introduction to Refractory Alloys
Table of Contents
Refractory alloys are fascinating materials that play a critical role in numerous high-temperature applications. They are designed to withstand extreme environments, such as those found in aerospace, nuclear reactors, and advanced manufacturing processes. This comprehensive guide will delve into the world of refractory alloys, discussing their types, properties, applications, and much more.
Overview of Refractory Alloys
Refractory alloys are metals that have exceptionally high melting points and are resistant to wear, corrosion, and deformation at high temperatures. These characteristics make them invaluable in industrial and technological applications where materials are subjected to severe conditions.
Key Characteristics of Refractory Alloys
- High Melting Points: Typically above 2000°C (3632°F)
- Strength at Elevated Temperatures: Maintain mechanical integrity at high temperatures
- Wear Resistance: High resistance to abrasion and wear
- Corrosion Resistance: Can withstand harsh chemical environments
- Thermal Stability: Minimal expansion or contraction with temperature changes
Common Refractory Alloys
Here’s a table showcasing some specific metal powder models of refractory alloys, along with their key compositions and properties:
Alloy | Composition | Melting Point | Density | Properties |
---|---|---|---|---|
Tungsten (W) | Pure Tungsten | 3422°C | 19.25 g/cm³ | Highest melting point, high density |
Molybdenum (Mo) | Pure Molybdenum | 2623°C | 10.28 g/cm³ | High thermal conductivity, excellent strength |
Tantalum (Ta) | Pure Tantalum | 3017°C | 16.65 g/cm³ | High corrosion resistance, ductility |
Niobium (Nb) | Pure Niobium | 2477°C | 8.57 g/cm³ | Good superconducting properties, malleability |
Rhenium (Re) | Pure Rhenium | 3186°C | 21.02 g/cm³ | High melting point, good creep resistance |
Hafnium (Hf) | Pure Hafnium | 2233°C | 13.31 g/cm³ | Excellent corrosion resistance, high density |
Zirconium (Zr) | Pure Zirconium | 1855°C | 6.52 g/cm³ | Low neutron-capture cross-section, corrosion resistance |
Titanium Zirconium Molybdenum (TZM) | Ti-Zr-Mo alloy | ~2600°C | 10.2 g/cm³ | Enhanced strength, high thermal conductivity |
Tungsten Heavy Alloy (WHA) | W-Ni-Fe/Cu | 2700°C | 17-18 g/cm³ | High density, good machinability |
Chromium (Cr) | Pure Chromium | 1907°C | 7.19 g/cm³ | High hardness, corrosion resistance |
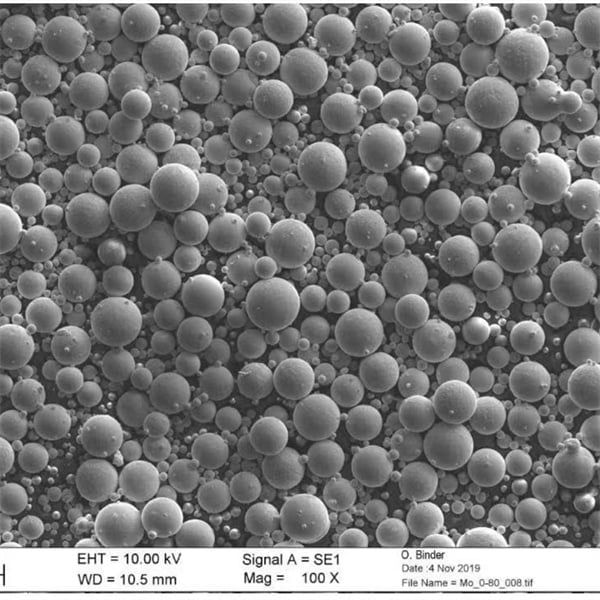
Applications of Refractory Alloys
Refractory alloys are utilized in a variety of industries due to their exceptional properties. Here’s a table detailing the applications of some common refractory alloys:
Alloy | Applications |
---|---|
Tungsten (W) | Light bulb filaments, X-ray tubes, rocket engine nozzles, radiation shielding |
Molybdenum (Mo) | Furnace components, electrodes, missile and aircraft parts |
Tantalum (Ta) | Capacitors, medical implants, chemical processing equipment |
Niobium (Nb) | Superconducting magnets, aerospace components, chemical reactors |
Rhenium (Re) | High-temperature thermocouples, jet engine components, electrical contacts |
Hafnium (Hf) | Control rods in nuclear reactors, rocket nozzles, plasma cutting tips |
Zirconium (Zr) | Nuclear reactors, chemical processing equipment, orthopedic implants |
TZM | Aerospace components, hot gas path components in turbines |
WHA | Counterweights, radiation shielding, kinetic energy penetrators |
Chromium (Cr) | Coatings for protection against oxidation, cutting tools, stainless steel production |
Specifications, Sizes, Grades, and Standards
Refractory alloys come in various specifications, sizes, and grades to meet diverse application requirements. Here’s a table illustrating some common standards and specifications:
Alloy | Standard/Specification | Sizes | Grades |
---|---|---|---|
Tungsten (W) | ASTM B760, MIL-T-21014 | Rods, sheets, wires | Pure, alloyed |
Molybdenum (Mo) | ASTM B386, ASTM B387 | Plates, rods, foils | Pure, TZM |
Tantalum (Ta) | ASTM B708, ASTM B365 | Sheets, rods, wires | RO5200, RO5400 |
Niobium (Nb) | ASTM B393, ASTM B394 | Bars, rods, sheets | R04200, R04210 |
Rhenium (Re) | ASTM B662 | Rods, wires | Pure |
Hafnium (Hf) | ASTM B776 | Rods, sheets, wires | Hf 99.9% |
Zirconium (Zr) | ASTM B551, ASTM B550 | Sheets, plates, bars | Zr702, Zr705 |
TZM | ASTM B386 | Sheets, rods, plates | TZM |
WHA | ASTM B777, MIL-T-21014 | Bars, plates, rods | Various compositions |
Chromium (Cr) | ASTM A739 | Plates, sheets, bars | Cr 99.5%, Cr 99.9% |
Advantages and Disadvantages of Refractory Alloys
When choosing materials for high-temperature applications, it’s crucial to understand the benefits and limitations of each option. Here’s a comparative table of the pros and cons of some popular refractory alloys:
Alloy | Advantages | Disadvantages |
---|---|---|
Tungsten (W) | Extremely high melting point, high density, good electrical conductivity | Brittle, difficult to work with, high cost |
Molybdenum (Mo) | High strength at elevated temperatures, good thermal conductivity | Prone to oxidation, requires protective atmosphere |
Tantalum (Ta) | Excellent corrosion resistance, ductility, biocompatibility | High cost, limited availability |
Niobium (Nb) | Good superconducting properties, corrosion resistance | Low hardness, oxidation at high temperatures |
Rhenium (Re) | High melting point, excellent creep resistance | Extremely expensive, limited supply |
Hafnium (Hf) | High corrosion resistance, good mechanical properties | Expensive, difficult to process |
Zirconium (Zr) | Low neutron-capture cross-section, good corrosion resistance | Prone to hydrogen embrittlement, high cost |
TZM | Enhanced strength, good thermal conductivity | Requires protective coatings, expensive |
WHA | High density, good machinability | Expensive, limited applications due to toxicity concerns |
Chromium (Cr) | High hardness, corrosion resistance | Brittle, difficult to machine |
Suppliers and Pricing Details
Finding reliable suppliers for refractory alloys is essential for ensuring quality and consistency. Here’s a table with some well-known suppliers and general pricing details:
Supplier | Alloys Offered | Pricing Range | Notes |
---|---|---|---|
H.C. Starck | Tungsten, Molybdenum, Tantalum, Niobium | $$$ – $$$$ | High-quality powders and alloys |
Plansee Group | Tungsten, Molybdenum, TZM, WHA | $$$ – $$$$ | Extensive product range |
ATI Metals | Zirconium, Hafnium, Niobium | $$$$ | Premium grades for specialized applications |
Special Metals Corporation | Chromium, Rhenium, Niobium, Tantalum | $$$ – $$$$ | Wide selection, custom alloys available |
Midwest Tungsten Service | Tungsten, Molybdenum, TZM | $$ – $$$ | Competitive pricing, smaller quantities |
Metalysis | Tungsten, Tantalum, Hafnium | $$$$ | Innovative production methods |
Advanced Refractory Metals | Tungsten, Molybdenum, Tantalum, Niobium | $$ – $$$ | Good customer service, bulk discounts |
Rhenium Alloys, Inc. | Rhenium, Tungsten-Rhenium alloys | $$$$ |
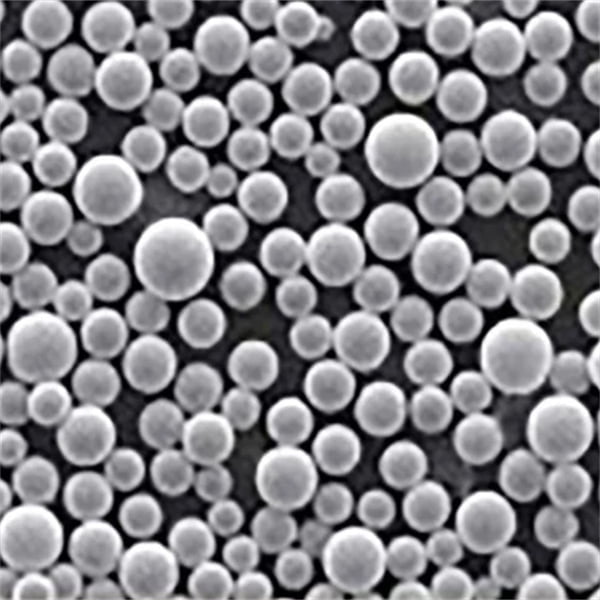
FAQs
Q: What are refractory alloys, and why are they important?
A: Refractory alloys are metals with exceptionally high melting points and resistance to extreme temperatures, wear, and corrosion. They play a crucial role in industries like aerospace, nuclear energy, and high-temperature manufacturing, where conventional materials would fail.
Q: How do I choose the right refractory alloy for my application?
A: Selecting the appropriate refractory alloy depends on several factors, including the operating environment, required properties (such as strength, corrosion resistance, and conductivity), and budget constraints. Consulting with materials engineers or suppliers can help in making an informed decision.
Q: Are refractory alloys expensive?
A: Yes, refractory alloys tend to be more costly compared to conventional metals due to their specialized properties and manufacturing processes. However, their performance and durability often justify the investment, especially in critical applications where reliability is paramount.
Q: Can refractory alloys be recycled?
A: Yes, many refractory alloys, such as tungsten and molybdenum, are recyclable. Recycling helps to conserve resources, reduce costs, and minimize environmental impact. However, the recycling process can be complex due to the alloys’ high melting points and chemical stability.
Q: What are some emerging trends in refractory alloys research and development?
A: Researchers are constantly exploring new alloy compositions, processing techniques, and applications for refractory alloys. Some trends include the development of alloys with improved mechanical properties, enhanced corrosion resistance, and suitability for additive manufacturing processes like 3D printing.
Q: Are there any environmental considerations associated with refractory alloys?
A: While refractory alloys themselves are not typically considered hazardous to the environment, the extraction and processing of raw materials, as well as the disposal of waste products, can have environmental impacts. Efforts to minimize these impacts include sustainable sourcing, recycling initiatives, and cleaner production methods.
Q: Can refractory alloys be used in medical implants?
A: Yes, certain refractory alloys, such as tantalum and niobium, are biocompatible and corrosion-resistant, making them suitable for medical implants like orthopedic implants and pacemaker components. These alloys offer excellent strength and durability, enhancing the longevity and performance of medical devices.
Q: How do I ensure the quality of refractory alloys purchased from suppliers?
A: When sourcing refractory alloys, it’s essential to choose reputable suppliers with a track record of providing high-quality materials. Certifications, such as ISO standards, and customer reviews can help gauge a supplier’s reliability. Additionally, requesting material testing certificates and conducting quality inspections upon receipt can verify the alloy’s conformance to specifications.
Q: What are some challenges associated with working with refractory alloys?
A: Refractory alloys pose challenges in terms of machining, fabrication, and handling due to their high hardness, brittleness, and tendency to react with cutting tools. Specialized equipment and processes may be required to work with these materials effectively. Additionally, their high cost and limited availability can present procurement challenges for certain applications.
Q: Are there any safety considerations when working with refractory alloys?
A: Yes, handling refractory alloys, particularly in powder or dust form, requires precautions to prevent exposure and inhalation, which can pose health risks. Proper ventilation, personal protective equipment (PPE), and safe handling procedures are essential to minimize potential hazards in the workplace.
Share On
MET3DP Technology Co., LTD is a leading provider of additive manufacturing solutions headquartered in Qingdao, China. Our company specializes in 3D printing equipment and high-performance metal powders for industrial applications.
Inquiry to get best price and customized Solution for your business!
Related Articles
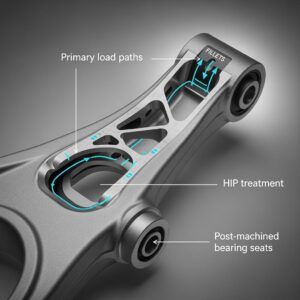
Metal 3D Printing for U.S. Automotive Lightweight Structural Brackets and Suspension Components
Read More »About Met3DP
Recent Update
Our Product
CONTACT US
Any questions? Send us message now! We’ll serve your request with a whole team after receiving your message.