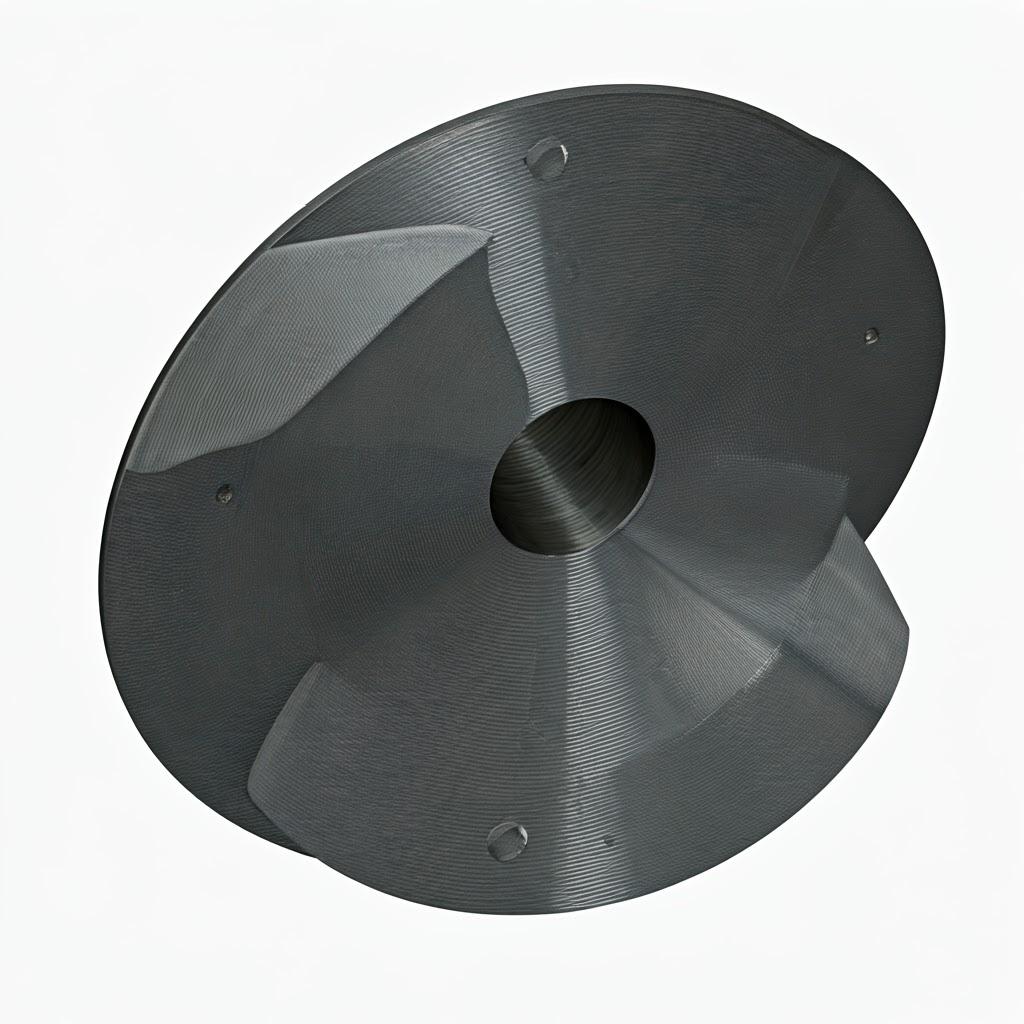
Frequently Asked Questions (FAQ) About Metal 3D Printing for Pump Volutes
Here are some frequently asked questions regarding the use of metal 3D printing for manufacturing pump volutes:
Q: Can metal 3D printed volutes achieve the same performance as traditionally manufactured ones? A: Yes, in many cases, metal 3D printed volutes can achieve comparable or even superior performance due to the design freedom offered by additive manufacturing. Optimized internal flow paths and lightweight designs can enhance efficiency and reduce energy consumption.
Q: What are the typical applications for 3D printed metal pump volutes? A: Custom metal 3D printed volutes are used in a wide range of applications across industries such as aerospace, automotive, medical, industrial manufacturing, and oil & gas, particularly where complex geometries, lightweighting, or specialized materials are required.
Q: Is metal 3D printing cost-effective for producing pump volutes? A: Metal 3D printing is particularly cost-effective for low to medium volume production of custom volutes, rapid prototyping, and complex designs where traditional tooling costs would be prohibitive. For very high volumes, traditional methods may still be more economical.
Q: What materials can be used to 3D print pump volutes? A: A variety of metal powders can be used, including stainless steels, nickel-based superalloys like IN625, copper-nickel alloys like CuNi30Mn1Fe, titanium alloys, and more, depending on the application requirements. Metal3DP offers a comprehensive portfolio of high-quality metal powders.
Q: What level of customization is possible with 3D printed pump volutes? A: Metal 3D printing offers a high degree of customization, allowing for the creation of complex internal geometries, optimized flow channels, integrated features, and designs tailored to specific performance requirements and spatial constraints.
Conclusion – The Future of Pump Volute Manufacturing with Metal Additive Technology
Metal 3D printing is revolutionizing the manufacturing of custom pump volutes, offering unparalleled design freedom, material efficiency, and the ability to create complex geometries for enhanced performance. By leveraging advanced materials like IN625 and CuNi30Mn1Fe and partnering with experienced providers like Metal3DP, engineers and procurement managers can unlock new possibilities for optimizing pump systems across a wide range of industries. From rapid prototyping and low-volume customization to the production of high-performance components for demanding applications, metal additive technology is poised to play an increasingly significant role in the future of pump manufacturing. Contact Metal3DP today to explore how our cutting-edge systems and high-quality metal powders can power your organization’s additive manufacturing goals.
Share On
MET3DP Technology Co., LTD is a leading provider of additive manufacturing solutions headquartered in Qingdao, China. Our company specializes in 3D printing equipment and high-performance metal powders for industrial applications.
Inquiry to get best price and customized Solution for your business!
Related Articles
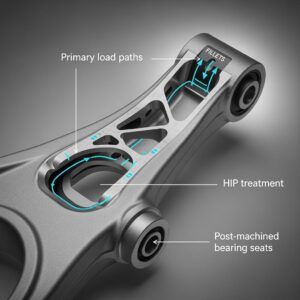
Metal 3D Printing for U.S. Automotive Lightweight Structural Brackets and Suspension Components
Read More »About Met3DP
Recent Update
Our Product
CONTACT US
Any questions? Send us message now! We’ll serve your request with a whole team after receiving your message.