the Power of REP Powders
Table of Contents
Introduction
Have you ever dreamt of building or repairing metal objects with a simple, efficient method? Well, REP powders, also known as Rapid Engineered Powder, might just be the answer you’ve been searching for. These revolutionary metal powders are transforming the way we approach metal fabrication, offering a faster, more precise, and often more cost-effective alternative to traditional techniques like welding and casting. But what exactly are REP powders, and how do they work? This in-depth guide will delve into the world of REP powders, exploring their characteristics, advantages, limitations, and various applications. We’ll also showcase a selection of top-notch REP powder models currently available on the market, equipping you with the knowledge to make informed decisions for your next project.
Characteristics of REP Powders
Feature | Description |
---|---|
Material | REP powders consist of finely-ground metal particles produced through various techniques like atomization or gas atomization. |
Particle Size | The size of the particles plays a crucial role in the powder’s properties. REP powders typically range from 10 to 150 micrometers, offering a good balance between flowability and printability. |
Sphericity | Ideal REP powder particles are nearly spherical, ensuring smooth flow and consistent printing behavior. |
Density | The density of REP powders closely resembles the density of their bulk metal counterparts. |
Chemical Composition | REP powders can be composed of various metals, including stainless steel, titanium, aluminum, and even exotic alloys, catering to diverse project needs. |
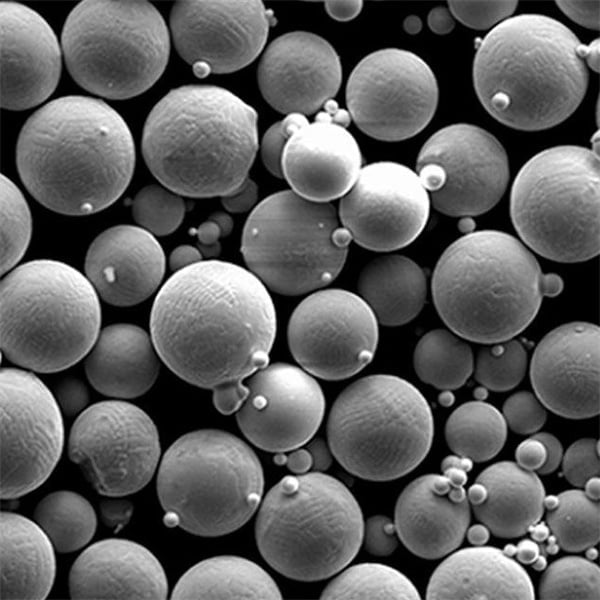
Advantages of REP Powders
Feature | Advantage | Description |
---|---|---|
Tailored Material Properties | Precise control over microstructure | REP powders allow for manipulation of particle size, shape, and distribution, leading to: * Enhanced mechanical properties: REP powders can be engineered to achieve superior strength, ductility, and fatigue resistance compared to conventional powders. This is due to the ability to control grain size and minimize defects within the final product. * Lightweighting: By optimizing pore characteristics, REP powders can be used to create components with a high strength-to-weight ratio, ideal for applications in aerospace and transportation. * Functionally graded materials: REP technology enables the creation of powders with a gradient in composition or microstructure. This allows for components with tailored properties in different regions, improving performance and efficiency. |
Improved Formability | Enhanced flow and packing characteristics | REP powders offer several advantages in terms of formability: * Near-spherical morphology: The spherical shape of REP powders promotes better flowability, reducing issues like segregation and hopper jamming during additive manufacturing processes. * Controlled porosity: REP allows for the introduction of controlled porosity within the powder particles. This can be beneficial for applications like filtration, catalysis, and drug delivery. * Reduced surface oxides: The rapid solidification process inherent to REP minimizes surface oxidation, improving powder wetting and leading to denser final products. |
Scalability and Cost-Effectiveness | Potential for high-volume production | While REP technology is still under development, it offers promising advantages for cost-effective, high-volume powder production: * Continuous process: Unlike traditional atomization methods, REP is a continuous process, enabling consistent production and potentially reducing manufacturing costs. * Reduced feedstock waste: REP utilizes molten metal feedstock efficiently, minimizing waste compared to processes that require powder crushing or milling. * Potential for automation: The continuous nature of REP lends itself well to automation, further reducing production costs and improving process control. |
Environmental Benefits | Minimized energy consumption and waste generation | REP offers several environmental advantages: * Lower energy consumption: Compared to traditional atomization methods, REP requires less energy due to the efficient use of feedstock and reduced need for post-processing. * Reduced water usage: Some atomization techniques rely heavily on water for cooling. REP utilizes an inert gas atmosphere, eliminating the need for large quantities of water. * Minimal airborne emissions: The enclosed nature of the REP process minimizes airborne dust and metal particulates, contributing to a cleaner working environment. |
Disadvantages of REP Powders
While revolutionary, REP powders also come with certain limitations:
Feature | Disadvantage | Description |
---|---|---|
Technological Maturity | Relatively new technology | REP technology is still under development compared to well-established powder production methods. This translates to: * Limited commercial availability: Currently, REP powders are not widely commercially available, restricting their use in large-scale applications. * Evolving process parameters: As research on REP continues, optimal process parameters for different materials are still being established. This can lead to challenges in achieving consistent powder properties. * Limited experience with long-term performance: The long-term performance of materials produced using REP powders is not yet fully understood. Extensive testing is needed to ensure their suitability for demanding applications. |
Process Complexity | High initial investment and technical expertise required | The REP process involves sophisticated equipment and precise control of various parameters. This translates to: * High capital costs: Setting up an REP system requires a significant initial investment in specialized equipment. This can be a barrier for smaller manufacturers or research institutions. * Need for skilled personnel: Operating and maintaining an REP system requires personnel with a strong understanding of the technology and its intricacies. This can be challenging to find, especially in the early stages of technology adoption. * Limited process flexibility: While REP offers some degree of control over powder properties, it may not be as flexible as other methods for producing highly customized powders with very specific characteristics. |
Safety Considerations | Potential for handling hazards and environmental concerns | The REP process involves handling molten metal and inert gases, requiring careful safety protocols: * High temperatures: The process operates at high temperatures, posing a risk of burns or fire if not managed properly. * Inert gas handling: Safe handling and storage of inert gases like argon are crucial to avoid asphyxiation hazards. * Potential for metal dust emissions: Although minimal compared to traditional atomization, some metal dust may be generated during the REP process, requiring proper ventilation and dust collection systems. |
Economic Uncertainties | Unproven cost-effectiveness for all applications | While REP holds promise for cost-effective powder production, there are some uncertainties: * Energy consumption: While potentially lower than some atomization methods, the true energy footprint of REP needs to be thoroughly evaluated across different scales of production. * Maintenance costs: The complexity of REP equipment raises questions about long-term maintenance costs, which could impact overall production economics. * Hidden costs: The initial investment and potential need for specialized personnel may add hidden costs that need to be factored into the overall economic viability of REP for specific applications. |
Applications of REP Powders
The versatility of REP powders allows them to be used in a wide range of industries:
Field | Application | Description |
---|---|---|
Additive Manufacturing (AM) | Production of high-performance components | REP powders hold significant promise for advancing the field of AM due to their: * Tailored properties: The ability to engineer REP powders with specific microstructures allows for the creation of AM parts with superior strength, ductility, and weight characteristics. This is ideal for demanding applications in aerospace, automotive, and medical industries. * Improved printability: The near-spherical morphology and controlled flowability of REP powders enhance printability, leading to smoother surface finishes, reduced support structures, and potentially faster printing speeds. * Functionally graded materials: REP technology enables the production of powders with a gradient in composition or porosity. This allows for AM of components with tailored properties in different regions, optimizing performance for specific loading conditions. |
Metal Injection Molding (MIM) | Creation of complex near-net-shape parts | REP powders offer advantages for MIM due to: * Controlled porosity: The ability to introduce controlled porosity within REP powders allows for the creation of MIM parts with specific permeability characteristics, beneficial for applications in filtration, catalysis, and drug delivery. * Reduced binder content: The good flowability of REP powders can potentially allow for the use of lower binder content in the MIM feedstock, leading to parts with improved mechanical properties after sintering. * Finer features: The potentially finer and more uniform particle size distribution of REP powders can enable the creation of MIM parts with finer features and tighter tolerances. |
Biomedical Engineering | Development of implants and prosthetics | REP powders have the potential to revolutionize biomedical engineering through: * Biocompatible materials: REP technology can be used to produce powders from biocompatible materials like titanium and tantalum, suitable for the creation of implants and prosthetics. * Tailored surface properties: The ability to control surface properties of REP powders allows for the creation of implants with improved biocompatibility and osseointegration (bone ingrowth). * Porous structures for tissue engineering: Controlled porosity within REP powders can be utilized to design scaffolds for tissue engineering, promoting cell growth and tissue regeneration. |
Electronic Applications | Production of conductive components and sensors | The potential applications of REP powders in electronics include: * High-conductivity materials: REP can be used to produce powders from conductive materials like copper and aluminum with minimal oxidation, leading to components with superior electrical conductivity. * Functionally graded conductors: The ability to create powders with a gradient in composition allows for the design of electronic components with tailored electrical properties in different regions. * Microfluidic devices: REP technology can be used to produce powders for the fabrication of microfluidic devices with precise channels and features for fluid manipulation. |
Top REP Powder Models
The REP powder market is constantly evolving, with new and improved models emerging regularly. Here’s a closer look at ten prominent REP powder options:
1. EOS Inox 316L: This stainless steel REP powder is renowned for its excellent corrosion resistance and printability, making it ideal for applications in harsh environments.
2. SLM Solutions RealAlloy AM260: This high-strength aluminum alloy REP powder offers a good balance between strength and weight, perfect for aerospace and automotive components.
3. Höganäs AM 301L: This stainless steel REP powder is known for its exceptional flowability and consistency, ensuring smooth printing processes.
4. Carpenter Incus™ 316L: This unique REP powder boasts superior wear resistance, making it a great choice for parts subjected to high friction.
5. LPW Ti-6Al-4V: This titanium alloy REP powder offers exceptional strength and biocompatibility, suitable for medical implants and aerospace applications.
6. ExOne M2 Tool Steel 1.2344: This tool steel REP powder is perfect for creating durable and wear-resistant tooling for various industries.
7. Proto Labs Cobalt Chrome (CoCr): This cobalt-chromium REP powder delivers exceptional strength, corrosion resistance, and biocompatibility, making it ideal for medical implants and prosthetics.
8. GE Additive Arcam Ti6Al4V: Backed by the reputation of GE Additive, this titanium alloy REP powder offers consistent quality and high performance for demanding aerospace applications.
9. 3D Systems LaserForm® 316L: This stainless steel REP powder from 3D Systems is known for its reliable printability and good mechanical properties, suitable for various industrial applications.
10. BASF AM Stainless Steel 17-4PH: This precipitation-hardening stainless steel REP powder offers a unique combination of high strength and good ductility, making it well-suited for parts requiring both strength and some flexibility.
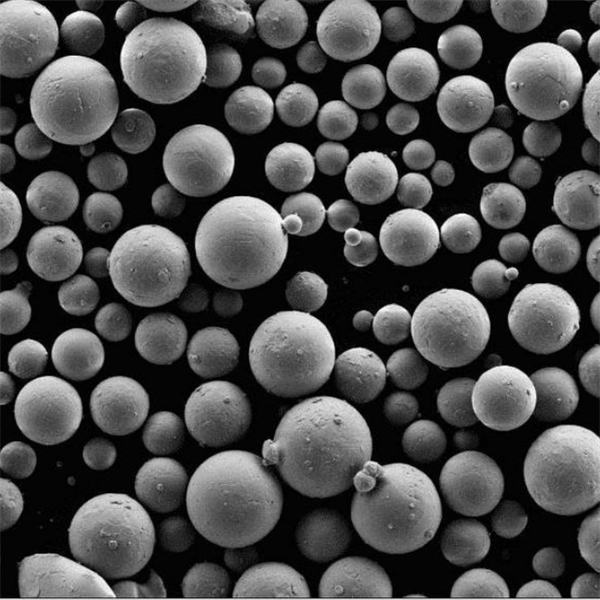
Comparing REP Powders: A Side-by-Side Analysis
While all the aforementioned REP powders share the core benefits of this technology, they possess distinct characteristics that cater to specific needs. Here’s a comparison table to help you choose the most suitable REP powder for your project:
Feature | EOS Inox 316L | SLM Solutions RealAlloy AM260 | Höganäs AM 301L | Carpenter Incus™ 316L | LPW Ti-6Al-4V | ExOne M2 Tool Steel 1.2344 | Proto Labs Cobalt Chrome (CoCr) | GE Additive Arcam Ti6Al4V | 3D Systems LaserForm® 316L | BASF AM Stainless Steel 17-4PH |
---|---|---|---|---|---|---|---|---|---|---|
Material | Stainless Steel | Aluminum Alloy | Stainless Steel | Stainless Steel | Titanium Alloy | Tool Steel | Cobalt Chrome | Titanium Alloy | Stainless Steel | Stainless Steel |
Key Properties | Corrosion resistance, printability | Strength, weight ratio | Flowability, consistency | Wear resistance | Strength, biocompatibility | Wear resistance, durability | Strength, biocompatibility | Strength, performance | Printability, mechanical properties | Strength, ductility |
Ideal Applications | Harsh environments | Aerospace, automotive | Various industries | High-wear parts | Medical implants, aerospace | Tooling | Medical implants, prosthetics | Aerospace | Industrial applications | Parts requiring strength and flexibility |
Additional Considerations When Choosing REP Powders
Beyond the technical specifications, consider these factors when selecting REP powders:
- Project Requirements: Align the powder’s properties with your project’s needs for strength, weight, corrosion resistance, and biocompatibility.
- Printer Compatibility: Ensure the chosen REP powder is compatible with your specific 3D printer model.
- Supplier Reputation: Opt for reputable REP powder suppliers known for consistent quality and reliable service.
- Cost: While REP can be cost-effective in the long run, compare prices from different suppliers to find the best value for your project.
FAQs
Q: What is the difference between REP powders and metal filaments used in FDM printing?
A: REP powders are significantly finer than metal filaments used in Fused Deposition Modeling (FDM) printing. REP powders are used in a different 3D printing technology called binder jetting or laser melting, which offer greater design freedom and accuracy compared to FDM.
Q: Are REP-printed parts as strong as traditionally manufactured parts?
A: With proper processing, REP-printed parts can achieve similar or even superior strength compared to traditionally manufactured parts. The strength depends on the chosen REP powder material and the post-processing techniques employed.
Q: How long does it take to print with REP powders?
A: Print times for REP vary depending on the part size, complexity, and chosen printer settings. Generally, REP printing can be significantly faster than traditional manufacturing methods for complex geometries.
Q: Can REP be used for home 3D printing?
A: Currently, REP technology is primarily utilized in industrial settings due to the high cost and complexity of REP printers. However, advancements in technology may lead to more affordable and user-friendly REP printers for home use in the future.
Share On
MET3DP Technology Co., LTD is a leading provider of additive manufacturing solutions headquartered in Qingdao, China. Our company specializes in 3D printing equipment and high-performance metal powders for industrial applications.
Inquiry to get best price and customized Solution for your business!
Related Articles
About Met3DP
Recent Update
Our Product
CONTACT US
Any questions? Send us message now! We’ll serve your request with a whole team after receiving your message.
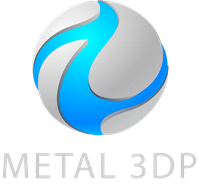
Metal Powders for 3D Printing and Additive Manufacturing