Refractory Metal Powders
Table of Contents
Refractory metal powders are a class of materials known for their extraordinary resistance to heat and wear, making them indispensable in various high-performance applications. But what makes these powders so special? Let’s dive into the fascinating world of refractory metal powders, explore their unique properties, and see how they compare to other materials.
Overview of Refractory Metal Powders
Refractory metals include tungsten, molybdenum, tantalum, niobium, and rhenium. These metals are characterized by their high melting points, exceptional hardness, and resistance to corrosion and wear. They are vital in industries where materials are exposed to extreme conditions.
Key Properties of Refractory Metal Powders
Metal | Melting Point (°C) | Density (g/cm³) | Hardness (Vickers) | Thermal Conductivity (W/m·K) | Electrical Conductivity (MS/m) |
---|---|---|---|---|---|
Tungsten | 3422 | 19.3 | 3430 | 173 | 18.52 |
Molybdenum | 2623 | 10.2 | 1530 | 138 | 18.7 |
Tantalum | 3017 | 16.6 | 873 | 57 | 7.89 |
Niobium | 2477 | 8.57 | 740 | 53 | 6.7 |
Rhenium | 3186 | 21.02 | 2450 | 48 | 5.1 |
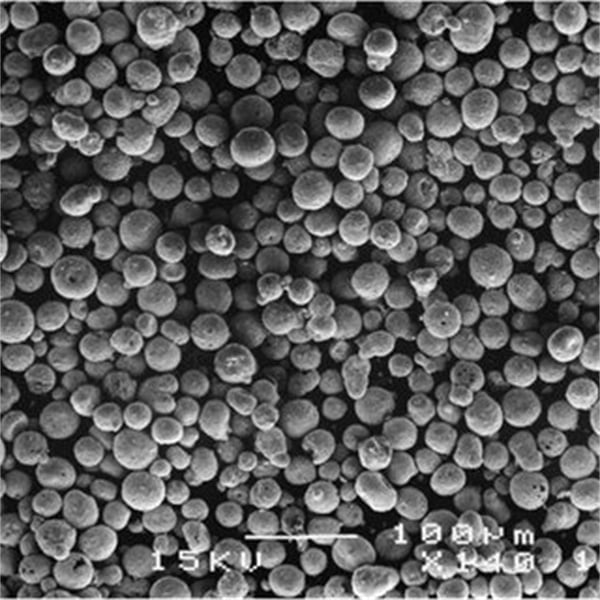
Applications of Refractory Metal Powders
Refractory metal powders find applications in various industries due to their unique properties. Here’s a look at where they are commonly used:
Application | Description | Key Metal Powders Used |
---|---|---|
Aerospace | High-temperature structural components, rocket nozzles | Tungsten, Rhenium, Tantalum |
Electronics | High-power electrical contacts, heat sinks | Tungsten, Molybdenum, Niobium |
Nuclear | Control rods, shielding materials | Tungsten, Tantalum, Niobium |
Medical | Imaging devices, surgical instruments | Tantalum, Niobium |
Chemical Processing | Catalysts, reactors, and heat exchangers | Tungsten, Molybdenum, Rhenium |
Defense | Armor-piercing projectiles, advanced weapon systems | Tungsten, Rhenium, Tantalum |
Specifications, Sizes, Grades, and Standards
Refractory metal powders come in various grades and sizes, tailored to specific applications and industry standards.
Metal | Grade | Particle Size (µm) | Purity (%) | Standards |
---|---|---|---|---|
Tungsten | W-1, W-2 | 1-10 | 99.95 | ASTM B777, MIL-T-21014 |
Molybdenum | Mo-1, TZM | 5-15 | 99.95 | ASTM B386, MIL-M-24149 |
Tantalum | Ta-1, Ta-2 | 2-20 | 99.9 | ASTM B708, MIL-T-9457C |
Niobium | Nb-1, C-103 | 10-50 | 99.9 | ASTM B391, MIL-N-21793 |
Rhenium | Re-1, Re-2 | 1-10 | 99.99 | ASTM B760, MIL-R-3065 |
Suppliers and Pricing Details
Finding the right supplier is crucial for obtaining high-quality refractory metal powders. Here’s a list of some notable suppliers and their pricing:
Supplier | Metal Powders Available | Price Range ($/kg) |
---|---|---|
H.C. Starck | Tungsten, Molybdenum, Tantalum, Niobium, Rhenium | 500-1500 |
Global Tungsten & Powders | Tungsten, Molybdenum | 400-1200 |
Rhenium Alloys | Rhenium | 1000-3000 |
Admat Inc. | Tantalum, Niobium | 600-2000 |
ACI Alloys | Tungsten, Tantalum, Niobium | 700-2500 |
Comparing Refractory Metal Powders
When choosing a refractory metal powder for a specific application, it’s essential to consider their pros and cons.
Metal | Advantages | Disadvantages |
---|---|---|
Tungsten | Extremely high melting point, high density, strong | Very heavy, difficult to machine |
Molybdenum | High thermal conductivity, good strength | Can be brittle at low temperatures |
Tantalum | Excellent corrosion resistance, biocompatible | Expensive, can be difficult to work with |
Niobium | Good ductility, excellent superconducting properties | Lower melting point compared to other refractory metals |
Rhenium | High melting point, excellent creep resistance | Very expensive, limited availability |
Detailed Look at Specific Refractory Metal Powders
Let’s delve deeper into some specific models of refractory metal powders and their unique characteristics.
1. Tungsten Powder (W-1)
Tungsten powder, particularly the W-1 grade, is renowned for its highest melting point of all metals and its ability to withstand extreme temperatures. This makes it indispensable in aerospace and defense applications.
Characteristics:
- Density: 19.3 g/cm³
- Melting Point: 3422°C
- Applications: Rocket nozzles, high-temperature furnace parts, armor-piercing projectiles
Advantages:
- Exceptional strength and durability at high temperatures
- High thermal and electrical conductivity
Disadvantages:
- Heavy weight
- Difficult to machine and form
2. Molybdenum Powder (TZM)
TZM (Titanium-Zirconium-Molybdenum) alloy powder is a high-strength material with superior thermal conductivity and corrosion resistance, making it ideal for use in the aerospace and nuclear industries.
Characteristics:
- Density: 10.2 g/cm³
- Melting Point: 2623°C
- Applications: Heat shields, electrodes, nuclear reactors
Advantages:
- High strength and toughness
- Good corrosion resistance
Disadvantages:
- Brittle at low temperatures
- Requires special handling to prevent oxidation
3. Tantalum Powder (Ta-2)
Tantalum powder, especially the Ta-2 grade, is known for its excellent corrosion resistance and biocompatibility, which makes it suitable for medical implants and electronics.
Characteristics:
- Density: 16.6 g/cm³
- Melting Point: 3017°C
- Applications: Surgical instruments, capacitors, chemical processing equipment
Advantages:
- Outstanding corrosion resistance
- Excellent biocompatibility
Disadvantages:
- High cost
- Difficult to machine and process
4. Niobium Powder (C-103)
Niobium powder, particularly the C-103 alloy, is valued for its good ductility and superconducting properties, making it a choice material for aerospace components and superconducting magnets.
Characteristics:
- Density: 8.57 g/cm³
- Melting Point: 2477°C
- Applications: Rocket nozzles, superconducting magnets, medical imaging
Advantages:
- Excellent ductility
- Good superconducting properties
Disadvantages:
- Lower melting point compared to other refractory metals
- Can oxidize at high temperatures
5. Rhenium Powder (Re-1)
Rhenium powder, especially the Re-1 grade, is known for its high melting point and excellent creep resistance, making it suitable for high-temperature applications like jet engines and gas turbines.
Characteristics:
- Density: 21.02 g/cm³
- Melting Point: 3186°C
- Applications: Jet engines, gas turbines, thermocouples
Advantages:
- High melting point
- Excellent creep resistance
Disadvantages:
- Very expensive
- Limited availability
6. Tungsten Heavy Alloy (W-Ni-Fe)
Tungsten heavy alloys, such as the W-Ni-Fe alloy, are known for their high density and excellent radiation shielding capabilities. They are commonly used in medical and defense applications.
Characteristics:
- Density: 17-19 g/cm³
- Melting Point: ~3422°C (composite)
- Applications: Radiation shielding, counterweights, projectiles
Advantages:
- High density
- Good machinability
Disadvantages:
- Expensive
- Heavy weight
7. Lanthanated Tungsten (WL-15)
Lanthanated tungsten powder, particularly WL-15, is an alloy containing 1.5% lanthanum oxide, which enhances its durability and performance in welding applications.
Characteristics:
- Density: 18.4 g/cm³
- Melting Point: 3422°C
- Applications: TIG welding electrodes, aerospace components
Advantages:
- Enhanced durability
- Improved arc stability in welding
Disadvantages:
- More expensive than pure tungsten
- Requires specialized handling
8. Molybdenum Disilicide (MoSi2)
Molybdenum disilicide powder is a compound used primarily for its high-temperature oxidation resistance, making it ideal for heating elements and coatings.
Characteristics:
- Density: 6.31 g/cm³
- Melting Point: 2020°C
- Applications: Heating elements, protective coatings, structural ceramics
Advantages:
- Excellent oxidation resistance at high temperatures
- High melting point
Disadvantages:
- Brittle at room temperature
- Requires careful handling
9. Tantalum Carbide (TaC)
Tantalum carbide powder is known for its extreme hardness and high melting point, making it a critical material for cutting tools and wear-resistant coatings.
Characteristics:
- Density: 14.5 g/cm³
- Melting Point: 3880°C
- Applications: Cutting tools, wear-resistant coatings, aerospace components
Advantages:
- Extremely hard
- High melting point
Disadvantages:
- Difficult to process
- Expensive
10. Niobium Carbide (NbC)
Niobium carbide powder is used for its hardness and high melting point, which makes it suitable for cutting tools and wear-resistant applications.
Characteristics:
- Density: 7.82 g/cm³
- Melting Point: 3490°C
- Applications: Cutting tools, wear-resistant coatings, superalloys
Advantages:
- High hardness
- Good wear resistance
Disadvantages:
- Can be brittle
- Requires specialized processing
Advantages of Refractory Metal Powders
Refractory metal powders offer numerous advantages, making them essential in various high-performance applications:
Heat Resistance
These metals have some of the highest melting points among all elements, making them ideal for high-temperature applications.
Strength and Durability
Refractory metals maintain their strength at high temperatures, ensuring durability in extreme environments.
Corrosion Resistance
Many refractory metals, such as tantalum and niobium, exhibit excellent resistance to corrosion, extending the lifespan of components.
Unique Properties
Some refractory metals, like niobium and tantalum, have unique properties like superconductivity and biocompatibility, making them suitable for specialized applications.
Disadvantages of Refractory Metal Powders
Despite their many advantages, refractory metal powders also have some limitations:
Cost
Refractory metals are generally more expensive than other metals, which can be a significant drawback for some applications.
Machinability
Many refractory metals are difficult to machine and require specialized equipment and techniques.
Density
Some refractory metals, such as tungsten, are very dense, which can be a disadvantage in applications where weight is a critical factor.
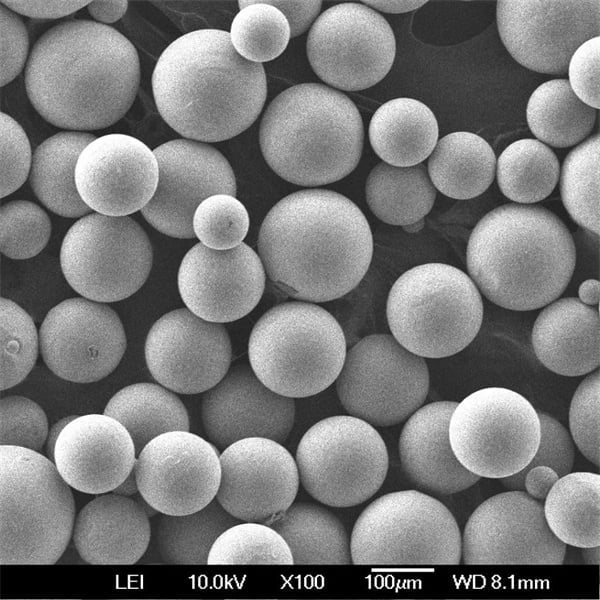
Comparison of Refractory Metal Powders Versus Other Materials
When comparing refractory metal powders to other materials, it’s essential to consider their unique properties and how they stack up against alternatives:
Property | Refractory Metals | Alternative Materials |
---|---|---|
Melting Point | Very high | Lower (e.g., steels, aluminum) |
Density | High (e.g., tungsten) | Lower (e.g., titanium, aluminum) |
Strength | High at elevated temperatures | Variable, often lower at high temperatures |
Corrosion Resistance | Excellent (e.g., tantalum, niobium) | Variable, often lower |
Cost | High | Generally lower |
Machinability | Difficult | Generally easier |
FAQs
What are refractory metal powders?
Refractory metal powders are fine particles of metals with extremely high melting points, such as tungsten, molybdenum, tantalum, niobium, and rhenium.
Why are refractory metal powders important?
These powders are crucial for applications requiring materials that can withstand extreme temperatures, wear, and corrosion, such as in aerospace, electronics, and medical industries.
How are refractory metal powders produced?
Refractory metal powders are typically produced through methods like chemical vapor deposition, hydrogen reduction, and mechanical alloying.
What are the common applications of refractory metal powders?
Common applications include aerospace components, electrical contacts, medical implants, and high-temperature furnace parts.
How do I choose the right refractory metal powder for my application?
Consider the specific requirements of your application, such as temperature resistance, strength, corrosion resistance, and cost, to select the appropriate refractory metal powder.
Where can I buy refractory metal powders?
You can purchase refractory metal powders from specialized suppliers such as H.C. Starck, Global Tungsten & Powders, Rhenium Alloys, Admat Inc., and ACI Alloys.
What are the main advantages of using refractory metal powders?
The main advantages include high melting points, excellent strength and durability, and resistance to corrosion and wear.
Are there any disadvantages to using refractory metal powders?
Yes, disadvantages include high cost, difficulty in machining, and high density, which can be a drawback in some applications.
Can refractory metal powders be recycled?
Yes, refractory metal powders can often be recycled, which helps to reduce costs and environmental impact.
How do refractory metal powders compare to other materials?
Refractory metal powders generally offer higher melting points, strength, and corrosion resistance compared to many other materials, but they are also more expensive and harder to machine.
Conclusion
Refractory metal powders are an incredible class of materials that offer unmatched performance in extreme conditions. Whether it’s the heat resistance of tungsten, the strength of molybdenum, or the corrosion resistance of tantalum, these powders are essential in pushing the boundaries of technology and innovation. By understanding their unique properties, applications, and limitations, you can make informed decisions for your high-performance needs.
Share On
MET3DP Technology Co., LTD is a leading provider of additive manufacturing solutions headquartered in Qingdao, China. Our company specializes in 3D printing equipment and high-performance metal powders for industrial applications.
Inquiry to get best price and customized Solution for your business!
Related Articles
About Met3DP
Recent Update
Our Product
CONTACT US
Any questions? Send us message now! We’ll serve your request with a whole team after receiving your message.
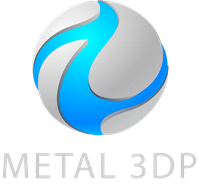
Metal Powders for 3D Printing and Additive Manufacturing