introduction of Reactive Alloys
Table of Contents
Types of Reactive Alloys
Here, we present specific metal powder models of reactive alloys, detailing their compositions, properties, and characteristics.
Alloy Model | Composition | Properties | Characteristics |
---|---|---|---|
Ti-6Al-4V | Titanium, Aluminum, Vanadium | High strength-to-weight ratio, corrosion-resistant | Widely used in aerospace and biomedical implants |
NiTi (Nitinol) | Nickel, Titanium | Shape memory, superelasticity | Used in medical devices and actuators |
Al-Mg (Magnalium) | Aluminum, Magnesium | Lightweight, good mechanical strength | Ideal for automotive and aerospace applications |
Zircaloy | Zirconium, Tin | Excellent corrosion resistance, high melting point | Used in nuclear reactors |
Nb-Ti (Niobium-Titanium) | Niobium, Titanium | High superconducting properties | Common in superconducting magnets |
CoCr (Cobalt-Chromium) | Cobalt, Chromium | High wear resistance, biocompatibility | Perfect for dental and orthopedic implants |
Cu-Be (Copper-Beryllium) | Copper, Beryllium | High strength, good conductivity | Used in aerospace and electronic connectors |
Fe-Al (Iron-Aluminum) | Iron, Aluminum | High strength, oxidation resistance | Utilized in high-temperature applications |
Mg-Zn (Magnesium-Zinc) | Magnesium, Zinc | Low density, good machinability | Suited for lightweight structural components |
Ti-Nb (Titanium-Niobium) | Titanium, Niobium | Excellent biocompatibility, low modulus | Used in medical implants and aerospace components |
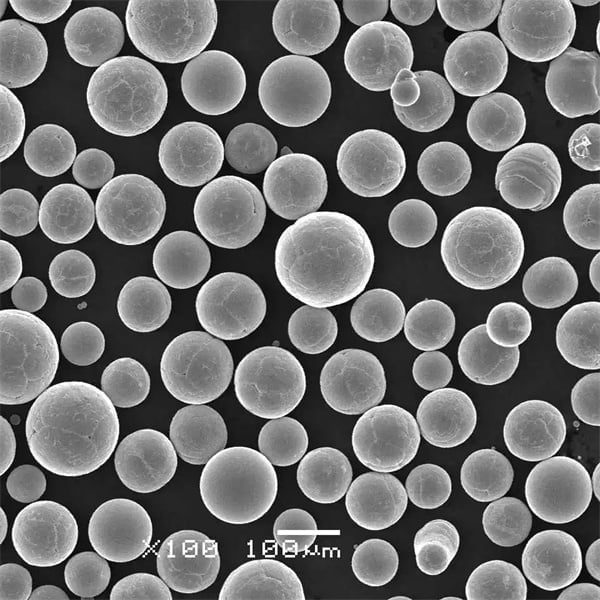
Applications of Reactive Alloys
Reactive alloys are utilized across various industries due to their unique properties. Here are some common applications:
Application | Alloy Model | Reason for Use |
---|---|---|
Aerospace Components | Ti-6Al-4V, Al-Mg | High strength-to-weight ratio, corrosion resistance |
Medical Implants | NiTi, CoCr, Ti-Nb | Biocompatibility, shape memory, durability |
Automotive Parts | Al-Mg, Cu-Be | Lightweight, strength, electrical conductivity |
Nuclear Reactors | Zircaloy | High melting point, corrosion resistance |
Superconducting Magnets | Nb-Ti | Superconducting properties |
Electronic Connectors | Cu-Be | High strength, good conductivity |
Dental Devices | CoCr, NiTi | Biocompatibility, wear resistance |
Specifications and Standards for Reactive Alloys
When selecting reactive alloys for specific applications, it’s crucial to consider their specifications and standards.
Alloy Model | Specifications | Sizes | Grades | Standards |
---|---|---|---|---|
Ti-6Al-4V | ASTM B348, AMS 4928 | Rods, bars, sheets | Grade 5 | ASTM, AMS |
NiTi (Nitinol) | ASTM F2063 | Wires, rods | N/A | ASTM |
Al-Mg (Magnalium) | ASTM B308 | Sheets, plates | 5005, 5052, 6061 | ASTM |
Zircaloy | ASTM B811, B352 | Tubes, sheets | N/A | ASTM, ASME |
Nb-Ti (Niobium-Titanium) | N/A | Wires, bars | N/A | N/A |
CoCr (Cobalt-Chromium) | ASTM F75, F1537 | Rods, bars | N/A | ASTM |
Cu-Be (Copper-Beryllium) | ASTM B196, B197 | Rods, bars, tubes | C17200, C17300 | ASTM, AMS |
Fe-Al (Iron-Aluminum) | N/A | Sheets, bars | N/A | N/A |
Mg-Zn (Magnesium-Zinc) | ASTM B107 | Sheets, plates | AZ31B, AZ61A | ASTM |
Ti-Nb (Titanium-Niobium) | N/A | Rods, bars | N/A | N/A |
Suppliers and Pricing Details
Finding reliable suppliers for reactive alloys is essential. Here are some top suppliers and their pricing details:
Supplier | Alloy Model | Price Range (per kg) | Location |
---|---|---|---|
ATI Metals | Ti-6Al-4V, CoCr | $100 – $150 | USA |
Fort Wayne Metals | NiTi, Ti-Nb | $200 – $300 | USA |
Materion Corporation | Cu-Be | $150 – $200 | USA |
Zapp Group | Nb-Ti, CoCr | $250 – $350 | Germany |
Magnesium Elektron | Al-Mg, Mg-Zn | $50 – $100 | UK |
Precision Castparts Corp | Zircaloy | $200 – $400 | USA |
VSMPO-AVISMA | Ti-6Al-4V, Ti-Nb | $150 – $250 | Russia |
Sandvik Materials Technology | NiTi, CoCr | $250 – $350 | Sweden |
Carpenter Technology | Cu-Be, Fe-Al | $150 – $250 | USA |
Allegheny Technologies | Al-Mg, Zircaloy | $100 – $200 | USA |
Advantages and Disadvantages of Reactive Alloys
Reactive alloys offer numerous benefits, but they also come with some drawbacks. Let’s compare:
Alloy Model | Advantages | Disadvantages |
---|---|---|
Ti-6Al-4V | High strength-to-weight ratio, corrosion resistance | Expensive, challenging to machine |
NiTi (Nitinol) | Shape memory, superelasticity | High cost, limited temperature range |
Al-Mg (Magnalium) | Lightweight, good mechanical properties | Lower strength compared to steel |
Zircaloy | Excellent corrosion resistance, high melting point | Limited applications, costly |
Nb-Ti (Niobium-Titanium) | Superconducting properties | Expensive, specialized applications |
CoCr (Cobalt-Chromium) | High wear resistance, biocompatibility | High cost, difficult to process |
Cu-Be (Copper-Beryllium) | High strength, good conductivity | Toxicity concerns, costly |
Fe-Al (Iron-Aluminum) | High strength, oxidation resistance | Brittleness, lower ductility |
Mg-Zn (Magnesium-Zinc) | Low density, good machinability | Lower strength, flammability concerns |
Ti-Nb (Titanium-Niobium) | Excellent biocompatibility, low modulus | High cost, limited availability |
In-Depth Comparison of Reactive Alloys
Ti-6Al-4V vs. NiTi (Nitinol)
Ti-6Al-4V is renowned for its high strength-to-weight ratio and excellent corrosion resistance, making it a top choice in aerospace and medical implants. However, it can be expensive and challenging to machine.
NiTi (Nitinol), on the other hand, is famous for its shape memory and superelasticity, which are crucial for medical devices and actuators. While it is also costly, its unique properties often justify the expense in highly specialized applications.
Comparison:
Feature | Ti-6Al-4V | NiTi (Nitinol) |
---|---|---|
Strength-to-weight ratio | High | Moderate |
Corrosion resistance | Excellent | Good |
Shape memory | No | Yes |
Biocompatibility | Excellent | Excellent |
Cost | High | High |
Machinability | Challenging | Moderate |
Temperature sensitivity | Low | High |
Al-Mg (Magnalium) vs. Mg-Zn (Magnesium-Zinc)
Al-Mg (Magnalium) is lightweight with good mechanical strength, making it suitable for automotive and aerospace applications. It offers a balanced mix of properties at a relatively low cost.
Mg-Zn (Magnesium-Zinc) alloys are prized for their low density and good machinability, ideal for lightweight structural components. However, they have lower strength and concerns about flammability.
Comparison:
Feature | Al-Mg (Magnalium) | Mg-Zn (Magnesium-Zinc) |
---|---|---|
Weight | Lightweight | Extremely lightweight |
Mechanical strength | Good | Moderate |
Corrosion resistance | Moderate | Moderate |
Machinability | Good | Excellent |
Flammability | Low | High |
Cost | Moderate | Low |
Application flexibility | High | Moderate |
Zircaloy vs. Nb-Ti (Niobium-Titanium)
Zircaloy is crucial in nuclear reactors due to its excellent corrosion resistance and high melting point. Its applications are somewhat limited but highly specialized.
Nb-Ti (Niobium-Titanium) is widely used in superconducting magnets, offering high superconducting properties at a premium price.
Comparison:
Feature | Zircaloy | Nb-Ti (Niobium-Titanium) |
---|---|---|
Corrosion resistance | Excellent | Good |
Melting point | High | High |
Superconducting properties | None | Excellent |
Cost | High | Very high |
Application | Nuclear reactors | Superconducting magnets |
Availability | Moderate | Limited |
CoCr (Cobalt-Chromium) vs. Cu-Be (Copper-Beryllium)
CoCr (Cobalt-Chromium) alloys are known for their high wear resistance and biocompatibility, making them perfect for dental and orthopedic implants. However, they are difficult to process and expensive.
Cu-Be (Copper-Beryllium) offers high strength and good conductivity, suitable for aerospace and electronic connectors. Concerns about toxicity and cost are notable drawbacks.
Comparison:
Feature | CoCr (Cobalt-Chromium) | Cu-Be (Copper-Beryllium) |
---|---|---|
Wear resistance | High | Moderate |
Biocompatibility | Excellent | Good |
Electrical conductivity | Low | High |
Strength | High | High |
Cost | High | High |
Processing difficulty | High | Moderate |
Toxicity concerns | None | Present |
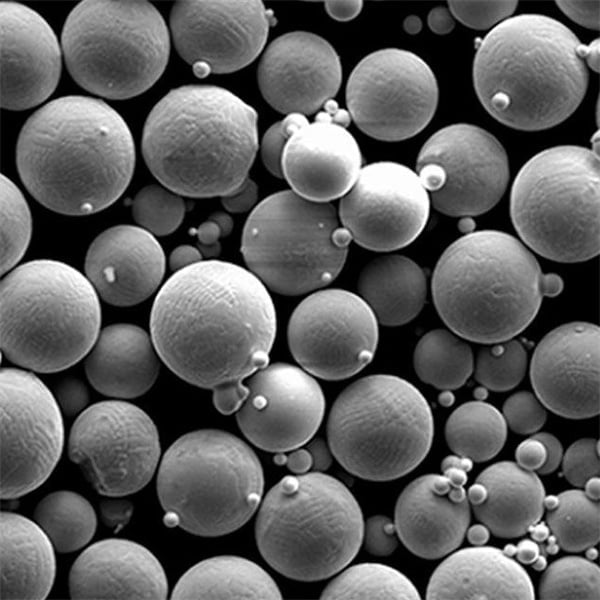
FAQ
Question | Answer |
---|---|
What are the key benefits of using reactive alloys in aerospace applications? | They offer a high strength-to-weight ratio and excellent corrosion resistance, crucial for the performance and longevity of aerospace components. |
How do reactive alloys improve medical device performance? | Their biocompatibility and unique properties like shape memory in NiTi make them ideal for implants and other medical devices. |
What considerations should be taken when machining reactive alloys? | Due to their reactivity and strength, specialized machining techniques and equipment are often required to avoid damage and ensure precision. |
Are there environmental concerns with the use of reactive alloys? | While some reactive alloys like Cu-Be have toxicity concerns, many are environmentally friendly and recyclable. Proper handling and disposal procedures are necessary to mitigate any environmental impact. |
How does the cost of reactive alloys compare to traditional metals? | Reactive alloys are generally more expensive due to their advanced properties and the complexity of their production processes. However, their performance benefits often justify the higher cost in critical applications. |
Share On
MET3DP Technology Co., LTD is a leading provider of additive manufacturing solutions headquartered in Qingdao, China. Our company specializes in 3D printing equipment and high-performance metal powders for industrial applications.
Inquiry to get best price and customized Solution for your business!
Related Articles
About Met3DP
Recent Update
Our Product
CONTACT US
Any questions? Send us message now! We’ll serve your request with a whole team after receiving your message.
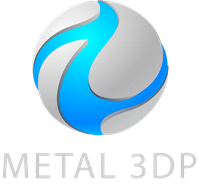
Metal Powders for 3D Printing and Additive Manufacturing